Introducción
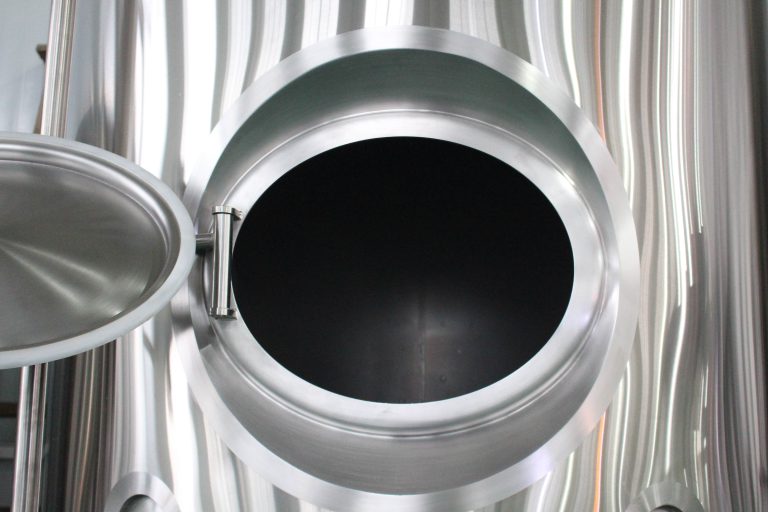
Los tanques de microcervecería son el corazón de cualquier cervecería artesanal. Estos recipientes son esenciales para cada etapa del proceso de elaboración de la cerveza, desde la maceración y la filtración hasta la fermentación y el acondicionamiento. Elegir los tanques de microcervecería adecuados es crucial para producir cerveza de alta calidad y garantizar la eficiencia de sus operaciones de elaboración. Esta guía completa profundizará en los distintos tipos de tanques de microcervecería, sus funcionalidades y los factores a tener en cuenta al seleccionarlos.
Tipos de Tanques de microcervecería
Existen varios tipos de tanques para microcervecerías, cada uno diseñado para un propósito específico en el proceso de elaboración de la cerveza. Estos son algunos de los más comunes:
Tinas de puré y tinas de filtración
- Puré de Tun: Este tanque es donde los granos molidos se mezclan con agua caliente para crear un puré. El tanque de maceración suele estar aislado para mantener una temperatura constante durante el proceso de maceración, lo cual es crucial para la actividad enzimática y la conversión de azúcar.
- Túnel Lauter: Después de la maceración, el líquido dulce llamado mosto se separa del grano usado en el tanque de filtración. Este tanque tiene un fondo falso con ranuras finas o rejillas que actúan como filtro. Algunas cervecerías utilizan una combinación de tanque de filtración y maceración, que realiza ambas funciones.
Hervidores de agua y tanques de hidromasaje
- Hervidor de cerveza: El mosto se hierve en el hervidor, que normalmente está hecho de acero inoxidable y se calienta con vapor, electricidad o fuego directo. La ebullición tiene varios propósitos, entre ellos, esterilizar el mosto, isomerizar los ácidos alfa del lúpulo para darle amargor y eliminar los compuestos volátiles no deseados.
- Tanque de hidromasaje: Después de hervir, el mosto se transfiere al tanque de hidromasaje, donde se hace girar para crear una fuerza centrífuga que separa los restos de lúpulo y el sedimento de proteínas del mosto claro.
Recipientes de fermentación: tanques unitarios, tanques cilindrocónicos y más
- Recipientes de fermentación: En estos tanques es donde se produce la magia de la fermentación. Se añade levadura al mosto enfriado y esta convierte los azúcares en alcohol y dióxido de carbono. Existen varios tipos de recipientes de fermentación:
- Tanques unitarios: Estos tanques versátiles se pueden utilizar tanto para fermentación como para acondicionamiento, ahorrando espacio y costos.
- Tanques Cilíndricos Cónicos (CCV): Este es el tipo de recipiente de fermentación más común en las cervecerías modernas. Su fondo cónico permite una fácil recolección de levadura y eliminación de turbios.
- Fermentadores abiertos: Estos recipientes tradicionales están abiertos al aire, lo que permite el desarrollo de un sabor único pero también aumenta el riesgo de contaminación.
Tanques de acondicionamiento (tanques de cerveza brillante)
- Tanques de acondicionamiento (tanques de cerveza brillante): Después de la fermentación, la cerveza se transfiere a tanques de acondicionamiento, también conocidos como tanques de cerveza brillante, para su maduración y carbonatación. Estos tanques suelen mantenerse a una temperatura fría para permitir que la cerveza se aclare y los sabores se suavicen.
