Introduction
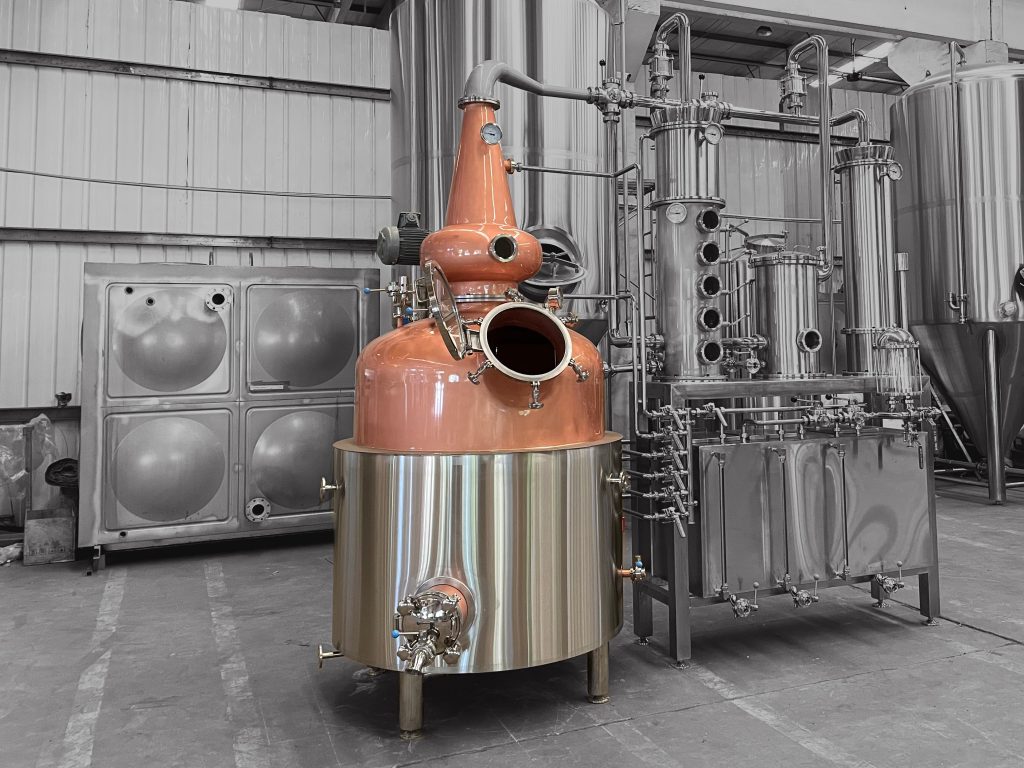
Steam condensers are crucial components in various industrial processes, particularly in power generation and chemical processing. They play a vital role in improving efficiency, conserving water, and reducing environmental impact. This comprehensive blog post delves into the numerous benefits of using steam condensers, exploring their working principles, diverse applications, and advantages over other cooling methods. We will also address frequently asked questions and conclude with a summary of the key benefits.
What are Steam Condensers and How Do They Work?
Steam condensers are heat exchangers designed to condense steam from its gaseous phase back into a liquid state (water). This process involves removing the latent heat of vaporization from the steam. There are two main types of steam condensers:
- Surface Condensers: In surface condensers, the steam and the cooling medium (usually water) are separated by a heat transfer surface, typically tubes. The steam condenses on the outside of the tubes, while the cooling water flows inside. This prevents direct contact between the steam and the cooling water, allowing for the recovery of high-quality condensate.
- Direct Contact Condensers (Jet Condensers): In direct contact condensers, the steam and the cooling water mix directly. The steam condenses as it comes into contact with the cooler water. While simpler in design, direct contact condensers result in the mixing of condensate and cooling water, making condensate recovery more challenging.
The condensation process creates a vacuum, which helps to improve the efficiency of the steam turbine or other equipment connected to the condenser. This vacuum allows for greater expansion of the steam, extracting more energy.
