Introduction
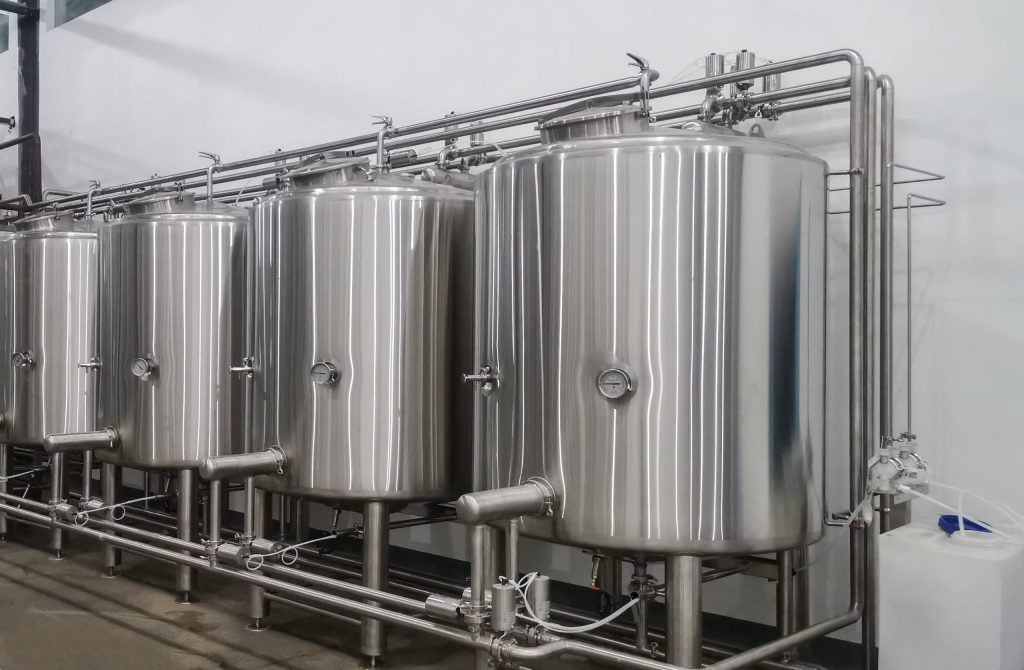
The clean in place process, commonly known as CIP, is a vital automated cleaning method used in industries where hygiene and cleanliness are paramount. This process aims to clean interior surfaces of pipes, vessels, process equipment, filters, and associated fittings without disassembly. By circulating cleaning solutions through the equipment, the clean in place process removes product residues, contaminants, and microorganisms, ensuring a safe and efficient production environment.
In today’s fast-paced manufacturing and processing environments, efficiency and hygiene go hand in hand. The clean in place process offers a streamlined approach to maintaining cleanliness, reducing downtime, and ensuring consistent product quality. This blog post explores the various facets of the clean in place process, its benefits, key components, optimization strategies, and frequently asked questions.
Understanding the Core Components of the Clean in Place Process
The effectiveness of the clean in place process hinges on several key components working in harmony. These components ensure thorough cleaning and contribute to the overall efficiency of the system.
Cleaning Solutions: The Heart of the Clean in Place Process
The selection of appropriate cleaning solutions is crucial. These solutions are typically tailored to the specific type of soil or residue being removed. Common solutions include:
- Caustic Solutions: Effective for removing organic soils and fats.
- Acid Solutions: Used to remove mineral deposits and scale.
- Detergents: Help to emulsify and lift soils from surfaces.
- Sanitizers/Disinfectants: Eliminate microorganisms and ensure hygienic conditions.
Circulation Systems: Ensuring Complete Coverage
The circulation system is responsible for delivering the cleaning solutions throughout the equipment. It comprises pumps, valves, and piping that ensure consistent flow and pressure. Optimizing the flow rate and pressure is essential for effective cleaning.
Temperature Control: Enhancing Cleaning Efficiency
Temperature plays a significant role in the effectiveness of the clean in place. Elevated temperatures can accelerate chemical reactions, enhance soil removal, and improve sanitation. Temperature control systems, such as heat exchangers, are used to maintain the optimal temperature during the cleaning cycle.
