مقدمة
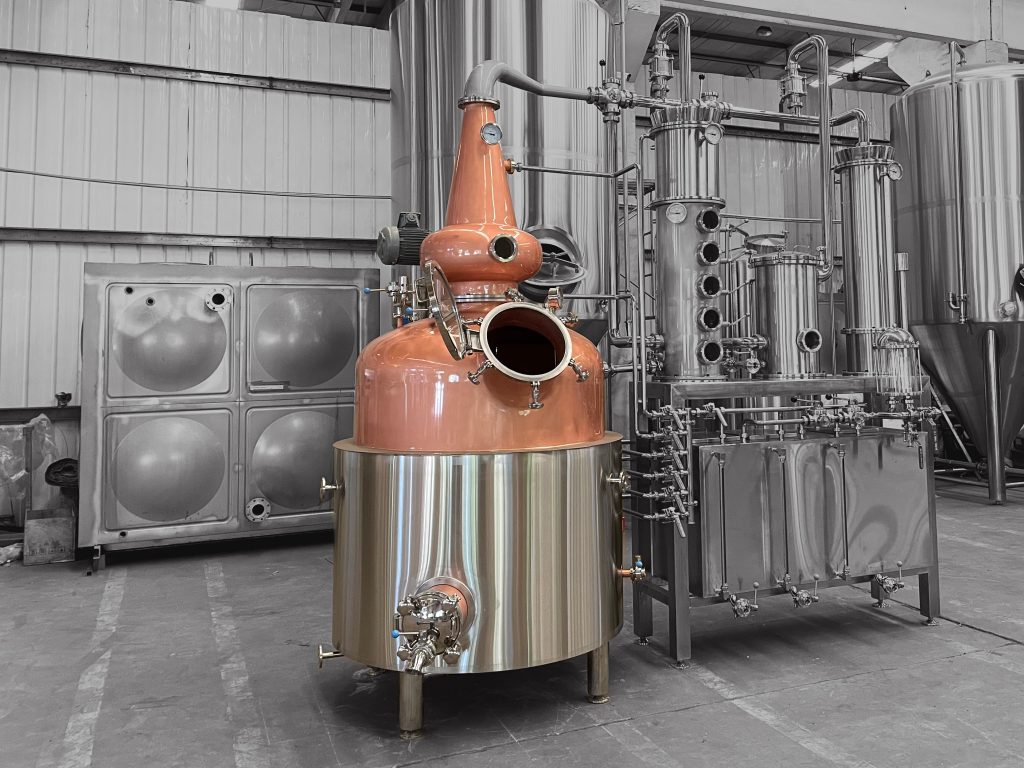
عمود التقطير الارتجاعي هو قطعة متخصصة من المعدات التي تلعب دورًا حاسمًا في الصناعة الكيميائية. تم تصميمه لفصل مخاليط السوائل إلى مكوناتها الفردية، وهي عملية ضرورية لإنتاج مجموعة واسعة من المنتجات، من البنزين ووقود الديزل إلى المواد الكيميائية الدقيقة والأدوية. من خلال فهم المبادئ الأساسية والعمل المعقد لهذه الأعمدة، يمكن للمهندسين والعلماء تحسين أدائها وتعزيز جودة المنتج.
فهم العملية
تتضمن عملية التقطير الارتجاعي في عمود التقطير عدة خطوات رئيسية:
- مقدمة التغذية: يتم إدخال الخليط المراد فصله، المعروف باسم التغذية، إلى العمود عند نقطة محددة. يتم اختيار هذه النقطة بعناية لضمان كفاءة الفصل المثلى في عمود التقطير.
- تبخير: يتم تسخين العلف، مما يؤدي إلى تبخر المكونات الأكثر تطايرًا. يرتفع هذا البخار عبر العمود، حاملاً المكونات المطلوبة إلى أعلى في عمود التقطير.
- البخار الصاعد: عندما يصعد البخار، فإنه يواجه سلسلة من الصواني أو مواد التعبئة. توفر هذه المكونات مساحة سطح كبيرة لنقل الكتلة، مما يسمح للبخار بالتفاعل مع الطور السائل في عمود التقطير.
