Distillation tower is the silent workhorse in every spirit, petrochemical, and fine‐food process—yet most people don’t realize it until they taste the final product. What if I told you that the height, plate count, and feed point of your distillation column can mean the difference between a bland spirit and an award‐winning one? Whether you spotted SKE Equipment’s demo at Fine Food Australia or you’re mapping out your first pilot plant, this deep dive will unravel:
What Is a Distillation Tower?
How Does a Distillation Tower Work?
Types of Distillation Towers
Typical Distillation Tower Process Flow
Factors Driving Distillation Tower Cost
Grab a cup of coffee (or a dram!), and let’s ascend to purity—plate by plate.
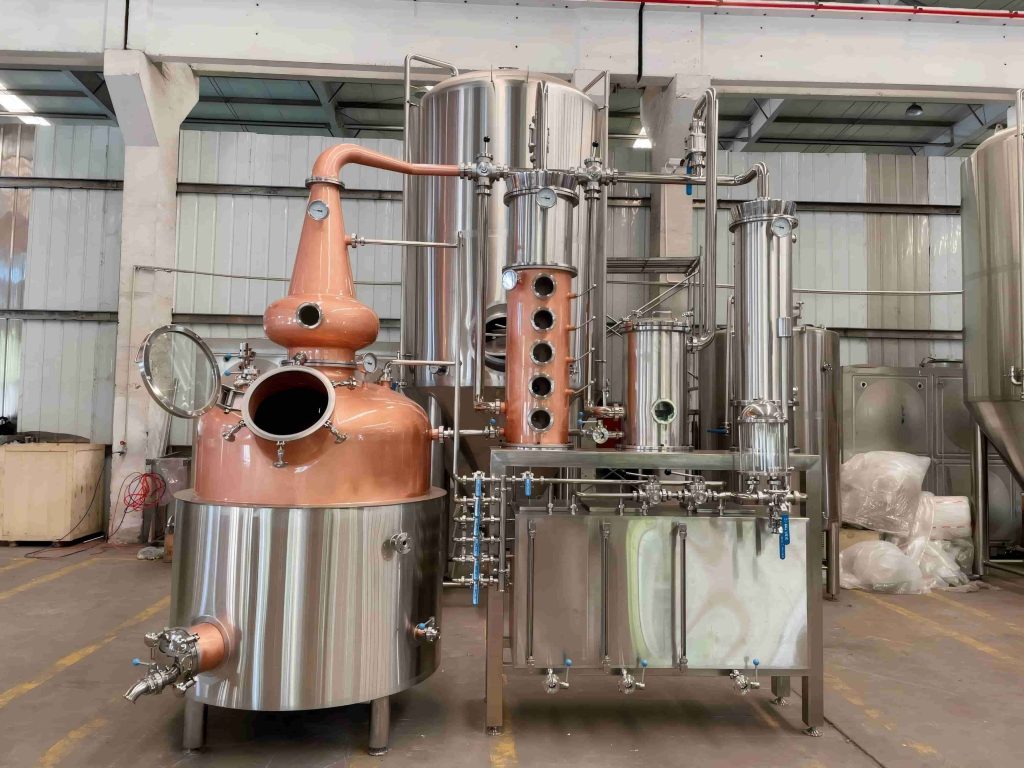
1. What Is a Distillation Tower?
A distillation tower (aka distillation column) is a vertical vessel filled with trays or packing that separates liquid mixtures based on boiling points. The feed enters at one point; as vapors rise and liquids descend, repeated vaporization and condensation across plates create high‐purity fractions.
Key terms:
Plate/Tray: Horizontal stages where vapor/liquid contact occurs.
Packing: Structured or random material that provides surface area for contact in packed columns.
Reflux: Liquid returned from condenser to improve separation.
Reboiler: Bottom heat source that drives vapor up the column.
