Introduction
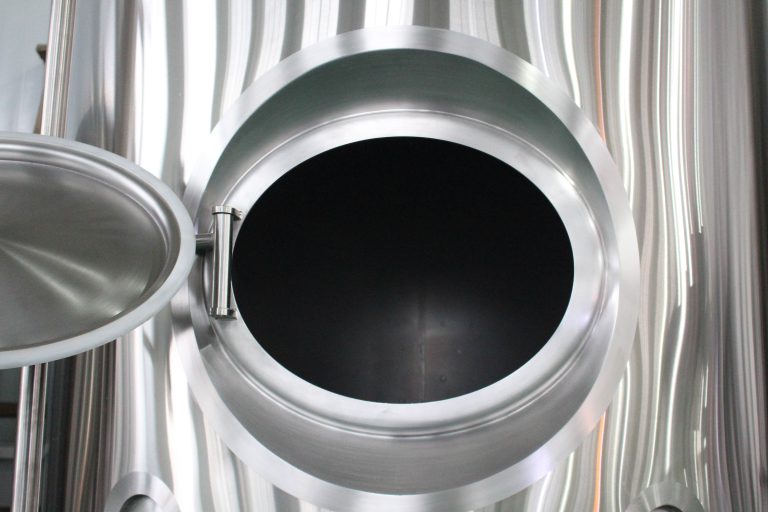
Brewery fermentation tanks are the heart of any brewery, where the magic of transforming wort into beer occurs. These vessels provide a controlled environment for yeast to consume sugars, producing alcohol and carbon dioxide. Understanding the different types of brewery fermentation tanks, their features, and how to properly maintain them is crucial for producing high-quality beer consistently. This comprehensive guide will delve into everything you need to know about brewery fermentation tanks, from basic principles to advanced considerations.
Types of Brewery Fermentation Tanks
Choosing the right type of brewery fermentation tank is essential for achieving the desired beer style and production scale. Several common types exist, each with its own advantages and disadvantages.
Cylindroconical Tanks (CCTs)
Cylindroconical tanks, often referred to as unitanks, are the most widely used type of brewery fermentation tank in modern breweries. Their conical bottom allows for easy yeast harvesting and trub removal, while the cylindrical body provides ample space for fermentation.
Unitanks for Primary and Secondary Fermentation
Unitanks are versatile because they can be used for both primary and secondary fermentation. This eliminates the need for transferring beer between vessels, reducing the risk of contamination and oxidation.
Open Fermentation Vessels
Open fermentation vessels are traditional tanks that are open to the air. While they offer unique flavor profiles due to wild yeast and bacteria exposure, they are more susceptible to contamination and require meticulous sanitation practices.
Horizontal Fermentation Tanks
Horizontal fermentation tanks are less common but offer advantages in terms of space utilization and temperature control. They are often used for lagering, a cold conditioning process.
Key Features of Brewery Fermentation Tanks
Several key features contribute to the performance and functionality of brewery fermentation tanks.
Tank Material: Stainless Steel
Stainless steel is the standard material for brewery fermentation tanks due to its durability, corrosion resistance, and ease of cleaning. Specifically, 304 or 316 stainless steel is preferred.
Cooling Jackets for Temperature Control
Cooling jackets are essential for maintaining the desired fermentation temperature. These jackets circulate glycol or other coolants to regulate the tank’s temperature.
Pressure Relief Valves and Manways
Pressure relief valves prevent over-pressurization within the tank, while manways provide access for cleaning and inspection.
Insulation for Energy Efficiency
Insulation helps maintain consistent temperatures and reduces energy consumption by minimizing heat transfer.
The Fermentation Process in Brewery Fermentation Tanks
The fermentation process within brewery fermentation tanks is a complex biological process.
Yeast Pitching and Growth
Yeast is pitched into the wort, where it begins to consume sugars and multiply.
Primary Fermentation: Sugar to Alcohol
During primary fermentation, the majority of sugars are converted into alcohol and carbon dioxide.
Secondary Fermentation and Conditioning
Secondary fermentation, or conditioning, allows the beer to mature and develop its flavor profile.