Monitoring and Control Systems: Maintaining Process Integrity
Modern clean in place systems are equipped with sophisticated monitoring and control systems. These systems track key parameters such as temperature, flow rate, conductivity, and pH, providing real-time data and ensuring process consistency.
Optimizing the Clean in Place Process for Maximum Efficiency
To maximize the benefits of the clean in place process, it’s essential to implement optimization strategies that enhance efficiency and effectiveness.
Flow Rate and Pressure Optimization in the Clean in Place
Optimizing the flow rate and pressure of the cleaning solutions is critical for effective cleaning. Insufficient flow can result in inadequate soil removal, while excessive flow can lead to energy waste and potential damage to equipment. The optimal flow rate ensures turbulent flow, which provides the necessary mechanical action to lift soils from surfaces.
Temperature Management in the Clean in Place
Maintaining the correct temperature during the cleaning cycle is crucial. Elevated temperatures can enhance the effectiveness of cleaning solutions, but excessively high temperatures can damage equipment and increase energy consumption. Careful temperature management ensures optimal cleaning performance while minimizing energy costs.
Chemical Concentration and Contact Time in the Clean in Place Process
The concentration of cleaning solutions and the contact time with the equipment surfaces are vital factors in the clean in place process. Ensuring the right balance between concentration and contact time ensures effective soil removal and sanitation without wasting chemicals or prolonging the cleaning cycle.
Validation and Verification of the Clean in Place Process
Regular validation and verification of the clean in place process are essential to ensure consistent cleaning performance. This includes monitoring key parameters, conducting microbiological testing, and performing visual inspections. Documenting these activities provides a record of compliance and helps to identify areas for improvement.
Benefits of Implementing the Clean in Place Process
Implementing the clean in place process offers numerous benefits, contributing to improved efficiency, hygiene, and overall operational performance.
Enhanced Hygiene and Product Safety
The clean in place process ensures thorough cleaning and sanitation, minimizing the risk of contamination and ensuring product safety. This is particularly crucial in industries such as food and beverage, pharmaceuticals, and cosmetics, where product quality and safety are paramount.
Reduced Downtime and Increased Productivity
Automating the cleaning process reduces downtime associated with manual cleaning methods. This allows for faster turnaround times between production cycles, increasing overall productivity.
Cost Savings and Resource Efficiency
The clean in place process optimizes the use of cleaning solutions, water, and energy, resulting in cost savings and resource efficiency. Automated systems also reduce labor costs associated with manual cleaning.
Consistent and Repeatable Cleaning Results
Automated systems provide consistent and repeatable cleaning results, minimizing variability and ensuring consistent product quality. This is particularly important in industries where regulatory compliance and product consistency are critical.
Key Considerations for the Clean in Place Process
When implementing the clean in place process, several key considerations must be addressed to ensure optimal performance and efficiency.
Equipment Design and Compatibility
The design of the equipment and its compatibility with the clean in place process are crucial. Equipment should be designed to facilitate effective cleaning, with smooth surfaces, minimal dead spots, and adequate drainage.
Chemical Compatibility and Material Selection
The selection of cleaning solutions and materials must be carefully considered to ensure compatibility. Incompatible materials can lead to corrosion, degradation, and contamination.
Environmental Impact and Sustainability
The environmental impact of the clean in place process should be considered. Minimizing water and chemical consumption, as well as optimizing energy usage, contributes to sustainability.
