Table of Contents
If you’ve ever savored a smooth whiskey or a delicate gin, you’ve tasted the results of precision distillery equipment commercial systems operating behind the scenes. Scaling from craft batches to full production requires specialized vessels, controls, and cleaning, all engineered to exacting standards. Today, we’ll uncover the anatomy of a modern commercial distillery, highlight SKE’s cutting-edge solutions, and give you the insights to select equipment that delivers consistency, efficiency, and compliance.
1. Why Commercial-Grade Distillery Equipment Matters
In a small pot still, a master distiller can coax nuanced flavors—but when you’re running multiple runs per day, you need reliable distillery equipment commercial systems that offer:
High Throughput: Process hundreds of liters per batch without bottlenecks.
Precision Control: PID temperature regulation and automated reflux adjustment ensure consistent hearts cuts.
Regulatory Compliance: Pressure-rated kettles and certified piping meet local safety codes.
Without properly engineered commercial gear, distilleries risk off-flavors, yield loss, and non-compliance. Investing in industrial-grade systems by brands like SKE safeguards both quality and reputation.
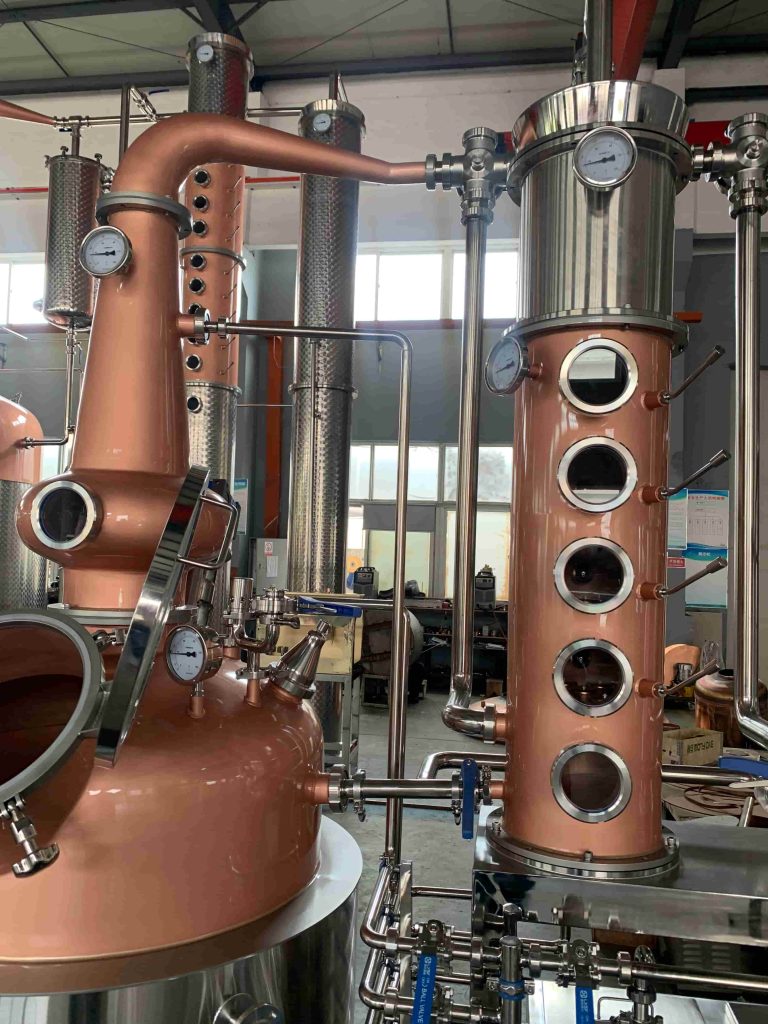
2. Core Components of a Commercial Distillery Setup
A robust distillery equipment commercial lineup integrates:
Component | Role | SKE Feature |
---|---|---|
Mash Tun | Converts grain starches to fermentable wort | Dual-jacket temperature control (±0.5 °C) |
Fermentation Tanks | Bulk fermentation with CO₂ recovery | Pressure relief and sampling ports |
Pot Still / Column | Separates alcohol fractions by vapor condensation | Modular plates, copper heads for sulfur removal |
Condenser / Reflux | Cools and condenses vapor into distillate | Shell-and-tube or coil options |
Control Panel (PLC/HMI) | Automates heating ramps, reflux ratio, and cut timing | Recipe library and remote monitoring |
CIP System | Clean-in-place for kettles and piping | 360° spray nozzles, automated dosing |
Together, these elements form a cohesive workflow—from mashing to final spirits—minimizing manual intervention and maximizing output.
