Introduction
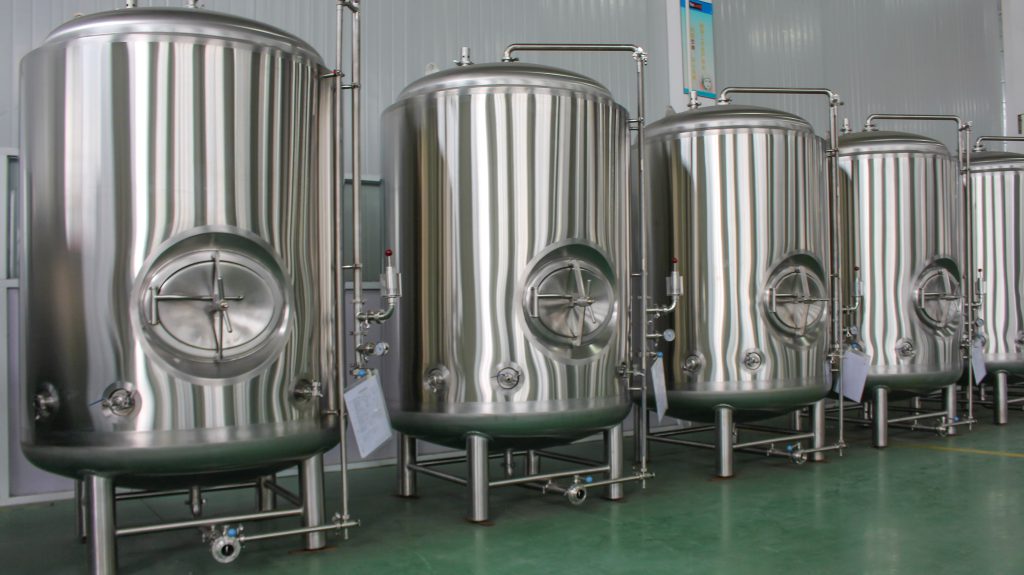
Choosing the right brewery tank manufacturers is a critical decision that can significantly impact the quality, efficiency, and scalability of your brewing operations. These tanks are the heart of any brewery, playing essential roles in mashing, lautering, boiling, fermentation, conditioning, and storage. Partnering with experienced and reliable brewery tank manufacturers ensures that you acquir equipment built to the highest standards, meeting your specific needs and regulatory requirements. This comprehensive guide will delve into the key factors you should consider when selecting brewery tank manufacturers to ensure a successful and sustainable brewing venture.
Understanding Your Brewery’s Specific Tank Requirements
Before reaching out to any brewery tank manufacturer, it’s crucial to have a clear understanding of your brewery’s specific tank requirements. This involves assessing your current and projected production capacity, the types of beer you plan to brew, and the available space in your brewery. Consider the following aspects:
Production Capacity and Tank Sizes from Brewery Tank Manufacturer
Determine your desired annual beer production. This will directly influence the required sizes and number of tanks. Brewery tank manufacturer offer a wide range of tank capacities, from small pilot system tanks to large-scale production vessels. Accurately forecasting your growth will help you choose tanks that can accommodate future expansion, potentially saving you significant costs in the long run. Discuss your production goals with potential brewery tank manufacturer to get their expert recommendations on optimal tank sizing.
Types of Beer and Specialized Tank Designs by Brewery Tank Manufacturer
Different beer styles may require specific tank configurations. For example, lagers typically require longer fermentation and maturation periods at colder temperatures, necessitating well-insulated tanks with precise temperature control. Sour beers might require dedicated tanks made of specific materials to prevent cross-contamination. When evaluating brewery tank manufacturer, inquire about their experience in fabricating tanks for the specific types of beer you intend to brew. Their expertise can ensure that the tanks are designed to optimize the brewing process for your desired styles.
Brewery Layout and Space Constraints When Working with Brewery Tank Manufacturers
The physical layout of your brewery will significantly impact the size and configuration of the tanks you can accommodate. Consider ceiling height, door widths, and any other spatial limitations. Brewery tank manufacturers can often provide customized tank designs to fit within your existing space. Sharing your brewery layout with potential manufacturers early in the process will help them propose feasible solutions and avoid potential installation challenges. Some brewery tank manufacturer also offer on-site consultation to assess your space and provide tailored recommendations.
