Introduction
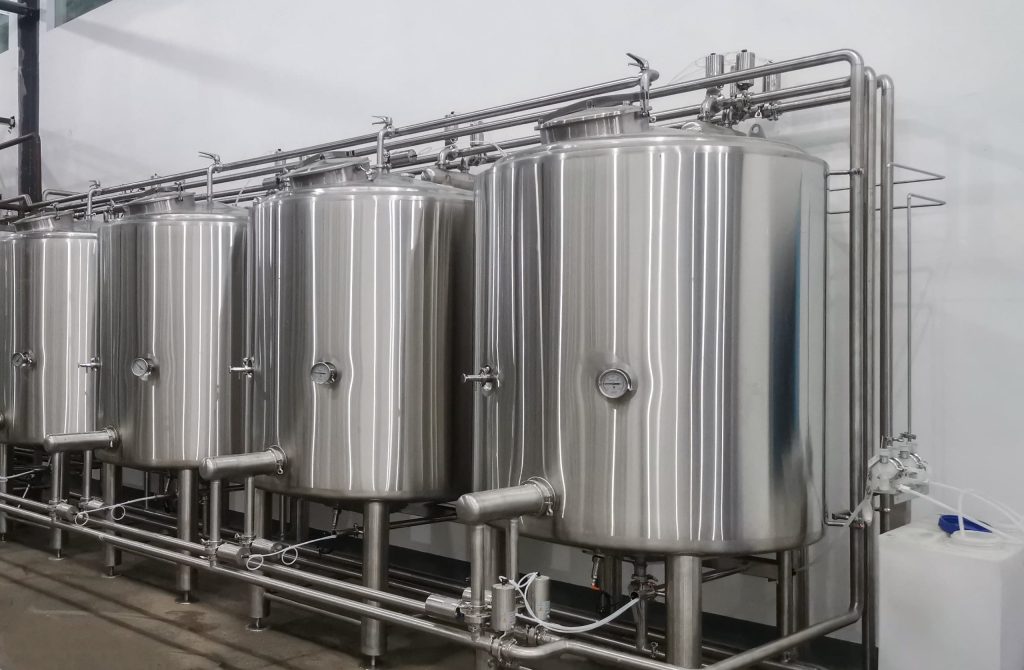
Brewing beer is both an art and a science, but behind the craft lies the necessity for stringent cleaning processes to maintain quality and consistency. In recent years, the advent of Clean-in-Place (CIP) systems has revolutionized the way breweries approach sanitation. This article explores the impact of CIP system brewery solutions on cleaning processes, efficiency, and overall brewery operations.
Understanding CIP Systems
Before delving into the specifics, it’s essential to grasp the fundamentals of CIP systems. These automated systems streamline the cleaning of brewing equipment by circulating cleaning solutions through tanks, lines, and other components without disassembly. CIP systems eliminate the need for manual cleaning, reducing labor costs and improving cleaning consistency.
Benefits of CIP System Brewery Solutions
- Enhanced Efficiency: CIP systems reduce downtime by enabling cleaning to be performed in place, allowing brewers to focus on production rather than manual cleaning tasks.
- Improved Sanitation: Consistent and thorough cleaning is essential for preventing contamination and maintaining product quality. CIP systems ensure that equipment is thoroughly cleaned and sanitized between batches, reducing the risk of off-flavors and microbial growth.
- Cost Savings: While the initial investment in a CIP system may be significant, the long-term cost savings are substantial. Reduced labor costs, lower water and chemical usage, and extended equipment lifespan contribute to significant financial benefits.
- Environmental Sustainability: By optimizing water and chemical usage, CIP systems contribute to environmental sustainability by reducing resource consumption and waste generation.
Implementing CIP Systems: Best Practices
Successfully implementing a CIP system requires careful planning and adherence to best practices:
- Customization: Tailor the CIP system to the specific needs and layout of the brewery to maximize efficiency and effectiveness.
- Training: Proper training is essential for brewery staff to operate and maintain the CIP system correctly.
- Monitoring and Maintenance: Regular monitoring and maintenance ensure that the CIP system operates optimally and prolongs equipment lifespan.
- Documentation: Keep detailed records of CIP procedures, including cleaning parameters and validation data, to comply with regulatory requirements and maintain quality standards.
