Introduction
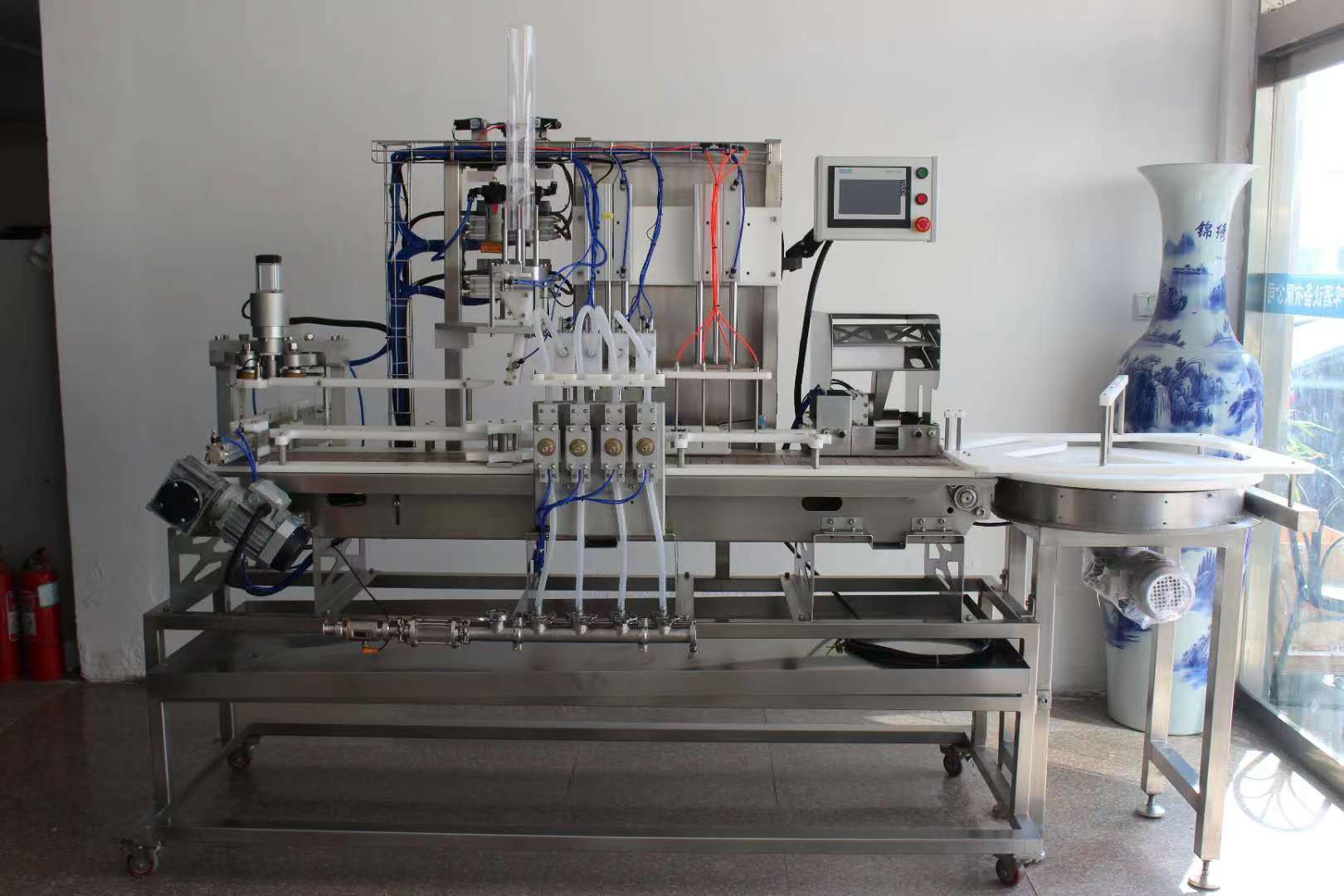
In the competitive world of brewing, maximizing efficiency is crucial for maintaining competitiveness and meeting consumer demand. One of the key components in achieving this efficiency is the utilization of beer can filling machines. These machines play a pivotal role in streamlining production processes, ensuring product quality, and optimizing overall brewery operations. This blog explores in detail the impact of filling machines on brewery efficiency, covering their functionalities, benefits, case studies, implementation considerations, and the future trends shaping this technology.
The Role of Filling Machines in Brewery Operations
Functionality and Types of Filling Machines
Beer can filling machines come in various types, each designed to cater to different brewery sizes and production needs.
