Introduction
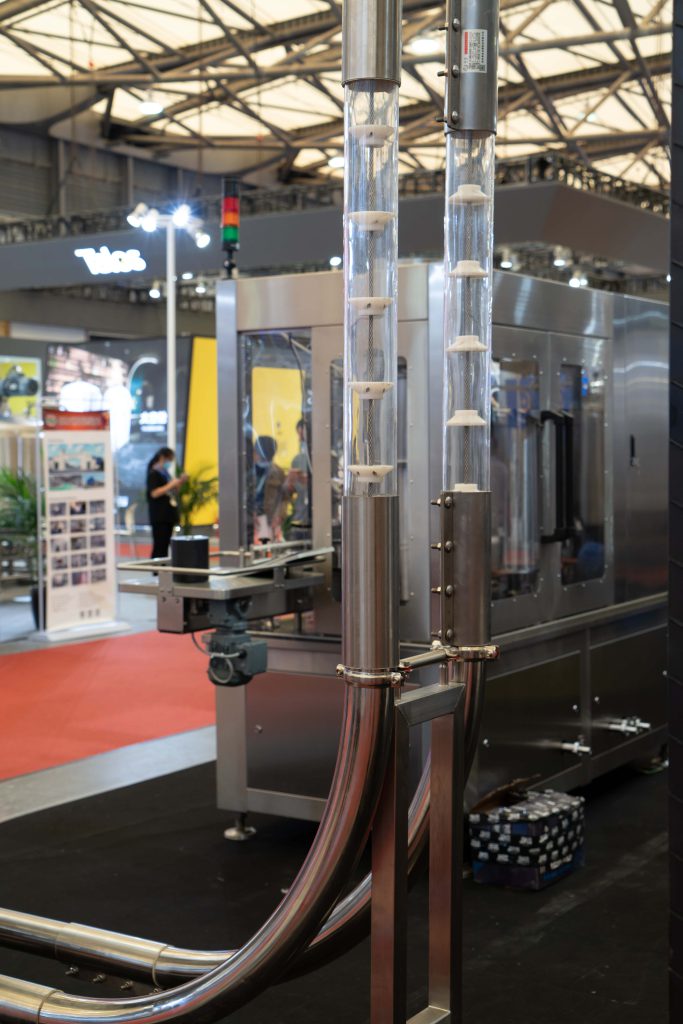
In today’s fast-paced manufacturing environment, efficiency is key to maintaining a competitive edge. A small conveyor system can significantly enhance productivity by optimizing the movement of materials and products within a production line. This blog will explore how a small conveyor system can streamline your operations, reduce labor costs, and improve overall efficiency. By examining various aspects—from types and benefits to implementation strategies—we aim to provide a comprehensive understanding of why investing in a small conveyor system could be a game-changer for your business.
Understanding Small Conveyor Systems
A small conveyor system is specifically designed to transport materials within limited spaces. Unlike larger conveyor systems, they are often more flexible and can be customized to fit various production line configurations. Their design allows for easy integration into existing workflows, making them an ideal choice for small to medium-sized enterprises. Whether you’re dealing with fragile components or heavy materials, a small conveyor system can be tailored to meet your specific needs.
Types of Small Conveyor Systems
- Belt Conveyors: These are among the most common types used in manufacturing. Ideal for transporting bulk materials and products, belt conveyors provide smooth and continuous movement. They can handle various shapes and sizes, making them versatile for different production needs.
- Roller Conveyors: Best suited for manual or gravity-assisted transport, roller conveyors are commonly used in warehouses and distribution centers. The ease of movement provided by roller conveyors helps streamline operations and reduce physical strain on workers.
- Modular Conveyors: These systems are highly flexible and easy to customize for specific needs. Modular conveyors can be reconfigured and expanded as production requirements change, making them a smart long-term investment for businesses planning for growth.
