導入
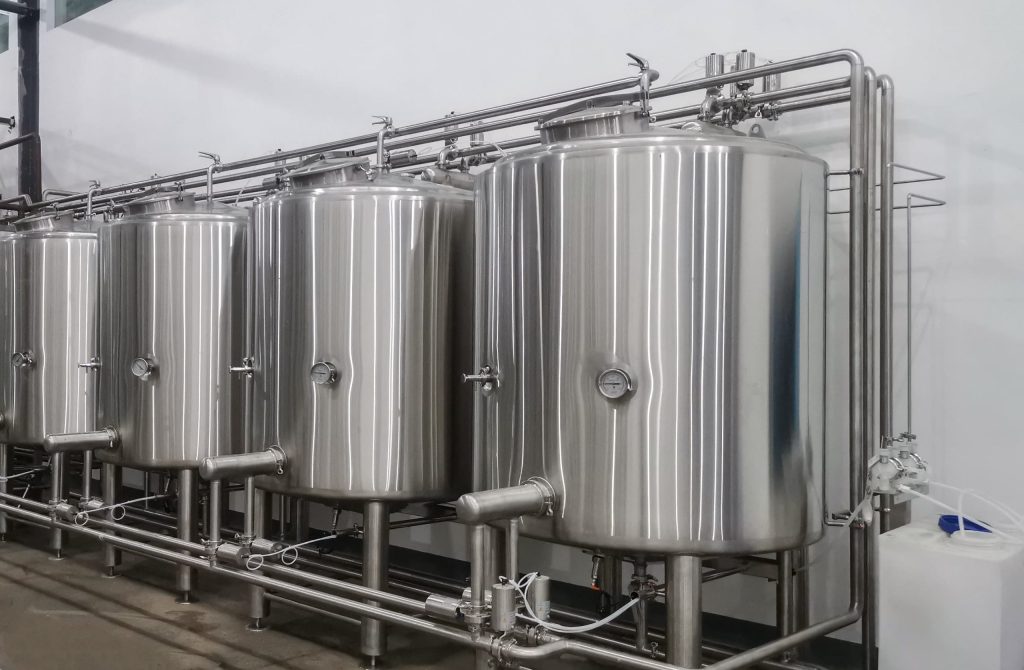
現代の産業環境では、衛生と運用効率の高水準を維持することが重要です。これらの目標を達成するための最も効果的な戦略の 1 つは、Clean in Place (CIP) 設計です。このプロセスでは、機器とパイプラインを分解せずに自動的に洗浄します。このブログでは、CIP 設計の原則、その利点、実装戦略、および衛生と運用効率の両方への影響について詳しく説明します。
理解 クリーンインプレイス設計
Clean in Place 設計は、食品・飲料、医薬品、化学薬品などの業界で、機器やパイプラインを分解せずに洗浄するために使用されているシステムです。この方法は、機器やパイプラインの清潔さを維持し、ダウンタイムを短縮し、健康と安全の規制に準拠するのに役立ちます。
CIP設計の原則
CIP システムは、いくつかの重要な原則に基づいて動作します。
- 自動清掃CIP システムは洗浄プロセスを自動化し、人的介入を最小限に抑え、汚染のリスクを軽減します。
- 洗浄剤のリサイクルCIP システムでは、廃棄物を最小限に抑えてコストを削減するために、洗浄剤をリサイクルすることがよくあります。
- サイクルコントロールCIP システムは洗浄サイクルを正確に制御し、徹底した洗浄と衛生化を保証します。
- 監視と検証CIP システムには、洗浄プロセスが必要な基準を満たしていることを確認するための監視および検証プロセスが含まれています。
CIPシステムのコンポーネント
CIP システムは通常、複数のコンポーネントで構成されます。
- 洗浄液の保管洗浄剤を保管するためのタンクまたは容器。
- パンプス: 装置内に洗浄液を循環させます。
- 熱交換器: 必要に応じて洗浄液を加熱します。
- 制御システム: クリーニング サイクルを管理し、パフォーマンスを監視します。
- パイプとバルブ: 洗浄液をシステム内に送り込みます。
のメリット クリーンインプレイス設計
CIP システムを実装すると、次のような多くの利点が得られます。
衛生と安全性の向上
- 汚染リスクの低減: 自動洗浄プロセスにより、手動洗浄に比べて汚染のリスクが軽減されます。
- 一貫した清掃品質CIP システムは均一な洗浄結果を提供し、機器のすべての部品が徹底的に洗浄されることを保証します。
- 規制の遵守CIP システムは、業界が厳しい衛生および安全基準を満たすのに役立ちます。
効率性の向上とコスト削減
