H2 New Energy Revolution: Efficiency Breakthroughs in Pure Water to Hydrogen Plants
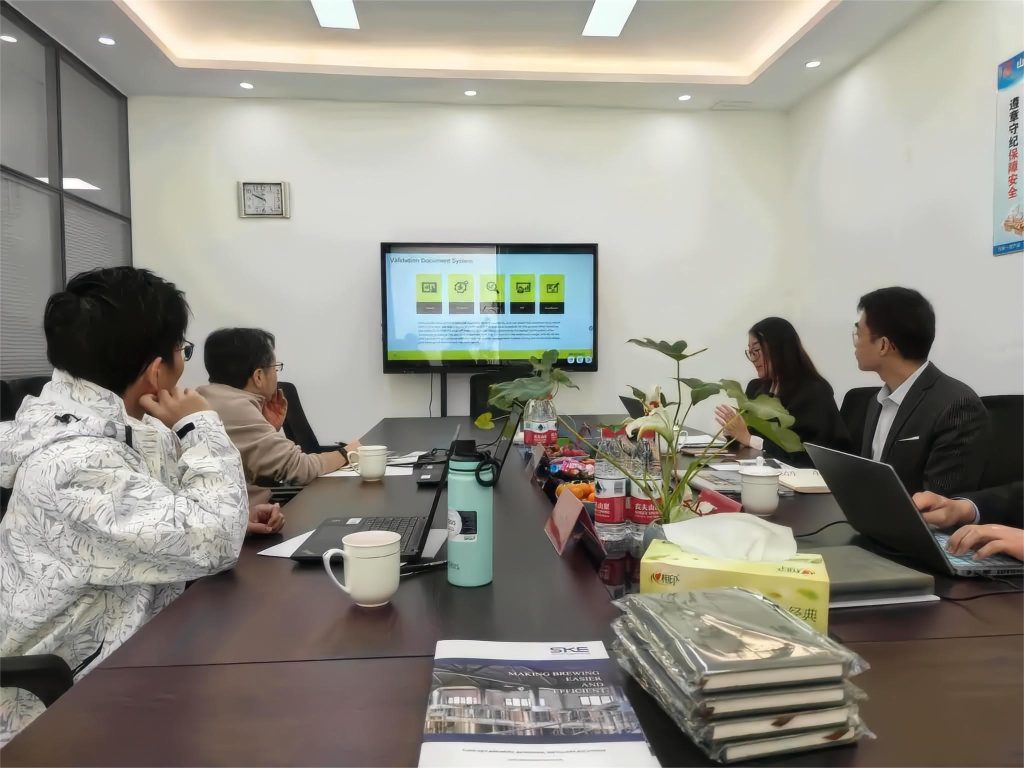
Driven by the “double carbon” strategy, SKE’s independently developed PEM pure water electrolysis hydrogen production system has achieved three major innovations:
- Energy efficiency revolution: The advanced corrugated manufacturing machine adopts innovative forming technology to significantly reduce the electrolyzer volume by 40%, while simultaneously boosting production capacity by a remarkable 65%. This cutting-edge innovation in manufacturing not only enhances energy savings but also greatly improves overall productivity.
- In terms of material innovation, we have successfully created an ultra-thin titanium plate with a thickness of 0.08 mm through laser welding technology. Its current density reached 3.2A/cm², setting a new industry record.
