introduzione
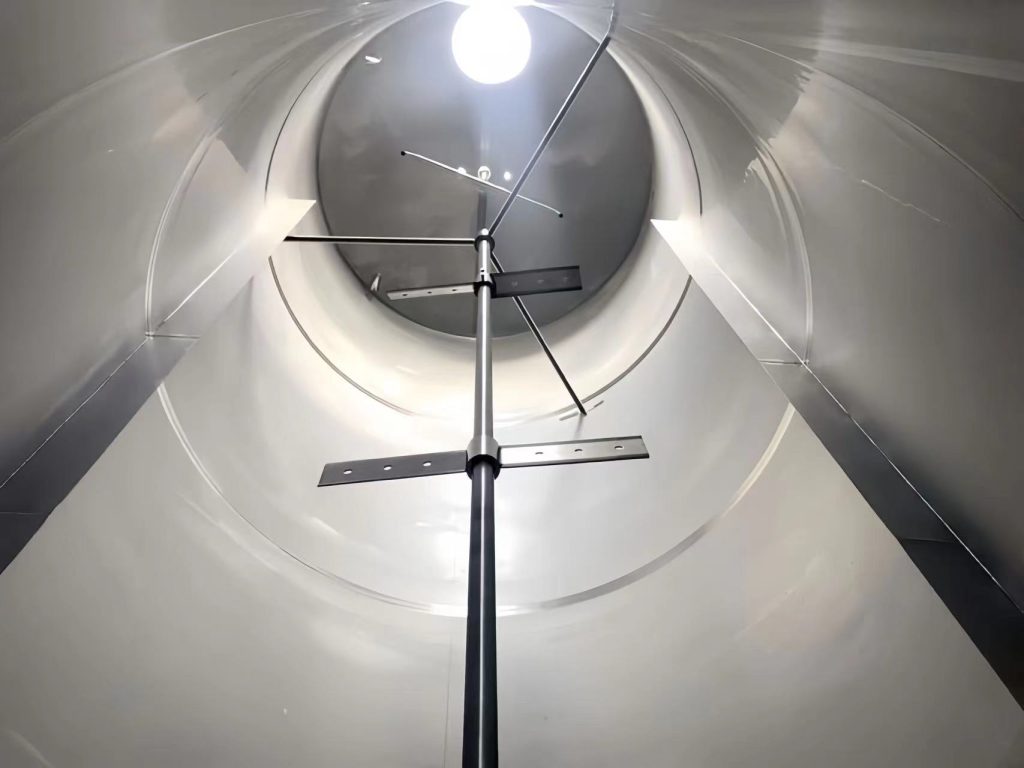
I serbatoi di miscelazione chimica sono componenti integrali in vari processi industriali, fondamentali per combinare diverse sostanze chimiche per ottenere una reazione o una proprietà desiderata. Svolgono un ruolo significativo in settori quali farmaceutica, chimica, alimentare e delle bevande e cosmetica. Comprendere le caratteristiche e i vantaggi principali dei serbatoi di miscelazione chimica è essenziale per ottimizzare le operazioni e garantire sicurezza ed efficienza. Questa guida completa esplorerà questi aspetti in dettaglio, fornendo preziose informazioni sulla funzionalità e sui vantaggi dei serbatoi di miscelazione chimica.
Comprensione Serbatoi di miscelazione chimica
I serbatoi di miscelazione chimica sono recipienti specializzati progettati per miscelare i prodotti chimici in modo efficiente e sicuro. Sono disponibili in varie dimensioni e configurazioni, su misura per specifici requisiti industriali. Questi serbatoi sono dotati di diverse caratteristiche per facilitare il processo di miscelazione, garantire uniformità e mantenere l'integrità delle sostanze chimiche coinvolte.
Tipi di serbatoi di miscelazione chimica
I serbatoi di miscelazione chimica sono categorizzati in base al design, all'applicazione e al tipo di miscelazione richiesta. I tipi più comuni includono:
- Serbatoi di miscelazione in lotti: Utilizzato per l'elaborazione di lotti discreti di prodotti chimici.
