Introduction
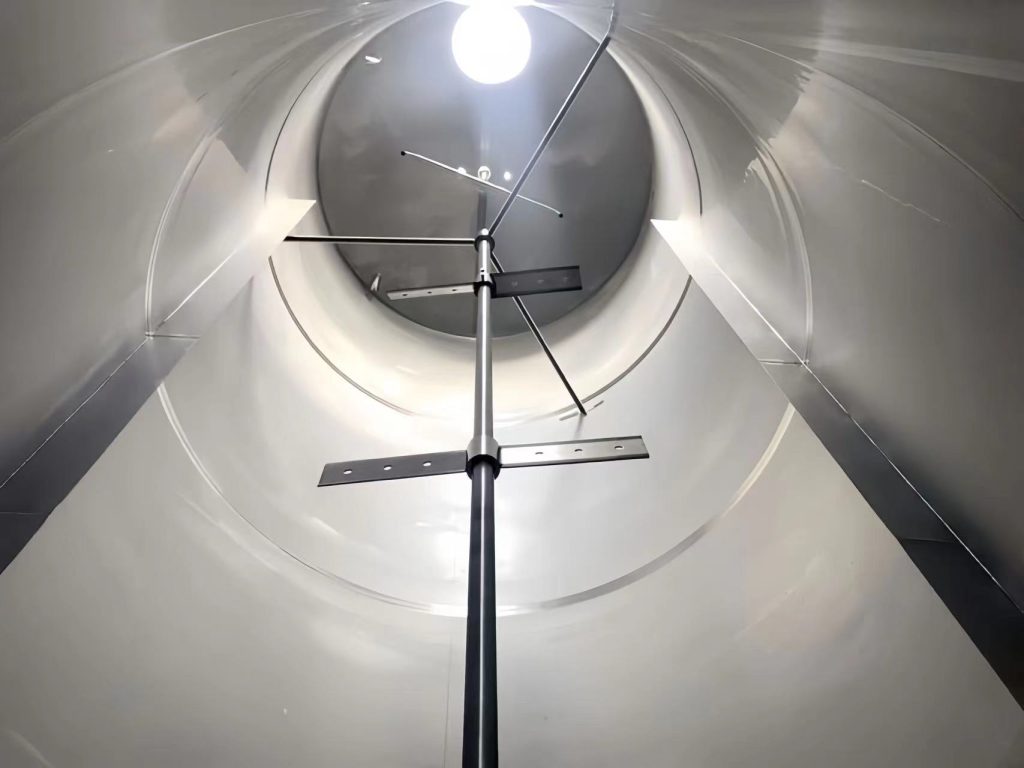
In the realm of modern manufacturing, tank mixers have become indispensable tools. They play a crucial role in ensuring product consistency, efficiency, and quality across various industries. From chemical processing to food and beverage production, tank mixers help achieve the desired homogeneity and effectiveness of materials. This blog delves into the essential aspects of mixing tanks, exploring their types, functions, applications, and benefits. We will also provide insights through detailed tables and address common queries about these vital devices.
Understanding Tank Mixers
What is a Tank Mixer?
A tank mixer is a device used to blend, agitate, or stir substances within a tank or vessel. It is designed to ensure uniformity and consistency of the mixed products, which is critical in manufacturing processes. Tank mixers come in various designs, including paddle mixers, turbine mixers, and impeller mixers, each suited for specific applications and types of fluids.
Types of Tank Mixers
There are several types of mixing tanks, each tailored to different mixing needs:
- Paddle Mixers: Utilize rotating paddles to mix substances. They are ideal for thick, viscous materials.
- Turbine Mixers: Employ high-speed rotating blades to create turbulence and ensure thorough mixing. Suitable for low to medium viscosity fluids.
- Impeller Mixers: Feature blades that push fluids in a radial or axial direction, making them versatile for various mixing tasks.
- Static Mixers: Operate without moving parts, using fixed elements to mix fluids as they pass through.
The Importance of Tank Mixers in Manufacturing
Enhancing Product Consistency
In manufacturing, product consistency is crucial for maintaining quality and meeting regulatory standards. Tank mixers help achieve uniform blending of raw materials, ensuring that every batch of product is of the same high quality. This consistency is particularly important in industries such as pharmaceuticals, where precise formulations are required.
Improving Efficiency
Mixing tanks contribute to operational efficiency by reducing the time required for mixing processes. High-quality mixers can achieve desired results faster, minimizing downtime and increasing production throughput. This efficiency is essential for meeting production targets and maintaining a competitive edge in the market.
Reducing Waste
Effective mixing reduces the likelihood of waste by ensuring that all materials are thoroughly blended and utilized. This reduction in waste not only benefits the environment but also helps in reducing overall production costs.
Applications of Tank Mixers
Chemical Processing
In chemical manufacturing, mixing tanks are used to blend various chemicals and ensure proper reactions. They are crucial for mixing components that need to be combined under specific conditions, such as temperature and pressure.
Food and Beverage Industry
Tank mixers are extensively used in the food and beverage industry to mix ingredients, emulsify products, and achieve the desired texture and flavor. They play a significant role in maintaining product quality and safety.