- Rotary Filling Machines: Ideal for high-speed operations, these machines fill cans in a continuous rotary motion, ensuring rapid throughput and consistency in fill levels.
- Counter-Pressure Fillers: These machines maintain CO2 pressure inside the can during filling, minimizing oxygen exposure and preserving beer freshness and flavor.
- Volumetric Fillers: Known for their accuracy, volumetric fillers measure exact volumes of beer per can, suitable for breweries prioritizing precise fill levels and minimizing product giveaway.
Each type offers distinct advantages depending on the brewery’s production volume, space constraints, and desired automation level.
Benefits of Using Filling Machines
Implementing filling machines in brewery operations provides several key benefits:
- Enhanced Production Efficiency: Automation reduces manual labor, speeds up production cycles, and allows for continuous operation.
- Consistent Product Quality: Precise filling controls minimize variations in fill levels, ensuring every can meets quality standards and enhancing consumer satisfaction.
- Reduced Operational Costs: Efficient use of raw materials (beer, CO2, water) and minimized product wastage contribute to overall cost savings.
- Improved Safety and Hygiene: Closed-system filling reduces exposure to contaminants, maintaining product integrity and brewery sanitation standards.
Case Studies and Industry Applications
Small Craft Brewery Integration
A small craft brewery adopted a rotary filling machine to scale up production while maintaining artisanal quality. By automating the filling process, the brewery doubled its output without compromising on product consistency or quality. This case study highlights how filling equipments can facilitate growth for smaller breweries looking to expand their market presence.
Large-Scale Brewery Efficiency
A large-scale brewery implemented a combination of counter-pressure fillers and volumetric fillers to optimize its production lines. These machines enabled the brewery to manage high-volume production efficiently, reduce downtime for cleaning and maintenance, and meet stringent quality control standards consistently. This case illustrates the scalability and versatility of filling equipments in accommodating the needs of large-scale brewery operations.
Implementing Filling Machines: Considerations and Best Practices
Factors to Consider Before Implementation
Before investing in filling machines, breweries should assess several factors:
- Production Capacity Requirements: Matching machine capabilities with projected production volumes and growth expectations.
- Technological Integration: Compatibility with existing brewery infrastructure (conveyor systems, quality control measures, packaging lines).
- Maintenance and Support: Availability of technical support, spare parts, and maintenance services from the manufacturer or supplier.
Best Practices for Maximizing Efficiency
- Regular Maintenance: Establishing a maintenance schedule to ensure optimal performance and longevity of filling equipments.