- ダウンタイムの短縮CIP システムは、分解と組み立ての必要がなくなるため、ダウンタイムを最小限に抑えます。
- 人件費の削減: 自動化により手作業の必要性が減り、コスト削減につながります。
- 資源効率: 洗浄剤のリサイクルと水の使用の最適化により、運用コストが削減されます。
環境上の利点
- 水使用量の削減CIP システムは水の使用量を最小限に抑えるように設計されており、環境の持続可能性に貢献します。
- 効率的な化学物質の使用: 洗浄剤をリサイクルすることで化学廃棄物と環境への影響が削減されます。
実装戦略 クリーンインプレイス設計
CIP システムの実装には、慎重な計画と実行が必要です。実装を成功させるための重要な手順は次のとおりです。
ニーズと目標の評価
- 機器の評価: 清掃が必要な機器とパイプラインの種類を決定します。
- 清掃要件を定義する各機器に必要な清掃基準と頻度を特定します。
- 目標を設定する衛生基準、効率目標、コスト削減など、CIP システムの明確な目標を設定します。
CIPシステムの設計
- コンポーネントを選択ポンプ、タンク、制御システムなど、CIP システムに適切なコンポーネントを選択します。
- 清掃サイクルを開発する: 機器やプロセスの特定のニーズを満たす洗浄サイクルを設計します。
- 既存のシステムとの統合CIP システムが既存の機器およびプロセスとシームレスに統合されることを確認します。
トレーニングとメンテナンス
- 人材育成CIP システムの操作と保守に関するトレーニングをスタッフに提供します。
- 定期メンテナンス: CIP システムが効果的かつ効率的に動作するように、メンテナンス スケジュールを実装します。
CIP 導入成功事例
食品・飲料業界
食品および飲料業界では、CIP システムが洗浄プロセスに革命をもたらしました。たとえば、大手乳製品メーカーは CIP システムを導入し、洗浄時間を 50% 短縮し、水と化学薬品の使用量を 30% 削減しました。
製薬業界
ある製薬会社は、生産ラインの厳格な清浄度要件を満たすために CIP システムを導入しました。このシステムにより、規制基準への準拠を維持しながら、ダウンタイムと人件費を削減することができました。
CIP パフォーマンスを評価するための主要指標
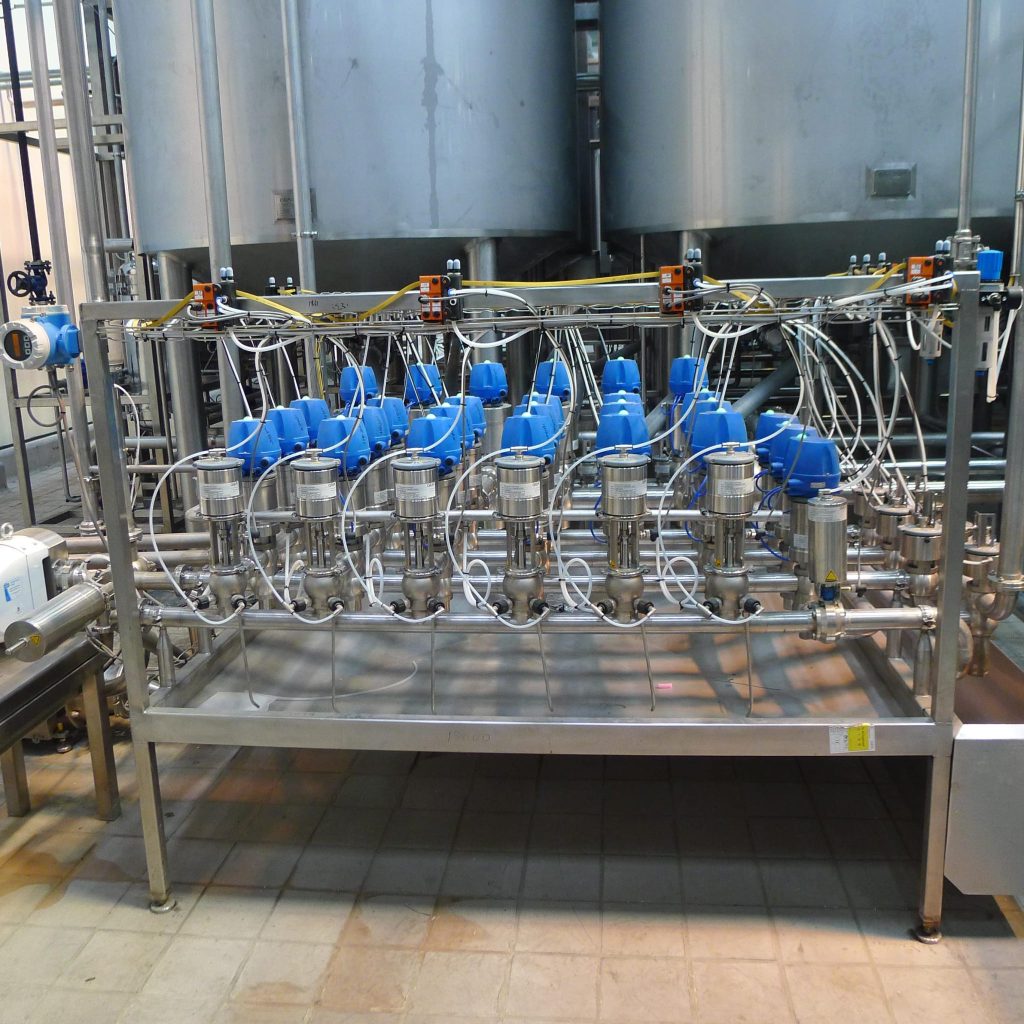
CIP システムのパフォーマンスを評価するには、次の指標を考慮してください。
メトリック | 説明 | 目標値 |
---|---|---|