Evaluating the Experience and Reputation of Brewery Tank Manufacturers
The experience and reputation of brewery tank manufacturer are paramount. Partnering with a well-established manufacturer with a proven track record can provide peace of mind and ensure you receive high-quality equipment and reliable service.
Years of Experience in the Brewing Industry Among Brewery Tank Manufacturers
Consider how long the brewery tank manufacturer have been in business. Manufacturers with many years of experience are likely to have a deep understanding of the brewing process and the specific requirements of breweries. They have likely encountered and overcome various challenges, refining their manufacturing processes and building expertise over time. Inquire about their history and significant projects they have completed.
Client Testimonials and References for Brewery Tank Manufacturers
Request client testimonials and references from brewery tank manufacturers you are considering. Speaking with their previous customers can provide valuable insights into their product quality, customer service, and overall reliability. Ask specific questions about the manufacturer’s responsiveness, adherence to timelines, and the performance of their tanks over time.
Industry Certifications and Standards Adhered to by Brewery Tank Manufacturer
Reputable brewery tank manufacturers will adhere to relevant industry certifications and standards, ensuring the safety and quality of their equipment. Inquire about certifications such as ASME (American Society of Mechanical Engineers) for pressure vessels and any food-grade certifications relevant to your region. Compliance with these standards demonstrates a commitment to quality and safety in their manufacturing processes.
Assessing the Quality and Materials Used by Brewery Tank Manufacturers
The quality of materials and construction directly impacts the longevity, performance, and sanitation of your brewery tanks. Choosing brewery tank manufacturers who prioritize high-quality materials and craftsmanship is essential.
Stainless Steel Grade and Tank Construction Standards of Brewery Tank Manufacturer
Food-grade stainless steel, typically 304 or 316L, is the standard material for brewery tanks due to its corrosion resistance, durability, and ease of cleaning. Inquire about the specific grade of stainless steel used by the brewery tank manufacturer and their welding procedures. High-quality welding is crucial to prevent leaks and ensure the structural integrity of the tanks. Look for manufacturers who employ skilled welders and have robust quality control processes.
Surface Finish and Sanitary Design Features Offered by Brewery Tank Manufacturers
The interior surface finish of the tanks is critical for maintaining hygiene and preventing microbial growth. Brewery tank manufacturer should offer smooth, polished surfaces that are easy to clean and sanitize. Sanitary design features, such as rounded corners, tri-clamp connections, and proper sloping for drainage, are also essential for preventing contamination and ensuring efficient cleaning processes. Discuss these features in detail with potential manufacturers.
Insulation and Cooling Systems Provided by Brewery Tank Manufacturers
Temperature control is vital in brewing, especially during fermentation and maturation. Brewery tank manufacturers should offer effective insulation and reliable cooling systems. Inquire about the type and thickness of insulation used, as well as the specifications of the cooling jackets and glycol systems they provide or recommend. Efficient temperature control contributes to consistent fermentation, beer quality, and energy efficiency.
Evaluating the Customization Options Offered by Brewery Tank Manufacturer
Every brewery has unique needs, and the ability to customize tanks can be a significant advantage. Brewery tank manufacturer who offer flexible customization options can provide solutions tailored to your specific requirements.
Tank Configurations and Fittings Available from Brewery Tank Manufacturers
Discuss your specific needs for tank configurations, such as the number and placement of ports, manways, and other fittings. Brewery tank manufacturer should be able to accommodate your requirements for CIP (Clean-in-Place) systems, level sensors, sample ports, and other necessary features. The flexibility in customizing these aspects can optimize your brewing processes and improve efficiency.
Integration with Existing Brewery Equipment by Brewery Tank Manufacturers
If you have existing brewery equipment, ensure that the new tanks from the brewery tank manufacturers can be seamlessly integrated. Discuss compatibility with your current piping, pumps, and control systems. Experienced manufacturers can provide solutions that ensure smooth integration and avoid potential bottlenecks in your workflow.
Unique Design Requirements and Collaboration with Brewery Tank Manufacturers
If you have unique design requirements or specific space constraints, choose brewery tank manufacturer who are willing to collaborate closely with you to develop tailored solutions. Their engineering and design teams should be able to translate your vision into functional and efficient tank designs. Open communication and a collaborative approach are key to achieving your desired outcomes.