- Operator Training: Providing comprehensive training for brewery staff to operate machines efficiently, troubleshoot issues, and perform routine maintenance tasks.
- Quality Control Protocols: Implementing robust quality assurance measures to monitor fill accuracy, detect anomalies, and uphold product consistency and safety standards.
Key Considerations and Benefits
Aspect | Description |
---|---|
Automation Level | Degree of automation offered by filling machines (e.g., manual, semi-automatic, fully automatic). |
Production Capacity | Range of cans filled per hour or per day depending on the machine type and brewery size. |
Fill Accuracy | Precision in filling cans to ensure consistent product quality and minimize wastage. |
Maintenance Requirements | Frequency and complexity of maintenance tasks required to keep machines operational. |
Integration with Systems | Compatibility with existing brewery infrastructure (conveyor systems, quality control measures). |
Cost Effectiveness | ROI calculation based on reduced labor costs, minimized product loss, and increased production output. |
The Future of Brewery Efficiency with Filling Machines
Innovations and Emerging Technologies
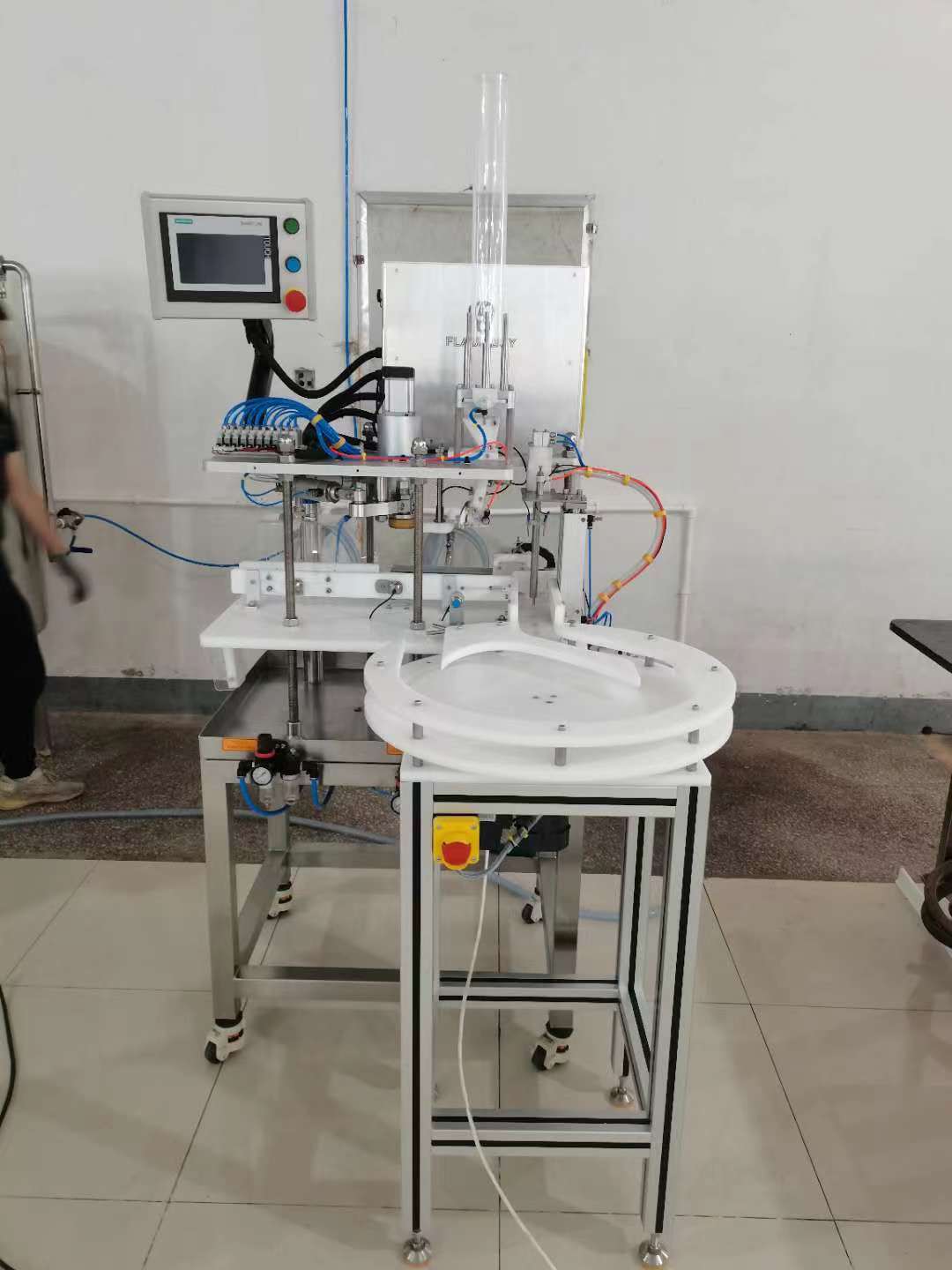
Future advancements in filling machine technology focus on:
- Smart Automation: Integration of IoT (Internet of Things) for real-time monitoring of machine performance, predictive maintenance, and data-driven decision-making.
- Environmental Sustainability: Developing eco-friendly solutions that reduce water and energy consumption, aligning with global sustainability goals.
- Enhanced Flexibility: Modular designs that allow breweries to adapt quickly to changing production demands and market trends.
These innovations promise to further elevate brewery efficiency, reduce operational costs, and enhance overall sustainability in beer production.
Conclusion
Beer can filling machines are indispensable tools for modern breweries seeking to optimize efficiency, maintain product quality, and meet growing consumer expectations. By automating the filling process and integrating advanced technologies, breweries can achieve higher throughput, minimize waste, and ensure consistent product excellence. As the industry continues to evolve, equipments will play a pivotal role in driving innovation and shaping the future of brewery operations.
FAQ
Q: How do filling machines improve brewery efficiency?
A:Filling machines streamline the can filling process, reducing manual labor, minimizing product wastage, and ensuring consistent product quality, thereby optimizing overall brewery efficiency.
Q: What types of filling machines are commonly used in breweries?
A:Common types include rotary filling machines, counter-pressure fillers, and volumetric fillers, each offering specific advantages in terms of speed, precision, and adaptability to brewery operations.
Q: What considerations should breweries take into account before investing in a filling machine?
A:Breweries should evaluate factors such as production capacity requirements, technological compatibility, maintenance needs, and quality control protocols to maximize efficiency and return on investment.