Cleaning and Sanitation of Brewery Fermentation Tanks
Proper cleaning and sanitation are crucial for preventing contamination and ensuring consistent beer quality.
CIP (Clean-in-Place) Systems
CIP systems automate the cleaning process, ensuring thorough sanitation without the need for manual scrubbing.
Sanitizing Agents: Chemicals and Heat
Various sanitizing agents, including chemicals and heat, are used to eliminate microorganisms within the tanks.
Brewery Fermentation Tank Sizing and Selection
Selecting the appropriate size and type of brewery fermentation tank depends on several factors.
Batch Size and Production Volume
The desired batch size and overall production volume will determine the necessary tank capacity.
Brewery Space and Layout
The available space within the brewery will influence the physical dimensions and layout of the tanks.
Budget Considerations for Brewery Fermentation Tanks
The budget allocated for brewery fermentation tanks will impact the choice of materials, features, and automation.
Factors Affecting Fermentation in Brewery Fermentation Tanks
Several factors influence the fermentation process within the tanks.
Temperature Control During Fermentation
Maintaining precise temperature control is crucial for yeast health and desired flavor development.
Yeast Strain and Viability
The chosen yeast strain and its viability will significantly impact the fermentation process.
Wort Composition and Gravity
The composition of the wort, including its sugar content (gravity), affects the fermentation rate and final alcohol content.
Pressure Management During Fermentation
Managing pressure within the tank can influence the production of esters and other flavor compounds.
Maintenance and Troubleshooting for Brewery Fermentation Tanks
Proper maintenance and troubleshooting are essential for extending the lifespan of brewery fermentation tanks and preventing costly downtime.
Regular Inspections and Cleaning Schedules
Regular inspections and adherence to cleaning schedules are crucial for preventing issues.
Troubleshooting Common Fermentation Problems
Understanding common fermentation problems, such as stuck fermentation or off-flavors, is essential for quick resolution.
Brewery Fermentation Tanks: A Comparison of Features
Feature | Description | Benefit |
---|---|---|
Material | 304 or 316 Stainless Steel | Durable, corrosion-resistant, easy to clean |
Cooling Jackets | External jackets circulating coolant (glycol) | Precise temperature control during fermentation |
Insulation | Layer of insulating material surrounding the tank | Maintains temperature, reduces energy consumption |
Pressure Relief Valve | Automatic valve that releases pressure if it exceeds a set limit | Prevents tank over-pressurization and potential damage |
Manway | Access port for cleaning, inspection, and maintenance | Easy access to the tank interior |
Conical Bottom | Sloped bottom for yeast and trub collection | Facilitates yeast harvesting and removal of sediment |
CIP System | Integrated cleaning system with spray balls and piping | Automated and thorough cleaning, reduces manual labor |
Advanced Considerations for Brewery Fermentation Tanks
For larger or more specialized breweries, several advanced considerations may come into play.
Automation and Control Systems
Automated systems can monitor and control various fermentation parameters, improving consistency and efficiency.
Specialized Tank Designs for Specific Beer Styles
Certain beer styles may benefit from specialized tank designs, such as horizontal tanks for lagering or open fermenters for wild ales.
Integration with Brewery Management Software
Integrating fermentation tank data with brewery management software can provide valuable insights into production efficiency.
Regulations and Safety Standards for Brewery Fermentation Tanks
Adhering to relevant regulations and safety standards is paramount for operating brewery fermentation tanks safely.
Pressure Vessel Safety Standards
Tanks must meet pressure vessel safety standards to prevent accidents related to over-pressurization.
Sanitary Design and Construction Standards
Tanks should be designed and constructed according to sanitary standards to prevent contamination.
Cost Considerations for Brewery Fermentation Tanks
The cost of brewery fermentation tanks can vary significantly depending on several factors.
Tank Size and Capacity Impact on Cost
Larger tanks generally cost more than smaller tanks.
Material and Feature Selection and Cost
The choice of materials and features, such as automation and specialized designs, will influence the final cost.