Factores a tener en cuenta al elegir Tanques de microcervecería
Seleccionar los tanques adecuados para una microcervecería es una inversión importante. A continuación, se indican algunos factores clave a tener en cuenta:
- Tamaño de la cervecería y capacidad de producción: El tamaño y la cantidad de tanques que necesitará dependerán del volumen de producción de su cervecería y de sus planes de crecimiento futuros.
- Diseño del sistema de elaboración de cerveza: La disposición de su sala de cocción y el flujo de su proceso de elaboración influirán en la ubicación y configuración de sus tanques.
- Material y construcción del tanque: El acero inoxidable es el material preferido para los tanques de las microcervecerías debido a su durabilidad, resistencia a la corrosión y facilidad de limpieza. La calidad de las soldaduras y la construcción general del tanque también son cruciales.
- Características y accesorios del tanque: Considere características como aislamiento, camisas de enfriamiento, sistemas de control de temperatura e indicadores de nivel.
- Presupuesto: Los tanques para microcervecerías representan una inversión importante. Busque un equilibrio entre calidad y características y sus limitaciones presupuestarias.
Cálculos de capacidad y dimensionamiento de tanques de microcervecerías
El tamaño adecuado del tanque es fundamental para que las operaciones de elaboración de cerveza sean eficientes. A continuación, se ofrece una descripción general básica de cómo calcular la capacidad del tanque:
- Determinar el tamaño del lote: Comience por determinar el tamaño de lote deseado en barriles o hectolitros.
- Considere Headspace: Agregue espacio de cabeza (normalmente 20-30%) para tener en cuenta la espuma y la expansión durante la fermentación.
- Calcular el volumen total del tanque: Multiplique el tamaño de su lote por el factor de espacio de cabeza para determinar el volumen total del tanque.
Limpieza y mantenimiento de tanques de microcervecerías
Una limpieza y un mantenimiento adecuados son esenciales para mantener la calidad de la cerveza y la longevidad de los tanques de la microcervecería. A continuación, se indican algunas prácticas clave:
- Sistemas de limpieza in situ (CIP): Los sistemas CIP automatizan el proceso de limpieza, garantizando una limpieza constante y exhaustiva de sus tanques.
- Inspecciones periódicas: Inspeccione periódicamente sus tanques para detectar cualquier signo de daño o desgaste.
- Almacenamiento adecuado: Cuando no estén en uso, guarde los tanques en un ambiente limpio y seco.
Configuraciones y distribución de tanques de microcervecerías
La disposición de los tanques de su microcervecería afectará la eficiencia de sus operaciones de elaboración de cerveza. Tenga en cuenta estos factores:
- Disposición de la sala de cocción: Organice sus tanques para facilitar un flujo fluido del proceso de elaboración.
- Restricciones de espacio: Optimice el uso de su espacio disponible.
- Expansión futura: Planifique una posible expansión futura dejando espacio para tanques adicionales.
Comparación de Tanque de microcervecería Características
Característica | Descripción | Beneficio |
---|---|---|
Material | Generalmente acero inoxidable (grado 304 o 316). | Durable, resistente a la corrosión, fácil de limpiar e higiénico. |
Aislamiento | Evita la pérdida o ganancia de calor, manteniendo temperaturas constantes durante la maceración, la fermentación y el acondicionamiento. | Mejora la eficiencia energética y el control de la temperatura, lo que conduce a una calidad de cerveza constante. |
Chaquetas refrigerantes | Camisas externas soldadas al exterior del tanque, a través de las cuales circula el refrigerante para controlar la temperatura. | Control preciso de la temperatura durante la fermentación y el acondicionamiento. |
Control de temperatura | Sistemas automatizados que monitorean y regulan las temperaturas de los tanques. | Fermentación y acondicionamiento consistentes, dando como resultado perfiles de cerveza predecibles. |
Indicadores de nivel | Dispositivos que muestran el nivel de líquido dentro del tanque. | Medición precisa del volumen de líquido para cálculos de preparación precisos. |
Bolas de pulverización CIP | Dispositivos rociadores giratorios dentro del tanque que distribuyen soluciones de limpieza. | Garantiza una limpieza exhaustiva y eficiente del interior del tanque. |
Pasarelas | Puertos de acceso para inspeccionar y limpiar el interior del tanque. | Permite un fácil acceso para mantenimiento e inspección. |
Válvulas de alivio de presión | Dispositivos de seguridad que evitan la sobrepresurización del tanque. | Garantiza el funcionamiento seguro de los tanques. |
Válvulas de muestra | Válvulas utilizadas para extraer muestras de la cerveza para realizar pruebas durante la fermentación y el acondicionamiento. | Permite monitorear el progreso de la fermentación y la calidad de la cerveza. |
Piedra de carbonatación | Una piedra porosa utilizada para introducir dióxido de carbono en la cerveza para su carbonatación. | Carbonatación eficiente y controlada de la cerveza. |
Problemas comunes y resolución de problemas con tanques de microcervecerías
Incluso con el cuidado adecuado, es posible que surjan algunos problemas con los tanques de su microcervecería. A continuación, se indican algunos problemas comunes y sus soluciones:
- Fugas: Revise las soldaduras y conexiones para detectar cualquier signo de fugas.