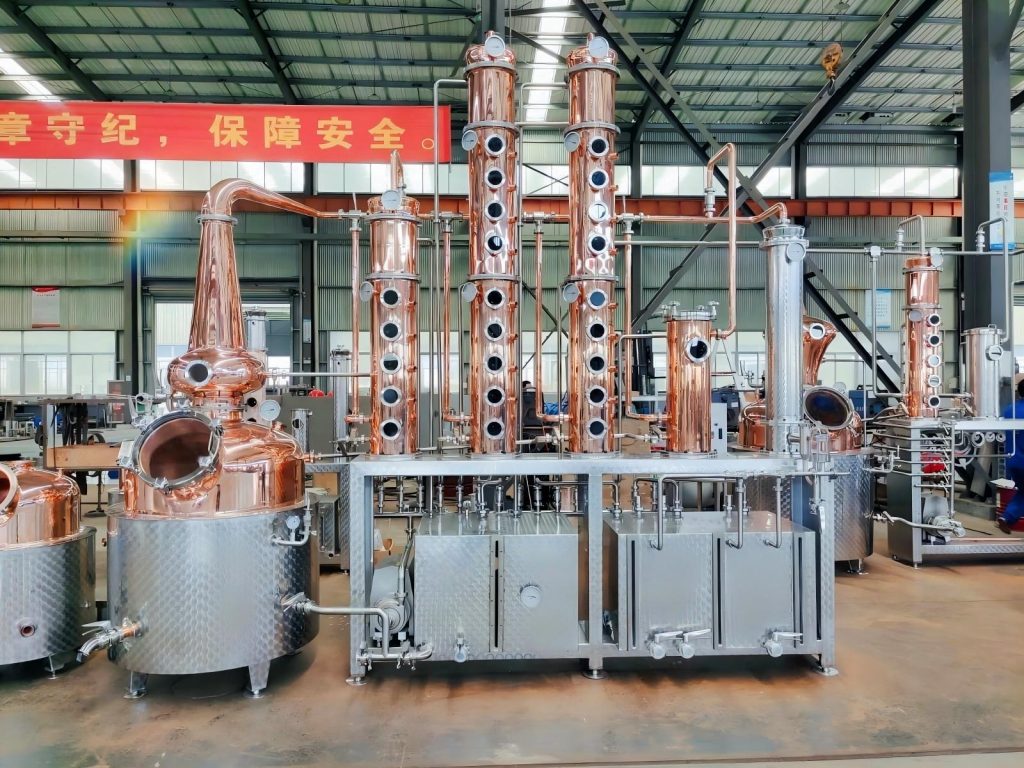
2. How Does a Distillation Tower Work?
At its core, a distillation tower relies on thermodynamics and mass transfer:
Heating: The reboiler boils the bottom liquid mixture.
Vapor Ascent: Lighter components vaporize and ascend.
Plate Contact: Vapor condenses on trays, exchanging heat with descending liquid.
Reflux Control: Condenser at the top cools a portion of vapor back to liquid, which returns down the column, sharpening separation.
Draw-Off: Purified distillate is collected at the top, while heavier bottoms leave via the reboiler return.
SKE Equipment’s distillation towers feature precise tray designs and advanced reflux control for maximized efficiency.
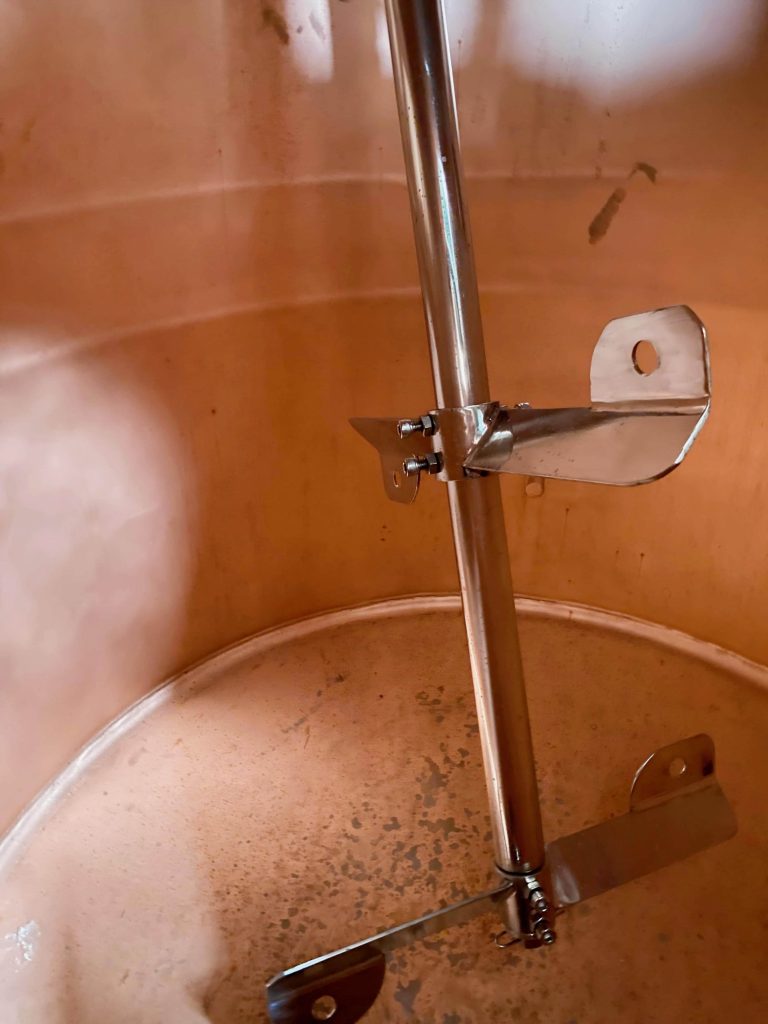
3. Types of Distillation Towers
Different applications demand different column architectures:
Column Type | Characteristics | Ideal For |
---|---|---|
Tray Columns | Series of perforated trays | Fine chemical separations |
Packed Columns | Structured/random packing | Low‐pressure drop; gentle fluids |
Dividing Wall | Internal wall divides feed into two sections | Multi‐product streams |
Vacuum Columns | Operate below atmospheric pressure | Heat‐sensitive components |
Hybrid Columns | Combines trays and packing | Broad feed variability |
At Fine Food Australia, SKE Equipment showcased their modular packed columns—perfect for aroma‐sensitive botanical distillates.
