introduzione
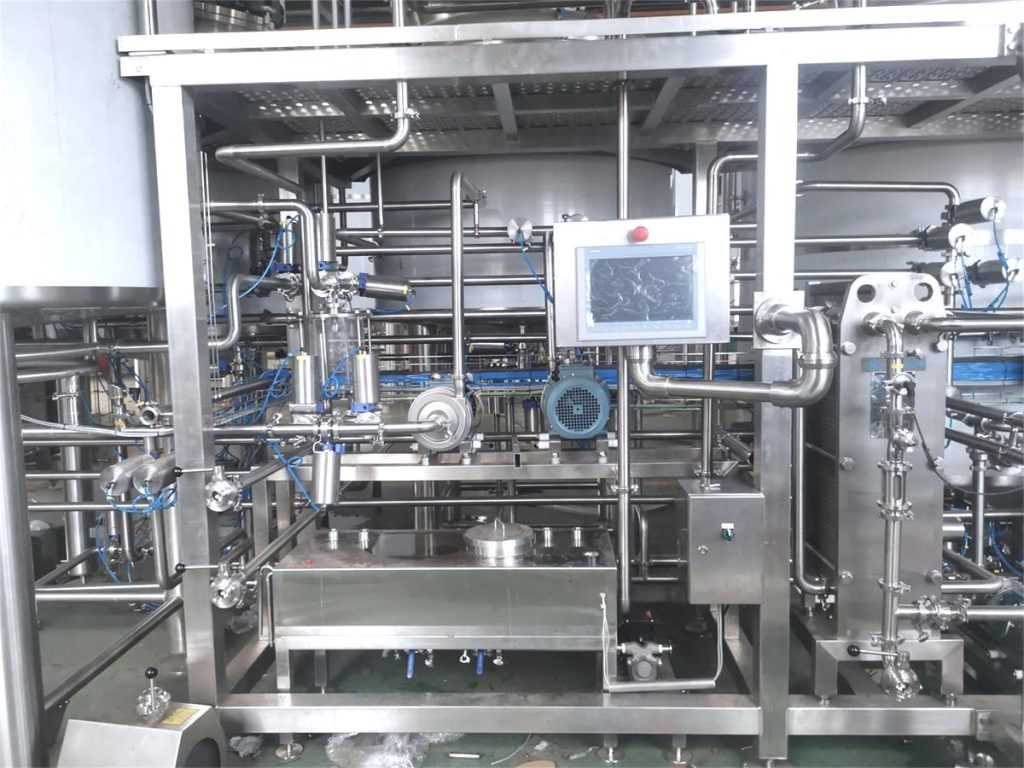
Nei settori in cui il vapore viene utilizzato per vari processi, la gestione efficiente della condensa di vapore è fondamentale per ragioni sia operative che ambientali. Le pompe di ritorno della condensa di vapore svolgono un ruolo fondamentale nel migliorare l'efficienza energetica restituendo il vapore condensato (condensa) al sistema di alimentazione della caldaia. Questo blog esplora l'importanza di queste pompe, la loro funzionalità e il modo in cui contribuiscono a pratiche industriali sostenibili.
Comprensione Pompe di ritorno della condensa del vapore
Cosa sono le pompe di ritorno della condensa del vapore?
Le pompe di ritorno della condensa di vapore sono dispositivi meccanici utilizzati per raccogliere e riportare la condensa dai sistemi a vapore alla caldaia o ad altre parti del sistema dove può essere riutilizzata. Questo processo è fondamentale per risparmiare energia e ridurre il consumo di acqua in contesti industriali.
Come funzionano le pompe di ritorno della condensa del vapore?
Queste pompe funzionano in genere sfruttando la differenza di pressione tra il sistema del vapore e la linea di ritorno della condensa. Sono progettate per gestire la condensa calda, spesso miscelata con vapore flash, e possono variare in dimensioni e capacità a seconda dell'applicazione specifica e dei requisiti del sistema.
