introduzione
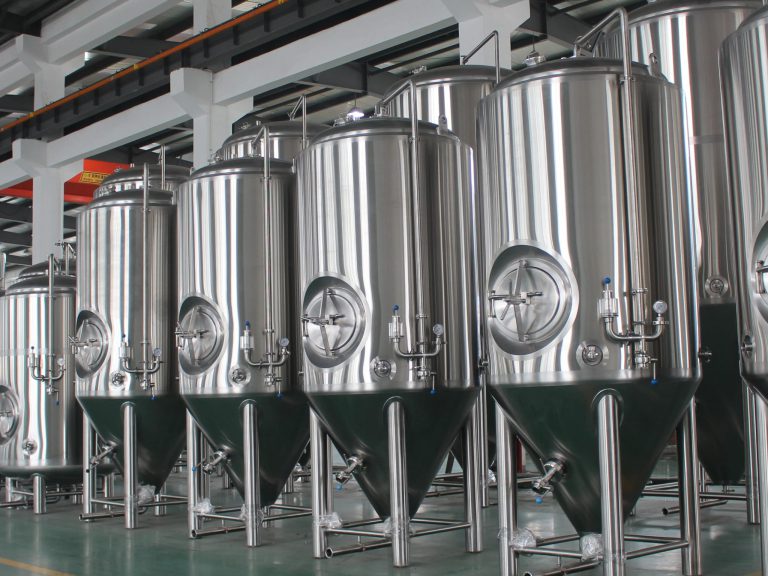
Nel competitivo mondo della produzione della birra, l'efficienza non riguarda solo la produzione di un'ottima birra; riguarda anche quanto bene si possono semplificare i processi di produzione per soddisfare la domanda senza compromettere la qualità. Le attrezzature per la produzione di birra industriale hanno rivoluzionato il settore, fornendo ai birrifici strumenti e tecnologie avanzati che migliorano significativamente l'efficienza produttiva. Questo blog esplora come investire in attrezzature per la produzione di birra industriale può portare a miglioramenti sostanziali nelle operazioni di produzione della birra, dall'aumento della produzione all'ottimizzazione del controllo di qualità.
Comprensione Attrezzatura per la produzione di birra industriale
Le attrezzature industriali per la produzione di birra si riferiscono ai macchinari e ai sistemi su larga scala utilizzati nella produzione di birra. Ciò include tutto, dai bollitori e fermentatori di birra ai sistemi di controllo automatizzati e alle linee di confezionamento. Questi pezzi di attrezzatura sono progettati per gestire grandi volumi e processi complessi con precisione e affidabilità.
Tipi di attrezzature per la produzione di birra industriale
- Bollitori per la preparazione del caffè: Vengono utilizzati per far bollire il mosto, a cui viene aggiunto il luppolo per infondere aromi.
- Fermentatori: Essenziali per la fermentazione, questi recipienti consentono al lievito di convertire gli zuccheri in alcol e carbonatazione.
- Scambiatori di calore: Utilizzato per raffreddare il mosto prima della fermentazione.
- Carri armati Brite: Utilizzato per il condizionamento della birra prima del confezionamento.
- Sistemi di controllo automatizzati:Questi sistemi gestiscono vari aspetti del processo di fermentazione, tra cui temperatura, pressione e tempistica.
- Linee di confezionamento: Macchine che gestiscono l'imbottigliamento, l'inscatolamento o l'infustamento del prodotto finale.
Come Attrezzatura per la produzione di birra industriale Migliora l'efficienza produttiva
Aumento della capacità produttiva
Uno dei vantaggi più significativi delle attrezzature industriali per la produzione di birra è l'aumento della capacità produttiva. I sistemi ad alto volume, come i fermentatori su larga scala e i bollitori di produzione automatizzati, consentono ai birrifici di produrre costantemente lotti di birra più grandi. Questa scalabilità è fondamentale per soddisfare le crescenti richieste del mercato e ottenere economie di scala.
Precisione e coerenza migliorate
Le attrezzature industriali per la produzione di birra offrono sistemi di controllo avanzati che assicurano un monitoraggio e una regolazione precisi dei parametri di produzione. Ad esempio, i controlli automatici di temperatura e pressione mantengono le condizioni ottimali per la fermentazione e la produzione. Questa precisione porta a una qualità del prodotto costante, riducendo le variazioni tra i lotti e assicurando che ogni birra soddisfi le specifiche desiderate.
Processi di produzione semplificati
L'automazione svolge un ruolo chiave nel migliorare l'efficienza riducendo il lavoro manuale e minimizzando l'errore umano. I sistemi automatizzati possono gestire attività come il dosaggio degli ingredienti, la regolazione della temperatura e la tempistica, il che velocizza il processo di fermentazione e riduce la necessità di una supervisione costante. Ciò consente ai birrai di concentrarsi su altri aspetti della produzione e della garanzia della qualità.
