Introduction
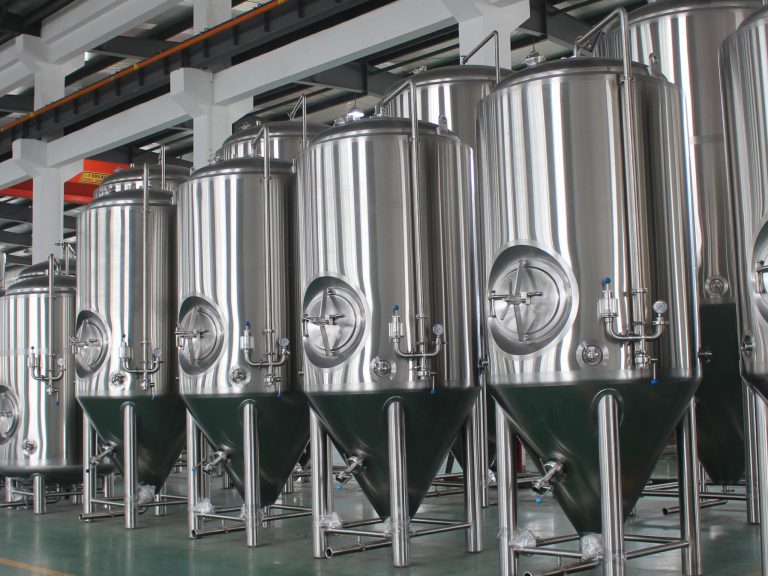
In the realm of industrial fermentation, the efficiency of your fermentation tank setup can significantly impact the quality and quantity of your product. Whether you’re brewing beer, fermenting yogurt, or producing biofuels, optimizing your fermentation tank setup is crucial for maximizing yields, minimizing costs, and ensuring consistent results. In this comprehensive guide, we’ll delve into various strategies and techniques to enhance the performance of your fermentation tank setup.
Understanding Fermentation Tank Dynamics
Before diving into optimization strategies, it’s essential to grasp the fundamental principles governing fermentation tank dynamics. Fermentation tanks are vessels designed to provide an ideal environment for microbial or biochemical processes to occur, typically involving the conversion of sugars into alcohol, acids, gases, or other products. These tanks come in various shapes, sizes, and configurations, but they all share common components and operational considerations.
Key Components of a Fermentation Tank Setup
To optimize your fermentation tank setup, it’s crucial to understand the role of each component and how they contribute to overall performance. Here are some key components to consider:
- Tank Design: The design of the fermentation tank plays a significant role in determining factors such as mixing efficiency, heat transfer rates, and microbial growth dynamics. Factors to consider include tank geometry, insulation, material of construction, and agitation mechanisms.
- Temperature Control: Maintaining optimal temperature conditions is critical for promoting the growth of desired microorganisms and preventing the proliferation of contaminants. Temperature control systems, such as jacketed tanks, heat exchangers, and thermostatic controls, are essential for achieving precise temperature regulation throughout the fermentation process.
- Aeration and Mixing: Adequate oxygen supply is essential for aerobic fermentation processes, where microorganisms require oxygen for growth and metabolism. Proper mixing techniques, such as mechanical agitation or sparging, ensure uniform distribution of nutrients and gases within the fermentation tank, enhancing microbial activity and product yield.
- pH Regulation: pH levels can significantly influence the growth and metabolic activity of microorganisms involved in fermentation. Monitoring and controlling pH within the optimal range is crucial for maintaining microbial viability and product consistency. pH control strategies may include the use of buffers, acids, or alkalis, along with automated pH monitoring and adjustment systems.
- Nutrient Addition: Microbial growth and metabolic activity depend on the availability of essential nutrients such as sugars, nitrogen sources, vitamins, and minerals. Optimizing nutrient supplementation strategies based on the specific requirements of the target microorganism can enhance fermentation performance and product quality.
Optimization Strategies for Enhanced Performance
Now that we’ve covered the key components of a fermentation tank setup, let’s explore some optimization strategies to maximize performance and efficiency:
- Process Monitoring and Control: Implementing robust monitoring and control systems allows real-time assessment of fermentation parameters such as temperature, pH, dissolved oxygen, and biomass concentration. Automated control algorithms can adjust operating conditions dynamically to maintain optimal fermentation conditions and respond promptly to deviations or disturbances.
- Optimized Agitation and Aeration: Experimenting with different agitation and aeration strategies can help optimize mixing efficiency and oxygen transfer rates within the fermentation tank. Techniques such as varying agitation speed, introducing baffles or impellers, or optimizing sparging rates can improve mass transfer and enhance microbial growth kinetics.
- Heat Transfer Optimization: Efficient heat transfer is essential for maintaining stable fermentation temperatures and preventing thermal gradients within the tank. Insulation improvements, heat exchanger upgrades, and optimization of heating/cooling systems can minimize energy consumption and reduce operational costs while ensuring precise temperature control throughout the fermentation process.
- Scale-Up Considerations: Scaling up fermentation processes from laboratory or pilot-scale to commercial production requires careful consideration of factors such as reactor size, mixing dynamics, and heat transfer characteristics. Conducting small-scale trials, computational modeling, and pilot plant studies can help identify potential scale-up challenges and optimize process parameters accordingly.
- Sanitation and Hygiene Practices: Maintaining a clean and sanitary fermentation environment is essential for preventing contamination and ensuring product quality and safety. Implementing rigorous cleaning protocols, sterilization procedures, and microbial monitoring strategies can minimize the risk of microbial spoilage or contamination events, safeguarding the integrity of the fermentation process.
