Einführung
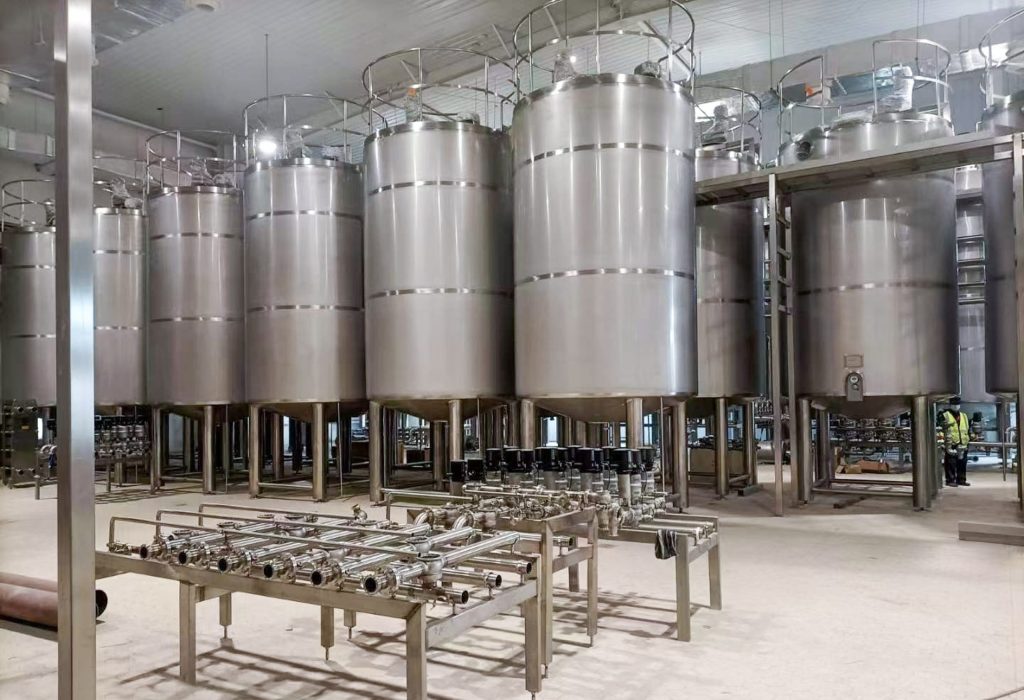
In various industries, maintaining hygiene and sanitation is paramount, especially in food and beverage, pharmaceutical, and biotechnology sectors. Contamination can lead to product spoilage, health hazards, and significant financial losses. Traditionally, cleaning involved manual disassembly and scrubbing of equipment, a time-consuming and labor-intensive process. However, the advent of clean in place (CIP) systems has revolutionized cleaning practices. A clean in place cip system is a method of cleaning interior surfaces of pipes, vessels, process equipment, filters and associated fittings, without disassembly. This automated process ensures consistent, efficient, and reliable cleaning, minimizing downtime and maximizing productivity. This blog post will delve into the numerous benefits of implementing a clean in place cip system.
How Does a Clean in Place (CIP) System Work?
A clean in place cip system typically involves a series of steps, each designed to remove specific types of contaminants. While specific sequences can be tailored to the application and type of soiling, a general cleaning cycle includes:
- Pre-Rinse: This initial step removes large debris and product residues using water.
- Ätzende Wäsche: A caustic solution (e.g., sodium hydroxide) is circulated to remove organic matter, fats, and proteins.
- Zwischenspülung: Water is used to flush out the caustic solution and loosened contaminants.
- Acid Wash (Optional): An acid solution (e.g., nitric acid or phosphoric acid) is circulated to remove mineral deposits and scale.
- Letzter Spülgang: A final rinse with purified water ensures the removal of any remaining cleaning agents.
- Sanitization (Optional): A sanitizing agent (e.g., hot water, steam, or chemical sanitizer) is used to eliminate microorganisms.
These steps are controlled and monitored by a programmable logic controller (PLC), ensuring precise control of time, temperature, flow rate, and chemical concentration. This automation is a key advantage of a clean in place cip system.
Key Components of a Clean in Place (CIP) System
A typical clean in place cip system comprises several essential components:
- Tanks: These hold the cleaning solutions (caustic, acid, water, sanitizer).
- Pumps: These circulate the cleaning solutions through the system.
- Valves: These direct the flow of cleaning solutions to the appropriate circuits.
- Wärmetauscher: These heat the cleaning solutions to the optimal temperature.