- Problemas de control de temperatura: Asegúrese de que su sistema de enfriamiento esté funcionando correctamente y que sus sensores de temperatura sean precisos.
- Mal funcionamiento del sistema CIP: Inspeccione y mantenga periódicamente su sistema CIP para evitar bloqueos o fallos de funcionamiento.
- Contaminación: Implementar procedimientos sanitarios estrictos para evitar la contaminación microbiana.
Tendencias futuras en la tecnología de tanques de microcervecerías (continuación)
La industria de la microcervecería está en constante evolución, al igual que la tecnología que se utiliza en sus tanques. A continuación, se presentan algunas tendencias emergentes:
- Automatización: Mayor automatización de las operaciones de los tanques, incluidos el control de temperatura, la limpieza in situ y el registro de datos, lo que genera una mayor uniformidad y reduce los costos de mano de obra. Esto incluye el control automatizado de válvulas, la captura automatizada de datos para registros de lotes y la integración con el software de gestión general de la cervecería.
- Tanques inteligentes: Integración de sensores y análisis de datos para optimizar los procesos de elaboración y mejorar la calidad de la cerveza. Estos “tanques inteligentes” pueden monitorear diversos parámetros como la temperatura, la presión, la gravedad e incluso el oxígeno disuelto en tiempo real, lo que brinda a los cerveceros información valiosa y permite un control preciso.
- Prácticas de elaboración de cerveza sostenible: Desarrollo de diseños y materiales de tanques más eficientes energéticamente y respetuosos con el medio ambiente. Esto incluye un mejor aislamiento para reducir el consumo de energía para calefacción y refrigeración, así como el uso de materiales reciclados o reciclables en la construcción de tanques.
- Sistemas de tanques modulares: El auge de los sistemas de tanques modulares que permiten a las cervecerías ampliar fácilmente su capacidad añadiendo más tanques según sea necesario. Esto proporciona mayor flexibilidad y escalabilidad para las cervecerías en crecimiento.
- Materiales avanzados: Exploración de nuevos materiales más allá del acero inoxidable tradicional, como polímeros o compuestos avanzados, que ofrecen un mejor rendimiento, durabilidad o rentabilidad. Estos materiales pueden ofrecer mejores propiedades de aislamiento, menor peso o mayor resistencia a la corrosión.
Invertir en Tanques de microcervecería:Una perspectiva a largo plazo
Invertir en tanques de alta calidad para microcervecerías es una inversión importante, pero que dará sus frutos a largo plazo. Si elige los tanques adecuados y les hace el mantenimiento adecuado, podrá garantizar la producción constante de cerveza de alta calidad, optimizar sus operaciones de elaboración de cerveza y posicionar su cervecería para el éxito a largo plazo. Tenga en cuenta estos puntos:
- Calidad vs. Costo: Si bien puede ser tentador optar por tanques más baratos, invertir en tanques de mayor calidad de fabricantes acreditados resultará en una mayor durabilidad, menos problemas de mantenimiento y, en última instancia, un mejor retorno de la inversión.
- Reputación del proveedor: Elija un proveedor con una trayectoria comprobada de suministro de equipos confiables y excelente atención al cliente. Busque proveedores que ofrezcan garantías y asistencia técnica.
- Instalación y capacitación: Asegúrese de que la instalación de sus tanques esté a cargo de profesionales calificados y que su equipo de elaboración de cerveza reciba la capacitación adecuada sobre su operación y mantenimiento.