Comparison of Manual Cleaning vs. CIP Systems
Aspect | Manual Cleaning | CIP Systems |
---|---|---|
Cleaning Time | Time-consuming, requires disassembly of equipment | Automated process, reduces cleaning time and labor |
Sanitation Levels | Inconsistent, dependent on manual scrubbing | Ensures consistent sanitation levels across all equipment |
Cost | Higher labor costs, increased water and chemical usage | Lower labor costs, reduced water and chemical consumption |
Environmental | Higher water and chemical usage, increased waste generation | Optimizes resource usage, reduces environmental footprint |
Case Studies: Real-World Applications
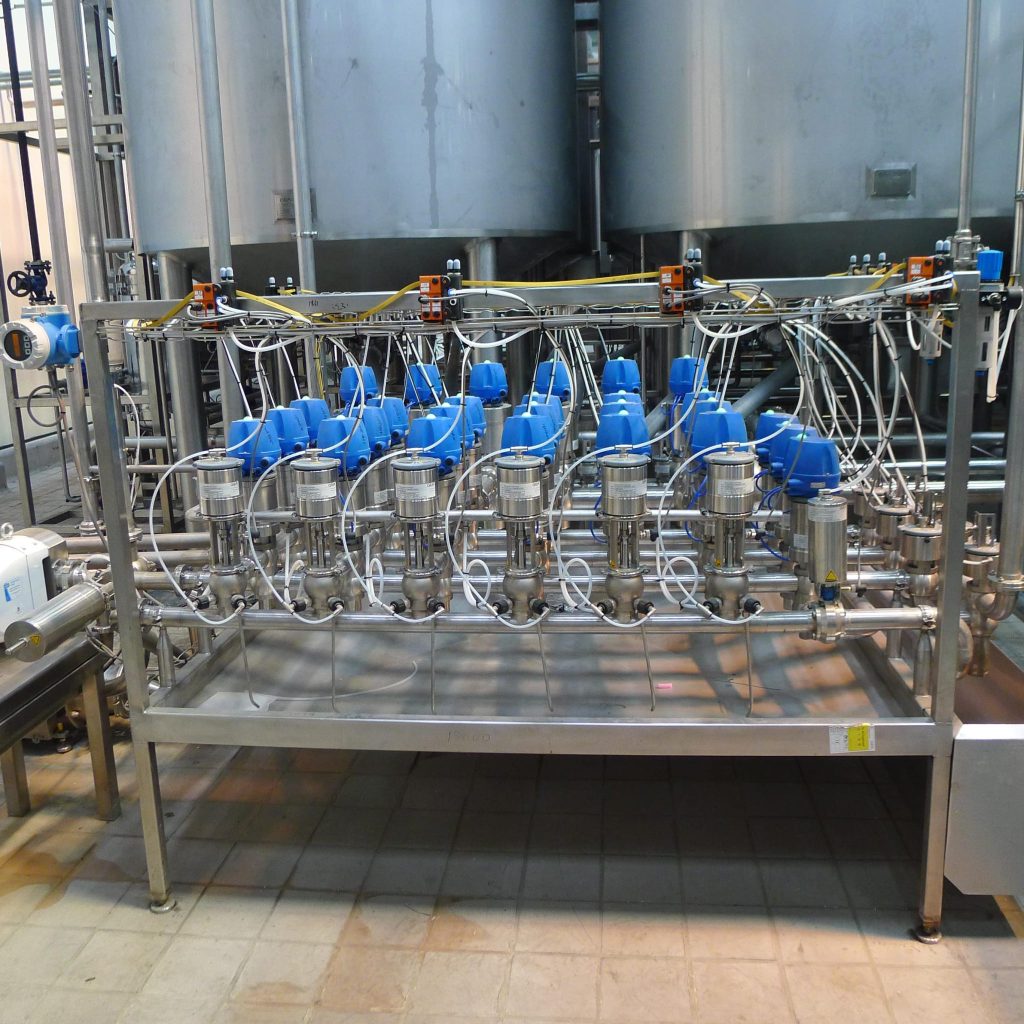
To illustrate the effectiveness of CIP system brewery solutions, let’s examine two case studies:
- Craft Brewery X: After implementing a CIP system, Craft Brewery X reduced cleaning time by 50% and decreased water usage by 30%, resulting in significant cost savings and improved production efficiency.
- Regional Brewery Y: By upgrading to a state-of-the-art CIP system, Regional Brewery Y achieved a 20% reduction in cleaning chemical usage while ensuring consistent sanitation levels across all production lines.
Conclusion
In conclusion, CIP system brewery solutions have transformed cleaning processes in the brewing industry, offering enhanced efficiency, improved sanitation, and significant cost savings. By investing in CIP systems and adhering to best practices, breweries can streamline operations, maintain product quality, and contribute to a more sustainable brewing process. As technology continues to evolve, the role of CIP systems in brewery operations will only become more integral, driving further innovation and efficiency in the craft of brewing.
FAQ
Q:What is the difference between manual cleaning and CIP systems?
A:Manual cleaning requires disassembly of equipment and manual scrubbing, whereas CIP systems automate the cleaning process without the need for disassembly.
Q:Are CIP systems suitable for all brewery sizes?
A:While CIP systems are commonly associated with larger breweries, they can be scaled to accommodate breweries of all sizes, from craft breweries to large-scale operations.
Q:How do CIP systems contribute to product quality?
A:By ensuring thorough cleaning and sanitation, CIP systems help maintain product quality and consistency by reducing the risk of contamination and off-flavors.