Comparing Pricing and Value Offered by Brewery Tank Manufacturers
While price is an important consideration, it should not be the sole determining factor when selecting brewery tank manufacturers. Focus on the overall value, which includes the quality of materials, craftsmanship, features, and after-sales service.
Initial Investment Costs Quoted by Brewery Tank Manufacturer
Obtain detailed quotes from multiple brewery tank manufacturer, clearly outlining the costs of the tanks, accessories, and any additional services such as shipping and installation. Compare the quotes carefully, paying attention to the specifications and inclusions. Be wary of significantly lower prices, as they may indicate lower quality materials or construction.
Long-Term Operational Costs and Efficiency of Tanks from Brewery Tank Manufacturers
Consider the long-term operational costs associated with the tanks. Energy-efficient cooling systems and well-insulated tanks can lead to significant savings over time. Durable and well-maintained tanks will also have a longer lifespan, reducing the need for premature replacements. Evaluate the efficiency and durability offered by different brewery tank manufacturers.
Return on Investment and Value Proposition of Different Brewery Tank Manufacturers
Assess the return on investment (ROI) offered by different brewery tank manufacturer. While a higher initial investment in quality tanks may seem daunting, the long-term benefits of durability, efficiency, and consistent beer quality can lead to a better ROI in the long run. Consider the overall value proposition, including the manufacturer’s reputation, experience, and after-sales support.
Evaluating the Lead Times and Delivery Schedules of Brewery Tank Manufacturers
The lead time for manufacturing and delivering brewery tanks can vary significantly. It’s crucial to choose brewery tank manufacturers whose timelines align with your project schedule.
Typical Manufacturing Lead Times Quoted by Brewery Tank Manufacturers
Inquire about the typical manufacturing lead times for the tanks you require. These timelines can be influenced by factors such as the complexity of the design, the size of the order, and the manufacturer’s current production schedule. Obtain realistic estimates and factor these timelines into your overall brewery setup or expansion plan.
Shipping and Installation Timelines Provided by Brewery Tank Manufacturers
Understand the shipping and installation timelines provided by the brewery tank manufacturer. Coordinate these timelines with your brewery setup schedule to avoid delays. Some manufacturers offer installation services, while others may require you to arrange for third-party installation. Clarify these details upfront.
Communication and Project Management Throughout the Process with Brewery Tank Manufacturers
Effective communication and project management from the brewery tank manufacturers are essential for a smooth and timely delivery and installation process. Choose manufacturers who are responsive, provide regular updates, and have clear communication channels. A dedicated project manager can help ensure that the project stays on track and address any issues that may arise.
Assessing the After-Sales Service and Support Offered by Brewery Tank Manufacturers
The relationship with your brewery tank manufacturer should extend beyond the initial purchase. Reliable after-sales service and support are crucial for ensuring the long-term performance and longevity of your tanks.
Warranty and Maintenance Services Provided by Brewery Tank Manufacturers
Inquire about the warranty offered on the tanks and the availability of maintenance services. A comprehensive warranty provides protection against manufacturing defects. Regular maintenance can help prevent problems and prolong the lifespan of your equipment. Understand the terms of the warranty and the scope of the maintenance services offered.
Availability of Spare Parts and Technical Support from Brewery Tank Manufacturers
Ensure that the brewery tank manufacturers can provide spare parts and technical support when needed. Downtime due to equipment failure can be costly, so having access to timely support and readily available spare parts is crucial. Inquire about their spare parts inventory and the responsiveness of their technical support team.
Training and Documentation Provided by Brewery Tank Manufacturers
Some brewery tank manufacturers offer training on the operation and maintenance of their tanks. Comprehensive documentation, including manuals and diagrams, is also essential for proper use and troubleshooting. Inquire about the availability of training and the quality of the documentation provided.
