Introdução
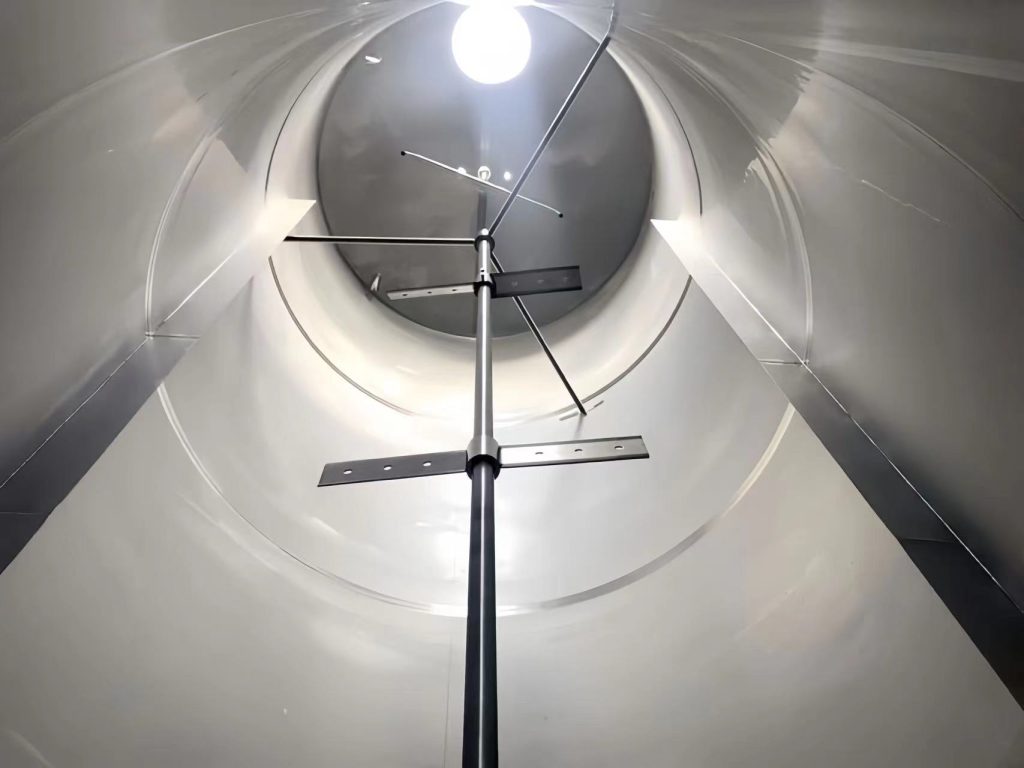
Mixer tanks are indispensable in a wide range of industries, from food and beverage production to pharmaceuticals and chemical processing. These tanks play a crucial role in blending, mixing, and storing various substances, ensuring uniformity, consistency, and quality in the final product. They are the workhorses of countless production lines, enabling manufacturers to create everything from the simplest beverages to the most complex pharmaceutical compounds. In this comprehensive blog post, we will delve into the numerous benefits of using mixer tanks, exploring their diverse applications, distinct advantages, key features to consider, and best practices for maintenance and safety. Understanding the intricacies of mixer tank technology can empower businesses to optimize their processes and achieve superior product outcomes.
What is a Mixer Tank and How Does it Work?
A mixer tank, also known as a mixing tank or blending tank, is a container specifically designed to hold liquids, or a combination of liquids and solids, while being agitated by a mixer. The mixer, typically powered by an electric motor, creates a rotational motion that facilitates the blending of the substances within the tank. This agitation can range from gentle stirring to high-shear mixing, depending on the specific requirements of the process. Mixer tanks come in various sizes, shapes (cylindrical, conical, etc.), and configurations, each tailored to specific applications and mixing requirements. The internal design of the tank, including baffles or other flow-directing elements, plays a crucial role in optimizing the mixing process and preventing vortex formation. The materials of construction, such as stainless steel or specialized polymers, are chosen based on the chemical compatibility of the substances being mixed and the desired level of hygiene.
Tipos de Tanques de mistura and Their Applications
Mixing tanks are available in a variety of designs, each suited to different mixing needs. Some common types include:
- Top-entry mixing tanks: These tanks have the mixer mounted on top, making them ideal for applications where headroom is not a constraint. They are often used for larger tanks and can accommodate a wide range of impeller types.
- Side-entry mixing tanks: These tanks have the mixer mounted on the side, making them suitable for low-headroom applications. They are often used for viscous liquids and can be more energy-efficient than top-entry mixers in certain situations.