- Instrumentation: Sensors monitor parameters such as temperature, flow rate, pressure, and conductivity.
- Kontrollsystem: The PLC controls and monitors the entire cleaning process.
The Advantages of a Clean in Place (CIP) System
Implementing a clean in place cip system offers a multitude of benefits across various aspects of operations:
Enhanced Cleaning Efficiency with a Clean in Place (CIP) System
A clean in place cip system provides consistent and thorough cleaning, eliminating human error associated with manual cleaning. The automated process ensures that all surfaces are exposed to the cleaning solutions for the appropriate time and at the correct temperature and concentration. This leads to superior cleaning results compared to manual methods. This consistency is a primary benefit of a clean in place cip system.
Reduced Downtime with a Clean in Place (CIP) System
Manual cleaning requires significant downtime for disassembly, cleaning, and reassembly of equipment. A clean in place cip system significantly reduces downtime, as cleaning can be performed without interrupting production. This maximizes production time and increases overall efficiency. The time saved is a massive advantage of a clean in place cip system.
Improved Safety with a Clean in Place (CIP) System
Manual cleaning often involves handling hazardous chemicals and working in confined spaces, posing safety risks to personnel. A clean in place cip system minimizes human intervention, reducing exposure to chemicals and physical hazards. This creates a safer working environment. The increased safety is a huge benefit of a clean in place cip system.
Lower Operating Costs with a Clean in Place (CIP) System
While the initial investment in a clean in place cip system may seem significant, it leads to long-term cost savings. Reduced labor costs, lower water and chemical consumption, and minimized downtime contribute to significant operational savings. The long-term savings are a key advantage of a clean in place cip system.
Increased Product Quality with a Clean in Place (CIP) System
Effective cleaning is crucial for maintaining product quality and preventing contamination. A clean in place cip system ensures consistent and thorough cleaning, minimizing the risk of product spoilage and recalls. This protects brand reputation and customer trust. The improvement in product quality is a major benefit of a clean in place cip system.
Environmental Benefits of a Clean in Place (CIP) System
Optimized chemical and water usage in a clean in place cip system reduces environmental impact. Precise control of cleaning parameters minimizes waste and promotes sustainable practices. This efficiency is an environmental benefit of using a clean in place cip system.
Traceability and Validation with a Clean in Place (CIP) System
The automated nature of a clean in place cip system allows for detailed data logging and recording of cleaning parameters. This facilitates traceability and validation of cleaning processes, which is essential for regulatory compliance and quality assurance. This data tracking is a benefit of a clean in place cip system.
Clean in Place (CIP) System Design Considerations
When designing a clean in place cip system, several factors must be considered:
- Equipment Design: Equipment should be designed with CIP in mind, with smooth surfaces, minimal dead legs, and adequate drainage.
- Cleaning Solution Compatibility: The cleaning solutions must be compatible with the materials of construction of the equipment.
- Flow Rate and Pressure: The flow rate and pressure of the cleaning solutions must be sufficient to ensure effective cleaning.
- Temperatur: The temperature of the cleaning solutions must be optimized for the type of soiling.
- Cleaning Time: The cleaning time must be sufficient to achieve the desired level of cleanliness.
Clean in Place (CIP) System Applications Across Industries
Clean in place cip systems find applications in a wide range of industries:
- Essen und Trinken: Dairy, brewing, beverage, and food processing.
- Pharmazeutisch: Manufacturing of sterile and non-sterile drug products.
- Biotechnologie: Production of biopharmaceuticals and other biological products.
- Kosmetika: Manufacturing of personal care products.
