All pressure vessels that are designed to AS1210/PED/ASME requirements must be pressure tested after fabrication and inspected to demonstrate their structural integrity before they are placed into operation.
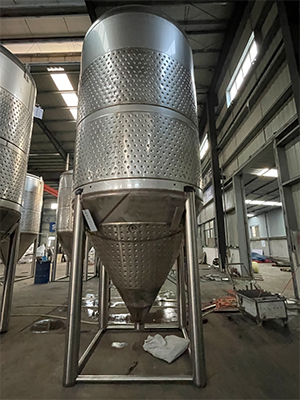
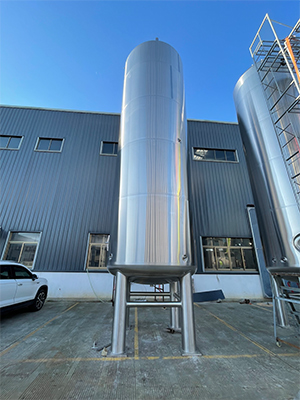
The pressure test is made at a pressure that is higher than the design pressure. The excess pressure provides a safety margin since the vessel component stress levels during the test will be higher than those that will occur during operation.
The objective of the pressure test is to bring the vessel to a high enough internal pressure, under controlled conditions, to demonstrate its mechanical integrity. Successful completion of the pressure test signifies that the vessel is acceptable for operation.
Prior to hydrostatic testing, the vessel is checked dimensionally for compliance with the construction drawing and manufacturing tolerances required.
Pressure tests are typically made using water as the test medium because of the relative safety of water compared to pneumatic test.
Water is nearly incompressible, therefore requiring relatively little work to develop a high pressure and is therefore only able to release a small amount of energy under high pressure if the container fails.
Pneumatic testing using high-pressure gas is permitted by agreement but is usually avoided because it presents a significant hazard due to the amount of stored energy in the compressed gas. A rupture could result in an explosive release of this energy which can potentially cause damage or injury to personnel carrying out the test.
Hydrostatic testing involves filling the vessel with a liquid, usually water, and pressurisation of the vessel to the specified test pressure and usually carried out by personnel having adequate experience and qualifications to carry out the examination.
The minimum required test pressure as per AS 1210/PED/ASME requirement is about 1.43x the design pressure and usually documented on the construction drawings, ITP, and inspection sheets.
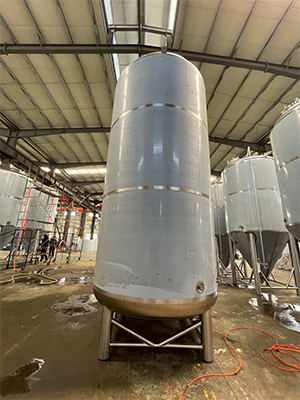
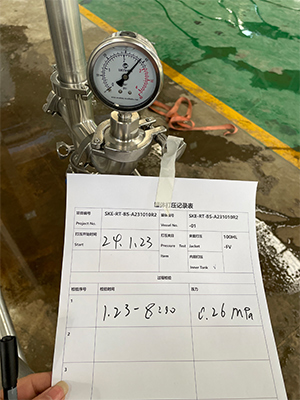
Pressure tightness can be tested by shutting off the supply valve and observing whether there is a pressure loss. Strength is usually tested by measuring permanent deformation in the vessel.
The system to be hydrostatically tested is gradually filled with water and vented to ensure air pockets are eliminated. The test shall not commence until the vessel and the water inside have equalised to the same temperature.
Once the system has been filled and stabilised, it is isolated, and the system is gradually pressurised to the designated test pressure. The test pressure will be held for 30 minutes and then reduced to 85-95% of the test pressure while the physical examination of the vessel will take place.
Any leaks, deformation/distortions, drop in pressure or other issues identified are then corrected and the pressure vessel is retested as per AS 4037 requirement.

Once completed, test records and reports are generated, and the results are recorded on the Hydrostatic Test Certificate to signal the successful completion of the test.
The unmatched combination of experience, flexibility, expertise, and technology for every ESK project serve to minimise production risk and ensure on-time, on-budget, and as-specified delivery.