- Bottom-entry mixing tanks: These tanks have the mixer mounted at the bottom, making them ideal for applications where complete drainage is required. They are often used in pharmaceutical and food processing where minimizing product loss is essential.
Mixing tanks find applications in a diverse range of industries, including:
- Food and beverage: Blending ingredients for sauces, mixing beverages, preparing dairy products, and creating emulsions for salad dressings.
- Produtos farmacêuticos: Mixing active ingredients, preparing solutions for intravenous fluids, blending powders for capsules, and creating creams and ointments.
- Chemical processing: Mixing chemicals for reactions, blending polymers for plastics, preparing emulsions for paints, and creating solutions for cleaning products.
- Cosméticos: Blending ingredients for lotions and creams, preparing fragrances, mixing pigments for makeup, and creating shampoos and conditioners.
- Water Treatment: Mixing chemicals for water purification, flocculation, and disinfection.
- Agricultura: Preparing fertilizers and pesticides, mixing animal feed, and creating solutions for irrigation.
Benefits of Using a Mixer Tank
Mixer tanks offer a multitude of benefits, including:
- Improved product quality: Mixer tanks ensure uniform mixing, resulting in consistent product quality and performance. This uniformity is critical for achieving desired characteristics such as color, texture, and efficacy.
- Enhanced efficiency: Mixer tanks can significantly reduce mixing time compared to manual methods, leading to increased productivity and cost savings. This efficiency translates to faster production cycles and optimized resource utilization.
- Versatilidade: Mixer tanks can handle a wide range of materials, from low-viscosity liquids to highly viscous pastes, making them suitable for various applications. This versatility reduces the need for specialized equipment and simplifies production processes.
- Escalabilidade: Mixer tanks are available in various sizes, from laboratory-scale units to large industrial-scale tanks, allowing for easy scale-up of production from research and development to commercial manufacturing.
- Ease of use: Modern mixer tanks are designed for easy operation and maintenance, often featuring user-friendly controls and automated features. This simplifies operation and reduces the risk of human error.
- Durabilidade: Mixer tanks are typically made from robust materials, such as stainless steel, ensuring long-lasting performance even in harsh operating conditions. This durability minimizes downtime and reduces replacement costs.
- Segurança: Mixer tanks can be equipped with safety features, such as interlocks and emergency stops, to prevent accidents and ensure operator safety. These safety features protect personnel and create a safer working environment.
Escolhendo o Certo Mixer Tank para suas necessidades
Selecting the right mixer tank is crucial for optimal performance and efficiency. Consider the following factors when choosing a mixer tank:
- Tank size and shape: Choose a tank that is appropriately sized for your batch volume and mixing requirements. The shape of the tank can also affect the mixing efficiency.
- Mixer type and power: Select a mixer that is suitable for the viscosity and properties of the materials being mixed. The type of impeller, its rotational speed, and the motor power are all critical considerations.
- Material of construction: Choose a material that is compatible with the substances being mixed and can withstand the operating conditions, including temperature and pressure.
- Accessories and features: Consider additional features such as heating or cooling jackets for temperature control, level indicators for monitoring fill levels, and safety interlocks for enhanced safety. Also consider the type of seal used (mechanical seal, packing, etc.) as this can impact maintenance requirements and potential for leakage.
- Mixing requirements: What degree of homogeneity is required? Are solids being incorporated into a liquid? Is a specific shear rate required? These factors will influence the type of mixer and impeller chosen.
Mixer Tank Maintenance and Care
Proper maintenance is essential for ensuring the longevity and performance of your mixer tank. Follow these tips for maintaining your mixer tank:
- Regular cleaning: Clean the tank and mixer after each use to prevent contamination and buildup of residues. The cleaning procedure will vary depending on the materials being mixed.
- Inspeção: Regularly inspect the tank, mixer, seals, bearings, and other components for wear and tear, corrosion, or damage. Early detection of problems can prevent more serious issues.
- Lubrificação: Lubricate moving parts, such as bearings and seals, as needed to ensure smooth operation and prevent premature wear. Follow the manufacturer’s recommendations for lubrication type and frequency.
- Reparos: Address any repairs promptly to prevent further damage and ensure continued safe operation. Do not attempt repairs unless properly trained and qualified.
- Manutenção Preventiva: Establish a preventative maintenance schedule that includes regular inspections, cleaning, lubrication, and replacement of wear parts. This will help maximize the lifespan of the mixer tank.
Mixer Tank Safety Considerations
Safety is paramount when operating mixer tanks. Adhere to these safety guidelines:
- Treinamento: Ensure that all operators are properly trained in the safe operation of mixer tanks, including startup, operation, shutdown, and emergency procedures.
