Introduction
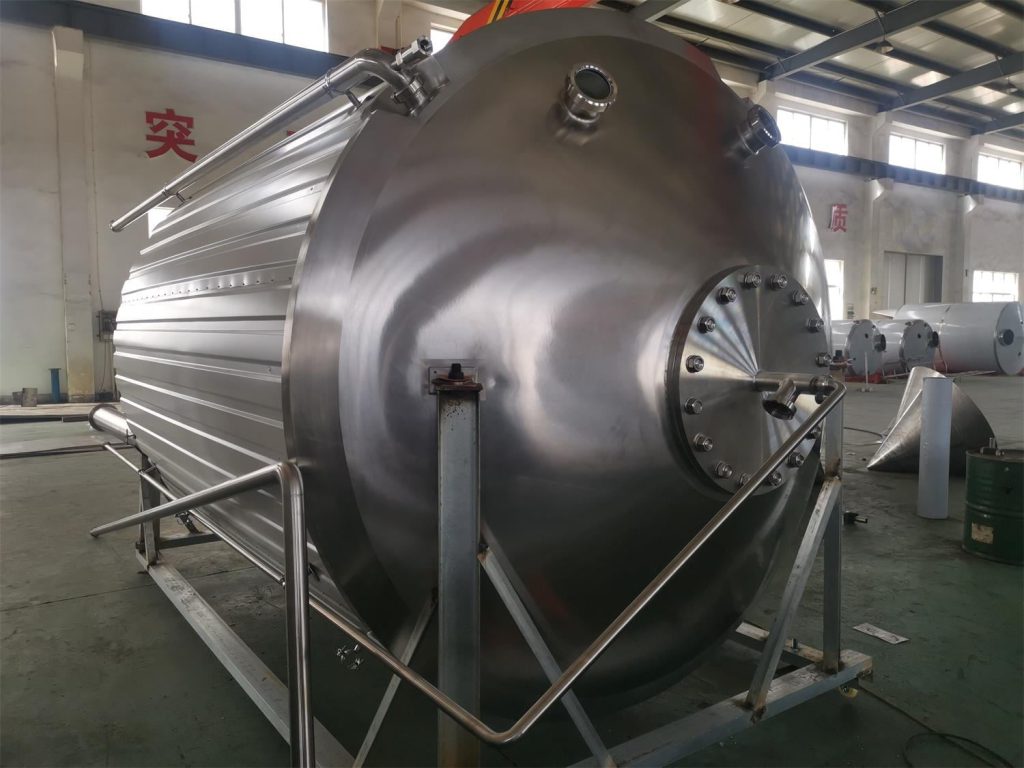
The selection of a suitable beverage tank is a pivotal decision for any business involved in the production, storage, or distribution of beverages. The right tank can significantly enhance efficiency, safeguard product quality, and optimize operational costs. This comprehensive guide will delve into the diverse factors to consider when choosing a beverage tank, empowering you to make an informed decision that aligns seamlessly with your specific business requirements.
Understanding Beverage Tanks
Beverage tanks, also recognized as liquid storage tanks, are indispensable equipment utilized to store and transport a wide array of beverages, encompassing water and juice to beer and wine. They are available in various sizes, materials, and designs to accommodate diverse volumes and product types.
Types of Beverage Tanks
Beverage tanks can be broadly categorized based on their construction materials and applications.
Stainless Steel Tanks:
Stainless steel reigns supreme as the most prevalent material for beverage tanks due to its exceptional durability, corrosion resistance, and ability to maintain product purity. It is highly versatile and suitable for a wide range of beverages, including beer, wine, and dairy products.
Plastic Tanks:
Plastic tanks offer a lightweight and cost-effective solution, making them ideal for smaller-scale operations or temporary storage. However, they may have limitations in terms of temperature range and chemical compatibility.
Glass-lined Tanks:
Glass-lined tanks provide outstanding corrosion resistance, making them perfect for storing highly acidic or alkaline beverages. They are durable and sanitary, but they can be more expensive than other options.
Factors to Consider When Choosing a Beverage Tank
Several crucial factors must be meticulously considered when selecting the ideal beverage tank for your business:
Capacity:
Accurately determine the required storage capacity based on your production volume and consumption rates. An undersized tank may hinder production capacity, while an oversized tank can lead to increased energy consumption for cooling or heating.
Material:
Choose a material that is compatible with your beverage and adheres to stringent regulatory standards. Consider factors like corrosion resistance, temperature tolerance, and ease of cleaning.
Temperature Control:
If your beverage requires temperature control, ensure the tank is equipped with appropriate heating or cooling systems. This is particularly important for products like beer, wine, and dairy.
Agitation:
For beverages that require mixing or blending, select a tank with suitable agitation systems. Agitation promotes uniform mixing and prevents sedimentation.
Cleaning and Sanitization:
Prioritize a tank that is easy to clean and sanitize to maintain optimal product quality and prevent contamination.