Efficienza energetica migliorata
Le moderne attrezzature industriali per la produzione di birra sono progettate tenendo a mente l'efficienza energetica. Gli scambiatori di calore, ad esempio, recuperano e riutilizzano il calore dal processo di produzione, riducendo il consumo di energia. Inoltre, pompe e motori a risparmio energetico riducono il consumo di elettricità, contribuendo al risparmio complessivo sui costi e a un impatto ambientale minore.
Controllo di qualità migliorato
Il controllo qualità è fondamentale nella produzione della birra e le attrezzature industriali forniscono strumenti per un monitoraggio e un'analisi precisi. Sensori avanzati e sistemi automatizzati possono tracciare vari parametri, come livelli di pH, gravità e temperatura, in tempo reale. Questi dati consentono ai birrifici di identificare e affrontare rapidamente eventuali deviazioni dagli standard qualitativi desiderati, garantendo un prodotto costantemente di alta qualità.
Tempi di produzione più rapidi
Le attrezzature industriali per la produzione di birra sono progettate per accelerare il processo di produzione. Tempi di riscaldamento e raffreddamento più rapidi, combinati con sistemi di fermentazione e condizionamento efficienti, riducono il tempo complessivo necessario per produrre birra. Questa rapida inversione di tendenza non solo aumenta la capacità produttiva, ma consente anche ai birrifici di rispondere più rapidamente alle richieste e alle tendenze del mercato.
Costi operativi ridotti
Sebbene l'investimento iniziale in attrezzature per la produzione di birra industriale possa essere significativo, i risparmi a lungo termine possono essere sostanziali. Costi di manodopera ridotti, consumi energetici inferiori e sprechi ridotti al minimo contribuiscono tutti a ridurre i costi operativi. Inoltre, l'aumento dell'efficienza produttiva consente ai birrifici di massimizzare il loro potenziale di fatturato e migliorare la redditività.
Analisi comparativa: tradizionale vs. Attrezzatura per la produzione di birra industriale
Aspetto | Attrezzatura tradizionale | Attrezzature industriali |
---|---|---|
Capacità produttiva | Da basso a moderato | Alto |
Precisione e coerenza | Variabile | Alto |
Livello di automazione | Basso | Alto |
Efficienza energetica | Inferiore | Più alto |
Controllo di qualità | Manuale | Automatizzato |
Tempo di consegna della produzione | Più a lungo | Più breve |
Costi operativi | Più alto | Inferiore |
Casi di studio: storie di successo di birrifici che utilizzano Attrezzature industriali
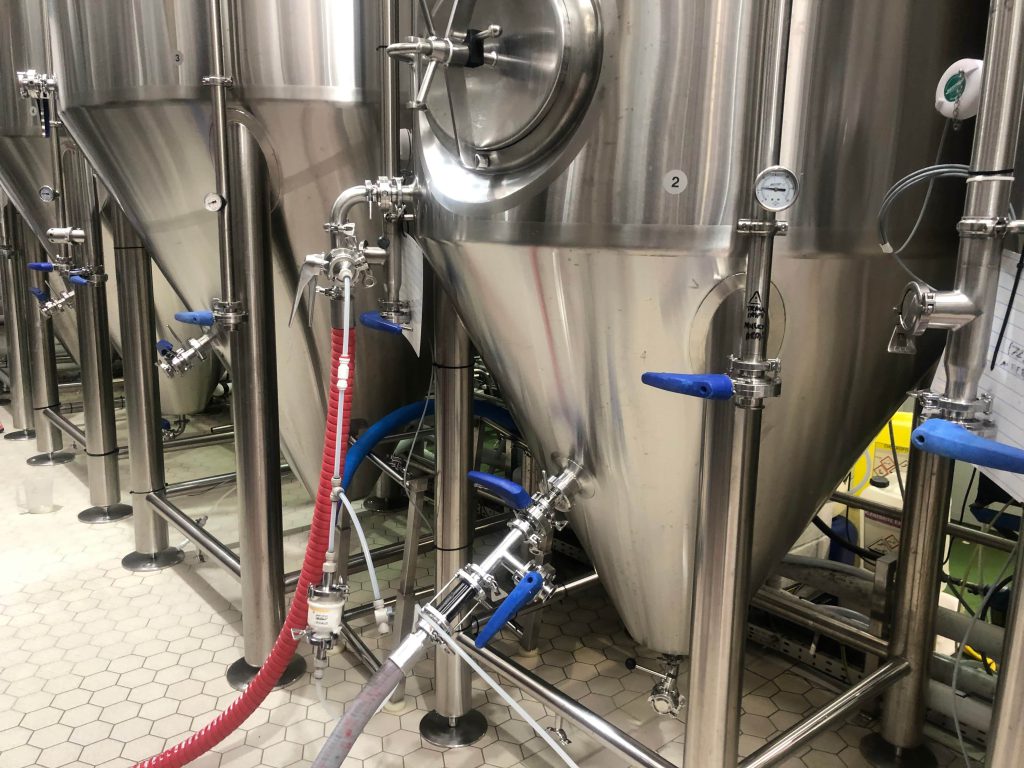
Caso di studio: Birrificio Brewing Legends
Brewing Legends Brewery, un affermato birrificio artigianale con sede a Portland, Oregon, ha compiuto un notevole passo avanti nella tecnologia di produzione investendo in un sistema di birrificazione all'avanguardia. Questo aggiornamento includeva bollitori di birrificazione automatizzati all'avanguardia e fermentatori avanzati, progettati per gestire con precisione la produzione di grandi volumi.
