Introduction
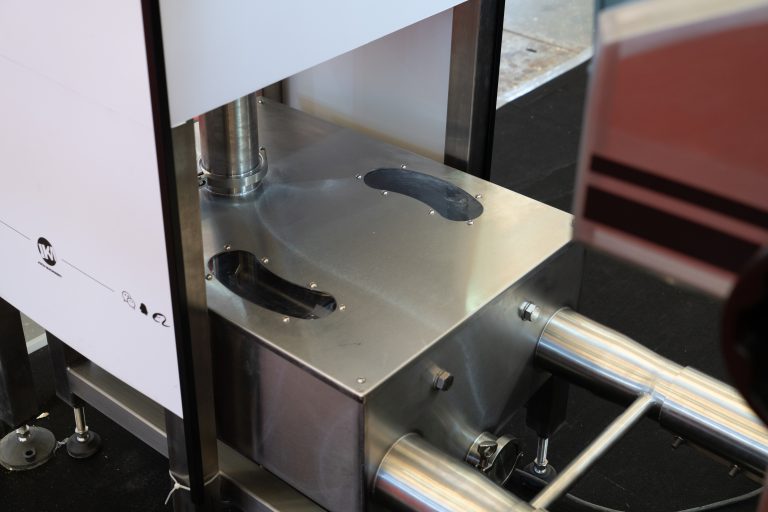
In today’s fast-paced industrial landscape, efficiency and productivity are paramount. Businesses across various sectors are constantly seeking innovative solutions to streamline their operations,reduce costs, and enhance overall output. Among the many advancements in material handling technology, industrial conveyor systems stand out as a cornerstone of modern manufacturing and logistics. These systems, ranging from simple belt conveyors to complex automated networks, offer a multitude of benefits that can significantly impact a company’s bottom line. This comprehensive guide delves into the numerous advantages of industrial conveyor systems, exploring their diverse applications and highlighting their crucial role in optimizing industrial processes. We will explore various aspects, including increased efficiency, improved safety, reduced labor costs, and enhanced flexibility, demonstrating why industrial conveyor systems are an indispensable asset for businesses striving for success in a competitive market.
Enhanced Efficiency with Industrial Conveyor Systems
One of the most significant advantages of implementing industrial conveyor systems is the dramatic improvement in operational efficiency. These systems automate the movement of materials, eliminating the need for manual handling and significantly reducing the time required to transport goods within a facility. This automation leads to several key benefits:
- Increased Throughput: Industrial conveyor systems can move large volumes of materials quickly and consistently, leading to a substantial increase in throughput. This is particularly beneficial for businesses with high production volumes or demanding delivery schedules.
- Reduced Handling Time: By automating material movement, conveyor systems minimize the time spent on manual handling, freeing up valuable employee time for other tasks. This reduction in handling time translates directly into increased productivity and faster turnaround times.
- Continuous Flow: Conveyor systems facilitate a continuous flow of materials through the production process, eliminating bottlenecks and delays. This continuous flow ensures a smooth and efficient workflow, maximizing overall output.
- Optimized Space Utilization: Industrial conveyor systems can be designed to navigate complex layouts and utilize vertical space, optimizing the use of available floor space. This is especially important in facilities with limited space.
Streamlining Production Processes with Conveyors
Industrial conveyor systems can be customized to fit specific production needs, seamlessly integrating into existing workflows. This adaptability allows businesses to optimize their processes and achieve greater efficiency. For example, in a manufacturing setting, a conveyor system can transport parts between workstations, ensuring a smooth and continuous production line. In a warehouse, a conveyor system can automate the movement of packages from receiving to shipping, significantly speeding up the order fulfillment process.
Improved Safety with Industrial Conveyor Systems
Manual handling of materials can be a major source of workplace injuries, including strains, sprains, and back injuries. Industrial conveyor systems significantly reduce the risk of these injuries by automating the movement of heavy or awkward items. This leads to a safer work environment for employees and reduces the costs associated with workplace accidents.