Future Trends in Brewery Fermentation Tank Technology
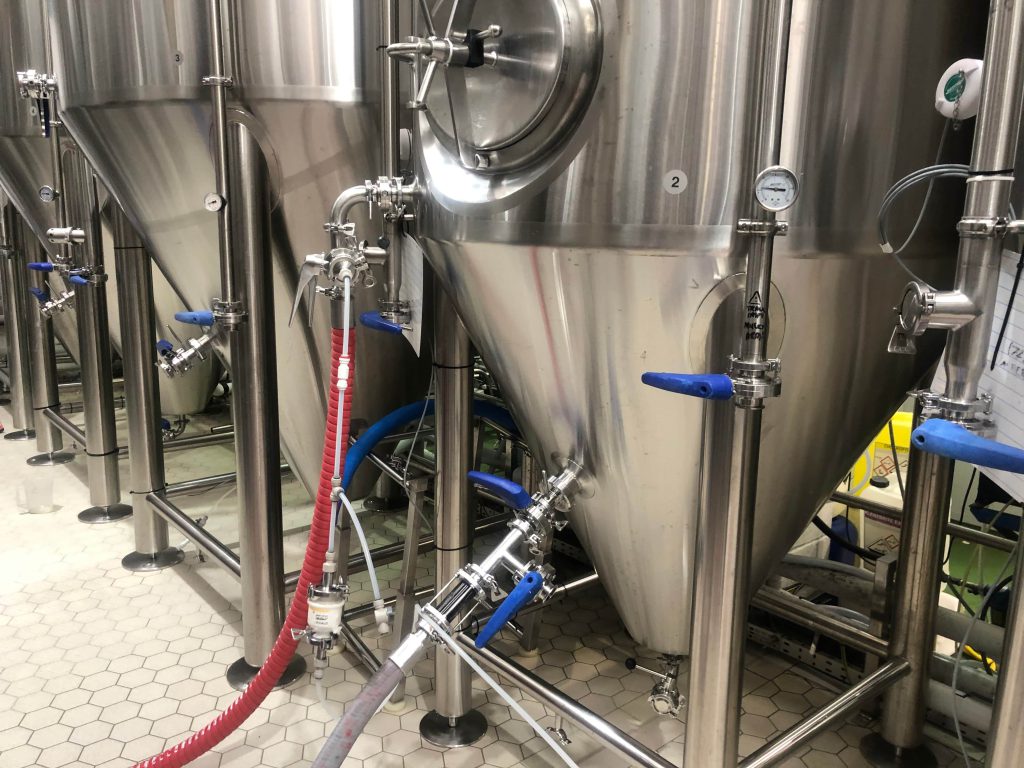
The field of brewery fermentation tank technology is constantly evolving.
Advancements in Temperature Control and Automation
New technologies are emerging to improve temperature control and automation, enhancing efficiency and consistency.
Sustainable and Energy-Efficient Tank Designs
There is a growing focus on developing sustainable and energy-efficient tank designs to reduce environmental impact.
Conclusion
Brewery fermentation tanks are essential for producing high-quality beer. By understanding the different types of tanks, their features, and the fermentation process, brewers can make informed decisions about tank selection and management. Proper cleaning, sanitation, maintenance, and adherence to safety standards are crucial for ensuring consistent beer quality and a safe working environment. As technology continues to advance, brewery fermentation tanks will likely become even more efficient, sustainable, and capable of producing a wider range of beer styles.
FAQ
What is the ideal temperature for fermentation in brewery fermentation tanks?
The ideal temperature depends on the yeast strain being used. Ale yeasts typically ferment at warmer temperatures (60-72°F or 15-22°C), while lager yeasts ferment at cooler temperatures (48-55°F or 9-13°C).
How long does fermentation typically take in brewery fermentation tanks?
Fermentation time can vary depending on the yeast strain, temperature, and wort gravity. Primary fermentation typically takes 1-2 weeks, while secondary fermentation can take several weeks or even months.
What is the difference between a unitank and a traditional fermentation tank?
A unitank can be used for both primary and secondary fermentation, eliminating the need for transferring beer between vessels. Traditional fermentation tanks are typically used for primary fermentation only.