Einführung
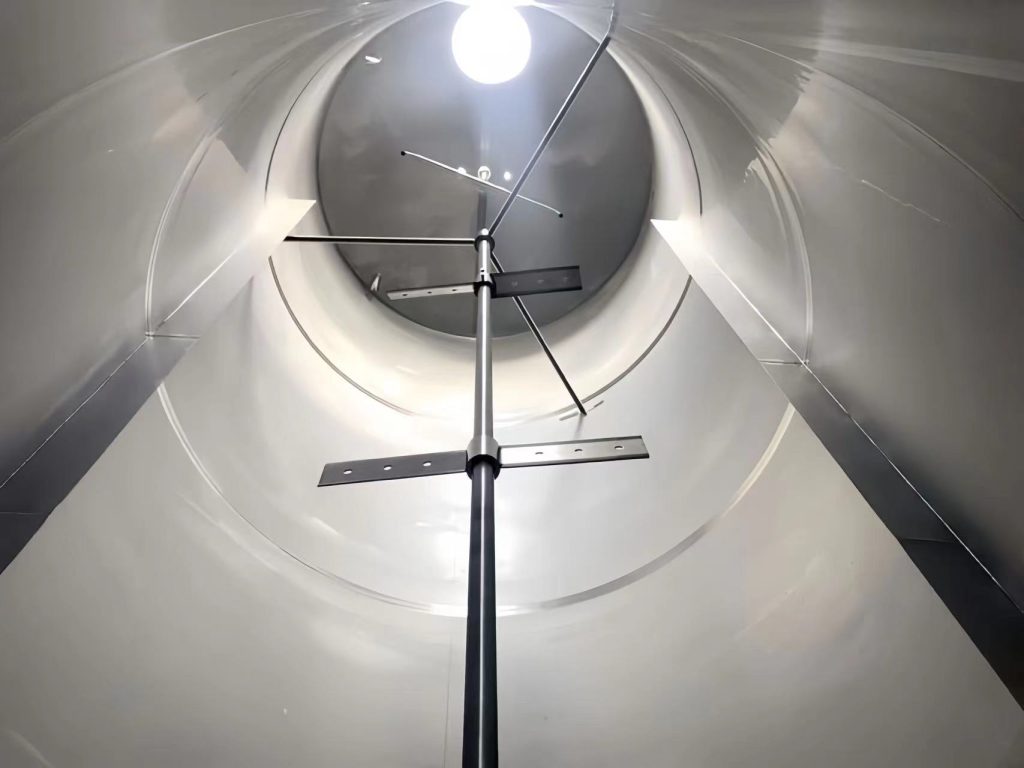
Industrielle Mischtanks sind in zahlreichen Branchen, von der Pharmaindustrie bis zur Lebensmittelverarbeitung, wichtige Ausrüstungsgegenstände. Diese vielseitigen Behälter sind dafür ausgelegt, Substanzen effizient zu mischen, zu emulgieren oder aufzulösen. Dieser umfassende Leitfaden befasst sich mit den Feinheiten industrieller Mischtanks und untersucht deren Konstruktion, Typen, Anwendungen und Auswahlkriterien.
Industrielle Mischtanks verstehen
Industrielle Mischtanks sind mehr als nur einfache Behälter. Sie sind sorgfältig konzipiert, um präzise Misch- und Vermischungsfunktionen zu ermöglichen. Zu den wichtigsten Komponenten gehören:
- Tankkörper: Der Tankkörper besteht in der Regel aus rostfreiem Stahl, emailliertem Stahl oder anderen korrosionsbeständigen Materialien und ist das Hauptgefäß zur Aufnahme der zu mischenden Substanzen.
- Agitator: Der Rührer ist das Herzstück des Mischvorgangs und sorgt für die Erzeugung von Turbulenzen und eine gleichmäßige Mischung. Für unterschiedliche Mischanforderungen sind verschiedene Rührertypen erhältlich, z. B. Propeller, Turbinen, Paddel und Anker.
- Antriebssystem: Das Antriebssystem sorgt für die nötige Leistung des Rührwerks. Es kann über eine Drehzahlregelung zur Feineinstellung des Mischvorgangs verfügen.
- Dichtungen und Dichtungsringe: Diese Komponenten spielen eine entscheidende Rolle bei der Vermeidung von Lecks und der Gewährleistung der Eindämmung der Substanzen im Tank.