Clean in Place Process Implementation Table
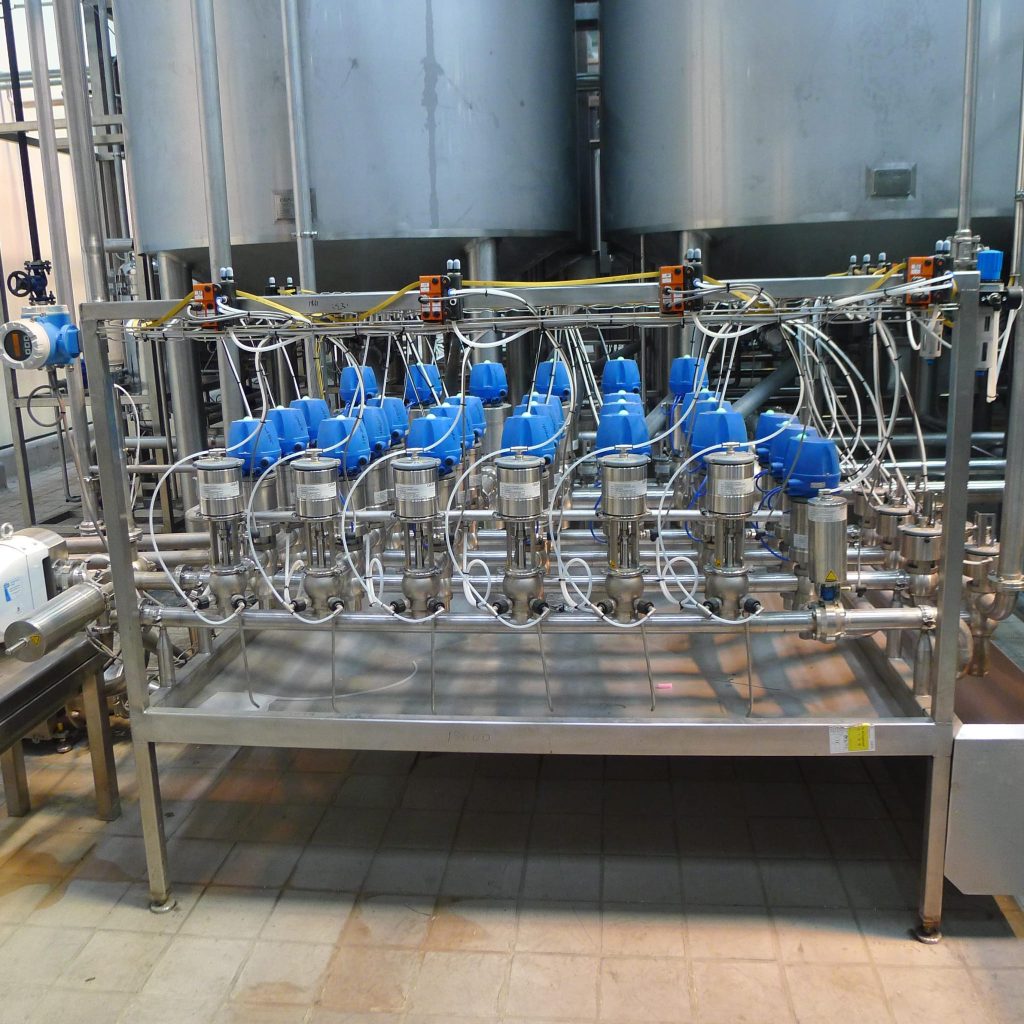
Parameter | Description | Importance |
---|---|---|
Temperature | Maintain optimal cleaning solution temperature. | Enhances chemical reaction and soil removal. |
Flow Rate | Ensure turbulent flow for mechanical cleaning. | Lifts soils and contaminants from surfaces. |
Chemical Concentration | Use appropriate chemical concentration. | Effective soil removal and sanitation. |
Contact Time | Ensure sufficient contact time for cleaning solutions. | Allows for thorough cleaning and sanitation. |
Monitoring | Track key parameters like pH and conductivity. | Maintains process integrity and consistency. |
Validation | Conduct regular validation and verification. | Ensures consistent cleaning performance. |
Drainage | Ensure complete drainage of cleaning solutions. | Prevents contamination and residue buildup. |
Conclusion
The clean in place process is an indispensable tool for maintaining hygiene and efficiency in various industries. By understanding the key components, optimizing the process, and implementing best practices, businesses can ensure consistent product quality, reduce downtime, and achieve cost savings. As technology advances, the clean in place process will continue to evolve, offering even greater efficiency and sustainability.
FAQ
What is the primary purpose of the clean in place process?
The primary purpose of the clean in place process is to clean the interior surfaces of process equipment without disassembly, ensuring hygiene and product safety.
How does temperature affect the clean in place process?
Temperature affects the rate of chemical reactions and soil removal. Elevated temperatures generally enhance the effectiveness of cleaning solutions.
What are the key components of a clean in place system?
Key components include cleaning solutions, circulation systems, temperature control systems, and monitoring and control systems.
How often should the clean in place process be validated?
The frequency of validation depends on industry regulations and specific requirements. Regular validation ensures consistent cleaning performance.