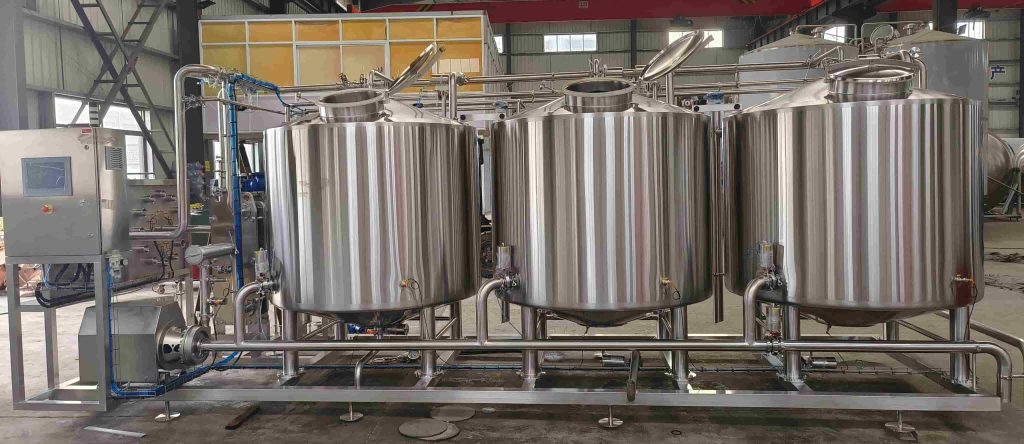
3. SKE’s Innovations in Commercial Distillery Equipment
SKE stands out in the distillery equipment commercial arena by delivering:
Adaptive Reflux Control: Inline sensors adjust reflux ratios in real time, optimizing spirit purity without manual tweaks.
Energy Recovery: Heat exchangers reclaim boiler steam to preheat mash water, cutting energy costs by up to 25 %.
Modular Expansion: Add extra column segments or fermenters without replacing core skids, allowing easy capacity scaling.
Smart Maintenance Alerts: PLC-driven diagnostics flag wear on gaskets and pumps before failures occur.
These innovations help distilleries maintain consistent product quality, reduce downtime, and control operating expenses.
4. Comparing Key Features & Specifications
Specification | Standard Commercial Kit | SKE Premium System |
---|---|---|
Batch Capacity (L) | 200 – 1 000 | 500 – 5 000 |
Temperature Control Accuracy | ±1 °C | ±0.5 °C |
Reflux Ratio Range | Fixed 10:1 | 1:1 – 20:1, programmable |
CIP Cycle Time | 1–2 hours | 30–45 minutes |
Energy Recovery Efficiency | 50 % | 75 % |
Installation Lead Time | 8–12 weeks | 4–6 weeks |
As the table shows, SKE’s distillery equipment commercial offerings deliver tighter control, faster cleaning, and quicker deployment.