Risultati:
- Aumento della capacità produttiva:Nel giro di sei mesi dall'installazione, Brewing Legends Brewery ha registrato un aumento della capacità produttiva di 30%, consentendole di soddisfare la crescente domanda delle sue birre chiare e chiare di punta.
- Riduzione dei costi energetici:Il nuovo sistema ha portato a una riduzione del 20% dei costi energetici grazie al miglioramento dell'efficienza energetica e all'implementazione di sistemi di recupero del calore.
- Coerenza e qualità migliorate: L'automazione ha svolto un ruolo cruciale nel ridurre i costi di manodopera e garantire la coerenza del prodotto. Questo miglioramento nel controllo di qualità ha portato a una maggiore soddisfazione del cliente e a una presenza più forte sul mercato.
Caso di studio: Birrificio Hop Haven
Hop Haven Brewery, situata a Denver, Colorado, ha dovuto affrontare sfide legate ai colli di bottiglia nella sua linea di produzione. Per risolvere il problema, ha investito in una nuova linea di confezionamento ad alta velocità progettata per semplificare il processo di imbottigliamento e migliorare l'efficienza complessiva.
Risultati:
- Velocità di confezionamento migliorata:La nuova attrezzatura ha aumentato la velocità di confezionamento di 50%, incrementando significativamente la loro capacità di soddisfare la crescente domanda delle loro popolari varietà IPA e stout.
- Crescita dei ricavi: Grazie all'efficienza e alla capacità migliorate, Hop Haven Brewery ha ottenuto un aumento di 25% nel fatturato annuo. Questa crescita è stata attribuita sia alle capacità di produzione migliorate sia alla capacità di capitalizzare le opportunità di mercato senza compromettere la qualità del prodotto.
Conclusione
Investire in attrezzatura per la produzione di birra industriale offre numerosi vantaggi che possono migliorare significativamente l'efficienza produttiva. Dall'aumento della capacità produttiva e della precisione migliorata alla riduzione dei costi operativi e ai tempi di consegna più rapidi, questi progressi sono fondamentali per rimanere competitivi nel settore della birra. Sfruttando le tecnologie e le attrezzature più recenti, i birrifici possono non solo soddisfare ma anche superare le richieste del mercato mantenendo elevati standard qualitativi.
FAQ
Qual è il vantaggio principale di attrezzatura per la produzione di birra industriale?
Il vantaggio principale è l'aumento dell'efficienza produttiva, che si traduce in una maggiore capacità produttiva, una migliore precisione e costi operativi ridotti.
In che modo l'automazione influisce sulle attività di produzione della birra?
L'automazione riduce il lavoro manuale, riduce al minimo l'errore umano e velocizza i processi di produzione, garantendo una qualità del prodotto più costante e costi di manodopera inferiori.
Ci sono benefici ambientali nell'uso attrezzatura per la produzione di birra industriale?
Sì, le attrezzature moderne sono progettate per essere più efficienti dal punto di vista energetico, il che riduce il consumo energetico complessivo e minimizza l'impatto ambientale delle attività di produzione della birra.
Quali sono i tipi più comuni di attrezzature industriali per la produzione di birra?
Tra le tipologie più comuni rientrano bollitori per la produzione della birra, fermentatori, scambiatori di calore, serbatoi di brillantatura, sistemi di controllo automatizzati e linee di confezionamento.
Come può attrezzatura per la produzione di birra industriale migliorare il controllo di qualità?
Sensori avanzati e sistemi automatizzati garantiscono il monitoraggio in tempo reale di vari parametri di fermentazione, consentendo un controllo preciso e una qualità costante del prodotto.
Vale la pena investire in attrezzature per la produzione di birra industriale per i piccoli birrifici?
Sebbene l'investimento iniziale possa essere elevato, i vantaggi a lungo termine, come l'aumento dell'efficienza e la riduzione dei costi operativi, possono renderlo un investimento utile per i piccoli birrifici che mirano ad ampliare le proprie attività.