- Reduced Manual Lifting: By automating material handling, conveyor systems minimize the need for manual lifting, reducing the risk of back injuries and other musculoskeletal disorders.
- Controlled Movement: Conveyor systems provide controlled movement of materials, preventing them from falling or shifting, which can cause injuries or damage to goods.
- Ergonomic Benefits: By reducing the physical strain on workers, conveyor systems contribute to a more ergonomic work environment, improving employee well-being and productivity.
Minimizing Workplace Hazards with Conveyor Integration
Implementing industrial conveyor systems can significantly minimize workplace hazards associated with manual material handling. For example, in a distribution center, a conveyor system can automate the unloading of trucks, eliminating the need for workers to manually lift and carry heavy boxes. This not only reduces the risk of injuries but also speeds up the unloading process.
Reduced Labor Costs with Industrial Conveyor Systems
While the initial investment in an industrial conveyor system may seem significant, the long-term cost savings can be substantial. By automating material handling, businesses can reduce their reliance on manual labor, leading to lower labor costs.
- Reduced Manpower Requirements: Conveyor systems can automate tasks that would otherwise require multiple employees, reducing the need for manpower and associated labor costs.
- Lower Overtime Costs: By streamlining operations and increasing efficiency, conveyor systems can help reduce the need for overtime, leading to further cost savings.
- Increased Productivity per Employee: By freeing up employees from manual handling tasks, conveyor systems allow them to focus on more value-added activities, increasing productivity per employee.
Long-Term Cost Efficiency of Conveyor Automation
The long-term cost efficiency of industrial conveyor systems extends beyond direct labor cost reductions. By minimizing handling errors and damage to goods, these systems also contribute to lower material waste and reduced replacement costs. Furthermore, the increased efficiency and throughput achieved with conveyor systems can lead to higher revenue generation, further enhancing the return on investment.
Enhanced Flexibility with Industrial Conveyor Systems
Industrial conveyor systems are highly adaptable and can be customized to meet the specific needs of a wide range of industries and applications. This flexibility is a key advantage, allowing businesses to tailor their material handling systems to their unique requirements.
- Customizable Configurations: Conveyor systems can be configured in various ways to accommodate different layouts, inclines, and material types.
- Integration with Other Systems: Conveyor systems can be seamlessly integrated with other automation technologies, such as robotics, barcode scanners, and warehouse management systems (WMS), creating a fully integrated and automated workflow.
- Scalability: Conveyor systems can be easily scaled up or down to accommodate changes in production volume or business needs.
Adapting Conveyors to Diverse Industrial Needs
The versatility of industrial conveyor systems is evident in their wide range of applications across diverse industries. From food processing and pharmaceuticals to automotive and e-commerce, conveyor systems play a crucial role in optimizing material handling processes.
Types of Industrial Conveyor Systems
There are various types of industrial conveyor systems, each designed for specific applications and material handling needs. Understanding the different types is crucial for selecting the right system for your business.
Conveyor Type | Material Handled | Key Features | Common Applications |
---|---|---|---|
Belt Conveyors | Packages, boxes, bulk materials | Versatile, reliable, can handle a wide range of materials | Manufacturing, warehousing, distribution, mining |
Roller Conveyors | Packages, boxes, pallets | Simple, cost-effective, ideal for gravity-powered or manual movement | Packaging, assembly lines, order picking |
Chain Conveyors | Heavy loads, pallets, irregular shapes | Durable, strong, can handle heavy loads and harsh environments | Automotive, heavy manufacturing, metalworking |
Overhead Conveyors | Parts, assemblies, garments | Utilizes overhead space, frees up floor space | Manufacturing, assembly lines, garment industry |
Vertical Conveyors | Packages, boxes, totes | Moves materials vertically, ideal for multi-level facilities | Warehousing, distribution centers, manufacturing |
Screw Conveyors | Bulk materials (powders, granules) | Efficient for moving bulk materials vertically or horizontally | Food processing, chemical processing, agriculture |
Vibrating Conveyors | Bulk materials (powders, granules, small parts) | Moves materials through vibration, gentle handling for fragile materials | Food processing, pharmaceuticals, recycling |
Choosing the Right Conveyor System
Selecting the appropriate industrial conveyor system requires careful consideration of several factors, including the type of material being handled, the required throughput, the available space, and the budget. Consulting with a reputable conveyor system supplier can help businesses make informed decisions and choose the optimal system for their needs.
