Introduction
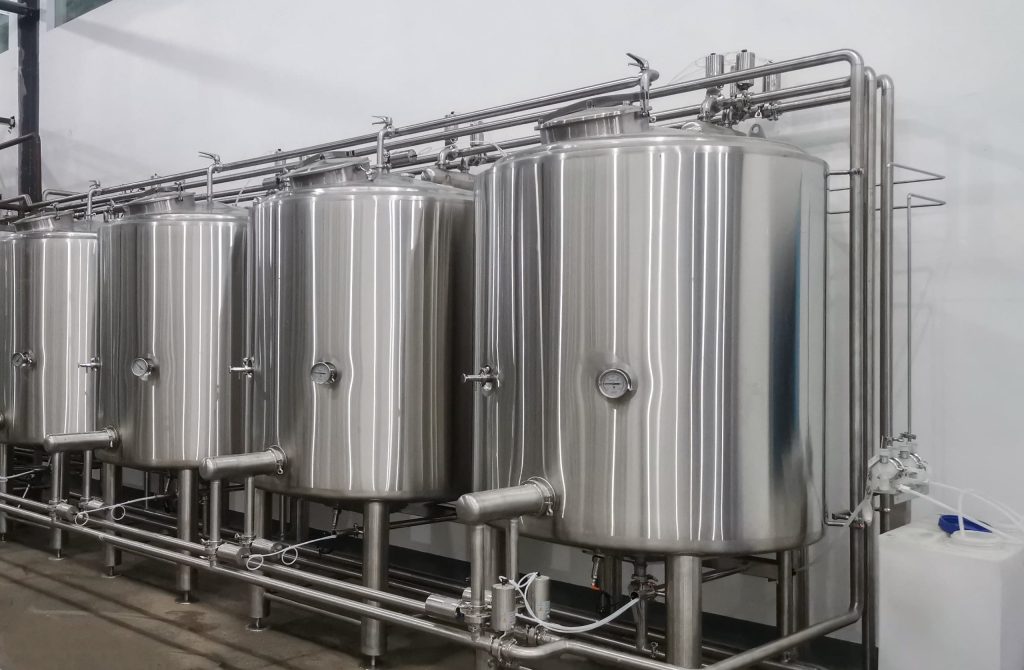
In today’s fast-paced industrial environment, efficiency and hygiene are paramount. The concept of cip clean in place has revolutionized cleaning processes across various sectors, offering significant advantages over traditional cleaning methods. This blog post delves into the intricacies of cip clean in place, exploring its benefits, applications, and the factors to consider when implementing such a system. The implementation of a well-designed cip clean in place system can significantly streamline operations, reduce potential contamination, and ensure consistent product quality.
Understanding the Principles of CIP Clean in Place
cip clean in place is an automated system designed to clean interior surfaces of pipes, tanks, and processing equipment without dismantling them. This process involves circulating cleaning solutions, rinses, and disinfectants through the equipment, ensuring thorough sanitation. The key principles of cip clean in place include:
- Chemical Action: Utilizing appropriate cleaning agents to remove soils and residues. The selection of the right chemical is crucial for effectively breaking down and removing specific types of contaminants.
- Temperature: Maintaining optimal temperatures to enhance cleaning effectiveness. Elevated temperatures can accelerate chemical reactions, improving the removal of stubborn residues.
- Mechanical Action: Generating sufficient flow and turbulence for thorough cleaning. The force of the circulating fluids helps to dislodge and carry away debris.
- Time: Ensuring adequate contact time between the cleaning solutions and the equipment surfaces. Sufficient contact time allows the cleaning agents to fully interact with and remove contaminants.
The Benefits of Implementing a CIP Clean in Place System
Implementing a cip clean in place system offers numerous advantages, including:
- Enhanced Hygiene: cip clean in place minimizes the risk of contamination, ensuring product safety and quality. Automated systems reduce human intervention, which can be a source of contamination.
- Increased Efficiency: Automation reduces cleaning time and labor costs, boosting productivity. This allows for more time dedicated to production rather than cleaning.
- Reduced Downtime: Clean in place systems allow for faster cleaning cycles, minimizing production interruptions. Faster changeovers between product batches allows for increased production output.
- Improved Safety: Automation reduces worker exposure to hazardous chemicals and manual handling risks. This ensures a safer work environment for all employees.