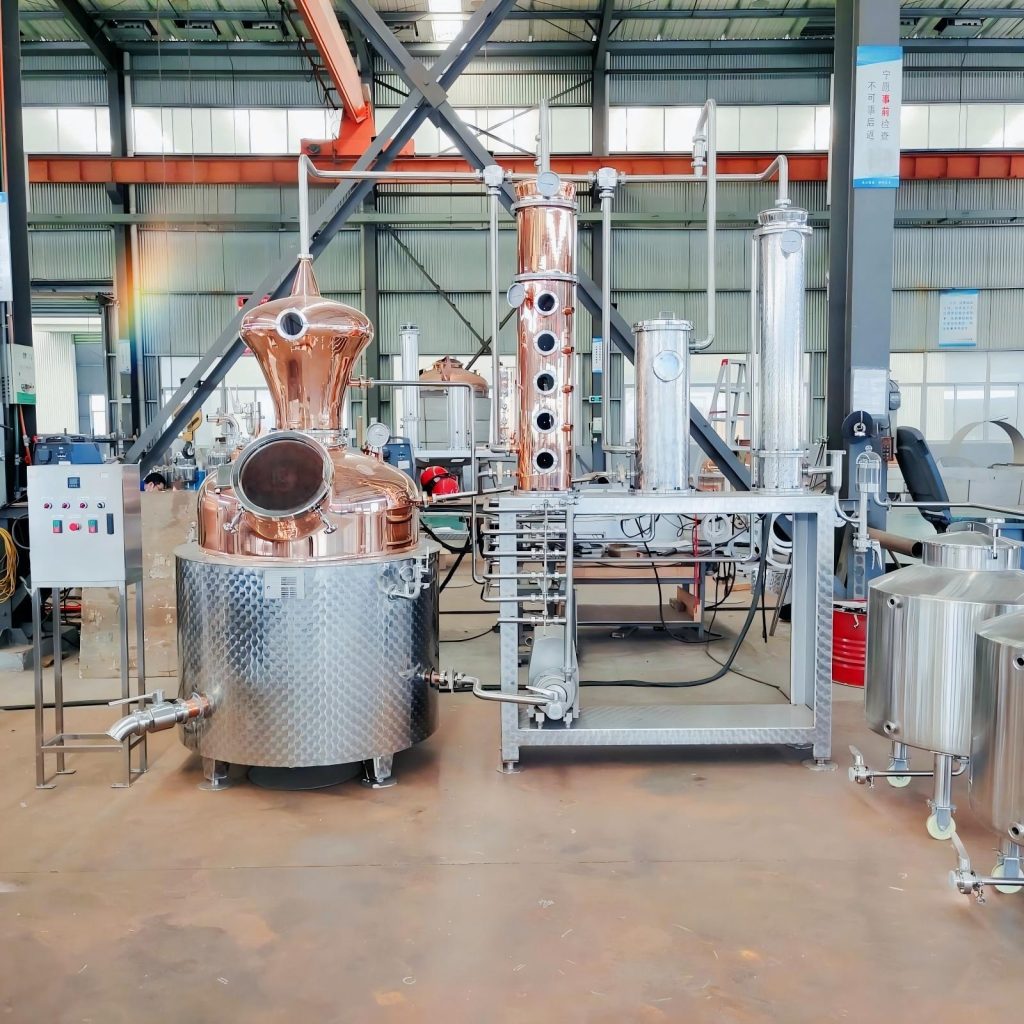
4. Typical Distillation Tower Process Flow
A standard process includes:
Pre‐Heating: Feed warmed via exchangers.
