Introduction
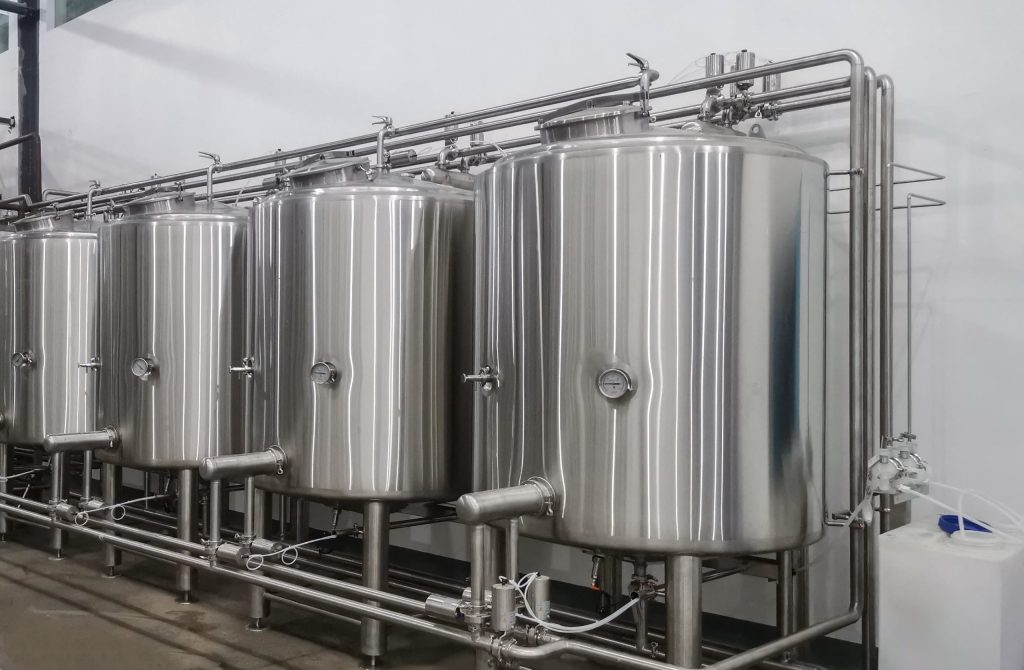
Clean in place (CIP) is a method of cleaning the interior surfaces of pipes, vessels, process equipment, filters and associated fittings, without disassembly. CIP has been used for many years in the food, beverage, dairy, pharmaceutical and other industries where hygiene is of utmost importance. The process is designed to remove product residues, biofilms and other contaminants from processing equipment, ensuring product quality and safety. Clean in place tanks are an integral part of this automated cleaning system, providing a reservoir for the cleaning solutions.
The Importance of Clean in Place Tanks in Hygienic Processing
Clean in place tanks are essential components in any CIP system. They are designed to hold and deliver the cleaning solutions used in the CIP process. These tanks are crucial for maintaining the efficacy and efficiency of the cleaning process. Without properly designed and maintained clean in place tanks, the CIP system may not effectively remove contaminants, leading to potential product contamination and safety issues.
Understanding the Clean in Place Process
The typical CIP process involves several steps:
- Pré-rinçage : This initial step removes gross soil and product residues with water.
- Caustic wash: A caustic solution (e.g., sodium hydroxide) is used to remove organic matter, such as fats and proteins.
- Intermediate rinse: Another water rinse removes the caustic solution and loosened soil.
- Acid wash: An acid solution (e.g., nitric acid or phosphoric acid) removes mineral deposits and scale.
- Final rinse: A final rinse with treated water (e.g., purified or potable water) removes any remaining cleaning solutions.
- Désinfection (facultatif) : A sanitizing agent may be used to further reduce microbial levels.
Clean in place tanks play a vital role in each of these stages by storing and supplying the necessary cleaning and rinsing solutions.
Design and Construction of Clean in Place Tank
The design and construction of clean in place tank are crucial for their effective operation. Several factors are considered during the design phase:
Materials of Construction for Clean in Place Tank
Stainless steel is the most common material used for clean in place tank due to its corrosion resistance, durability, and hygienic properties. Specifically, 304L and 316L stainless steel grades are preferred. 316L stainless steel offers superior corrosion resistance, particularly against chlorides, making it suitable for applications involving aggressive cleaning chemicals.
Tank Shape and Configuration
Clean in place tank typically come in vertical cylindrical or rectangular shapes. The design should minimize dead legs and areas where cleaning solutions can stagnate. Sloped bottoms and conical bottoms are often incorporated to facilitate complete drainage.
Agitation and Mixing Systems within Clean in Place Tank
Effective agitation or mixing within the clean in place tank is important to ensure a homogenous cleaning solution and prevent stratification. Agitation can be achieved through various methods, including mechanical agitators, recirculation pumps, or eductors.
Insulation and Temperature Control of Clean in Place Tank
Maintaining the correct temperature of the cleaning solutions is critical for optimal cleaning performance. Clean in place tank can be insulated to minimize heat loss and equipped with heating or cooling systems to maintain the desired temperature.
Operation and Maintenance of Clean in Place Tanks
Proper operation and maintenance are vital to ensure the longevity and effectiveness of clean in place tanks.
Monitoring Cleaning Solution Parameters in Clean in Place Tank
Regular monitoring of cleaning solution parameters, such as concentration, temperature, and conductivity, is essential. This ensures that the cleaning solutions are within the specified parameters for optimal cleaning.