- Serbatoi di miscelazione continua: Progettato per processi di miscelazione continui e ininterrotti.
- Serbatoi di miscelazione ad alto taglio: Dotato di miscelatori ad alto taglio per la gestione di materiali viscosi.
- Miscelatori per serbatoi: Incorporare meccanismi di miscelazione per una miscelazione accurata e uniforme.
Caratteristiche principali dei serbatoi di miscelazione chimica
I serbatoi di miscelazione chimica sono dotati di varie caratteristiche per migliorare le loro prestazioni e la loro sicurezza. Alcune delle caratteristiche principali includono:
- Meccanismi di agitazione: Per garantire una corretta miscelazione vengono utilizzati diversi tipi di agitatori, come turbine ed eliche.
- Sistemi di controllo della temperatura: Include giacche riscaldanti e raffreddanti per mantenere la temperatura desiderata.
- Materiale di costruzione:I serbatoi sono spesso realizzati in acciaio inossidabile, acciaio smaltato o altri materiali resistenti alle reazioni chimiche.
- Caratteristiche di sicurezza: Include valvole di sicurezza, motori antideflagranti e sistemi di rilevamento delle perdite.
- Sistemi di pulizia: Sistemi di pulizia automatizzati (CIP) per garantire l'igiene e prevenire la contaminazione incrociata.
Vantaggi dell'utilizzo Serbatoi di miscelazione chimica
I serbatoi di miscelazione chimica offrono diversi vantaggi che migliorano i processi industriali. Comprendere questi vantaggi può aiutare le aziende a prendere decisioni informate sulle proprie apparecchiature di miscelazione.
Efficienza e coerenza
Uno dei principali vantaggi dei serbatoi di miscelazione chimica è la loro capacità di fornire una miscelazione efficiente e uniforme. Ciò è fondamentale per garantire che il prodotto finale soddisfi gli standard di qualità e funzioni come previsto. I meccanismi di agitazione avanzati e i sistemi di controllo precisi nei moderni serbatoi di miscelazione contribuiscono a questa uniformità.
Sicurezza e conformità
I serbatoi di miscelazione chimica sono progettati tenendo a mente la sicurezza. Sono dotati di varie caratteristiche di sicurezza per gestire sostanze chimiche pericolose e prevenire incidenti. La conformità alle normative e agli standard del settore è inoltre garantita tramite l'uso di materiali robusti e meccanismi di sicurezza.
Flessibilità e personalizzazione
I serbatoi di miscelazione chimica offrono flessibilità nella progettazione e nel funzionamento. Possono essere personalizzati per soddisfare requisiti di processo specifici, tra cui dimensioni variabili, velocità di agitazione e controlli della temperatura. Questa versatilità li rende adatti a un'ampia gamma di applicazioni e settori.
Efficacia dei costi
Investire in serbatoi di miscelazione chimica di alta qualità può portare a risparmi sui costi a lungo termine. Processi di miscelazione efficienti riducono gli sprechi e migliorano la resa del prodotto, il che può abbassare i costi operativi. Inoltre, la durata e l'affidabilità di questi serbatoi riducono al minimo le spese di manutenzione e sostituzione.
Considerazioni chiave quando si sceglie un Serbatoio di miscelazione chimica
La scelta del serbatoio di miscelazione chimica giusto comporta diverse considerazioni per garantire prestazioni e sicurezza ottimali. I fattori chiave da considerare includono:
Compatibilità chimica
Il materiale del serbatoio di miscelazione deve essere compatibile con i prodotti chimici in lavorazione. Ciò impedisce la corrosione, la contaminazione e la degradazione del serbatoio. L'acciaio inossidabile e l'acciaio smaltato sono materiali comunemente utilizzati per la loro resistenza alle reazioni chimiche.
