Introduction
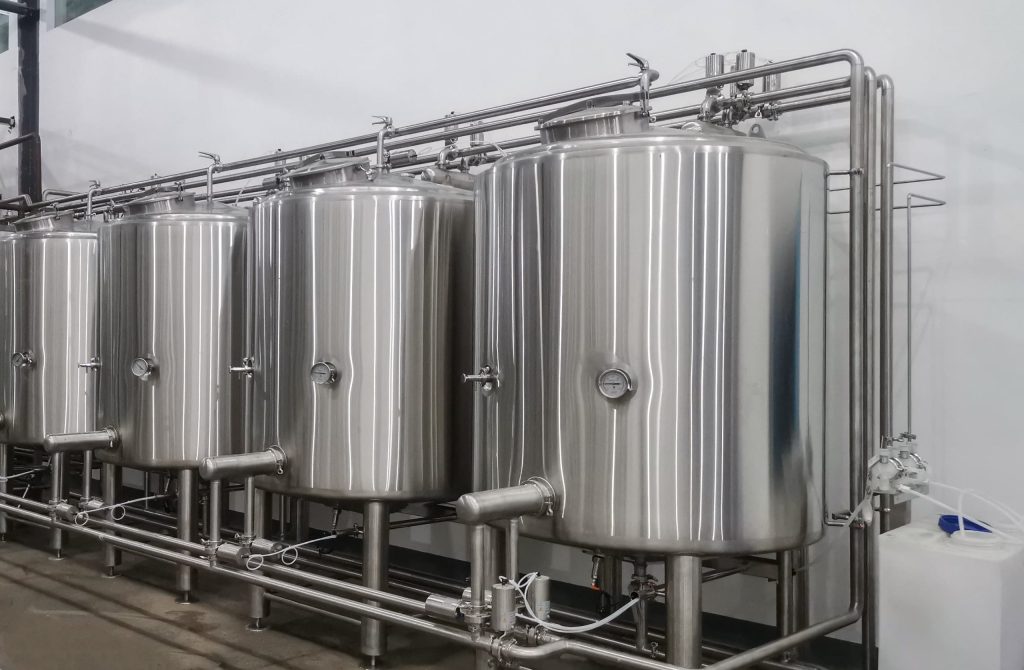
Clean in place cleaning (CIP) is a method of cleaning interior surfaces of pipes, vessels, process equipment, filters and associated fittings, without disassembly. It involves the use of turbulence and flow of cleaning solutions, heat and chemical action to remove product residues, bioburden and other contaminants. Clean in place cleaning is widely used in industries with high hygiene standards, such as food and beverage, pharmaceutical, and biotechnology. This guide provides a comprehensive overview of the key equipment used in clean in place cleaning systems, their functions, and considerations for selection.
Key Components of a Clean In Place Cleaning System
A typical clean in place cleaning system comprises several key components that work together to achieve effective cleaning. These components include:
- Tanks: These tanks store the cleaning solutions, such as detergents, acids, and sanitizers.
- Pumps: Pumps are used to circulate the cleaning solutions through the system at the required flow rates and pressures.
- Valves: Valves control the flow of cleaning solutions, directing them to the appropriate parts of the system.
- Heat Exchangers: Heat exchangers are used to heat the cleaning solutions to the optimal temperature for effective cleaning.
- Sensors: Sensors monitor various parameters, such as temperature, pressure, and conductivity, to ensure that the cleaning process is carried out correctly.
- Control Systems: Control systems automate the CIP process, ensuring consistent and repeatable cleaning results.
- Spray Devices: Spray devices are used to distribute the cleaning solutions evenly over the surfaces to be cleaned.
- Piping: Piping is used to transport the cleaning solutions throughout the system.
Clean In Place Cleaning Tanks: Storage and Preparation
Clean in place cleaning tanks are essential for storing and preparing the cleaning solutions. These tanks are typically made of stainless steel to ensure compatibility with the cleaning chemicals and to prevent contamination. The size and design of the tanks will depend on the specific CIP application. Considerations for clean in place cleaning tank selection include:
- Tank capacity: The tank capacity should be sufficient to hold the required volume of cleaning solution.
- Tank material: Stainless steel is the preferred material for CIP tanks.
- Tank design: The tank design should facilitate thorough cleaning and drainage.
- Agitation: Many tanks will have agitation systems to help mix the cleaning solutions.
Clean In Place Cleaning Pumps: Circulation and Pressure
Clean in place cleaning pumps are responsible for circulating the cleaning solutions through the system at the required flow rates and pressures. Centrifugal pumps are commonly used in CIP applications due to their ability to handle high flow rates and low viscosities. Considerations for clean in place cleaning pump selection include:
- Flow rate: The pump flow rate should be sufficient to ensure adequate turbulence and cleaning effectiveness.