Importance of Vacuum in Steam Condenser Operation
The vacuum created by the condensation process is a crucial aspect of steam condenser operation. The lower the pressure in the condenser, the greater the pressure difference between the turbine exhaust and the condenser, leading to more efficient energy conversion. Maintaining a high vacuum is essential for maximizing the performance of steam power plants.
Key Benefits of Steam Condensers
Steam condensers offer a wide range of advantages across various applications. Here are some of the most significant benefits:
Increased Thermal Efficiency with Steam Condenser
By condensing the exhaust steam, condensers create a vacuum that significantly reduces the back pressure on the steam turbine. This allows the turbine to extract more work from the steam, leading to a substantial improvement in thermal efficiency. In power plants, this translates to lower fuel consumption and reduced operating costs.
Water Conservation with Steam Condenser
In many industrial processes, water is used as the cooling medium in steam condenser. Closed-loop cooling systems can be implemented, significantly reducing water consumption compared to once-through cooling systems. This is particularly important in regions with limited water resources.
Reduced Environmental Impact with Steam Condensers
By improving thermal efficiency and reducing water consumption, steam condenser contribute to a smaller environmental footprint. Lower fuel consumption leads to reduced greenhouse gas emissions. Additionally, minimizing water usage helps to conserve this precious resource.
Condensate Recovery and Reuse with Steam Condensers
Surface condensers allow for the recovery of high-quality condensate, which can be reused as boiler feedwater. This reduces the need for makeup water and saves on water treatment costs. Recovered condensate is also preheated, which further improves overall system efficiency.
Lower Operating Costs with Steam Condensers
The increased efficiency, reduced water consumption, and condensate recovery offered by steam condensers all contribute to lower operating costs. These savings can be substantial over the lifetime of the equipment.
Improved Plant Performance and Reliability with Steam Condensers
By maintaining a stable vacuum and ensuring efficient condensation, steam condenser contribute to improved plant performance and reliability. This minimizes downtime and maximizes production output.
Versatility of Steam Condensers in Various Industries
Steam condensers find applications in diverse industries, including power generation, chemical processing, refineries, and desalination plants. Their versatility makes them an essential component in various thermal systems.
Applications of Steam Condensers
Steam condensers are used in a wide range of applications, including:
- Power Plants: Steam condenser are integral to steam turbine power plants, where they condense the exhaust steam from the turbines.
- Chemical Processing: In chemical plants, steam condenser are used in various processes, such as distillation and evaporation.
- Refineries: Refineries utilize steam condensers in various refining processes.
- Desalination Plants: Steam condensers play a vital role in thermal desalination processes, where they condense the steam used to evaporate seawater.
Comparison of Different Condenser Types
The following table summarizes the key differences between various types of condensers, focusing on their characteristics and applications:
Feature | Surface Condenser | Direct Contact Condenser (Jet) | Air-Cooled Condenser |
---|---|---|---|
Condensation Method | Indirect (through heat transfer surface) | Direct (mixing of steam and water) | Indirect (heat transfer to air) |
Condensate Quality | High (recoverable and reusable) | Mixed with cooling water | High (recoverable and reusable) |
Vacuum Level | High | Moderate | Lower compared to water-cooled condensers |
Cooling Medium | Water (or other fluid) | Water | Air |
Space Requirements | Moderate | Smaller | Larger |
Capital Cost | Higher | Lower | Higher |
Operating Cost | Lower (due to condensate recovery and efficiency) | Higher (due to water consumption) | Higher (due to fan power consumption), lower water cost |
Typical Application | Power plants, large industrial processes | Smaller processes, where condensate recovery is not critical | Where water is scarce, smaller power plants, industrial applications |
Maintaining Steam Condensers for Optimal Performance
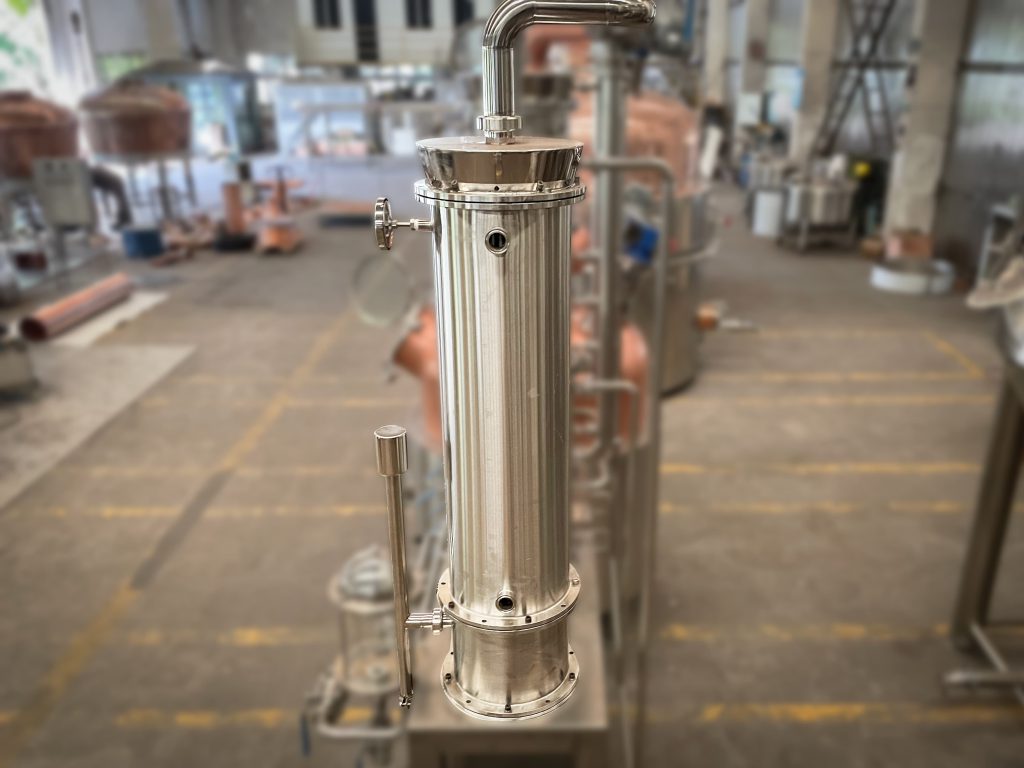
Regular maintenance is essential for ensuring the optimal performance and longevity of steam condensers. This includes:
- Cleaning: Regularly cleaning the heat transfer surfaces to remove fouling and scale buildup.
- Leak Testing: Checking for leaks in the tubes and other components.
- Vacuum Testing: Monitoring the vacuum level to ensure efficient operation.
- Cooling Water Treatment: Implementing appropriate cooling water treatment to prevent corrosion and scaling.
Importance of Regular Inspections of Steam Condensers
Regular inspections are crucial for identifying potential problems early on and preventing costly downtime. These inspections should include visual checks, performance monitoring, and non-destructive testing.
Conclusion
Steam condensers are essential components in various industrial processes, offering numerous benefits, including increased thermal efficiency, water conservation, reduced environmental impact, condensate recovery, and lower operating costs. By understanding the working principles, applications, and maintenance requirements of steam condensers, industries can maximize their benefits and contribute to more sustainable and efficient operations. The use of steam condensers represents a significant step towards optimizing energy usage and resource management. Their continued development and implementation are crucial for achieving greater efficiency and sustainability in various industrial sectors. This comprehensive analysis of steam condensers highlights their importance in modern industrial practices and emphasizes their role in improving overall system performance and minimizing environmental impact.
FAQ
Q: What is the primary function of a steam condenser?
A: The primary function of a steam condenser is to condense exhaust steam from its gaseous phase back into a liquid state (water).
Q: How does a steam condenser improve efficiency?
A: By creating a vacuum, steam condensers reduce the back pressure on the steam turbine, allowing it to extract more work from the steam.
Q: What are the different types of steam condensers?
A: The two main types are surface condensers and direct contact condensers (jet condensers).
Q: What are the benefits of condensate recovery?
A: Condensate recovery reduces the need for makeup water, saves on water treatment costs, and improves overall system efficiency.
Q: How often should steam condensers be maintained?
A: Regular maintenance should be performed according to the manufacturer’s recommendations and operating conditions.