- Intelligent control: AI algorithm dynamically adjusts voltage fluctuations, and the hydrogen purity is stably maintained at 99.999%
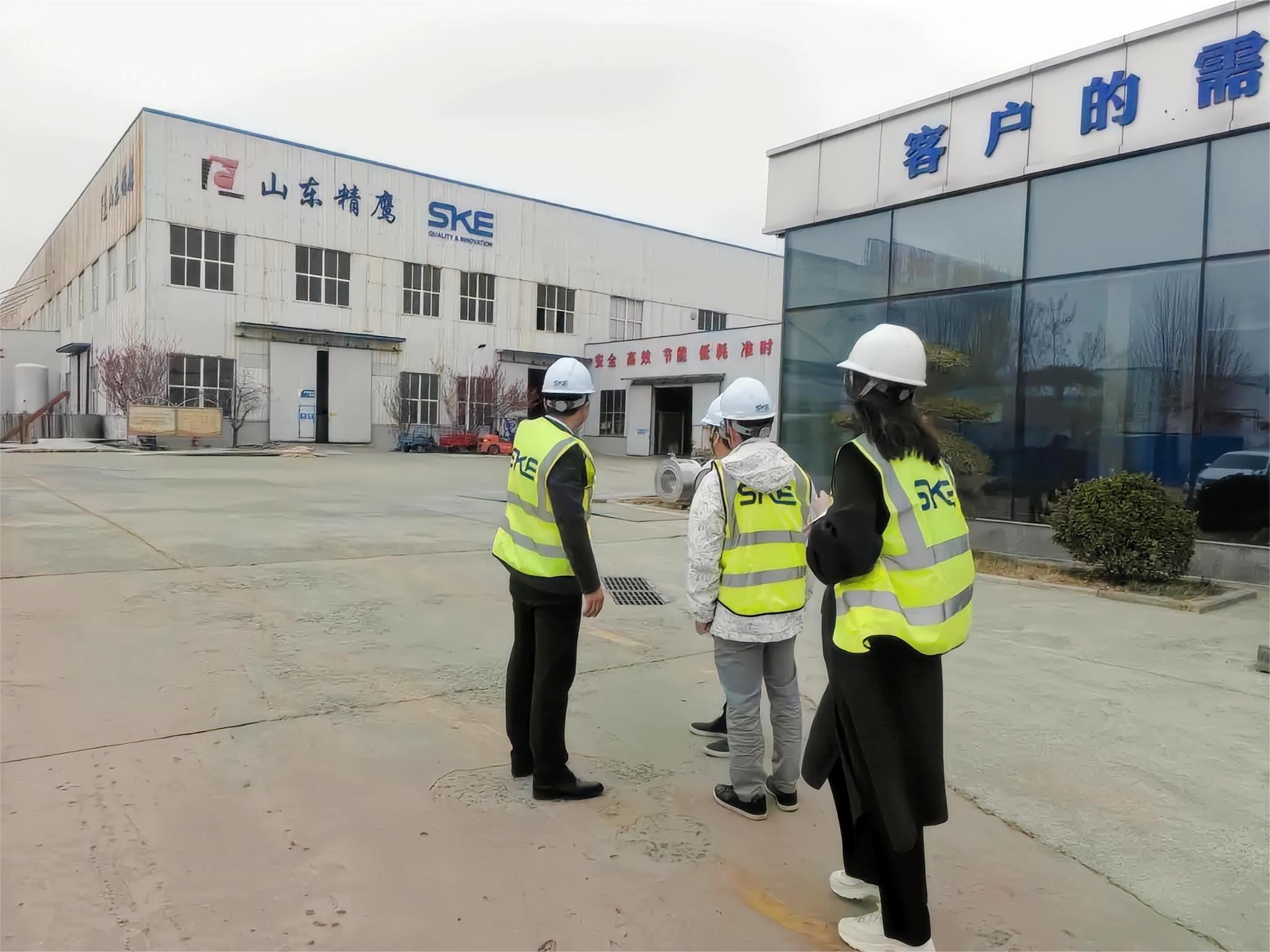
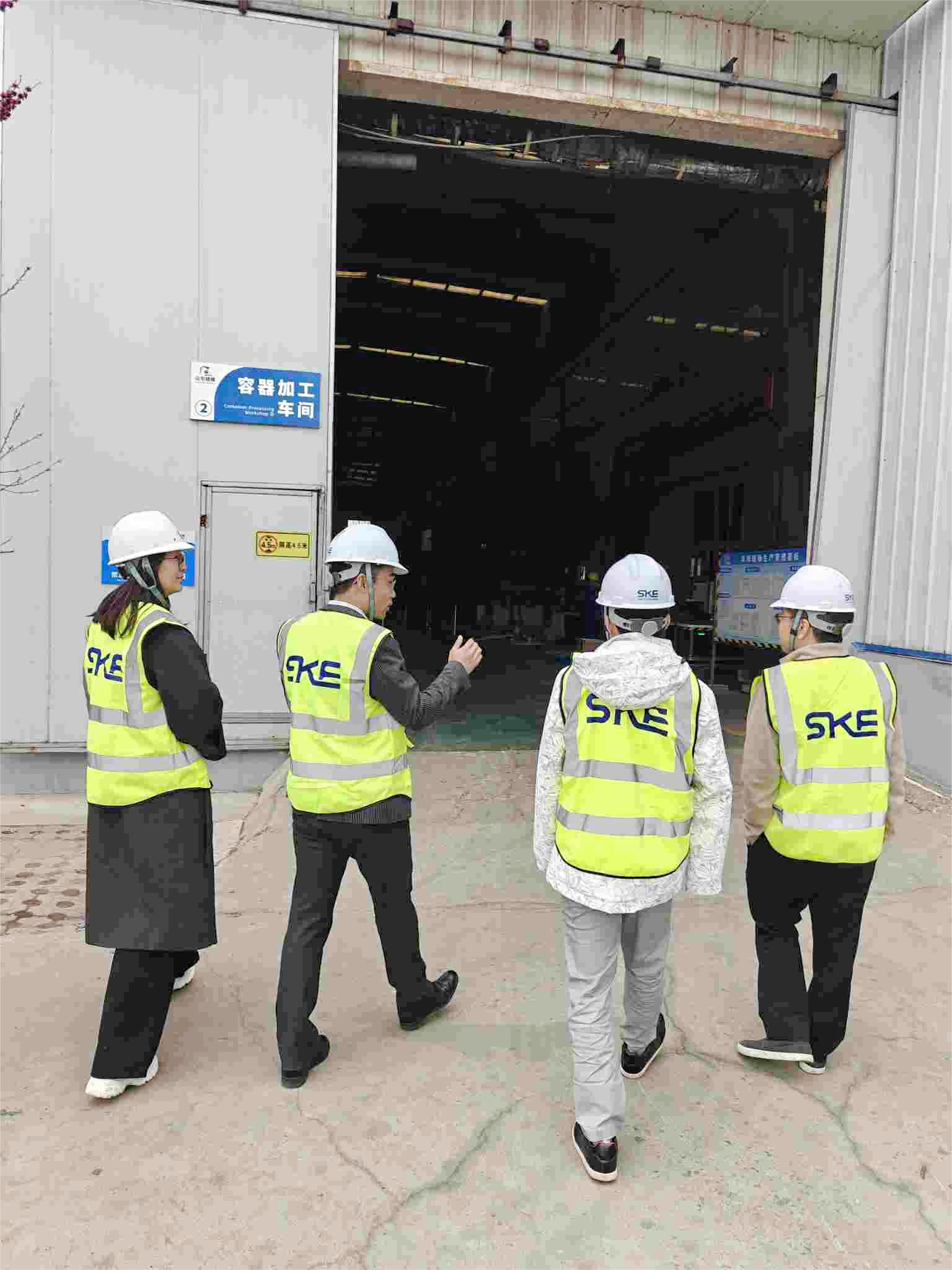
Analysis of cutting-edge manufacturing processes
Precise Control of Laser Welding Technology
- Micron-level welding accuracy (±5μm) ensures equipment airtightness
- The heat-affected zone is precisely controlled within a mere 0.3mm, thereby significantly enhancing the material’s strength by a remarkable 30%.