Maintenance and Upkeep of Industrial Conveyor Systems
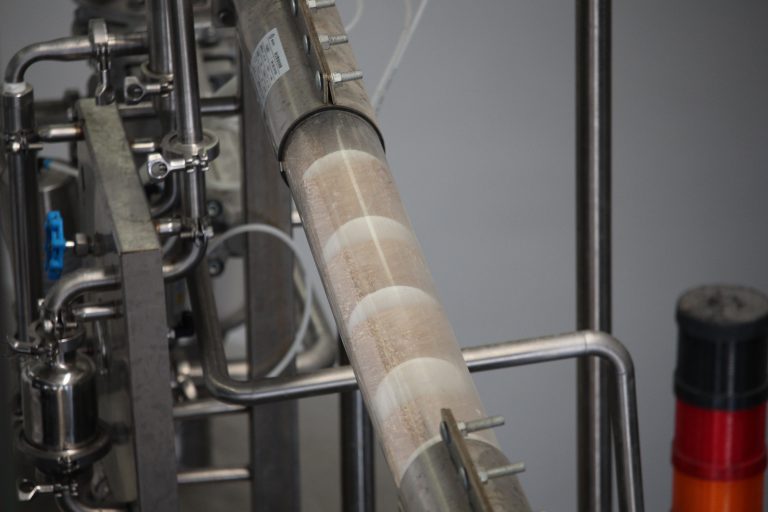
Proper maintenance is essential for ensuring the reliable and efficient operation of industrial conveyor systems. Regular inspections, lubrication, and component replacement can help prevent downtime and extend the lifespan of the system.
- Regular Inspections: Regular visual inspections can identify potential problems early on, preventing costly breakdowns.
- Lubrication: Proper lubrication of moving parts is crucial for reducing friction and wear, ensuring smooth operation and extending component life.
- Component Replacement: Worn or damaged components should be replaced promptly to prevent further damage and ensure the continued reliability of the system.
Maximizing Conveyor Lifespan Through Preventive Measures
Implementing a preventive maintenance program can significantly extend the lifespan of industrial conveyor systems and minimize downtime. This program should include regular inspections, lubrication, cleaning, and component replacement based on manufacturer recommendations and operating conditions.
Conclusion
In conclusion, industrial conveyor systems offer a wide range of benefits that can significantly improve a business’s efficiency, safety, and profitability. From increased throughput and reduced labor costs to enhanced flexibility and improved safety, these systems are an indispensable asset for businesses across various industries. By carefully selecting the right type of conveyor system and implementing a proper maintenance program, businesses can maximize their return on investment and gain a significant competitive edge in today’s demanding market. The advantages are clear: optimized material flow, minimized manual handling, reduced operational costs, and enhanced workplace safety. Investing in industrial conveyor systems is not just an expense; it’s a strategic investment in the future success and growth of any modern industrial operation.
FAQ
What are the primary applications of industrial conveyor systems?
Industrial conveyor systems are used in a wide range of industries, including manufacturing, warehousing, distribution, food processing, pharmaceuticals, mining, and e-commerce. They are used for various applications, such as material handling, assembly line automation, packaging.
How do I choose the right conveyor system for my business?
Choosing the right conveyor system requires careful consideration of several factors, including the type of material being handled, the required throughput, the available space, and the budget. Consulting with a reputable conveyor system supplier can help businesses make informed decisions.
What are the different types of industrial conveyor systems?
There are many types of conveyor systems, including belt conveyors, roller conveyors, chain conveyors, overhead conveyors, vertical conveyors, screw conveyors, and vibrating conveyors. Each type is designed for specific applications and material handling needs.