Introduction
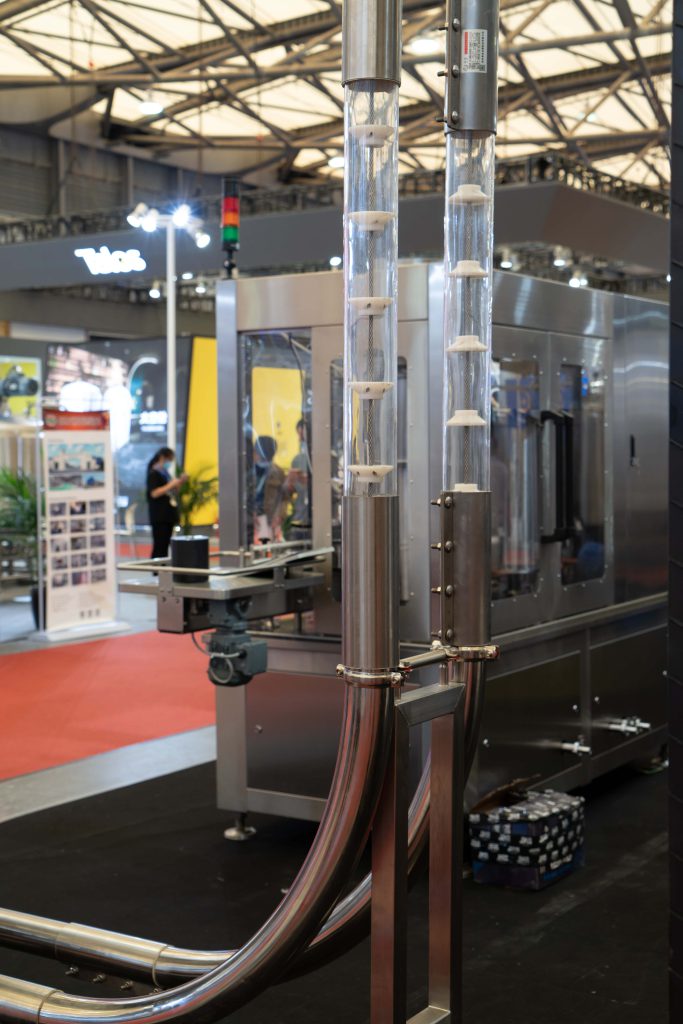
In today’s competitive industrial landscape, efficiency is key to maintaining profitability and meeting customer demands. Automated conveyor systems have emerged as a pivotal technology, revolutionizing logistics and manufacturing processes across various industries. This blog explores how conveyor systems enhance efficiency, streamline operations, and contribute to overall productivity gains.
Understanding Conveyor Systems
Conveyor systems are mechanical handling equipment that move materials from one location to another within a facility. They are integral in automating repetitive tasks such as sorting, packaging, and transportation of goods. Key components include belts, rollers, motors, and sensors, all working together to ensure seamless material flow.
Types of Conveyor Systems
There are several types of conveyor systems tailored to different operational needs:
- Belt Conveyors: Belt conveyors are indispensable for transporting bulk materials efficiently over long distances within industrial facilities. They utilize a continuous loop of sturdy material, typically rubber or fabric, which supports and moves items along a belt surface. This design minimizes friction and facilitates smooth material flow, making belt conveyors suitable for industries ranging from mining to food processing. Their versatility allows customization with various belt types and configurations to handle specific loads and environmental conditions, ensuring optimal performance and longevity.
- Roller Conveyors: Roller conveyors are essential for assembly lines and order picking operations due to their ability to move products smoothly and efficiently. These systems consist of rollers mounted on a series of frames that facilitate the movement of items along a fixed path. By reducing manual handling and optimizing material flow, roller conveyors enhance productivity and streamline production processes. They come in various configurations, including gravity-driven and powered options, tailored to meet diverse operational requirements and space constraints in manufacturing and distribution environments.
- Overhead Conveyors: Overhead conveyors are highly efficient for transporting products through vertical spaces or across overhead paths within a facility. They consist of a continuous chain or cable loop that supports and moves items suspended from hooks, carriers, or trolleys. Overhead conveyors maximize floor space utilization and facilitate complex material handling tasks such as paint finishing in automotive manufacturing or garment storage in textile industries. Their flexibility allows for customization with various attachments and controls to ensure precise and reliable movement of goods throughout the production or distribution process.