Type | Best For | Advantages |
---|---|---|
Belt Conveyors | Bulk materials | Smooth, continuous movement |
Roller Conveyors | Manual transport | Low maintenance, cost-effective |
Modular Conveyors | Custom applications | Highly adaptable |
Benefits of Implementing a Small Conveyor System
Increased Efficiency
One of the primary advantages of a small conveyor system is the significant increase in efficiency it brings to production lines. By automating the transport of materials, businesses can reduce bottlenecks and ensure that each stage of production runs smoothly. This automation minimizes the need for manual handling, which can lead to delays and errors. Additionally, a small conveyor system allows for real-time tracking of materials, ensuring that inventory levels are always maintained and that production schedules are adhered to.
Space Optimization
Small conveyor systems are designed to fit in tight spaces, making them perfect for facilities with limited floor space. Their compact design allows for better utilization of the production area, enabling manufacturers to maintain high output without requiring a large footprint. By implementing a conveyor system, businesses can create efficient workflows that maximize available space, often integrating them into existing layouts without extensive renovations or disruptions.
Cost-Effective Solution
Implementing a small conveyor system can lead to cost savings in the long run. While the initial investment may vary, the reduced labor costs and increased productivity often justify the expense. Many companies find that the return on investment (ROI) from automating processes is realized within a short timeframe. Furthermore, the decreased likelihood of errors and product damage leads to fewer financial losses and a more stable production environment.
Improved Safety
Safety is a top priority in any production environment. Small conveyor systems can help minimize workplace injuries by reducing the need for manual lifting and transporting of heavy items. This not only protects employees but also contributes to a more efficient workflow. By automating repetitive tasks, businesses can create a safer workplace, leading to higher employee morale and lower turnover rates.
Flexibility and Customization
Small conveyor systems are highly customizable. Whether you need a conveyor that can handle different product sizes or one that can be adjusted for specific production requirements, there are options available to meet your needs. This flexibility is crucial for businesses that frequently change their product lines or need to adapt to new manufacturing processes.
How to Choose the Right Small Conveyor System
Selecting the appropriate small conveyor system requires careful consideration of various factors, including:
Type of Materials
Different materials may require specific conveyor types. Consider the weight, size, and shape of the products you plan to transport. For instance, heavy items might require a robust belt conveyor, while smaller components might be better suited for a roller system.
Production Volume
Understanding your production volume helps determine the conveyor system’s speed and capacity. High-volume operations may require more robust systems that can handle continuous flow, while smaller operations may benefit from simpler setups.
Layout of the Production Line
The design of your production line will significantly impact the type of conveyor you need. Assess the available space and configuration options to find a system that integrates seamlessly with your existing operations.
Future Scalability
Choose a conveyor system that allows for future growth. Scalability ensures that your investment remains viable as your production needs change, allowing for expansions without requiring a complete overhaul of your system.
Integration with Existing Systems
Integrating a small conveyor system into your existing production line can seem daunting, but it can be a seamless process with proper planning. Here are steps to ensure a smooth integration:
Conduct a Workflow Analysis
Analyze your current production workflow to identify bottlenecks and areas where a conveyor system can add value. This analysis will provide insights into the specific functions the conveyor should perform.
Collaborate with Experts
Consulting with conveyor system experts can provide valuable insights into the best solutions for your needs. They can help tailor a system that fits seamlessly into your operations, ensuring optimal performance and efficiency.
Plan for Downtime
Implementing a new system may require some downtime. Planning for this downtime can help minimize disruption to your production process and allow for a smoother transition.
Case Study: Successful Implementation of a Small Conveyor System
Overview
A mid-sized manufacturer of consumer goods faced challenges with slow product movement between different production stages. After implementing a small conveyor system, they saw significant improvements in efficiency and output.
Results
- Before Implementation: Average production time per unit was 5 minutes, leading to bottlenecks and delays.
- After Implementation: Average production time per unit dropped to 3 minutes, demonstrating a clear improvement in workflow efficiency.