Table of Considerations When Choosing Brewery Tank Manufacturers
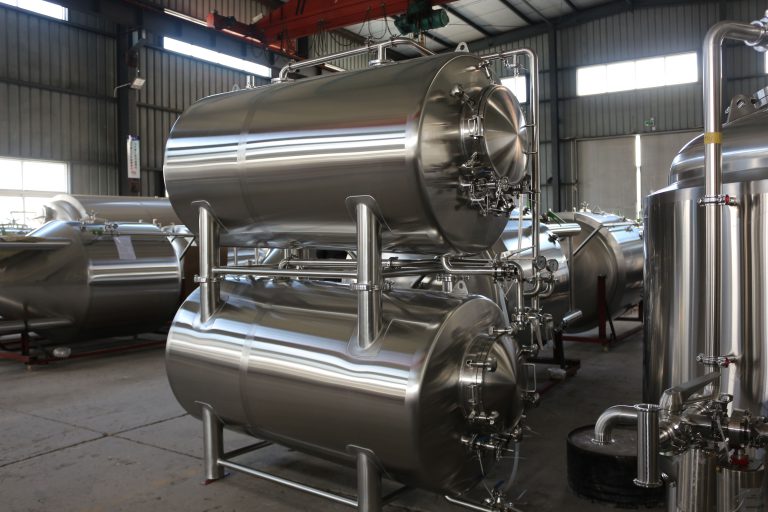
Feature | Key Considerations |
---|---|
Tank Requirements | Production capacity, beer styles, brewery layout, space constraints |
Experience & Reputation | Years in business, client testimonials, industry certifications |
Quality & Materials | Stainless steel grade, construction standards, surface finish, sanitary design, insulation, cooling systems |
Customization | Tank configurations, fittings, integration with existing equipment, unique design requirements |
Pricing & Value | Initial investment costs, long-term operational costs, ROI |
Lead Times & Delivery | Manufacturing lead times, shipping and installation timelines, communication and project management |
After-Sales Service | Warranty, maintenance services, spare parts availability, technical support, training, documentation |
Company Stability | Financial health, manufacturing capacity, long-term vision |
Location & Accessibility | Proximity for potential visits, ease of communication across time zones |
Conclusion
Selecting the ideal brewery tank manufacturers is a pivotal decision that will shape the future of your brewery. By carefully considering your specific requirements, evaluating the experience and reputation of potential partners, assessing the quality and customization options, comparing pricing and value, understanding lead times, and ensuring robust after-sales support, you can make an informed choice that sets your brewery up for success. Investing in high-quality tanks from reliable brewery tank manufacturers is an investment in the quality of your beer and the efficiency of your operations. Contact us today to discuss your brewery tank needs and discover how our expertise can help you achieve your brewing goals.
FAQ
What are the typical types of brewery tanks offered by brewery tank manufacturers?
Brewery tank manufacturers typically offer a range of tanks, including:
- Mash Tuns: Used for mixing malted grains with hot water to create mash.
- Lauter Tuns: Used to separate the sweet wort from the spent grains.
- Brew Kettles: Used for boiling the wort with hops.
- Whirlpools: Used to separate hop debris and trub from the boiled wort.
- Fermentation Tanks (Unitanks or Conical Fermenters): Used for fermenting the wort into beer.
- Conditioning Tanks (Lagering Tanks or Bright Beer Tanks): Used for maturing and carbonating the beer.
- Storage Tanks: Used for storing finished beer before packaging.
Some brewery tank manufacturers also offer specialized tanks for sour beers, pilot systems, and other unique brewing processes.
What is the difference between 304 and 316L stainless steel used by brewery tank manufacturers?
Both 304 and 316L stainless steel are commonly used by brewery tank manufacturers due to their excellent corrosion resistance and hygienic properties. However, 316L stainless steel contains molybdenum, which provides enhanced resistance to pitting and crevice corrosion, particularly in environments with high chloride content. While 304 stainless steel is suitable for most brewery applications, 316L may be preferred for certain processes or in coastal environments where corrosion risks are higher.
How important is insulation in brewery tanks provided by brewery tank manufacturers?
Insulation is crucial for maintaining stable temperatures in brewery tanks, especially fermentation and conditioning tanks. Effective insulation provided by brewery tank manufacturers offers several benefits:
- Temperature Stability: Reduces fluctuations in temperature, which can negatively impact fermentation.
- Energy Efficiency: Minimizes heat transfer, reducing the energy required for cooling.
- Condensation Prevention: Helps prevent condensation on the exterior of the tanks, which can lead to hygiene issues.
Consider the type and thickness of insulation offered by brewery tank manufacturers to ensure optimal temperature control and energy efficiency.