- التكثيف والارتداد: يتكثف جزء من البخار المتصاعد على الصواني أو العبوات، مكونًا سائلًا. يتدفق هذا السائل، المعروف باسم السائل الراجع، إلى الأسفل عبر العمود، في اتجاه معاكس للبخار المتصاعد في عمود التقطير.
- التوازن: في كل صينية أو عبوة، يتم إنشاء توازن ديناميكي بين الطور البخاري والسائل. تميل المكونات الأكثر تطايرًا إلى التركيز في الطور البخاري، بينما تظل المكونات الأقل تطايرًا في الطور السائل في عمود التقطير.
- سحب المنتج: يتم جمع المكون الأكثر تطايرًا، والذي تم إثراؤه في الطور البخاري، كمنتج في الجزء العلوي من عمود التقطير. وعلى العكس من ذلك، يتم سحب المكون الأقل تطايرًا، والذي تم تركيزه في الطور السائل، كمنتج في الجزء السفلي من عمود التقطير.
المكونات الرئيسية
يشتمل عمود التقطير الارتجاعي على عدة مكونات أساسية:
- عمود: الوعاء الأسطواني الرأسي الذي يحتضن عملية الفصل، ويعتبر ارتفاعه وقطره من العوامل الحاسمة في تحديد سعة العمود وكفاءته في عمود التقطير الارتجاعي.
- الصواني أو التعبئة: توفر هذه المكونات، الموجودة داخل عمود التقطير، مساحة السطح اللازمة لاتصال السائل بالبخار. يمكن أن تكون الصواني من أنواع مختلفة، مثل غطاء الفقاعات، أو صينية الغربال، أو صينية الصمام، ولكل منها مزاياها وعيوبها. توفر مواد التعبئة، مثل حلقات راشيج أو حلقات بال، سطح اتصال أكثر استمرارية في عمود التقطير بالارتداد.
- إعادة الغليان: مصدر حرارة، عادةً ما يكون فرنًا أو ملف بخار، يقع في أسفل عمود التقطير الارتجاعي. وهو يوفر الطاقة اللازمة لتبخير السائل المغذي.
- مكثف: مبادل حراري يقع في أعلى عمود التقطير، حيث يقوم بتبريد البخار وتكثيفه إلى سائل يتدفق مرة أخرى إلى العمود كتدفق رجعي.
- طبلة الارتجاع: وعاء يجمع السائل المكثف من المكثف. يتم إرجاع جزء من هذا السائل إلى عمود التقطير كتدفق رجعي، بينما يتم سحب الباقي كمنتج.
انواع من أعمدة التقطير الارتجاعي
يعتمد اختيار نوع عمود التقطير الارتجاعي على عوامل مختلفة، بما في ذلك تركيبة التغذية ونقاء المنتج المطلوب والقيود التشغيلية. فيما يلي بعض الأنواع الشائعة لأعمدة التقطير:
- عمود التقطير الارتجاعي بغطاء الفقاعات: كل صينية في هذا النوع من أعمدة التقطير مزودة بأغطية فقاعية تسمح للبخار بالمرور عبر السائل، مما يعزز نقل الكتلة بكفاءة. ومع ذلك، فإن أعمدة التقطير ذات الأغطية الفقاعية معقدة نسبيًا ومكلفة في البناء والصيانة.
- عمود التقطير الارتجاعي لصينية الغربال: تحتوي صواني الغربال على ألواح مثقبة تسمح للبخار بالمرور عبر السائل. وهي أبسط وأقل تكلفة من صواني الأغطية الفقاعية ولكنها قد تكون ذات سعة وكفاءة أقل في عمود التقطير.
- عمود التقطير الارتجاعي المعبأ: تمتلئ أعمدة التقطير المعبأة بمواد تعبئة، مثل حلقات راشيج أو حلقات بال. توفر هذه المواد مساحة سطح كبيرة لنقل الكتلة، مما يؤدي إلى كفاءة عالية. غالبًا ما تُستخدم أعمدة التقطير المعبأة في فصل المخاليط المعقدة أو عندما تكون هناك حاجة إلى نقاء عالي.