Vergleich von Clean in Place (CIP) System Parameter
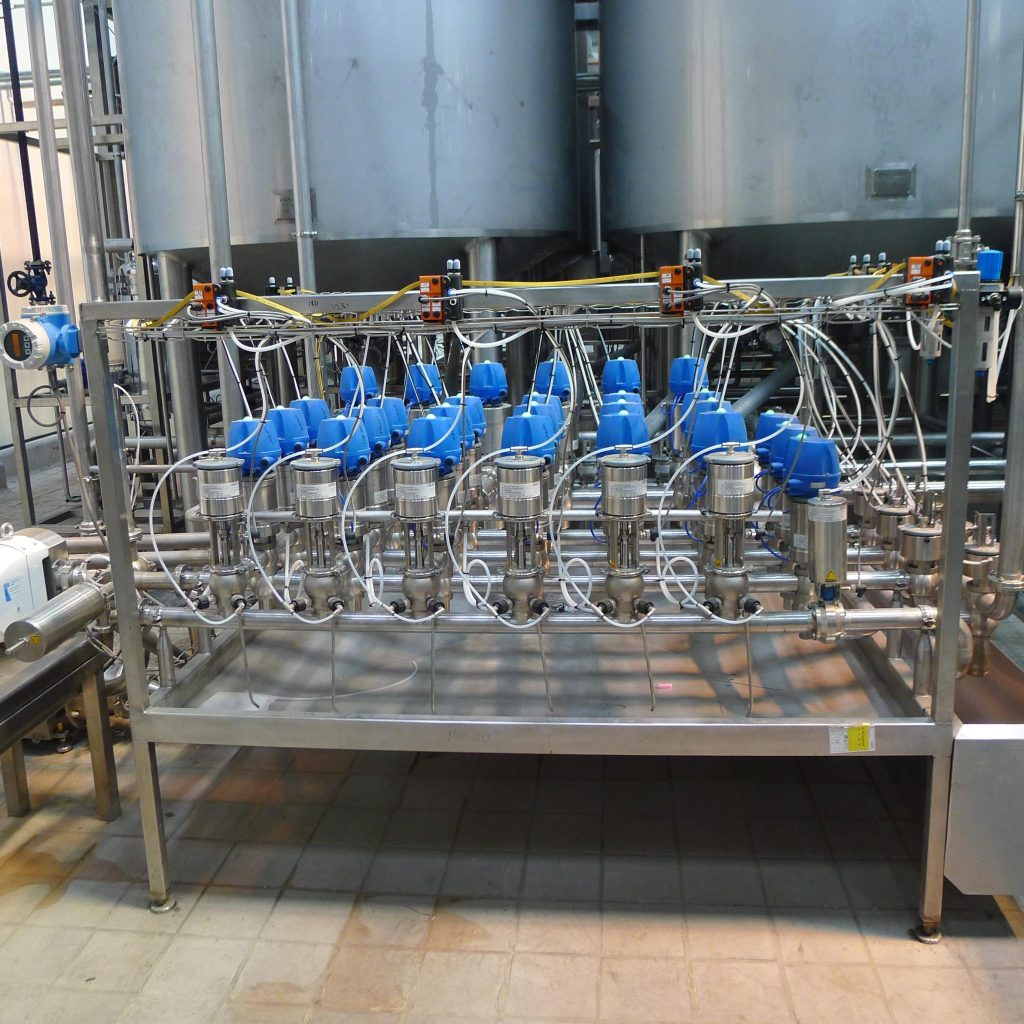
The following table presents a comparison of typical parameters for different stages of a clean in place cip system:
Cleaning Stage | Temperature (°C) | Time (minutes) | Chemical Concentration | Flow Velocity (m/s) |
---|---|---|---|---|
Pre-Rinse | Ambient | 5-10 | Wasser | 1.5-3.0 |
Caustic Wash | 60-80 | 15-30 | 1-3% NaOH | 1.5-3.0 |
Intermediate Rinse | Ambient | 5-10 | Wasser | 1.5-3.0 |
Acid Wash | 50-70 | 10-20 | 0.5-1.5% HNO3/H3PO4 | 1.5-3.0 |
Final Rinse | Ambient | 5-10 | Purified Water | 1.5-3.0 |
Desinfektion | 75-85 (Hot Water) | 15-20 | As per Manufacturer | 1.5-3.0 |
Abschluss
Implementierung einer clean in place cip system is a strategic investment that offers numerous benefits, including enhanced cleaning efficiency, reduced downtime, improved safety, lower operating costs, increased product quality, environmental advantages, and improved traceability. While the initial investment requires careful planning and design, the long-term benefits make a clean in place cip system a valuable asset for any industry where hygiene and sanitation are critical. By understanding the function and benefits of a clean in place cip system, businesses can make informed decisions to optimize their cleaning processes and improve
Häufig gestellte Fragen
What is the difference between CIP and COP?
CIP (Clean-in-Place) cleans equipment without disassembly, while COP (Clean-Out-of-Place) requires disassembly for cleaning.
Wie oft sollte KVP be performed?
The frequency depends on the specific application and product being processed. It can range from daily to weekly.
What are the key factors affecting CIP effectiveness?
Key factors include time, temperature, chemical concentration, and flow rate.
Is CIP suitable for all types of equipment?
While CIP is widely applicable, some equipment may require modification or manual cleaning due to design limitations.
How can CIP-Systeme be validated?
CIP systems can be validated by monitoring key parameters, conducting visual inspections, and performing microbial testing.