Einführung
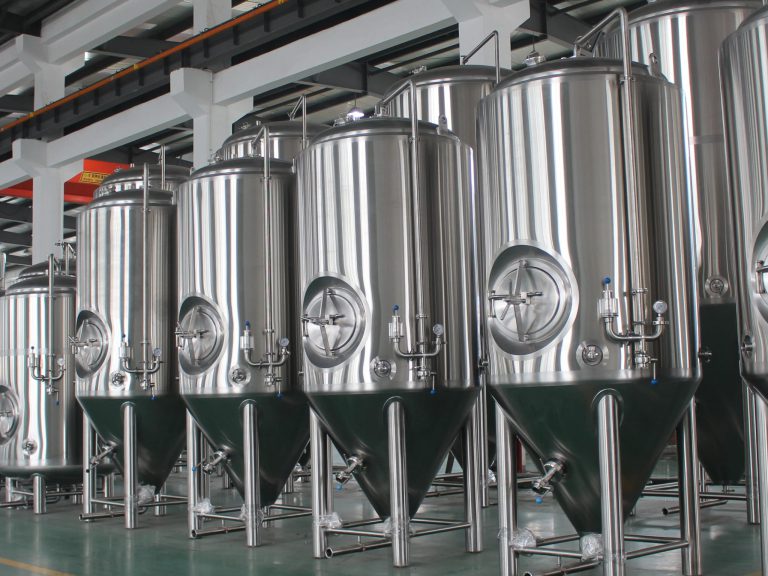
In der heutigen Industrielandschaft spielt die Fermentationstanktechnologie in verschiedenen Branchen eine zentrale Rolle, darunter in der Pharmaindustrie, Biotechnologie sowie der Lebensmittel- und Getränkeindustrie. Diese Spezialbehälter sind darauf ausgelegt, optimale Bedingungen für mikrobielles Wachstum und biochemische Produktion zu schaffen. Dieser Blog befasst sich mit den Fortschritten in der modernen Fermentationstanktechnologie und hebt wichtige Merkmale, Innovationen und ihre vielfältigen Anwendungen hervor.
Verständnis Gärtanks
Fermentation tanks are engineered to control and maintain crucial parameters such as temperature, pH levels, and oxygenation during the fermentation process. This control ensures the reproducibility and efficiency of microbial or enzymatic activity, critical for industries ranging from medicine to agriculture.
Arten von Gärtanks
Modern fermentation tanks are available in several configurations to meet specific operational needs:
- Edelstahltanks: Known for their durability, corrosion resistance, and ease of cleaning, stainless steel tanks are widely used in industries requiring strict hygiene standards such as pharmaceuticals and biotechnology.
- Konische Fermenter: These tanks are designed to facilitate the easy collection of yeast and sediment, crucial for processes in brewing and biofuel production.
- Open-Top Fermenters: Often used in traditional fermentation processes, these tanks allow for manual control of the fermentation environment, ideal for artisanal and specialty products.
Hauptmerkmale von Modern Gärtanks
Advancements in fermentation tank technology have introduced several key features:
- Automated Control Systems: Integrated sensors and automated control systems monitor and adjust fermentation parameters in real-time, ensuring consistent product quality.
- Hygienic Design: Smooth surfaces and sanitary fittings minimize the risk of contamination and simplify cleaning procedures.
- Modularity and Scalability: Tanks can be easily integrated into existing production lines and scaled up or down to meet varying production demands.
Innovations in Gärtank Design
Recent innovations focus on improving efficiency, sustainability, and operational flexibility:
- Smart Sensors and IoT Integration: Real-time data analytics and remote monitoring capabilities optimize process control and predictive maintenance.
- Fortgeschrittene Materialien: Emerging materials such as biocompatible polymers and composite alloys offer enhanced durability, thermal insulation, and reduced environmental impact.
- Energy-Efficient Systems: Innovations in heat recovery, insulation technologies, and efficient agitation mechanisms minimize energy consumption and operational costs.
Case Studies: Applications Across Industries
Fermentation tanks play a critical role in diverse industrial applications:
- Pharmazeutika: Bioreactors and Fermenter are used in the production of antibiotics, vaccines, and therapeutic proteins, where precise control of fermentation conditions is essential.
- Essen und Trinken: From brewing beer and fermenting wine to producing probiotics and enzymes, fermentation tanks enable consistent product quality and flavor development.
- Biofuel Production: Fermenter are integral to the conversion of biomass into biofuels, supporting renewable energy initiatives worldwide.
Vorteile und Herausforderungen
While modern fermentation tanks offer significant advantages in terms of process control and efficiency, they also present challenges:
- Erstinvestition: High upfront costs associated with purchasing and installing advanced fermentation systems.