- Heiz-/Kühlsystem: Für temperaturgeregelte Prozesse können Heiz- oder Kühlsysteme in die Tankkonstruktion integriert werden.
Arten von Industrie Mischbehälter
Die Auswahl eines Mischbehälters hängt von der spezifischen Anwendung und den Eigenschaften der zu verarbeitenden Materialien ab. Gängige Typen sind:
- Batch-Mischbehälter: Batch-Mischtanks eignen sich ideal für die Produktion im kleinen Maßstab und für Prozesse, bei denen die Rezeptur häufig geändert werden muss, da sie das Mischen und Verarbeiten einzelner Chargen ermöglichen.
- Kontinuierliche Mischbehälter: Kontinuierliche Mischtanks sind für die Produktion großer Mengen konzipiert und sorgen für einen konstanten Fluss des gemischten Produkts. Sie eignen sich für Anwendungen, bei denen eine stetige Versorgung mit der gemischten Substanz erforderlich ist.
- Doppelwandige Mischtanks: Doppelwandige Mischtanks sind mit einem Mantel zum Erhitzen oder Kühlen des Inhalts ausgestattet und werden in Prozessen eingesetzt, die eine präzise Temperaturregelung erfordern.
- Vakuum-Mischbehälter: Vakuummischtanks werden für Anwendungen verwendet, bei denen Luft oder andere Gase entfernt werden müssen. Sie erzeugen eine Niederdruckumgebung, um den Entgasungsprozess zu erleichtern.
Anwendungen von Industrie Mischbehälter
Industrielle Mischtanks finden in zahlreichen Branchen Anwendung, darunter:
- Pharmazeutisch: Mischen pharmazeutischer Wirkstoffe, Vorbereiten von Formulierungen und Vermengen von Pulvern.
- Essen und Trinken: Mischen von Zutaten für Saucen, Dressings und Getränke sowie Fermentationsprozesse.
- Chemisch: Chemikalien mischen, Harze vorbereiten und Reaktionen durchführen.
- Kosmetika: Mischen von Zutaten für Lotionen, Cremes und Parfüms.
Wichtige zu berücksichtigende Funktionen
Bei der Auswahl eines industriellen Mischbehälters sollten mehrere Faktoren sorgfältig berücksichtigt werden:
- Kapazität: Stellen Sie sicher, dass der Tank die erforderliche Chargengröße oder Durchflussrate aufnehmen kann.
- Materialverträglichkeit: Wählen Sie ein Tankmaterial, das mit den verarbeiteten Substanzen kompatibel ist, um Korrosion und Verunreinigungen zu verhindern.
- Mischanforderungen: Berücksichtigen Sie die Viskosität der Materialien, die gewünschte Mischzeit und den erforderlichen Grad der Homogenität.
- Rührwerkstyp: Wählen Sie einen Rührer aus, der für die jeweilige Mischaufgabe geeignet ist. Berücksichtigen Sie dabei beispielsweise die Viskosität der Materialien und die gewünschte Mischintensität.
- Sicherheitsmerkmale: Stellen Sie sicher, dass der Tank mit Sicherheitsvorrichtungen wie Überdruckventilen, Not-Aus und Verriegelungen ausgestattet ist, um das Bedienpersonal zu schützen und Unfälle zu vermeiden.