- Screw Conveyors: Screw conveyors are particularly well-suited for handling bulk materials in diverse industrial applications, including agriculture, mining, and wastewater treatment. These conveyors consist of a rotating helical screw blade, known as an auger, enclosed within a tube or trough. As the screw rotates, it pushes materials forward along the conveyor path, effectively conveying powders, grains, or sludge with minimal risk of material degradation or contamination. Screw conveyors are versatile and adaptable, offering various configurations such as horizontal, inclined, or vertical orientations to meet specific material handling requirements and operational environments.
Benefits of Automated Conveyor Systems
Automated conveyor systems offer numerous benefits:
- Increased Efficiency: Reduces manual handling and labor costs.
- Enhanced Safety: Minimizes worker exposure to hazardous environments.
- Improved Accuracy: Ensures precise movement and sorting of goods.
- Scalability: Easily expandable to accommodate growing production needs.
Implementing Conveyor Systems
Implementing a conveyor system involves careful planning and integration:
- Needs Assessment: Analyze current workflows and identify areas for improvement.
- System Design: Custom-design conveyor layout and choose appropriate components.
- Installation: Ensure proper installation and integration with existing infrastructure.
- Testing and Optimization: Conduct thorough testing to fine-tune performance and efficiency.
Case Studies: Real-World Applications
Conveyor systems have been successfully deployed in various industries:
- Automotive: Streamlining assembly processes and parts handling.
- Food and Beverage: Ensuring hygiene and efficiency in packaging lines.
- E-commerce: Facilitating order fulfillment and logistics operations.
ROI Analysis
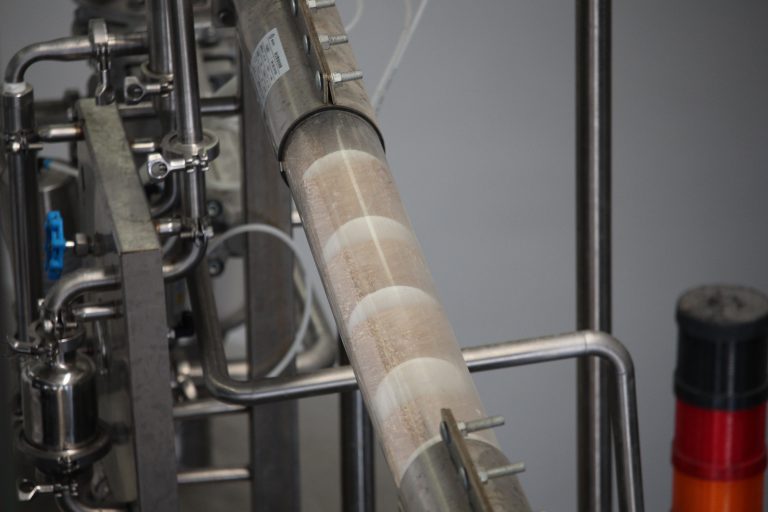
Conveyor systems contribute to a positive return on investment (ROI) through:
- Cost Savings: Reduced labor costs and improved operational efficiency.
- Increased Throughput: Faster processing times and minimized bottlenecks.
- Operational Flexibility: Adaptable to changing production demands.
Conclusion
Automated conveyor systems play a pivotal role in enhancing efficiency and productivity across industries. By streamlining material handling and logistics processes, these systems contribute to cost savings, improved safety, and operational scalability. As technology continues to advance, the role of conveyor systems in modern manufacturing and distribution will only grow, driving further innovations and efficiencies.
FAQ
Q: How do conveyor systems improve workplace safety?
A:Conveyor systems automate repetitive tasks, reducing the need for manual handling and minimizing workplace injuries.
Q: What maintenance is required for conveyor systems?
A:Regular inspection of belts, motors, and bearings is crucial to prevent downtime and ensure optimal performance.
Q: Can conveyor systems be customized for specific industry needs?
A:Yes, conveyor systems can be tailored with specialized belts, sensors, and controls to meet unique operational requirements.