Comparison of Agitation Techniques in Fermentation Tanks
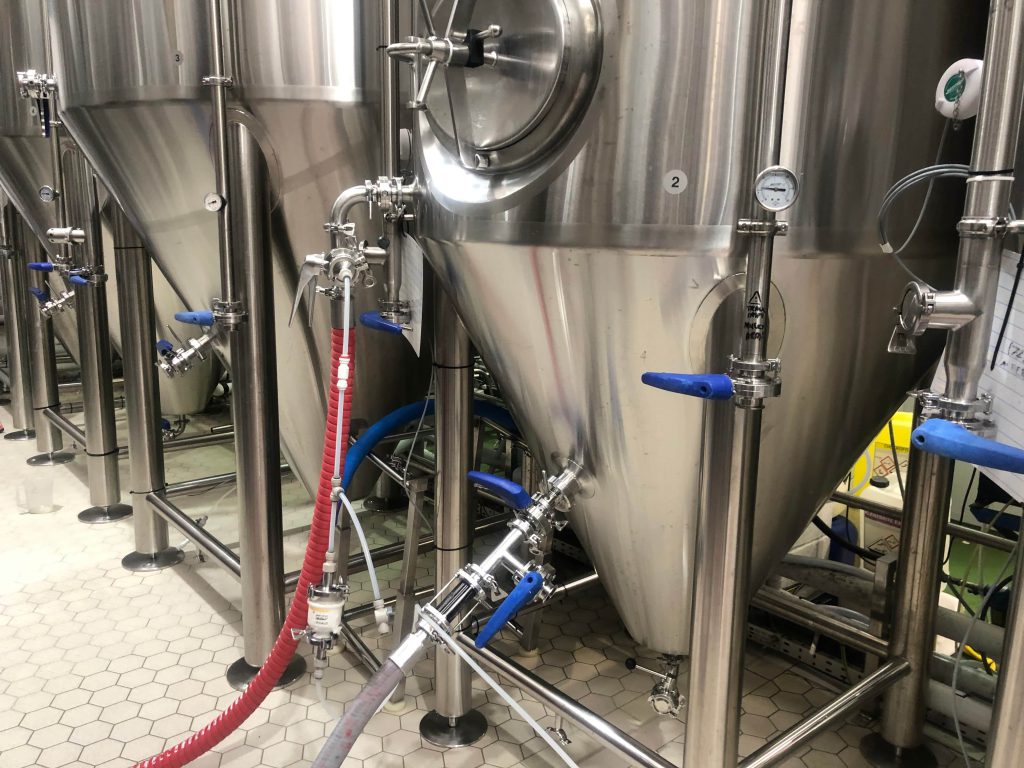
After understanding the key components and optimization strategies for fermentation tank setups, it’s essential to explore the various agitation techniques available for enhancing mixing efficiency and promoting optimal microbial growth. Different agitation methods offer unique advantages and disadvantages, depending on factors such as process requirements, vessel geometry, and the rheological properties of the fermentation media. Let’s delve into a comparative analysis of popular agitation techniques commonly employed in fermentation tanks.
Agitation Technique | Description | Advantages | Disadvantages |
---|---|---|---|
Mechanical Agitation | Propeller or impeller-driven agitation | Effective mixing of large volumes | High energy consumption, potential shear stress on microorganisms |
Air Sparging | Introduction of air bubbles for mixing | Gentle agitation, efficient oxygen transfer | Limited mixing efficiency in high-viscosity media |
Magnetic Stirring | Use of magnetic field to rotate stirring bar | Low energy consumption, uniform mixing | Limited scalability for large-scale operations |
Recirculation Pump | Recirculation of liquid through tank | Uniform mixing, adjustable flow rates | Requires additional equipment, potential dead zones |
Ultrasonic Agitation | Application of ultrasonic waves for mixing | Efficient mixing, minimal heat generation | Limited penetration in dense or viscous media |
Conclusion
In conclusion, optimizing your fermentation tank setup is essential for maximizing productivity, improving product quality, and minimizing operational costs. By understanding the key components of a fermentation tank system and implementing targeted optimization strategies, you can enhance process efficiency, achieve consistent results, and stay competitive in today’s dynamic fermentation industry.
FAQ
Q:How can I determine the optimal fermentation conditions for my specific application?
A:Conducting thorough experimentation, process modeling, and data analysis can help identify optimal operating parameters tailored to your fermentation process’s requirements.
Q:What are some common challenges associated with fermentation tank optimization?
A:Common challenges include microbial contamination, inadequate mixing or aeration, temperature fluctuations, and scale-up issues. Addressing these challenges requires a systematic approach, including process monitoring, troubleshooting, and continuous improvement efforts.
Q:What role does automation play in fermentation tank optimization?
A:Automation technologies, such as programmable logic controllers (PLCs), sensors, and data acquisition systems, play a crucial role in optimizing fermentation tank operations by enabling real-time monitoring, control, and optimization of key process parameters.
Q:How can I ensure regulatory compliance while optimizing my fermentation tank setup?
A:Adhering to relevant regulatory standards and guidelines, implementing Good Manufacturing Practices (GMP), and maintaining comprehensive documentation of process parameters and quality control measures are essential for ensuring regulatory compliance throughout the optimization process.
Q:Are there any emerging trends or technologies in fermentation tank optimization?
A:Emerging trends include the adoption of advanced analytics, machine learning algorithms, and bioprocess automation platforms to further enhance fermentation tank performance, optimize resource utilization, and accelerate process development and scale-up efforts.