Introdução
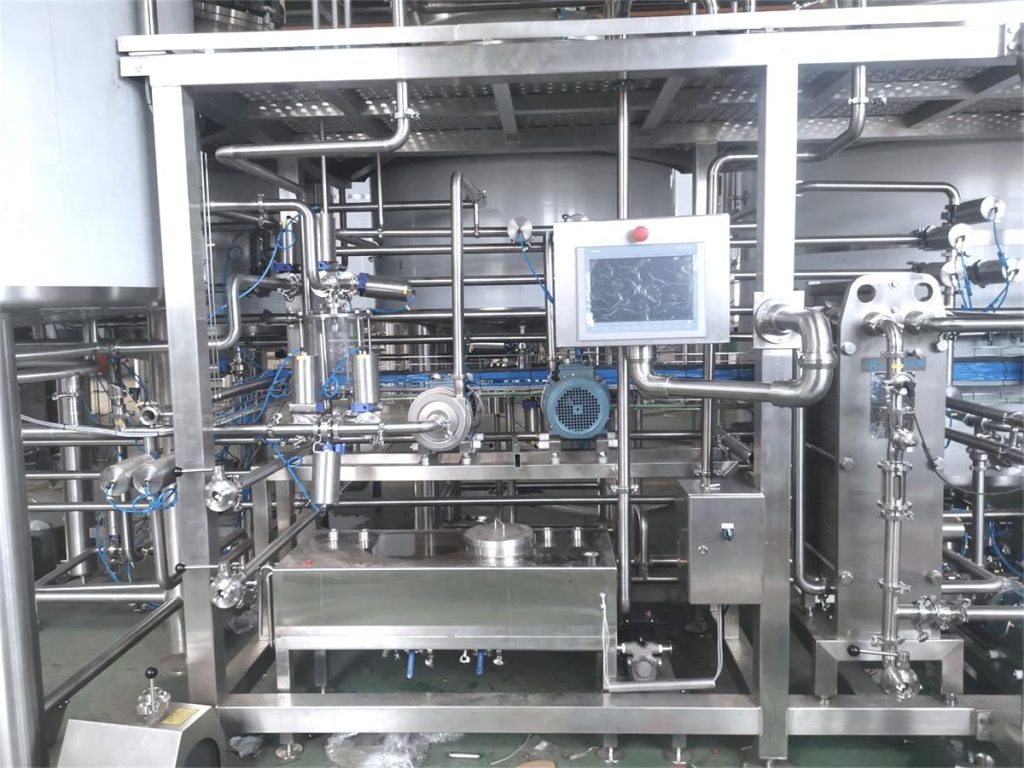
As bombas de condensado de vapor desempenham um papel fundamental em vários processos industriais onde o vapor é usado para aquecimento, esterilização ou geração de energia. A remoção eficiente de condensado garante desempenho ideal, conservação de energia e longevidade do equipamento. Neste blog, nos aprofundamos na importância das bombas de condensado de vapor, seus princípios operacionais, requisitos de manutenção e benefícios para sistemas industriais.
Entendimento Steam Condensate Pumps
Steam condensate pumps are specifically designed to handle the condensate generated during steam processes. This condensed steam, or condensate, contains significant thermal energy that, if not recovered, represents a loss in efficiency and operational cost. Steam condensate pumps facilitate the removal of this condensate from the system, enabling its reuse or safe disposal.
Operational Principles
Steam condensate pumps operate based on the principle of converting kinetic energy into mechanical energy to move the condensate. They utilize various mechanisms such as centrifugal force, positive displacement, or vacuum systems to achieve efficient condensate removal. These pumps are often equipped with sensors and controls to optimize performance and prevent issues such as cavitation and water hammer.
Importance in Industrial Systems
In industrial settings, steam condensate pumps are essential for maintaining optimal operating conditions and maximizing energy efficiency. By promptly removing condensate, these pumps prevent waterlogging, corrosion, and steam trap failure, thereby prolonging the lifespan of equipment and reducing downtime. Moreover, recovered condensate can be returned to the boiler feedwater system, reducing water and energy consumption.
Benefícios de Steam Condensate Pumps
- Energy Efficiency: By recovering and recycling condensate, steam condensate pumps contribute to significant energy savings by minimizing the need for fresh water and reducing fuel consumption for steam generation.
- Equipment Protection: Efficient condensate removal prevents damage to steam traps, valves, and other components, leading to extended equipment lifespan and reduced maintenance costs.
- Environmental Sustainability: Recycling condensate conserves water resources and reduces the environmental impact associated with water consumption and wastewater discharge.
Requisitos de manutenção
Proper maintenance is crucial for ensuring the reliable operation of steam condensate pumps. Regular inspection, lubrication, and testing of pump components are essential to prevent malfunctions and optimize performance. Additionally, monitoring condensate quality and addressing issues such as corrosion and contamination are vital for prolonging pump lifespan and minimizing downtime.