掃除の時間 | クリーニングサイクルを完了するのに必要な時間 | 30分 |
水の使用 | 洗浄サイクルあたりの水使用量 | 200リットル |
化学物質の使用 | 使用した洗浄剤の量 | 5リットル |
ダウンタイムの削減 | CIPの導入による設備のダウンタイムの減少 | 40%削減 |
コンプライアンス率 | 規制基準を満たす洗浄プロセスの割合 | 100% |
結論
クリーンインプレイス設計 産業現場での衛生と効率性の向上に重要な役割を果たします。洗浄プロセスの自動化、ダウンタイムの削減、リソース効率の向上により、CIP システムは運用の成功に大きく貢献します。適切に設計された CIP システムを実装すると、コスト削減、環境の持続可能性、規制遵守など、大きなメリットが得られます。
CIP システムへの投資は、産業オペレーションのさまざまな側面の改善を推進できる戦略的な決定です。業界では衛生と効率が引き続き優先されるため、CIP 設計はこれらの目標を達成するための重要な要素であり続けます。
よくある質問
何ですか クリーンインプレイス設計?
Clean in Place 設計とは、分解せずに機器やパイプラインを自動的に洗浄するために使用されるシステムを指します。ダウンタイムと人的介入を最小限に抑えながら、効果的な洗浄を保証します。
CIP はどのように衛生を改善するのでしょうか?
CIP システムは、洗浄プロセスを自動化し、汚染リスクを軽減し、機器の一貫した徹底的な洗浄を保証することで衛生状態を向上させます。
の主なメリットは何ですか? クリーンインプレイス設計?
CIP (Clean In Place) 設計の主な利点には、衛生状態の改善、ダウンタイムの短縮、人件費の削減、資源の効率化、環境の持続可能性などがあります。
CIP システムをどのように実装すればよいですか?
CIP システムの導入には、ニーズの評価、システムの設計、既存のプロセスとの統合、および人員のトレーニングが含まれます。最適なパフォーマンスを得るには、定期的なメンテナンスも重要です。
できる CIPシステム すべての業界で使用可能ですか?
CIP システムは、食品・飲料、医薬品、化学薬品などの業界で広く使用されています。ただし、その適用性は各業界の特定の洗浄要件によって異なります。
CIP パフォーマンスを評価するために重要な指標は何ですか?
CIP パフォーマンスを評価するための重要な指標には、洗浄時間、水の使用量、化学薬品の使用量、ダウンタイムの削減、コンプライアンス率などがあります。