متطلبات التصميم
يتضمن تصميم عمود التقطير الارتجاعي عدة اعتبارات بالغة الأهمية:
- عدد الصواني أو ارتفاع التعبئة: يحدد عدد الصواني أو ارتفاع العبوة قدرة عمود التقطير الارتجاعي على الفصل. يسمح العدد الأكبر من الصواني أو ارتفاع العبوة الأكبر بفصل أكثر كفاءة في عمود التقطير.
- تباعد الدرج: تؤثر المسافة بين الصواني أو كثافة التعبئة على انخفاض الضغط واحتباس السائل في عمود التقطير. يعد التباعد المناسب أمرًا ضروريًا لموازنة هذه العوامل وتحسين الأداء في عمود التقطير.
- نسبة الارتجاع: تؤثر نسبة الارتداد، التي تُعرف بأنها نسبة السائل الذي يعود إلى عمود التقطير عند الارتداد إلى المنتج المسحوب، بشكل كبير على كفاءة الفصل. تؤدي نسبة الارتداد الأعلى عمومًا إلى فصل أفضل ولكنها تزيد أيضًا من استهلاك الطاقة في عمود التقطير.
- تكوين العلف ومعدل التدفق: يؤثر تكوين ومعدل تدفق خليط التغذية على ظروف تشغيل عمود التقطير والفصل المطلوب.
- قطر العمود: يحدد قطر عمود التقطير قدرته على الضخ. يمكن للقطر الأكبر التعامل مع معدلات تدفق تغذية أعلى في عمود التقطير.
تطبيقات أعمدة التقطير الارتجاعي
تجد أعمدة التقطير الارتجاعي تطبيقات واسعة النطاق في مختلف الصناعات:
- تكرير البترول: فصل النفط الخام إلى منتجات مختلفة، مثل البنزين ووقود الديزل والكيروسين، باستخدام عمود التقطير.
- التصنيع الكيميائي: إنتاج مواد كيميائية نقية لمجموعة واسعة من التطبيقات، بما في ذلك الأدوية والبلاستيك والأسمدة، باستخدام عمود التقطير.
- معالجة الأغذية: تقطير المشروبات الكحولية وتنقية المواد الكيميائية الصالحة للأكل باستخدام عمود التقطير.
- الإصلاح البيئي: فصل المكونات القيمة واستعادتها من مجاري النفايات، باستخدام عمود التقطير.
مقارنة بين أنواع الصواني المختلفة
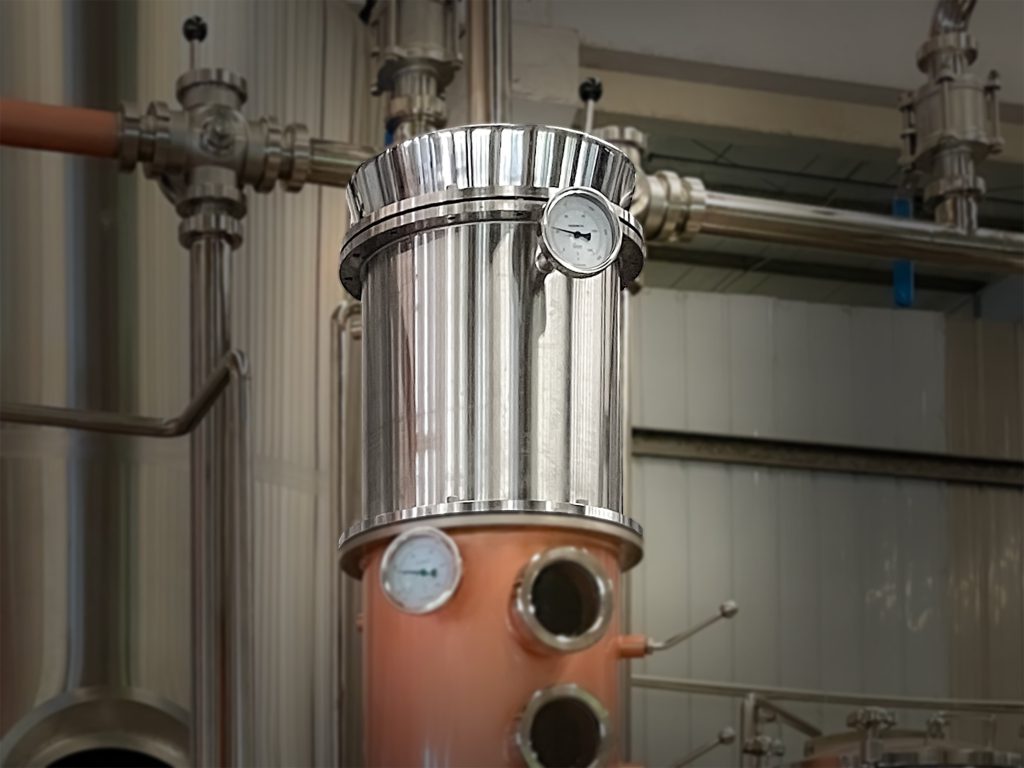
نوع الدرج | مزايا | سلبيات |
---|---|---|
غطاء الفقاعات | قدرة عالية، انخفاض ضغط منخفض، كفاءة عالية | تصميم معقد، تكلفة عالية، عرضة للتلوث |