Feed Entry: Introduced at optimal tray/pack height.
Fractionation: Vapor/liquid interaction through stages.
Overhead Condenser & Reflux Drum: Controls reflux ratio.
Side Draws: Intermediate products removed.
Bottoms Product Removal.
Step | Equipment | Control Parameter |
---|---|---|
Pre‐Heat | Heat Exchanger | Inlet temp |
Feed Introduction | Feed Tray/Pump | Flow rate |
Fractionation | Column Trays/Packing | Reflux ratio, plate count |
Overhead Condense | Condenser | Cooling water flow |
Bottoms Removal | Reboiler/Bottoms Pump | Reboiler duty |
5. Factors Driving Distillation Tower Cost
Several variables influence pricing:
Height & Diameter: Larger columns cost more steel and internal hardware.
Number of Trays or Packing Height: More stages increase material and labor.
Material of Construction: Stainless vs. exotic alloys.
Automation & Controls: Advanced DCS integration vs. manual control.
CIP & Sanitation Features: Required in food applications.
SKE Equipment’s flexible skids allow breweries and kitchens to start small—adding trays or packing modules over time to spread capital costs.
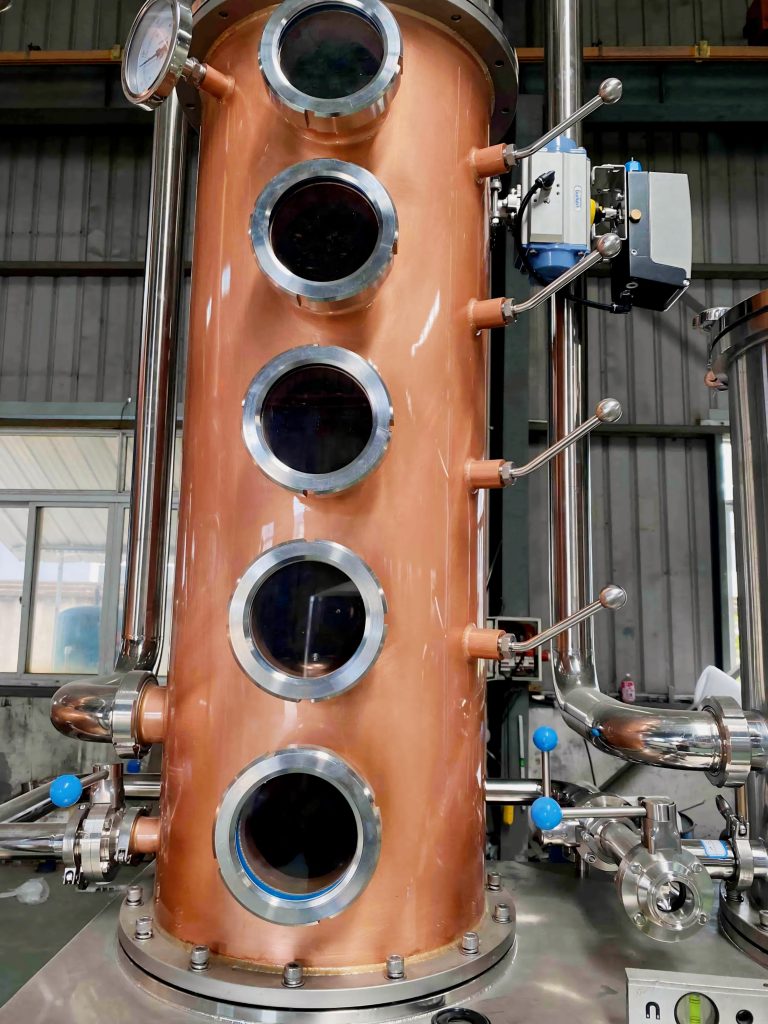
Ready to elevate your separation processes and unlock unparalleled purity? Partner with SKE Equipment—featured at Fine Food Australia—for modular distillation towers tailored to your application. Whether you need packed columns for delicate botanicals or tray towers for high-throughput operations, our experts will guide you from design to startup.
👉 Request Your Custom Tower Consultation: Contact SKE Equipment
📘 Download Our Distillation Tower Design Guide: Grab Your Free Copy
Harness the power of precision separation—let’s distill excellence together! 🚀