- Pressure: The pump pressure should be sufficient to overcome the system’s resistance and deliver the cleaning solutions to all parts of the system.
- Pump material: The pump material should be compatible with the cleaning chemicals.
- Pump type: Centrifugal pumps are often preferred.
Clean In Place Cleaning Valves: Flow Control and Direction
Clean in place cleaning valves play a crucial role in controlling the flow of cleaning solutions and directing them to the appropriate parts of the system. Valves can be manually operated or automated, depending on the complexity of the CIP process. Considerations for CIP valve selection include:
- Valve type: The valve type should be suitable for the specific CIP application.
- Valve material: The valve material should be compatible with the cleaning chemicals.
- Valve actuation: The valve actuation should be appropriate for the level of automation required.
Clean In Place Cleaning Heat Exchangers: Temperature Control
Clean in place cleaning heat exchangers are used to heat the cleaning solutions to the optimal temperature for effective cleaning. Heat exchangers can be plate heat exchangers or shell and tube heat exchangers. Considerations for CIP heat exchanger selection include:
- Heat transfer capacity: The heat exchanger should be able to heat the cleaning solutions to the required temperature.
- Heat exchanger material: The heat exchanger material should be compatible with the cleaning chemicals.
- Heat Exchanger type: Plate or shell and tube.
Clean In Place Cleaning Sensors: Monitoring and Control
Clean in place cleaning sensors monitor various parameters, such as temperature, pressure, and conductivity, to ensure that the cleaning process is carried out correctly. Sensors provide valuable data that can be used to optimize the CIP process and ensure consistent and repeatable cleaning results. Considerations for CIP sensor selection include:
- Sensor type: The sensor type should be appropriate for the parameter being measured.
- Sensor accuracy: The sensor accuracy should be sufficient for the CIP application.
- Sensor material: The sensor material should be compatible with the cleaning chemicals.
Clean In Place Cleaning Control Systems: Automation and Optimization
Clean in place cleaning control systems automate the CIP process, ensuring consistent and repeatable cleaning results. Control systems can be simple programmable logic controllers (PLCs) or more complex distributed control systems (DCSs). Considerations for CIP control system selection include:
- Control system complexity: The control system complexity should be appropriate for the clean in place cleaning application.
- Control system features: The control system features should meet the specific requirements of the CIP process.
- Control system reliability: The control system should be reliable and provide consistent performance.
Clean In Place Cleaning Spray Devices: Distribution and Coverage
Clean in place cleaning spray devices are used to distribute the cleaning solutions evenly over the surfaces to be cleaned. Spray devices can be static spray balls or rotary spray heads. Considerations for clean in place cleaning spray device selection include:
- Spray pattern: The spray pattern should provide adequate coverage of the surfaces to be cleaned.
- Spray device material: The spray device material should be compatible with the cleaning chemicals.
- Spray device design: The spray device design should facilitate thorough cleaning.
Clean In Place Cleaning Piping: Transport and Flow
Clean in place cleaning piping is used to transport the cleaning solutions throughout the system. The piping material should be compatible with the cleaning chemicals and the operating temperatures and pressures. Considerations for CIP piping selection include:
- Piping material: The piping material should be compatible with the cleaning chemicals.
- Piping size: The piping size should be sufficient to handle the required flow rates.
- Piping design: The piping design should minimize dead legs and ensure thorough drainage.