Benefici di Pompe di ritorno della condensa del vapore
Efficienza energetica migliorata
Le pompe di ritorno del condensato di vapore aiutano a migliorare l'efficienza energetica recuperando e riutilizzando il condensato caldo che altrimenti andrebbe perso. Ciò riduce la necessità di riscaldare l'acqua fredda per l'alimentazione della caldaia, riducendo così il consumo di carburante e i costi operativi.
Impatto ambientale
Riducendo il consumo energetico, queste pompe contribuiscono anche a ridurre le emissioni di gas serra e l'impatto ambientale complessivo associato alle operazioni industriali. Ciò è in linea con gli obiettivi di sostenibilità e i requisiti di conformità normativa.
Componenti chiave e considerazioni di progettazione
Componenti di una pompa di ritorno della condensa del vapore
Componente | Funzione |
---|---|
Corpo pompa | Racchiude la girante e dirige il flusso |
Girante | Ruota per impartire energia al fluido |
Cuscinetti | Supportare l'albero e ridurre l'attrito |
Foche | Prevenire perdite lungo l'albero |
Meccanismo di controllo | Regola il funzionamento della pompa e la portata |
considerazioni sul design
- Selezione del materiale: I materiali resistenti alla corrosione sono essenziali a causa della natura calda e spesso chimicamente aggressiva della condensa. L'acciaio inossidabile e l'acciaio inossidabile duplex sono comunemente scelti per la loro resistenza alla corrosione e alle alte temperature. Inoltre, rivestimenti come epossidici o ceramici possono essere applicati alle superfici interne per proteggere ulteriormente dalla corrosione, prolungando la durata della pompa e riducendo i costi di manutenzione.
- Dimensioni e capacità: Un dimensionamento corretto assicura prestazioni ottimali e longevità della pompa, soddisfacendo al contempo le richieste del sistema. Ciò comporta il calcolo della portata di condensa in base ai tassi di consumo di vapore e tenendo conto di fattori quali periodi di picco della domanda e cadute di pressione. La scelta di una pompa con capacità adeguata impedisce il sovraccarico del sistema e garantisce un funzionamento costante in condizioni variabili, migliorando così l'efficienza e l'affidabilità complessive.
- Luogo di installazione: Posizionare correttamente la pompa riduce al minimo le perdite di tubazione e garantisce un funzionamento efficiente. Idealmente, la pompa dovrebbe essere installata vicino al punto di raccolta della condensa per ridurre al minimo la prevalenza di aspirazione e il consumo energetico. Inoltre, posizionare la pompa a un'altezza sufficiente sopra la linea di ritorno della condensa aiuta a mantenere un NPSH (Net Positive Suction Head) adeguato e previene la cavitazione, che può danneggiare la pompa nel tempo. Un'installazione corretta include anche garantire l'accessibilità per scopi di manutenzione e monitoraggio, facilitando la risoluzione dei problemi e la manutenzione tempestive.
Suggerimenti per la manutenzione e l'uso
Pratiche di manutenzione
Una manutenzione regolare è essenziale per garantire la longevità e l'efficienza delle pompe di ritorno del condensato di vapore. Ciò include:
- Controllo e sostituzione di guarnizioni e cuscinetti.
- Monitoraggio delle prestazioni e dell'efficienza della pompa.
- Ispezione periodica dei componenti della pompa per verificarne l'usura.
Suggerimenti operativi
- Esecuzione di indagini sulle trappole di condensa per ridurre al minimo le perdite di vapore.
- Monitoraggio delle velocità di ritorno della condensa per identificare inefficienze.
- Effettuare regolarmente corsi di formazione per gli operatori sul corretto funzionamento e manutenzione delle pompe.