Vergleich der Rührwerkstypen
Rührwerkstyp | Beschreibung | Anwendungen |
---|---|---|
Propeller | Axialfluss, effizient für Flüssigkeiten mit niedriger Viskosität | Vermengen, Mischen und Suspendieren von Feststoffen |
Turbine | Radiale Strömung, erzeugt hohe Schergeschwindigkeiten | Emulgierung, Dispersion und Lösung |
Paddeln | Schonendes Mischen, ideal für viskose Materialien | Mischen von Schlämmen, Pasten und Hochleistungsanwendungen |
Anker | Schabwirkung, verhindert Wandablagerungen | Mischen viskoser Materialien und Wärmeübertragung |
Faktoren, die die Mischeffizienz beeinflussen
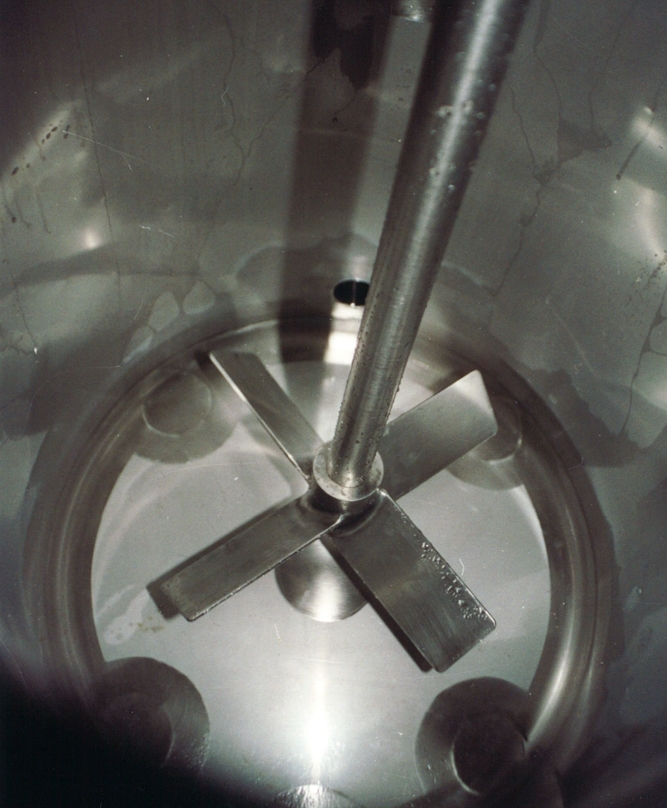
Die Effizienz des Mischens in Industrietanks wird von mehreren Faktoren beeinflusst:
- Rührwerksdrehzahl: Höhere Geschwindigkeiten führen im Allgemeinen zu einer besseren Durchmischung, eine übermäßige Geschwindigkeit kann jedoch zu Kavitation und verringerter Effizienz führen.
- Laufraddesign: Form und Größe des Laufrads beeinflussen das Strömungsmuster im Tank. Für eine optimale Durchmischung ist die richtige Laufradkonstruktion entscheidend.
- Leitbleche: Leitbleche können die Durchmischung verbessern, indem sie Verwirbelungen verhindern und eine radiale Strömung fördern.
- Flüssigkeitseigenschaften: Viskosität, Dichte und Oberflächenspannung der zu mischenden Flüssigkeiten beeinflussen Mischzeit und Energiebedarf.
Abschluss
Industrie Mischbehälter sind unverzichtbare Werkzeuge in der modernen Fertigung. Wenn Sie die verschiedenen Typen, Anwendungen und Auswahlkriterien verstehen, können Sie den optimalen Mischbehälter für Ihre spezifischen Anforderungen auswählen. Eine sorgfältige Berücksichtigung von Faktoren wie Kapazität, Materialverträglichkeit und Mischanforderungen gewährleistet effiziente und effektive Mischprozesse.
Häufig gestellte Fragen
Was ist der Unterschied zwischen Batch- und kontinuierlichem Mischen?
Beim Chargenmischen wird eine bestimmte Materialmenge in einem einzigen Zyklus verarbeitet, während beim kontinuierlichen Mischen ein konstanter Materialfluss durch den Tank erfolgt.
Wie wähle ich das richtige Rührwerk für meine Anwendung aus?
Die Wahl des Rührwerks hängt von Faktoren wie Viskosität, gewünschter Mischintensität und Vorhandensein von Feststoffen ab. Gängige Typen sind Propeller, Turbinen, Paddel und Anker.
Welche Materialien werden üblicherweise für industrielle Mischbehälter?
Zu den üblichen Materialien gehören Edelstahl, glasbeschichteter Stahl und verschiedene Kunststoffarten. Die Materialauswahl hängt von Faktoren wie chemischer Verträglichkeit, Temperaturanforderungen und Druckwerten ab.
Wie kann ich die Mischeffizienz verbessern?
Um die Mischleistung zu verbessern, berücksichtigen Sie Faktoren wie Rührwerksgeschwindigkeit, Laufraddesign, Prallplattenplatzierung und die Zugabe von Tensiden oder Dispergiermitteln.
Welche Sicherheitsvorkehrungen sollten beim Betrieb eines Industriebetriebs getroffen werden? Mischbehälter?
Zu den Sicherheitsvorkehrungen gehören eine angemessene Schulung des Bedienpersonals, regelmäßige Inspektionen, die Einhaltung von Sicherheitsprotokollen und die Verwendung persönlicher Schutzausrüstung.