Installation and Maintenance:
Evaluate the available space and accessibility for installation and maintenance. Consider the tank’s weight, dimensions, and the required infrastructure.
Budget:
Assess the initial investment and ongoing operational costs, including energy consumption, cleaning supplies, and maintenance.
The Importance of Proper Sizing
Properly sizing your beverage tank is essential to optimize efficiency and minimize costs. An undersized tank may limit production capacity, while an oversized tank can lead to increased energy consumption and unnecessary space utilization.
Key Features to Look For
- Insulation: Insulation helps maintain the desired temperature and reduces energy consumption, especially for temperature-sensitive beverages.
- Valves and Fittings: High-quality valves and fittings ensure accurate filling, emptying, and sampling, minimizing product loss and contamination.
- Heating and Cooling Systems: For temperature-sensitive beverages, efficient heating and cooling systems are crucial to maintain optimal product quality.
- Agitation Systems: Agitation systems promote uniform mixing, prevent sedimentation, and enhance product consistency.
Comparison of Beverage Tank Materials
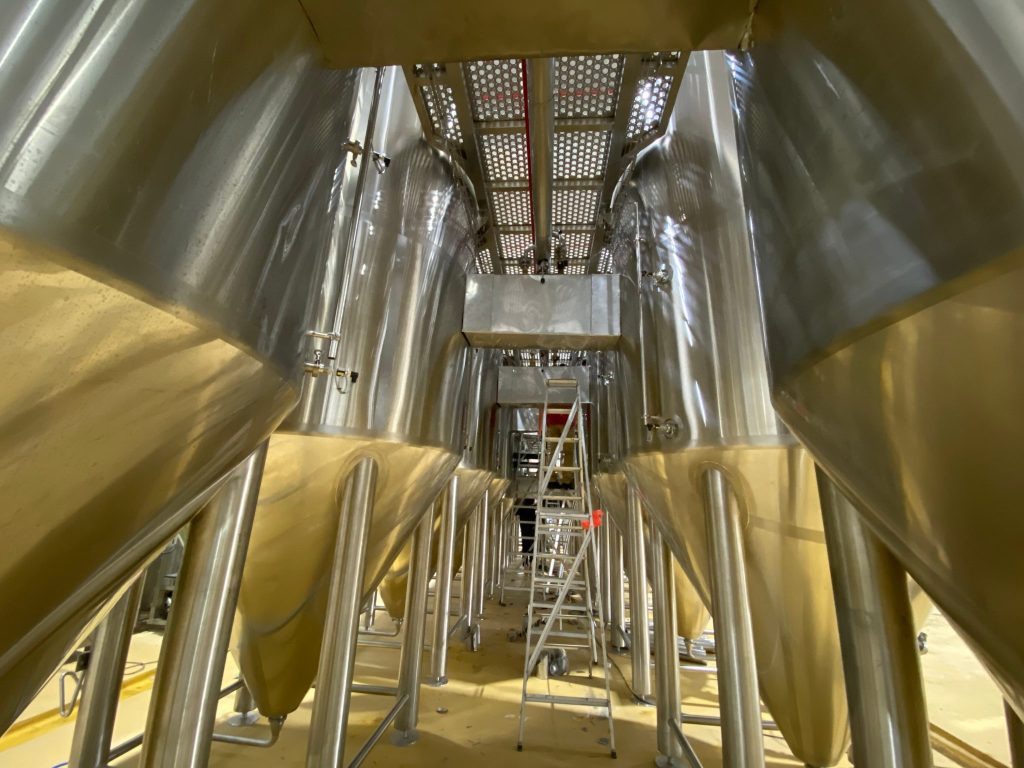
Material | Advantages | Disadvantages | Applications |
---|---|---|---|
Stainless Steel | Durable, corrosion-resistant, sanitary | High cost | Most beverages, including beer, wine, and dairy |
Plastic | Lightweight, cost-effective | Susceptible to chemical damage, limited temperature range | Water, juice, and non-alcoholic beverages |
Glass-lined | Excellent corrosion resistance, sanitary | Fragile, high cost | Highly acidic or alkaline beverages |
Conclusion
Selecting the appropriate beverage tank is a crucial decision that can significantly impact your business operations. By meticulously considering factors such as capacity, material, temperature control, agitation, and budget, you can select a tank that aligns seamlessly with your specific needs and enhances your production efficiency and product quality.
FAQ
What is the optimal material for a beverage tank?
Stainless steel is generally regarded as the best material due to its exceptional durability, corrosion resistance, and sanitary properties.
How can I determine the required capacity of a beverage tank?
Calculate your daily production volume and consider peak demand periods to accurately estimate the necessary storage capacity.
What is the distinction between a storage tank and a process tank?
Storage tanks are primarily utilized for long-term storage, while process tanks are employed for mixing, blending, and other processing activities.
How frequently should I clean and sanitize my beverage tank?
The frequency of cleaning and sanitization depends on the type of beverage, regulatory requirements, and the specific tank material.