Pharmaceutical Industry
In pharmaceuticals, mixing tanks are used to blend active ingredients and excipients to create consistent formulations. They help ensure that medications are effective and safe for consumption.
Key Features to Consider in Tank Mixers
Mixing Speed
The speed at which a tank mixer operates affects its efficiency and effectiveness. High-speed mixers are suitable for low-viscosity fluids, while slower speeds may be required for thicker materials.
Material of Construction
The material of the mixing tank affects its durability and compatibility with various substances. Stainless steel is commonly used for its resistance to corrosion and ease of cleaning.
Mixer Configuration
The configuration of the mixer, including the type and arrangement of blades or paddles, impacts its performance. Different configurations are suited for specific mixing tasks and fluid types.
Benefits of Using Tank Mixers
Increased Production Capacity
By improving the efficiency of mixing processes, mixing tanks help increase production capacity. This enhancement is beneficial for meeting higher demand and expanding manufacturing operations.
Enhanced Product Quality
Tank mixers ensure that products are consistently mixed to meet quality standards. This consistency helps in building a reliable brand reputation and gaining customer trust.
Cost Savings
Effective tank mixers contribute to cost savings by reducing waste and improving production efficiency. This reduction in costs can lead to increased profitability and a better return on investment.
Table: Key Specifications of Different Tank Mixers
Mixer Type | Ideal Use | Speed Range | Material of Construction | Typical Viscosity Range |
---|---|---|---|---|
Paddle Mixer | Thick, viscous materials | Low to medium | Stainless Steel | High |
Turbine Mixer | Low to medium viscosity | High | Stainless Steel/Alloy | Medium to Low |
Impeller Mixer | Versatile applications | Variable | Stainless Steel | Low to Medium |
Static Mixer | Continuous processes | N/A | Plastic/Metal | Low to Medium |
Challenges and Solutions
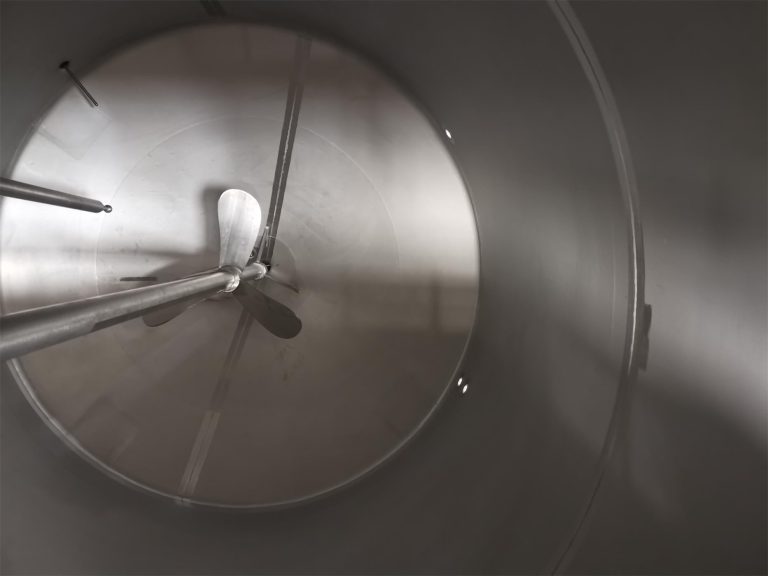
Maintenance and Cleaning
Regular maintenance and cleaning of mixing tanks are essential to ensure their optimal performance. Proper procedures and schedules should be established to avoid contamination and maintain hygiene.
Selection of the Right Mixer
Choosing the appropriate tank mixer for specific applications can be challenging. It requires careful consideration of factors such as fluid properties, mixing requirements, and operational conditions.
Managing Energy Consumption
Tank mixers can consume significant amounts of energy. Energy-efficient models and practices should be adopted to minimize energy use and reduce operational costs.
Conclusion
Tank mixers are vital components in modern manufacturing processes. They ensure product consistency, enhance efficiency, and contribute to overall operational success. By understanding the various types of tank mixers, their applications, and the factors to consider, manufacturers can make informed decisions and optimize their mixing processes. As industries continue to evolve, the role of mixing tanks will remain central to achieving high-quality and efficient production outcomes.
FAQ
What are the main types of tank mixers?
The main types of tank mixers include paddle mixers, turbine mixers, impeller mixers, and static mixers. Each type is designed for specific mixing needs and fluid properties.
How do mixing tanks improve efficiency in manufacturing?
Mixing tanks improve efficiency by reducing the time required for mixing processes, minimizing waste, and ensuring consistent product quality. This leads to increased production throughput and cost savings.
What factors should be considered when selecting a tank mixer?
When selecting a tank mixer, consider factors such as mixing speed, material of construction, mixer configuration, and the specific requirements of the fluid being mixed.
How often should mixing tanks be maintained?
Mixing tanks should be regularly maintained according to the manufacturer’s guidelines and the specific operational conditions. Regular cleaning and inspections are essential to ensure optimal performance and avoid contamination.
What are the common challenges associated with tank mixers?
Common challenges include maintenance and cleaning, selecting the right mixer for specific applications, and managing energy consumption. Addressing these challenges involves implementing proper procedures and choosing efficient equipment.