- Maintenance Requirements: Regular cleaning, calibration of sensors, and preventive maintenance are essential to ensure optimal performance and longevity.
- Skill Requirements: Operators require specialized training to manage complex fermentation processes and utilize advanced control systems effectively.
Future Trends and Outlook
Looking ahead, the future of fermentation tank technology is driven by ongoing research and development efforts:
- Bioprocess Automation: Integration of artificial intelligence (AI) and machine learning (ML) for real-time process optimization and decision-making.
- Biorefinery Concepts: Integration of multiple fermentation processes within a single facility to maximize resource efficiency and product diversity.
- Circular Economy Initiatives: Closed-loop systems and biorefinery concepts aim to minimize waste and maximize the utilization of raw materials and by-products.
Comparison of Common Gärtank Arten
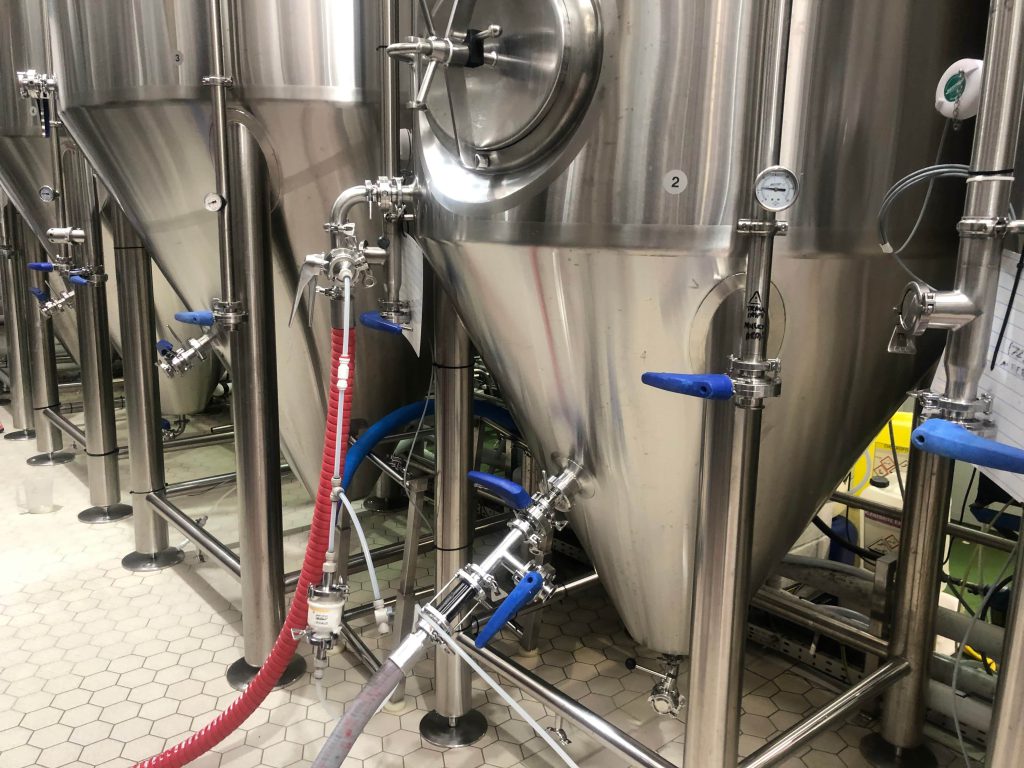
Now, let’s delve deeper into the comparative advantages of different fermentation tank types through the provided table.
Tanktyp | Material | Kapazitätsbereich | Vorteile |
---|---|---|---|
Edelstahl | Edelstahl | Small to Large | Durability, Ease of Cleaning, Corrosion Resistance |
Konischer Fermenter | Stainless Steel, Glass | Klein bis mittel | Facilitates Yeast Collection, Clearing of Sediment |
Open-top Fermenter | Wood, Plastic, Stainless Steel | Medium to Large | Traditional Techniques, Improved Aeration |
Abschluss
Modern Gärtank technology continues to evolve, enhancing process efficiency, product quality, and sustainability across industries. As advancements in materials, automation, and bioprocess engineering continue, the role of fermenter in enabling scalable and sustainable production processes becomes increasingly crucial.
Häufig gestellte Fragen
F: Welche Faktoren sollten bei der Auswahl eines Gärtank?
A: Factors such as capacity, material compatibility, ease of cleaning, and integration with existing processes are crucial considerations.
Q: How can fermenter technology contribute to sustainable practices?
A: Innovations in tank design can reduce energy consumption, minimize waste generation, and optimize resource utilization, thus promoting sustainability.
Q: What are the maintenance requirements for modern Gärtanks?
A: Regular cleaning, calibration of sensors, and inspection for wear are essential for maintaining optimal performance and longevity of fermentation tanks.