Micron-level welding accuracy (±5μm) ensures equipment airtightness
The heat-affected zone is precisely controlled within a mere 0.3mm, thereby significantly enhancing the material’s strength by a remarkable 30%.
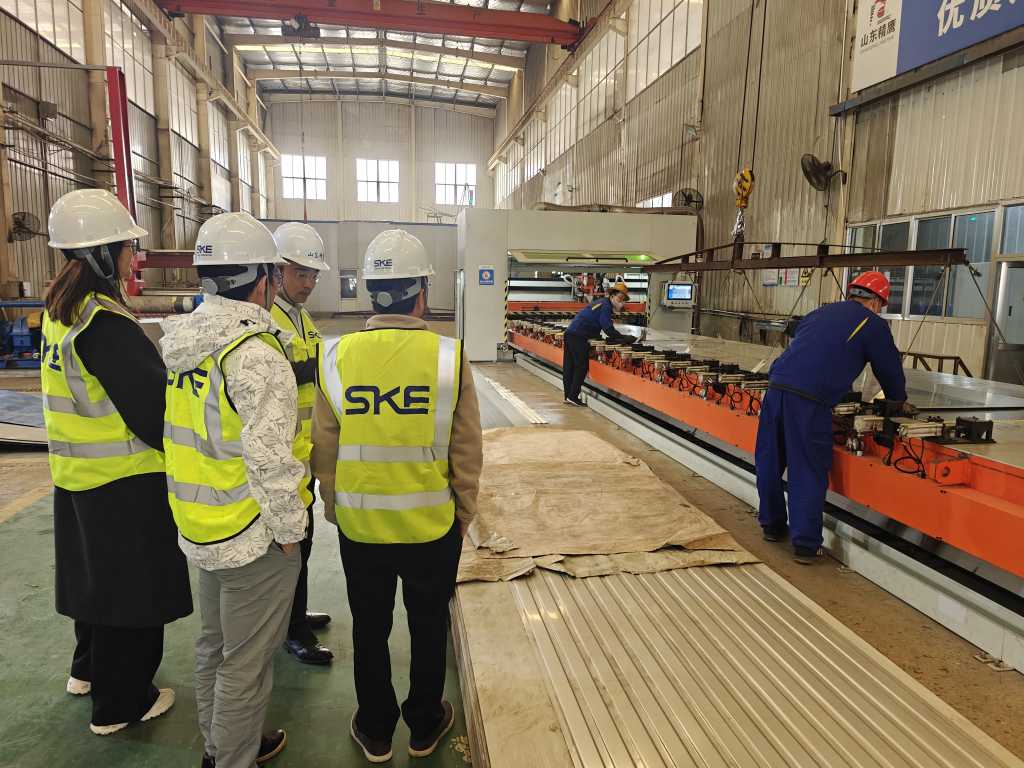
Structural innovation of corrugated forming technology
- This innovative technology, which uses a three-dimensional corrugated plate design, increases the effective reaction area by 30%, significantly improving performance.