Metric | Before Implementation | After Implementation |
---|---|---|
Production Time (min) | 5 | 3 |
Labor Costs ($) | 15,000 | 10,000 |
Output (Units/Day) | 500 | 800 |
This case study highlights the tangible benefits that can be realized by integrating a small conveyor system into existing operations.
Potential Challenges and Solutions
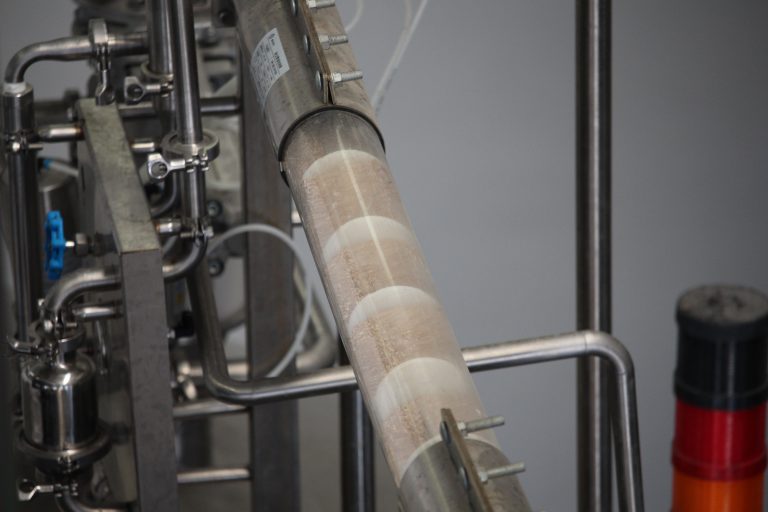
Space Constraints
Challenge: Limited space can restrict the layout of a small conveyor system, making it difficult to find a suitable configuration.
Solution: Modular conveyor systems can be tailored to fit specific dimensions and operational needs, ensuring they can be effectively utilized even in compact environments.
Maintenance
Challenge: Conveyor systems require regular maintenance to function optimally. Neglecting this can lead to breakdowns and operational inefficiencies.
Solution: Establishing a routine maintenance schedule can help prevent downtime and ensure the longevity of the conveyor system. Regular checks and preventive measures are essential for optimal performance.
Conclusion
Incorporating a small conveyor system into your production line can lead to substantial benefits, including increased efficiency, cost savings, and improved safety. By understanding the types of systems available and how to integrate them effectively, manufacturers can streamline their operations and maintain a competitive edge in their industry. Investing in a small conveyor system is not just about enhancing productivity; it’s about creating a sustainable and efficient future for your business.
FAQ
Q:What is a small conveyor system?
A:A small conveyor system is a compact, automated solution designed to transport materials efficiently within production lines, suitable for small to medium-sized operations.
Q:How can a small conveyor system save costs?
A:By reducing manual labor and increasing production efficiency, a small conveyor system can lower operational costs, leading to a favorable return on investment.
Q:What types of materials can small conveyor systems handle?
A:Small conveyor systems can transport a wide range of materials, including packaged goods, bulk items, and small components, making them versatile for various applications.
Q:How do I know if a small conveyor system is right for my business?
A:Assess your production needs, including volume, space, and material types, to determine if a small conveyor system aligns with your operational goals and challenges.
Q:Can small conveyor systems be customized?
A:Yes, small conveyor systems are highly customizable to fit specific production needs and layouts, ensuring optimal integration into your workflow.
Q:What are the maintenance requirements for a small conveyor system?
A:Regular maintenance includes checking for wear and tear, lubrication of moving parts, and ensuring proper alignment to prevent operational issues, which helps maintain efficiency.
Q:How long does it take to implement a small conveyor system?
A:Implementation time can vary, but with proper planning, a small conveyor system can typically be integrated within a few days to weeks, depending on complexity and operational needs.