Clean in Place Cleaning Equipment Table Example
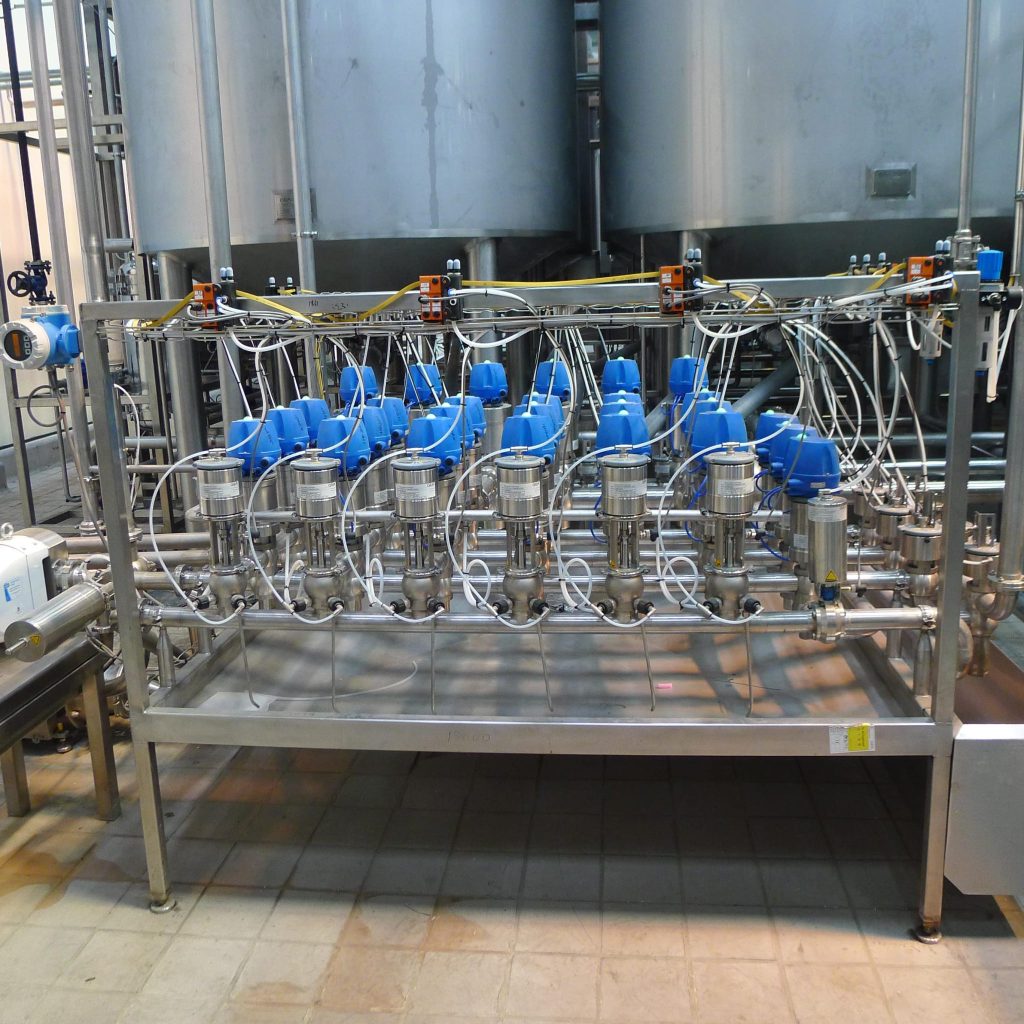
Equipment Type | Function | Material Considerations | Key Features |
---|---|---|---|
Storage Tank | Storing cleaning solutions | Stainless Steel | Agitation, drainage design |
Centrifugal Pump | Circulating cleaning solutions | Stainless Steel, chemical compatibility | Flow rate, pressure rating |
Automated Valve | Controlling solution flow | Stainless Steel, chemical compatibility | Actuation type, flow precision |
Plate Heat Exchanger | Heating cleaning solutions | Stainless Steel, titanium | Heat transfer rate, temperature control |
Conductivity Sensor | Monitoring solution concentration | Stainless Steel, PTFE | Accuracy, chemical resistance |
PLC Control System | Automating cleaning cycles | Industrial grade components | Programming flexibility, data logging |
Rotary Spray Head | Distributing cleaning solutions | Stainless Steel, PTFE | Spray pattern, rotation speed |
Stainless Steel Pipe | Transporting cleaning solutions | Stainless Steel | Diameter, pressure rating, smooth interior |
Conclusion
Clean in place cleaning is an essential process for industries that require high hygiene standards. Selecting the right clean in place cleaning equipment is crucial for ensuring effective cleaning and optimizing the CIP process. When considering your next purchase of clean in place cleaning equipment, contact us today, so we can help you find the best solution for your business.
FAQ
Q: Why is CIP preferred over manual cleaning in many industries?
A: CIP minimizes downtime by eliminating the need for equipment disassembly. It also enhances hygiene by reducing human contact with the process, leading to more consistent and reliable cleaning results. Furthermore, it often reduces water and chemical usage compared to manual methods.
Q: What types of cleaning solutions are typically used in clean in place cleaning systems?
A: Common cleaning solutions include alkaline detergents for removing organic residues, acidic detergents for mineral deposits, and sanitizers for eliminating microorganisms. The specific solutions are chosen based on the type of soil to be removed and the materials of the equipment being cleaned.
Q: How does the flow rate of cleaning solutions affect the effectiveness of CIP?
A: Adequate flow rate is crucial for creating turbulence, which is essential for dislodging residues from equipment surfaces. Insufficient flow can lead to ineffective cleaning, while excessive flow may cause damage or excessive wear.
Q: What role do sensors play in clean in place cleaning systems?
A: Sensors monitor critical parameters such as temperature, pressure, conductivity, and flow rate. This data helps ensure that the cleaning process is operating within optimal parameters and provides valuable feedback for process control and optimization.