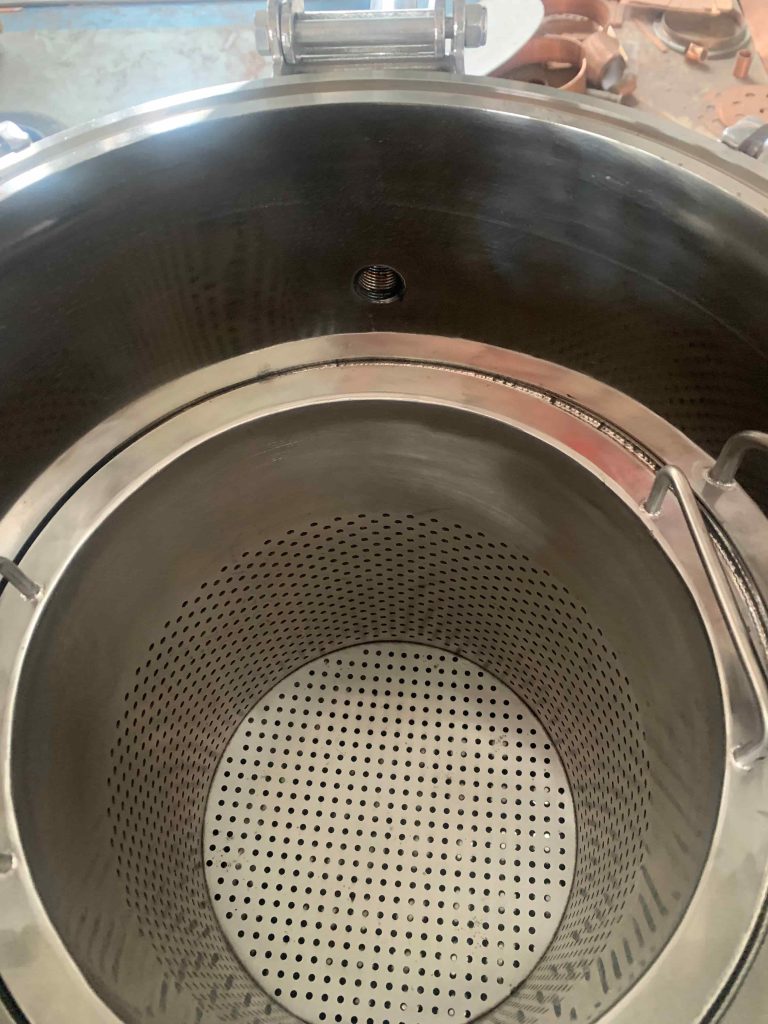
5. How to Choose the Right Distillery Equipment Commercially
When evaluating distillery equipment commercial options, consider:
Production Volume & Growth Plans: Match current needs but allow room for expansion.
Automation vs. Manual: Decide how much process control you want versus manual craft techniques.
Compliance Requirements: Ensure ASME, CE, or local certifications for pressure vessels.
Cleaning & Maintenance: Look for integrated CIP and remote diagnostics to minimize downtime.
Support & Training: Partner with manufacturers like SKE offering installation, spare parts, and operator training.
A well-matched system pays for itself through improved yields, lower labor costs, and consistent product quality.
6. Conclusion & Next Steps
A modern distillery equipment commercial setup is the foundation of scalable, consistent spirit production. By choosing SKE’s precision-engineered systems—complete with adaptive controls, energy recovery, and rapid CIP—you ensure every run meets your exacting standards.
Ready to elevate your distillery? Comment below with your biggest production challenge or contact SKE for a personalized equipment consultation. Your next great batch is just one upgrade away! 🚀🥃
Ready to take your distillery to the next level? Whether you’re targeting 500 L pilot runs or 5 000 L commercial batches, SKE’s cutting-edge distillery equipment commercial solutions deliver the control, efficiency, and reliability you need.
👉 Which upgrade will transform your operation—adaptive reflux control, integrated CIP, or energy-saving heat recovery? Drop a comment below or message us for a free, no-obligation consultation. Let’s design your perfect distillery system together! 🥃🚀
Distiller FAQs You’re Wondering About
Q1: How do I choose between a pot still and a column still?
A1: Pot stills retain more flavor congeners—ideal for whiskey—while column stills offer higher ABV and neutrality suited for vodka. SKE offers hybrid options, letting you adjust plates for either style.
Q2: What’s the real ROI on installing CIP?
A2: Most distilleries recoup their CIP investment in 6–12 months through labor savings, reduced water/chemical use, and faster batch turnover.
Q3: Can I retrofit existing kettles with SKE’s adaptive reflux control?
A3: Yes—our modular reflux packages bolt on to most standard stills, adding real-time ratio adjustment without replacing your entire system.
Q4: How much energy could I save with heat recovery?
A4: SKE’s vapor condensers and heat exchangers can cut your mash-water heating costs by up to 25%, depending on throughput and boiler efficiency.
Q5: What support comes with a SKE distillery package?
A5: Every system includes remote commissioning, on-site training, and a global spare-parts network—ensuring you’re never more than a call away from expert assistance.