صينية الغربال | تصميم بسيط، تكلفة منخفضة، انخفاض الضغط منخفض | سعة أقل من صواني الغطاء الفقاعي، وعرضة للتسرب والانسكاب |
عمود معبأ | كفاءة عالية، انخفاض ضغط منخفض، تصميم مرن | يمكن أن تكون عرضة للفيضانات وسوء التوزيع، ويصعب تنظيفها |
خاتمة
أعمدة التقطير الارتجاعي تعتبر أعمدة التقطير هذه أدوات لا غنى عنها في الصناعة الكيميائية، حيث تمكن من فصل المخاليط المعقدة إلى مكوناتها الفردية. ومن خلال فهم المبادئ الأساسية واعتبارات التصميم والتقنيات التشغيلية، يمكن للمهندسين تصميم أعمدة التقطير هذه وتشغيلها وتحسينها بشكل فعال لتلبية متطلبات التطبيقات المتنوعة.
التعليمات
ما هو الفرق بين التقطير والتقطير الجزئي في عمود التقطير الارتجاعي?
التقطير هو تقنية فصل تعتمد على الاختلاف في نقاط غليان المكونات في الخليط. التقطير الكسري، وهو تقنية أكثر تقدمًا، ينطوي على دورات متعددة من التبخير والتكثيف في عمود التقطير الارتجاعي، مما يسمح بفصل المكونات ذات نقاط الغليان المتشابهة.
كيف يتم تحديد نسبة الارتداد في عمود التقطير؟
يتم تحديد نسبة الارتداد بناءً على نقاء المنتج المطلوب وكفاءة الطاقة في عملية التقطير في عمود التقطير. تؤدي نسبة الارتداد الأعلى عمومًا إلى فصل أفضل ولكنها تزيد أيضًا من استهلاك الطاقة في عمود التقطير.
ما هي العوامل التي تؤثر على كفاءة عمود التقطير الارتجاعي?
هناك العديد من العوامل التي تؤثر على كفاءة عمود التقطير الارتجاعي، بما في ذلك عدد الصواني أو ارتفاع التعبئة، وتباعد الصواني، ونسبة الارتجاع، وتركيبة التغذية، وضغط التشغيل.
هل يمكنك شرح مفهوم اللوحات النظرية في عمود التقطير الارتجاعي؟
اللوحة النظرية هي مرحلة افتراضية في عمود التقطير الارتجاعي حيث تصل الطوران البخاري والسائل إلى حالة التوازن. يحدد عدد اللوحات النظرية في عمود التقطير قدرته على الفصل. يسمح العدد الأكبر من اللوحات النظرية بفصل أفضل للمكونات ذات نقاط الغليان المتشابهة في عمود التقطير.