- Using a modular assembly system, the installation cycle is shortened by 60%
- Cross-border application of 316L stainless steel brewing equipment-grade anti-corrosion treatment technology

Diversified production map: Hydrogen energy equipment and brewing technology fly together
- The beer brewing equipment production line adheres to the stringent standards of food-grade stainless steel, ensuring the utmost quality and safety in the brewing process.
- Advanced precision density control system ensures an extremely narrow
- concentration error range of only 3%, demonstrating excellent performance accuracy and reliability
- The use of intelligent CIP cleaning system can significantly reduce energy consumption, saving 35% of energy compared to traditional methods. This advanced technology achieves high efficiency and energy saving by optimizing the cleaning process and reducing unnecessary energy waste. Under the current trend of advocating environmental protection and energy saving, the intelligent CIP cleaning system not only reduces operating costs for enterprises, but also contributes to sustainable development. Its efficient performance has been widely recognized and is gradually becoming the first choice for cleaning systems in various industries.
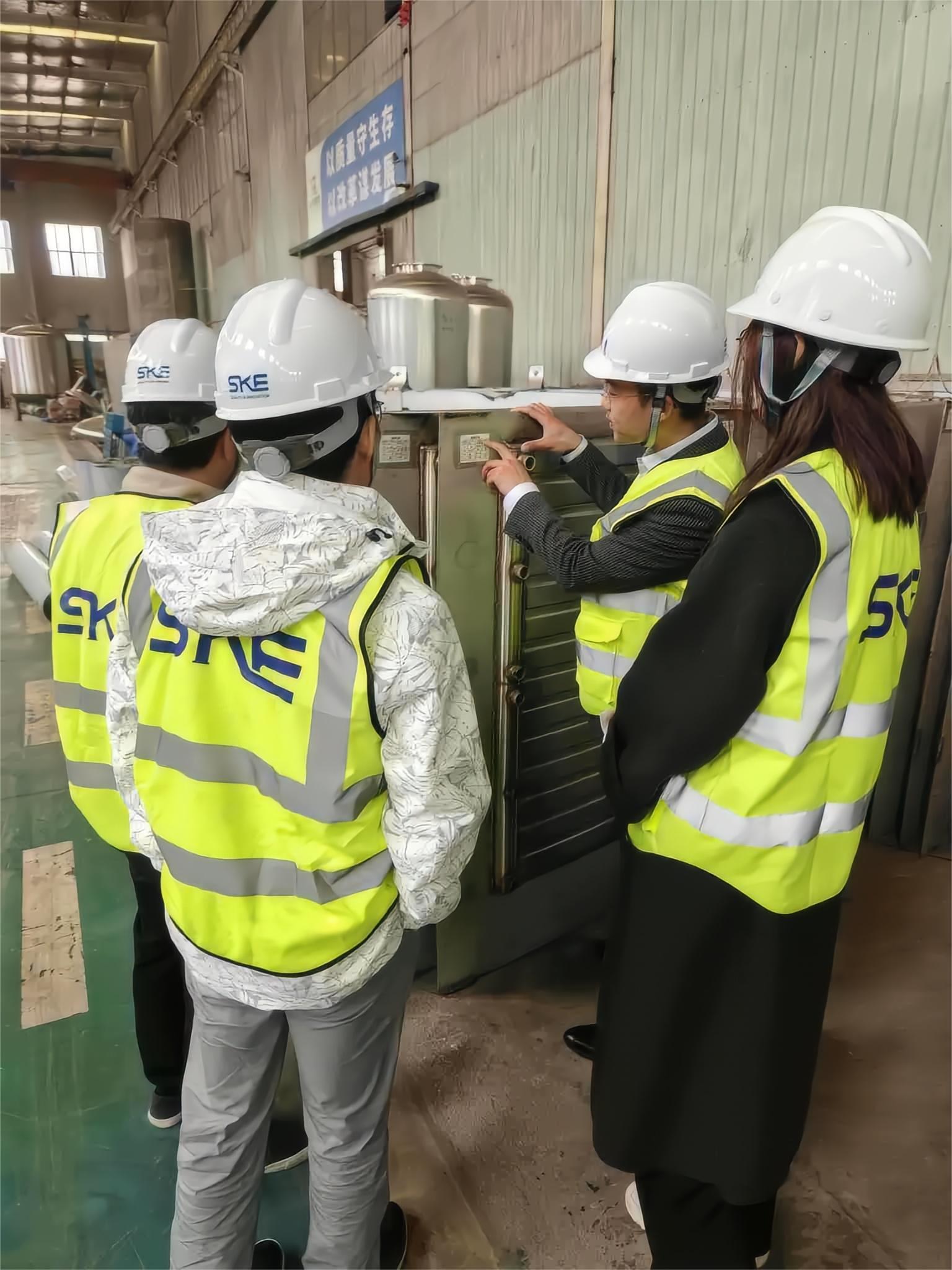
Quality control system: SKE’s manufacturing philosophy
- Implement ISO 9001:2025 and ASME dual certification standards
- Each device undergoes a 72-hour quality inspection test.
- Build digital twin archives throughout the lifecycle of critical components
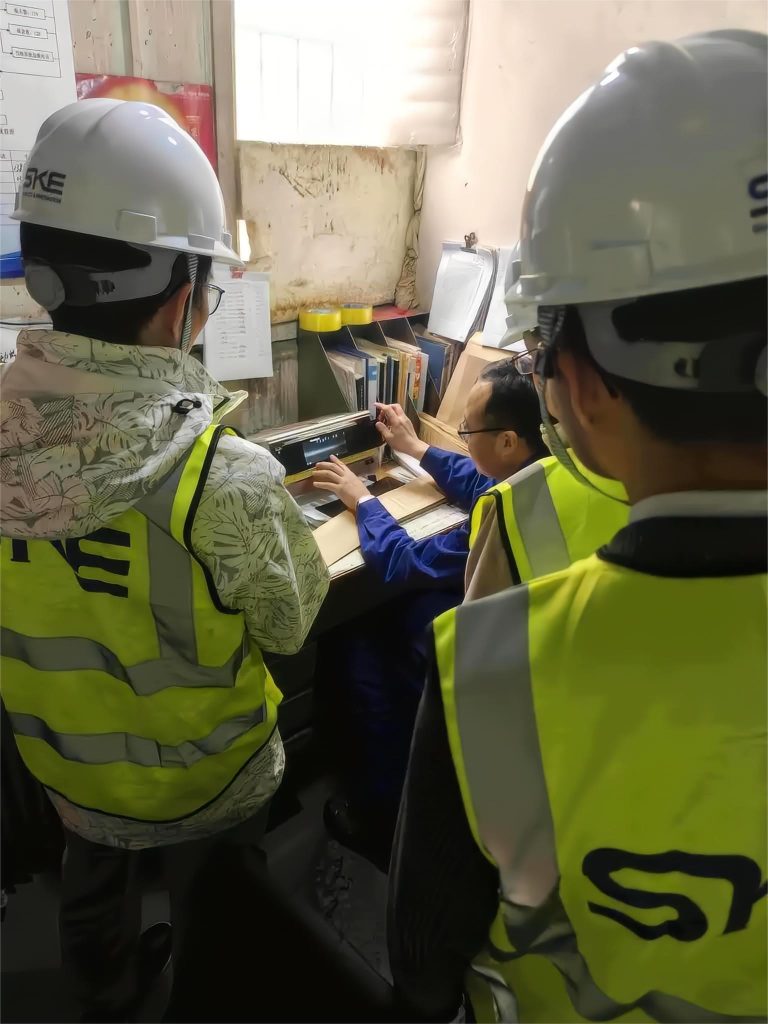