Example table for a bomba de condensado de vapor maintenance schedule
Maintenance Task | Freqüência | Descrição |
---|---|---|
Visual Inspection | Semanalmente | Inspect pump for leaks, unusual noises, and signs of corrosion or wear. |
Lubrication | Mensal | Lubricate bearings, shafts, and other moving parts according to manufacturer’s recommendations. |
Performance Testing | Trimestral | Conduct performance tests to ensure the pump is operating within specified parameters. |
Seal Replacement | Anualmente | Replace pump seals to prevent leaks and maintain efficiency. |
Motor Alignment | Bi-annually | Check and adjust motor alignment to prevent premature wear and ensure optimal performance. |
Vibration Analysis | Bi-annually | Perform vibration analysis to identify potential issues with pump operation or alignment. |
Impeller Inspection | Anualmente | Inspect impeller for damage or wear, and clean if necessary. |
Bearing Replacement | Every 3-5 years | Replace bearings as recommended by the manufacturer or based on condition monitoring results. |
Case Studies
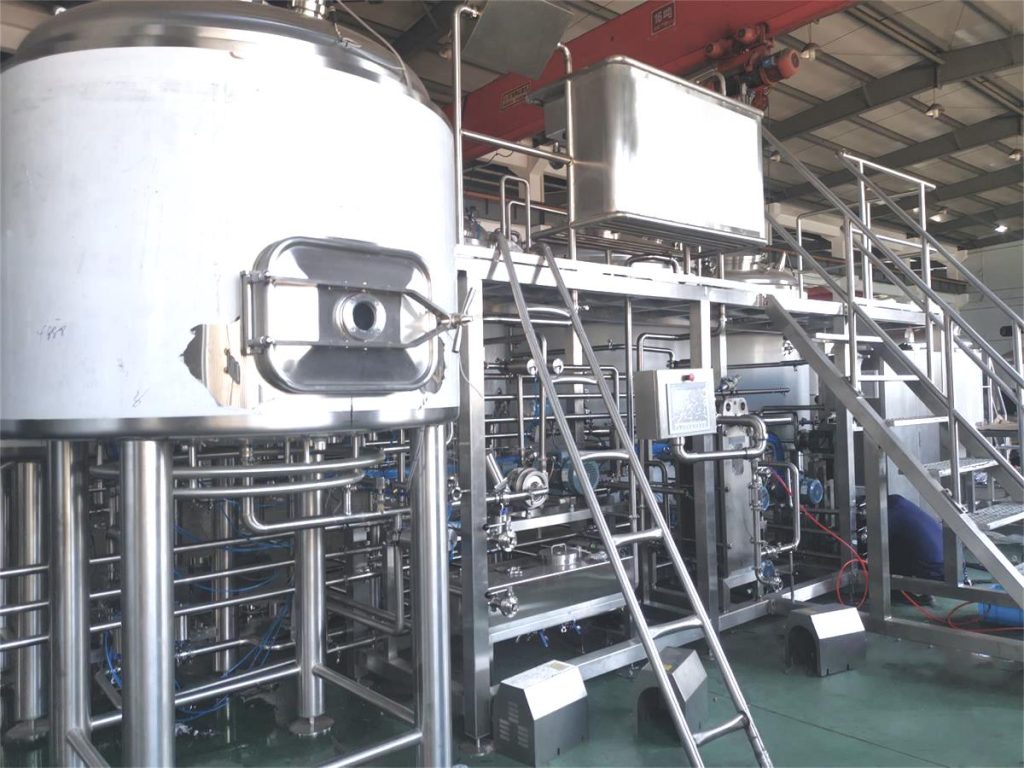
To illustrate the importance of steam condensate pumps in industrial applications, let’s consider two case studies:
- Brewery Operations: In a brewery, steam is used for various processes such as brewing, sterilization, and bottling. Efficient condensate removal is critical to maintaining product quality and maximizing production output. By installing high-performance steam condensate pumps, the brewery achieved significant energy savings and reduced water consumption, leading to improved sustainability and operational efficiency.
- Chemical Processing Plant: In a chemical processing plant, steam is utilized for heating, reaction control, and distillation. Steam condensate pumps play a vital role in removing condensate from heat exchangers and process vessels, preventing corrosion and ensuring optimal process conditions. By implementing a comprehensive condensate management system, the plant minimized downtime, reduced maintenance costs, and enhanced overall productivity.
Conclusão
Steam condensate pumps play a crucial role in industrial systems by efficiently removing condensate, optimizing energy usage, and protecting equipment. Proper selection, installation, and maintenance of these pumps are essential for ensuring reliable operation and maximizing the benefits of condensate recovery. By integrating steam condensate pumps into industrial processes, companies can achieve significant energy savings, reduce environmental impact, and enhance overall operational efficiency.
Perguntas frequentes
P: Qual é a função principal de um bomba de condensado de vapor?
A:The primary function of a steam condensate pump is to remove condensate (liquid) that forms as a result of steam condensing within a system. This ensures efficient operation by preventing waterlogging and maintaining optimal performance.
Q:How does condensate removal contribute to energy efficiency?
A:Efficient condensate removal prevents water buildup in steam systems, reducing the energy required to heat or reheat the system. Recovering and reusing condensate also conserves thermal energy, leading to overall energy savings.
Q:What are the common maintenance tasks for bombas de condensado de vapor?
A:Common maintenance tasks for steam condensate pumps include visual inspections for leaks and wear, lubrication of moving parts, performance testing, seal replacement, motor alignment, vibration analysis, impeller inspection, and bearing replacement.
Q:Can steam condensate be reused in industrial processes?
A:Yes, steam condensate can be reused in various industrial processes, such as boiler feedwater, preheating, and makeup water for cooling systems. This practice reduces water consumption and energy usage, contributing to cost savings and environmental sustainability.
Q:What factors should be considered when selecting a bomba de condensado de vapor?
A:When selecting a steam condensate pump, factors to consider include the required flow rate and head, pump efficiency, system pressure and temperature, material compatibility with the pumped fluid, reliability, maintenance requirements, and cost-effectiveness over the pump’s lifespan.