Casi di studio e applicazioni nel mondo reale
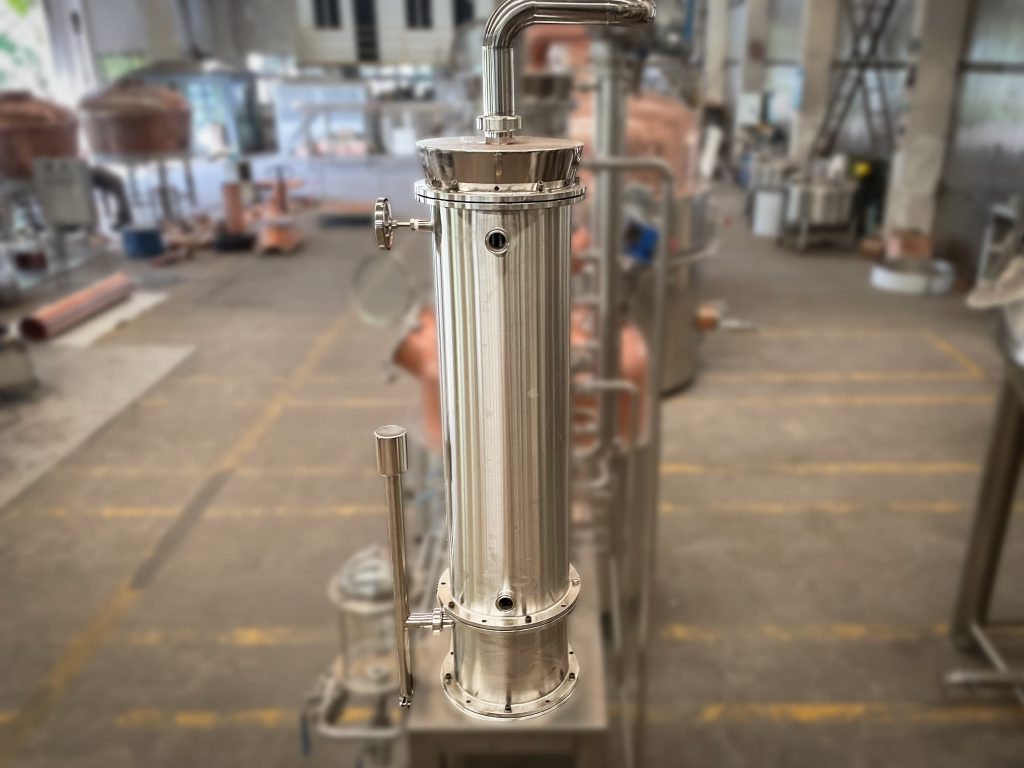
Stabilimento di produzione tessile
In uno stabilimento di produzione tessile, l'installazione di pompe di ritorno della condensa del vapore ha portato a una riduzione del consumo di carburante pari a 15% ottimizzando le temperature dell'acqua di alimentazione della caldaia.
Stabilimento di lavorazione alimentare
In uno stabilimento di lavorazione alimentare, l'aggiornamento a pompe di ritorno della condensa ad alta efficienza ha portato a un risparmio annuo di oltre $50.000 sui costi energetici.
Conclusione
Pompe di ritorno condensa vapore sono parte integrante del miglioramento dell'efficienza energetica nei sistemi industriali a vapore. Recuperando e riutilizzando la condensa, queste pompe aiutano a ridurre il consumo energetico, i costi operativi e a minimizzare l'impatto ambientale. Una progettazione, una manutenzione e delle pratiche operative adeguate sono fondamentali per massimizzare i vantaggi di queste pompe in contesti industriali.
FAQ
D:Qual è lo scopo di a pompa di ritorno condensa vapore?
A: Le pompe di ritorno della condensa del vapore vengono utilizzate per raccogliere e restituire il vapore condensato (condensa) al sistema di alimentazione dell'acqua della caldaia, riducendo il consumo di energia e migliorando l'efficienza.
D: In che modo le pompe di ritorno della condensa del vapore contribuiscono all'efficienza energetica?
R: Recuperando e riutilizzando la condensa calda, queste pompe riducono la necessità di riscaldare l'acqua fredda per l'alimentazione della caldaia, riducendo così il consumo di carburante e i costi operativi.
D: Quali sono alcune considerazioni chiave sulla progettazione per pompe di ritorno condensa vapore?
R: Tra le considerazioni importanti rientrano la scelta del materiale per la resistenza alla corrosione, il dimensionamento corretto per prestazioni ottimali e la corretta installazione per ridurre al minimo le perdite nelle tubazioni.