Dimensioni e capacità del serbatoio
Le dimensioni e la capacità del serbatoio devono essere in linea con i requisiti di produzione. I serbatoi più grandi sono adatti per processi ad alto volume, mentre i serbatoi più piccoli sono ideali per l'elaborazione in batch. È importante considerare la scalabilità del serbatoio per adattarsi alla crescita futura.
Requisiti di agitazione
Processi diversi richiedono tipi diversi di agitazione. La scelta dell'agitatore, come un miscelatore a pale, a elica o ad alto taglio, dovrebbe basarsi sulla viscosità e sulle proprietà delle sostanze chimiche da miscelare. Un'agitazione corretta assicura una miscelazione uniforme e un'elaborazione efficace.
Esigenze di controllo della temperatura
Il controllo della temperatura è fondamentale per alcune reazioni chimiche. I serbatoi dotati di camicie di riscaldamento o raffreddamento aiutano a mantenere la temperatura desiderata, assicurando condizioni di reazione ottimali e qualità del prodotto.
Manutenzione e pulizia
La facilità di manutenzione e pulizia è un fattore importante da considerare. I sistemi di pulizia automatizzata in loco (CIP) possono semplificare il processo di pulizia, riducendo i tempi di fermo e garantendo l'igiene. Dovrebbero anche essere stabiliti programmi di manutenzione regolari per prolungare la durata del serbatoio.
Applicazioni di Serbatoi di miscelazione chimica
I serbatoi di miscelazione chimica sono utilizzati in vari settori e applicazioni. La comprensione di queste applicazioni può fornire spunti sulla versatilità e l'importanza di questi serbatoi.
Industria farmaceutica
Nell'industria farmaceutica, i serbatoi di miscelazione chimica vengono utilizzati per la produzione di farmaci e vaccini. Una miscelazione precisa è essenziale per mantenere coerenza ed efficacia. I serbatoi in questo settore richiedono spesso elevati livelli di igiene e sterilizzazione.
Produzione chimica
I serbatoi di miscelazione chimica svolgono un ruolo cruciale nella produzione di vari prodotti chimici, tra cui prodotti chimici speciali, detergenti e polimeri. La capacità di gestire sostanze corrosive e reattive è importante in questo settore.
Industria alimentare e delle bevande
Nel settore alimentare e delle bevande, i serbatoi di miscelazione chimica vengono utilizzati per miscelare ingredienti, aromatizzare e processare. La conformità agli standard di sicurezza alimentare e la capacità di gestire diverse viscosità sono considerazioni chiave.
Cosmetici e cura della persona
I serbatoi di miscelazione chimica sono utilizzati nell'industria cosmetica per la produzione di lozioni, creme e altri prodotti per la cura della persona. Coerenza e controllo della qualità sono essenziali in questo settore per soddisfare le aspettative dei consumatori.
Problemi comuni e risoluzione dei problemi
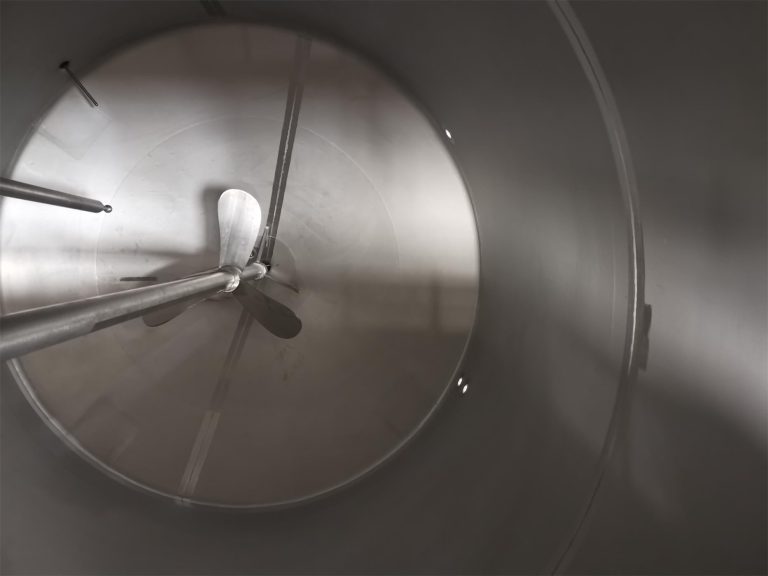
Sebbene i serbatoi di miscelazione chimica siano progettati per essere affidabili, durante il funzionamento potrebbero verificarsi alcuni problemi. Comprendere i problemi comuni e le relative soluzioni può aiutare a mantenere prestazioni ottimali.