- Water and Chemical Savings: Optimized clean in place processes can reduce water and chemical consumption. Precise control over cleaning solution usage minimizes waste.
- Consistent Cleaning Results: Automated systems ensure consistent and repeatable cleaning outcomes. This guarantees that every cleaning cycle meets the same high standards.
Applications of CIP Clean in Place Across Industries
cip clean in place is widely used across various industries, including:
- Food and Beverage: Ensuring hygiene in processing equipment for dairy, brewing, and food production. This is essential for maintaining product safety and preventing spoilage.
- Pharmaceuticals: Maintaining sterile conditions in drug manufacturing and biotechnology. Strict adherence to cleanliness standards is vital for producing safe and effective medications.
- Cosmetics: Ensuring product purity in the production of personal care products. This prevents contamination that can affect product quality and safety.
- Chemical Processing: Cleaning reactors, tanks, and pipelines in chemical manufacturing. This is critical for preventing cross-contamination and ensuring process integrity.
Key Components of a Clean in Place System
A typical cip clean in place system comprises several key components:
- Tanks: Holding cleaning solutions, rinses, and disinfectants. These tanks must be constructed of materials that are compatible with the cleaning agents used.
- Pumps: Circulating the cleaning solutions through the equipment. The pumps must be capable of delivering the required flow rate and pressure.
- Valves: Controlling the flow of liquids through the system. Automated valves allow for precise control of the cleaning process.
- Sensors: Monitoring temperature, flow, and conductivity. These sensors provide real-time data to ensure the cleaning process is operating within optimal parameters.
- Control System: Automating the cleaning process and ensuring optimal parameters. The control system allows for the programming and monitoring of cleaning cycles.
Factors to Consider When Designing a CIP Clean in Place System
Designing an effective clean in place system requires careful consideration of several factors:
- Equipment Design: Ensuring the equipment is designed for efficient cleaning. Equipment with smooth surfaces and minimal dead spots are easier to clean.
- Cleaning Chemistry: Selecting appropriate cleaning agents for specific soils and residues. The chemical must be compatible with the equipment materials.
- Flow Rate and Pressure: Optimizing flow and pressure for effective cleaning. Sufficient flow and pressure are needed to ensure thorough cleaning.
- Temperature Control: Maintaining optimal temperatures for cleaning effectiveness. Temperature control is crucial for maximizing the effectiveness of the cleaning solutions.
- Automation: Implementing automated controls for consistent and efficient cleaning. Automation reduces human error and ensures repeatable results.
Optimizing Your CIP Clean in Place Process
To maximize the effectiveness of your cip clean in place system, consider the following optimization strategies:
- Regular Maintenance: Ensuring the system is properly maintained and calibrated. Regular maintenance prevents system failures and ensures optimal performance.
- Monitoring and Analysis: Tracking key parameters and analyzing cleaning results. This data can be used to fine-tune the cleaning process.
- Process Optimization: Fine-tuning cleaning cycles and parameters for efficiency. Optimizing the cleaning process can reduce water and chemical consumption.
- Training: Providing adequate training for operators and maintenance personnel. Proper training ensures that the system is operated and maintained correctly.