Cleaning and Inspection of Clean in Place Tank
Clean in place tank themselves must be cleaned periodically to prevent the buildup of contaminants. Regular visual inspections should be conducted to check for any signs of corrosion, damage, or leaks.
Safety Considerations for Clean in Place Tank
Working with cleaning chemicals requires proper safety precautions. Appropriate personal protective equipment (PPE) should be worn, and safety procedures should be followed to minimize the risk of chemical exposure.
Applications de Clean in Place Tanks
Clean in place tanks are utilized in a variety of industries:
Industrie alimentaire et des boissons
In the food and beverage industry, clean in place tanks are used to clean processing equipment such as tanks, pipes, fillers, and heat exchangers.
Industrie pharmaceutique
The pharmaceutical industry relies on CIP systems and clean in place tanks to maintain stringent hygiene standards in the production of drugs and other pharmaceutical products.
Industrie laitière
Clean in place tanks are essential in dairy processing plants for cleaning equipment used in milk processing, cheese making, and other dairy product manufacturing.
Types of Clean in Place Systems and Their Tanks
CIP systems can be categorized into several types, each with its own specific requirements for clean in place tanks.
Single-Use CIP Systems
Single-use systems use cleaning solutions once and then discard them. These systems may use smaller, simpler clean in place tanks.
Re-Use CIP Systems
Re-use systems recover and reuse cleaning solutions for multiple cleaning cycles. These systems require larger, more complex clean in place tanks with features for solution storage, filtration, and reconditioning.
Multi-Tank CIP Systems
Multi-tank systems utilize multiple clean in place tanks to store different cleaning solutions, allowing for more complex cleaning cycles and greater flexibility.
Advantages and Disadvantages of Clean in Place Tanks
Clean in place tanks provide numerous advantages:
Advantages of Clean in Place Tanks
- Improved hygiene: CIP systems and clean in place tanks effectively remove contaminants, ensuring product safety and quality.
- Reduced downtime: CIP cleaning is faster and more efficient than manual cleaning, minimizing production downtime.
- Reduced labor costs: CIP systems automate the cleaning process, reducing the need for manual labor.
- Improved safety: CIP systems minimize worker exposure to cleaning chemicals.
- Consistency and repeatability: CIP processes can be precisely controlled, ensuring consistent and repeatable cleaning results.
Disadvantages of Clean in Place Tanks
- Initial investment: Implementing a CIP system and installing clean in place tanks requires a significant initial investment.
- Design complexity: Designing and installing a CIP system requires careful planning and engineering.
- Chemical usage: CIP systems use cleaning chemicals, which must be handled and disposed of properly.
Clean in Place Tank Tableau de comparaison

Fonctionnalité | Description |
---|---|
Matériel | Typically 304L or 316L stainless steel for corrosion resistance and hygiene. |
Forme | Usually vertical cylindrical or rectangular with sloped or conical bottoms for complete drainage. |
Capacité | Varies depending on the CIP system and application, ranging from small tanks for individual equipment to large tanks for entire processing lines. |
Agitation/Mixing | Mechanical agitators, recirculation pumps, or eductors to ensure homogenous cleaning solutions. |
Isolation | Optional insulation to minimize heat loss and maintain solution temperature. |
Heating/Cooling | Optional heating or cooling jackets or coils to control solution temperature. |
Connections | Connections for inlet, outlet, recirculation, and instrumentation. |
Instrumentation | Sensors and transmitters for monitoring parameters such as level, temperature, conductivity, and pressure. |
Cleaning/Inspection Access | Manways or other access points for internal inspection and cleaning. |
Des dispositifs de sécurité | Pressure relief valves, level alarms, and other safety devices to prevent accidents. |
Surface Finish | Smooth interior surface finish (e.g., electropolished) to prevent bacterial adhesion and facilitate cleaning. |
Automatisation | Integration with the CIP system control system for automated operation and data logging. |
Conformité | Compliance with relevant industry standards and regulations (e.g., 3-A Sanitary Standards, EHEDG guidelines). |
Considérations sur la conception | Minimizing dead legs, ensuring complete drainage, and providing adequate access for cleaning and inspection are important design considerations for clean in place tanks. The tank should be sized appropriately for the system, and all materials should be compatible with the cleaning solutions. |
Conclusion
Clean in place tanks are essential components of CIP systems, playing a crucial role in maintaining hygiene and product safety in various industries. Proper design, construction, operation, and maintenance of clean in place tanks are vital for their effectiveness and longevity. By understanding the key aspects of clean in place tanks and staying informed about emerging trends, businesses can ensure the efficient and reliable operation of their CIP systems and maintain the highest standards of hygiene and product quality.
FAQ
What is the purpose of a réservoir propre en place?
Clean in place tanks store and supply the cleaning solutions used in CIP systems.
What material are clean in place tanks made of?
Stainless steel, typically 304L or 316L, is the most common material.
How are clean in place tanks cleaned?
Clean in place tanks are cleaned as part of the overall CIP process, often using the same cleaning solutions used to clean the processing equipment.
What industries use clean in place tanks?
Clean in place tanks are used in industries with strict hygiene requirements, such as food and beverage, pharmaceutical, and dairy.
What is the difference between single-use and re-use CIP systems?
Single-use systems discard cleaning solutions after one use, while re-use systems recoverre-use cleaning solutions for multiple cycles.