Perdite e guarnizioni
Le perdite possono verificarsi a causa di guarnizioni usurate o installazione non corretta. L'ispezione e la manutenzione regolari di guarnizioni e guarnizioni sono essenziali per prevenire perdite e garantire il corretto contenimento delle sostanze chimiche.
Problemi di agitazione
Una miscelazione inadeguata può derivare da agitatori malfunzionanti o impostazioni non corrette. Controllare l'agitatore per eventuali danni e regolare la velocità o il tipo di agitazione può risolvere questi problemi.
Fluttuazioni della temperatura
Le fluttuazioni di temperatura possono influire sulla qualità del prodotto miscelato. Assicurare che i sistemi di controllo della temperatura funzionino correttamente e calibrarli regolarmente può prevenire questi problemi.
Conclusione
Serbatoi di miscelazione chimica sono componenti essenziali in un'ampia gamma di processi industriali. Le loro caratteristiche principali, come meccanismi di agitazione avanzati, sistemi di controllo della temperatura e funzioni di sicurezza, contribuiscono a una miscelazione efficiente e costante. Comprendere i vantaggi e le considerazioni associate a questi serbatoi può aiutare le aziende a selezionare l'attrezzatura giusta per le loro esigenze, garantendo sicurezza, qualità ed economicità.
Considerando fattori quali compatibilità chimica, dimensioni del serbatoio e requisiti di agitazione, le aziende possono ottimizzare i loro processi di miscelazione e ottenere risultati migliori. Con una corretta manutenzione e risoluzione dei problemi, i serbatoi di miscelazione chimica possono fornire prestazioni affidabili e supportare varie applicazioni industriali.
FAQ
Quali sono i principali tipi di serbatoi di miscelazione chimica?
I principali tipi di serbatoi di miscelazione chimica includono serbatoi di miscelazione a lotti, serbatoi di miscelazione continua, serbatoi di miscelazione ad alto taglio e miscelatori di serbatoi. Ogni tipo è adatto a diverse applicazioni e requisiti di miscelazione.
Come faccio a scegliere il serbatoio di miscelazione chimica più adatto alle mie esigenze?
Quando si sceglie un serbatoio di miscelazione chimica, occorre considerare fattori quali la compatibilità chimica, le dimensioni e la capacità del serbatoio, i requisiti di agitazione, le esigenze di controllo della temperatura e la facilità di manutenzione.
Quali materiali sono comunemente utilizzati per serbatoi di miscelazione chimica?
I materiali comuni utilizzati per i serbatoi di miscelazione chimica includono acciaio inossidabile, acciaio smaltato e altri materiali resistenti alle reazioni chimiche. La scelta del materiale dipende dalle sostanze chimiche in lavorazione.
Quali sono le caratteristiche di sicurezza dei serbatoi di miscelazione chimica?
Le caratteristiche di sicurezza dei serbatoi di miscelazione chimica includono valvole di sicurezza, motori antideflagranti, sistemi di rilevamento delle perdite e materiali di costruzione robusti per gestire sostanze chimiche pericolose.
Come posso mantenere e pulire un serbatoio di miscelazione chimica?
La manutenzione e la pulizia comportano l'ispezione regolare di guarnizioni e sigilli, il controllo della funzionalità dell'agitatore e l'uso di sistemi di pulizia automatizzati in loco (CIP) per l'igiene. L'impostazione di un programma di manutenzione può prolungare la durata del serbatoio.