CIP Clean in Place System Components Table
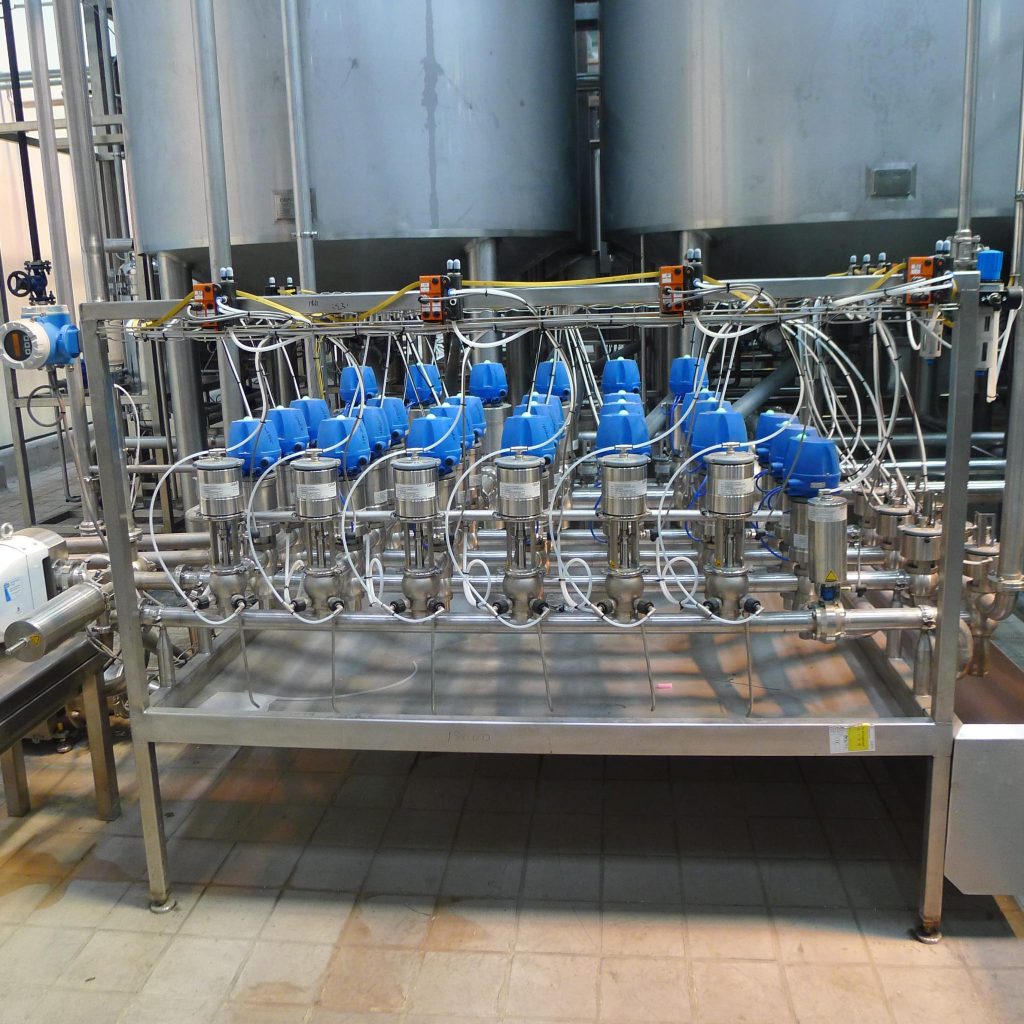
Component | Function | Key Considerations |
---|---|---|
Tanks | Storage of cleaning solutions | Material compatibility, capacity, insulation |
Pumps | Circulation of fluids | Flow rate, pressure, material compatibility |
Valves | Control of fluid flow | Valve type, automation, material compatibility |
Sensors | Monitoring of process parameters | Accuracy, reliability, sensor type |
Control System | Automation of cleaning process | Programmability, integration, data logging |
Conclusion
cip clean in place is an indispensable technology for industries requiring high levels of hygiene and efficiency. By automating cleaning processes, businesses can achieve consistent results, reduce operational costs, and enhance product quality. Understanding the key principles, benefits, and applications of cip clean in place is crucial for optimizing cleaning processes and ensuring a competitive edge. The adoption of well implemented cip clean in place systems leads to better overall operational efficiency and a decrease in risks related to contamination.
To experience the benefits of a optimized cip clean in place systems, and to elevate your industrial cleaning standards, contact us today. Let our experts assist you in designing and implementing a system that meets your specific needs.
FAQ
What is the difference between cip clean in place and manual cleaning?
cip clean in place is an automated system, while manual cleaning involves disassembling equipment and cleaning it by hand. cip clean in place offers greater efficiency, consistency, and hygiene, reducing the potential for human error and contamination. Manual cleaning, on the other hand, is labor-intensive and can lead to inconsistent results.
What are the key benefits of cip clean in place?
Key benefits include enhanced hygiene, increased efficiency, reduced downtime, improved safety, and water and chemical savings. These benefits translate to lower operational costs and improved product quality. The consistency of cip clean in place ensures that all cleaning cycles adhere to the same high standards.
What industries use cip clean in place?
cip clean in place is used in food and beverage, pharmaceuticals, cosmetics, and chemical processing industries. These industries require high levels of hygiene and cleanliness to ensure product safety and quality. The systems are designed to meet the specific cleaning needs of each industry.