- Personal protective equipment (PPE): Wear appropriate PPE, such as gloves, eye protection, and protective clothing, when working with mixer tanks, especially when handling hazardous materials.
- Lockout/Tagout: Follow lockout/tagout procedures before performing any maintenance or repairs to prevent accidental startup of the mixer.
- Emergency procedures: Familiarize yourself with emergency procedures in case of accidents, spills, or equipment malfunctions. Have emergency contact information readily available.
- Ventilation: Ensure adequate ventilation in the area where the mixer tank is located, especially when mixing volatile or hazardous substances.
- Material Safety Data Sheets (MSDS): Always consult the MSDS for the materials being mixed to understand the potential hazards and take appropriate precautions.
Mixer Tank Applications Across Industries
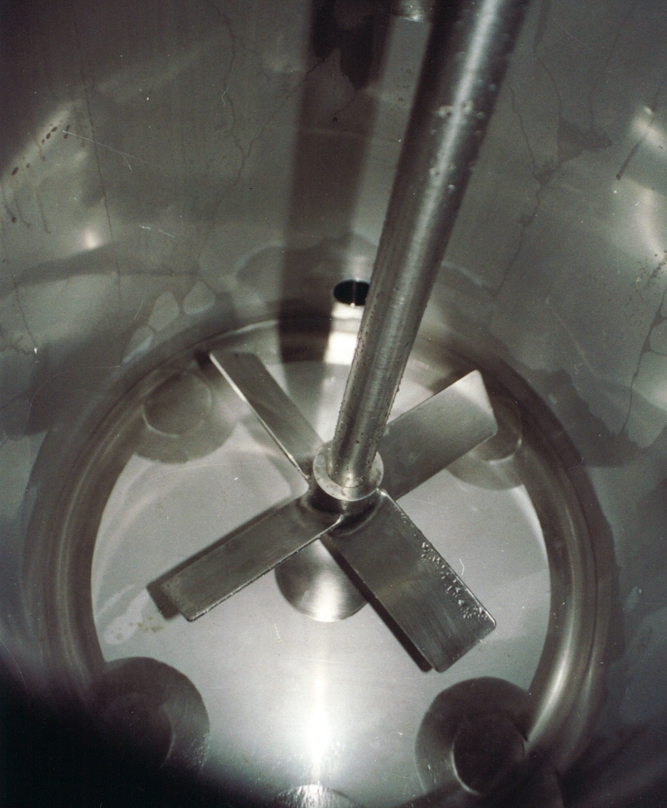
Here’s a table showcasing the diverse applications of mixer tanks across various industries:
Indústria | Aplicativo | Exemplos |
---|---|---|
Alimentos e Bebidas | Blending ingredients, mixing beverages, preparing sauces | Mixing ingredients for a cake batter, blending juices for a beverage, preparing a tomato sauce |
Produtos farmacêuticos | Mixing active ingredients, preparing solutions, blending powders | Mixing different drugs for a combination pill, preparing an IV solution, blending powders for capsules |
Processamento químico | Mixing chemicals, blending polymers, preparing emulsions | Mixing reactants for a chemical synthesis, blending different types of plastic polymers, preparing an oil-in-water emulsion |
Cosméticos | Blending ingredients, preparing lotions, mixing fragrances | Blending oils and emulsifiers for a lotion, mixing different fragrance components, mixing pigments for makeup |
Water Treatment | Mixing chemicals for water purification | Mixing coagulants and flocculants for water treatment |
Agricultura | Preparing fertilizers and pesticides | Mixing different nutrients for a fertilizer, mixing pesticides for crop spraying |
Conclusão
Mixer tanks are essential equipment for a multitude of industries, offering numerous benefits in terms of product quality, efficiency, versatility, and safety. By understanding the different types of mixer tanks, their applications, and maintenance requirements, businesses can maximize the benefits of these valuable tools and ensure smooth and efficient operations. Proper selection, operation, and maintenance of mixer tanks are key to achieving optimal results and ensuring a safe working environment.
Perguntas frequentes
Q: What is the difference between a mixer tank and a storage tank?
A: Mixer tanks are designed for blending and mixing substances, while storage tanks are primarily used for holding and storing liquids or solids.
Q: How do I choose the right mixer tank size for my needs?
A: Consider your batch volume, mixing requirements, and available space when selecting a mixer tank size.
Q: What safety precautions should I take when operating a mixer tank?
A: Always wear appropriate PPE, follow lockout/tagout procedures, and familiarize yourself with emergency procedures.
Q: How often should I clean my mixer tank?
A: Clean your mixer tank after each use to prevent contamination and ensure optimal performance.