Estudios de caso: uso exitoso de Tanques de microcervecería
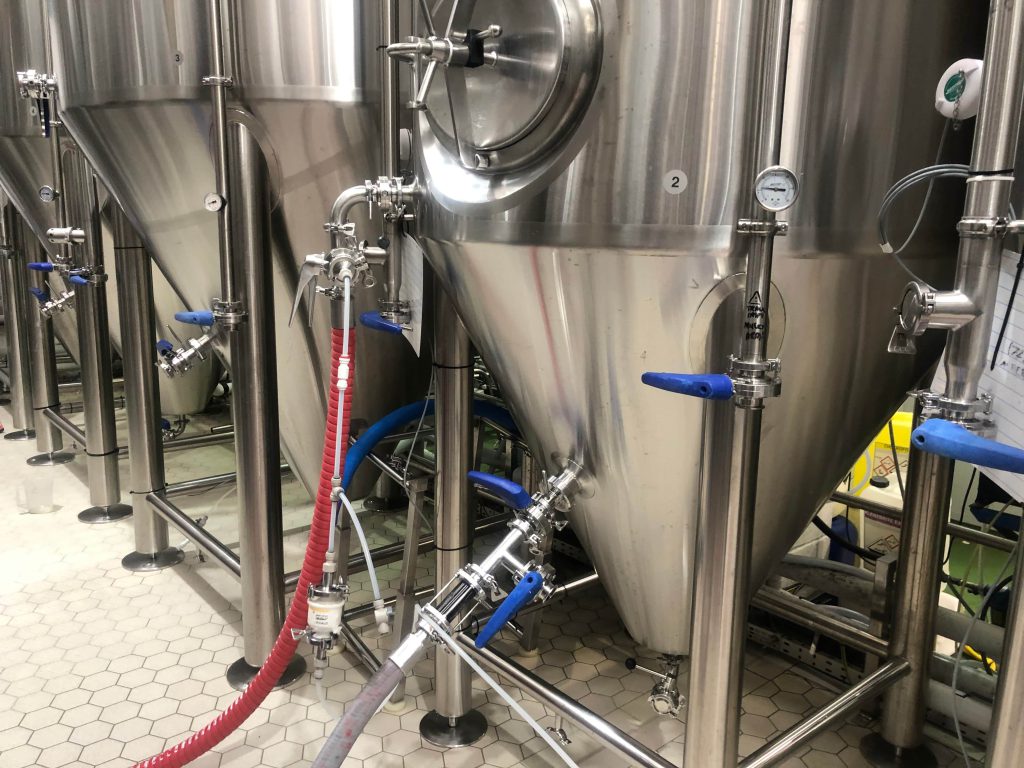
El examen de ejemplos del mundo real puede brindar información valiosa sobre el uso eficaz de los tanques de las microcervecerías:
- Estudio de caso: Expansión de la producción: Una pequeña cervecería experimentó un rápido crecimiento y necesitaba aumentar su capacidad de producción. Al agregar recipientes de fermentación más grandes y un tanque especial para cerveza brillante, pudieron satisfacer la mayor demanda y, al mismo tiempo, mantener una calidad de cerveza constante.
- Estudio de caso: Mejora de la eficiencia: Una cervecería implementó un nuevo sistema CIP para sus tanques, lo que redujo significativamente el tiempo de limpieza y el consumo de agua, lo que generó una mayor eficiencia y ahorro de costos.
- Estudio de caso: Cómo lograr estilos de cerveza específicos: Una cervecería especializada en cervezas lager invirtió en tanques cilindrocónicos con control preciso de temperatura, lo que les permitió lograr los perfiles de fermentación específicos requeridos para estos estilos.
Conclusión
Elegir lo correcto tanques de microcervecería es una decisión fundamental para cualquier cervecería artesanal. Si comprende los diferentes tipos de tanques, los factores que debe tener en cuenta al seleccionarlos y la importancia de un mantenimiento adecuado, podrá tomar decisiones informadas que beneficiarán a su cervecería en los años venideros. Recuerde tener en cuenta las necesidades específicas de su cervecería, su presupuesto y sus objetivos a largo plazo al hacer sus selecciones. Una planificación cuidadosa y la inversión en equipos de calidad contribuirán significativamente al éxito de su cervecería.
Preguntas más frecuentes
¿Con qué frecuencia debería? tanques de microcervecería limpiarse?
Los recipientes de fermentación deben limpiarse después de cada lote, mientras que otros tanques pueden requerir una limpieza menos frecuente según su uso. La implementación de un sistema CIP sólido es fundamental para una limpieza constante y eficiente.
¿Cuál es la diferencia entre un unitank y un tanque cilindrocónico?
Un tanque unitario se puede utilizar tanto para la fermentación como para el acondicionamiento, mientras que un tanque cilíndrico-cónico se utiliza principalmente para la fermentación. Los tanques unitarios suelen ser una buena opción para cervecerías más pequeñas con espacio limitado.
¿Cómo elijo los tanques de tamaño adecuado para mi cervecería?
El tamaño y la cantidad de tanques que necesita dependerán del tamaño de lote deseado, el volumen de producción y los planes de crecimiento futuros. Consulte con un proveedor de equipos de elaboración de cerveza para obtener ayuda con los cálculos de tamaño.
¿Cuáles son las consideraciones de seguridad para trabajar con tanques de microcervecería?
Se deben seguir los procedimientos de seguridad adecuados al trabajar con tanques de microcervecerías, incluido el uso de equipo de protección personal (EPP) adecuado y el cumplimiento de los protocolos de ingreso a espacios confinados al ingresar a los tanques para limpieza o mantenimiento. Las válvulas de alivio de presión se deben inspeccionar periódicamente para garantizar un funcionamiento seguro.