導入

In today’s industrial landscape, cleanliness is not just a matter of aesthetics—it’s a critical factor affecting product quality, safety, and operational efficiency. Clean in Place (CIP) systems have revolutionized the way industries maintain hygiene standards by offering automated cleaning solutions that minimize downtime and maximize productivity. This blog delves into the essential role of clean in place systems in industrial settings, exploring their components, advantages, and diverse applications across different sectors.
の重要性 Clean in Place Systems
Clean in Place (CIP) systems represent a cornerstone of modern industrial hygiene practices, particularly in sectors such as food and beverage, pharmaceuticals, and dairy processing. These systems allow for the cleaning and sterilization of process equipment without the need for disassembly, thereby reducing the risk of contamination and ensuring compliance with stringent regulatory standards.
Components of Clean in Place Systems
A typical clean in place system comprises several key components that work together seamlessly to facilitate efficient cleaning:
- Cleaning Solution Tanks: These tanks store the cleaning agents required for the clean in place process, including detergents, sanitizers, and sometimes acids for more rigorous cleaning.
- パンプス: Essential for circulating the cleaning solutions throughout the system, ensuring that all surfaces are thoroughly cleaned.
- 熱交換器: Used to heat or cool cleaning solutions to the optimal temperature for effective cleaning.
- 制御システム: Monitor and regulate various parameters such as temperature, pressure, and flow rates to maintain cleaning efficacy.
- Valves and Sensors: Control the flow of cleaning solutions and provide feedback on critical parameters, ensuring consistent cleaning results.
使用の利点 Clean in Place Systems
The adoption of clean in place systems offers numerous advantages to industrial operations:
- Time Efficiency: clean in place systems reduce downtime by allowing equipment to be cleaned in place, eliminating the need for time-consuming disassembly and reassembly.
- 一貫性: Automated cleaning processes ensure uniform cleaning results, contributing to consistent product quality and reducing variability in production.
- Resource Savings: By optimizing the use of water, chemicals, and energy, clean in place systems contribute to significant cost savings and sustainability efforts.
- 安全性: Minimize the exposure of personnel to potentially hazardous cleaning agents, enhancing workplace safety.
- コンプライアンス: Facilitate adherence to strict hygiene and safety regulations, crucial for industries such as food manufacturing and pharmaceuticals.
Implementation Across Industries
Clean in Place (CIP) systems find application across a wide range of industries, each with unique requirements and challenges:
- 食品と飲料: Essential for cleaning processing equipment, filling machines, and packaging lines to maintain food safety standards and prevent cross-contamination.
- 医薬品: Used to sterilize production equipment and maintain aseptic conditions critical for drug manufacturing processes.
- Dairy: Crucial for cleaning and sanitizing milk processing equipment to ensure product quality and extend equipment lifespan.
- 醸造: Utilized in cleaning fermentation tanks, brewing equipment, and piping systems to maintain hygiene standards and preserve product integrity.
ケーススタディと例
Examples of clean in place System Implementations
業界 | 応用 | 利点 |
---|---|---|
食品および飲料 | Cleaning filling equipment | Reduced downtime, improved product safety |
Pharmaceutical | Sterilizing production equipment | Compliance with regulatory standards |
乳製品 | Cleaning milk processing equipment | Enhanced hygiene, extended equipment lifespan |
Brewing | Cleaning fermentation tanks | Consistent product quality, reduced cleaning time |
課題と検討事項
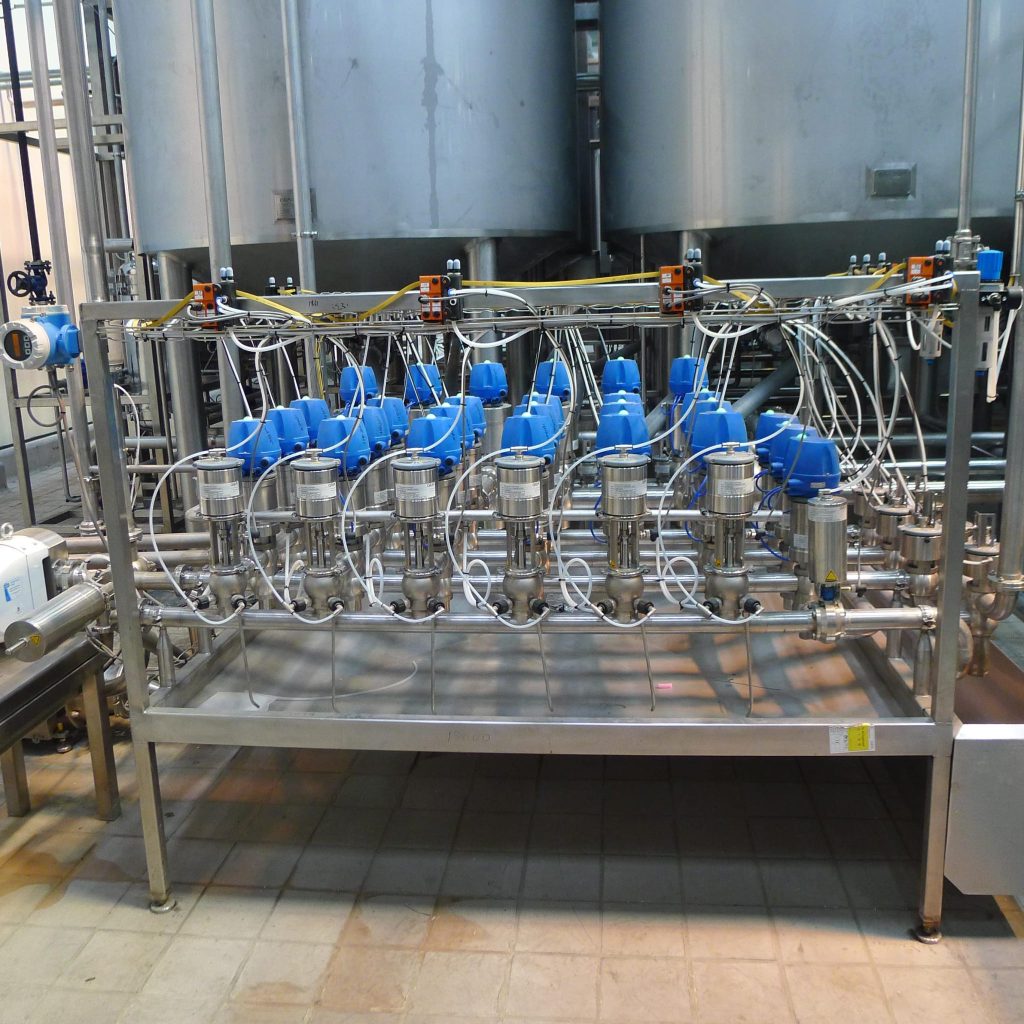
While Clean in Place (CIP) systems offer significant benefits, their implementation comes with challenges that need to be addressed:
- 初期投資: The upfront cost of installing clean in place systems can be considerable, including equipment purchase, installation, and integration with existing infrastructure.
- Complexity: Proper design and configuration are crucial to ensure effective cleaning and system reliability.
- メンテナンス: Regular maintenance is essential to keep the system operating at peak efficiency and to prevent downtime.
- Compatibility: Clean in place systems must be compatible with existing equipment and processes to avoid disruptions and ensure seamless integration.
結論
Clean in Place (CIP) systems represent a cornerstone of modern industrial hygiene practices, offering automated cleaning solutions that enhance efficiency, ensure product quality, and comply with stringent regulatory standards. Despite initial challenges, the long-term benefits of CIP systems justify their adoption across various industries. By investing in CIP technology, businesses can streamline operations, reduce costs, and maintain high standards of cleanliness and safety.
よくある質問
Q: どの業界が最も恩恵を受けているか clean in place systems?
A: Industries such as food and beverage, pharmaceuticals, dairy, and brewing benefit significantly from clean in place systems due to their stringent cleanliness requirements and regulatory standards.
Q: How do CIP systems improve operational efficiency?
A: CIP systems reduce downtime by cleaning equipment in place, minimize resource consumption, and ensure consistent cleaning results, thereby improving overall operational efficiency.
Q: Are there different types of cleaning agents used in clean in place systems?
A: Yes, clean in place systems utilize various cleaning agents such as detergents, acids, and sanitizers, selected based on the type of soil and equipment being cleaned.