Introduction
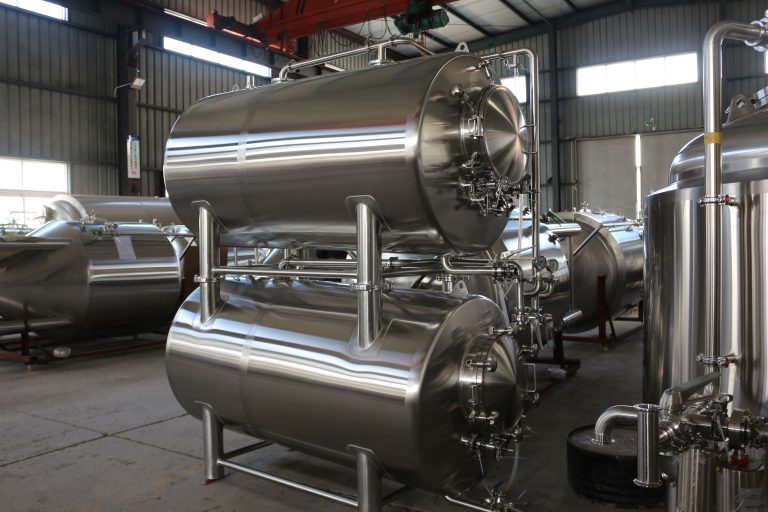
Industrial brewing systems represent the pinnacle of brewing technology, designed for large-scale beer production. Unlike smaller craft breweries, industrial systems prioritize efficiency, consistency, and volume, producing vast quantities of beer for mass consumption. These sophisticated setups incorporate advanced automation, precise control mechanisms, and robust equipment to ensure optimal brewing conditions and consistent product quality. This guide delves into the intricacies of industrial brew systems, exploring their components, processes, and significance in the global beer market.
The Significance of Industrial Brew Systems in the Global Beer Market
Industrial brew systems play a crucial role in meeting the global demand for beer. Their high production capacity enables large breweries to supply beer to vast markets, both domestically and internationally. These systems also contribute to economies of scale, reducing production costs and making beer more accessible to consumers. Furthermore, ongoing advancements in industrial brewing technology continuously improve efficiency, sustainability, and product quality within the industry.
Key Components of Industrial Brew Systems
An industrial brew system is a complex network of interconnected equipment, each playing a vital role in the brewing process. Understanding these components is crucial for comprehending the overall system functionality.
The Brewhouse: The Heart of Industrial Brewing
The brewhouse is where the initial stages of brewing occur, involving mashing, lautering, boiling, and whirlpooling. Industrial brewhouses are significantly larger and more automated than those found in smaller breweries. They often incorporate multiple vessels to handle larger volumes and ensure continuous production.
Fermentation Vessels: Where the Magic Happens
Fermentation vessels, also known as fermenters, are where yeast converts sugars into alcohol and carbon dioxide. Industrial breweries utilize large cylindrical-conical tanks made of stainless steel. These tanks are equipped with temperature control systems to maintain optimal fermentation conditions.
Filtration and Clarification: Achieving Clarity and Stability
Filtration and clarification processes remove any remaining solids and impurities from the beer, resulting in a clear and stable final product. Industrial systems employ various filtration techniques, including centrifugation and filtration through diatomaceous earth or membrane filters.
Packaging Lines: Preparing Beer for Distribution
Packaging lines automate the filling, sealing, and labeling of beer into bottles, cans, or kegs. High-speed packaging lines are essential for industrial breweries to keep up with production volumes and ensure timely distribution.
The Industrial Brewing Process: A Step-by-Step Overview
The industrial brewing process follows the same fundamental principles as traditional brewing but on a much larger scale and with greater automation.
Milling and Mashing: Preparing the Grains
Milling crushes the malted grains to expose the starches. The milled grains are then mixed with hot water in the mash tun, where enzymes convert the starches into fermentable sugars. Industrial systems use large mills and mash tuns with automated temperature control and mixing mechanisms.
Lautering and Wort Separation: Extracting the Sweet Wort
Lautering separates the sweet wort (sugar-rich liquid) from the spent grain. Industrial lauter tuns are designed for efficient wort extraction and often incorporate automated rakes and sparge systems.
Boiling and Whirlpooling: Adding Hops and Clarifying the Wort
The wort is boiled in the brew kettle, where hops are added for bitterness, aroma, and preservation. After boiling, the wort is transferred to a whirlpool to remove any remaining solids.
Fermentation and Maturation: Developing Flavor and Complexity
The cooled wort is transferred to fermentation vessels, where yeast is added. The fermentation process typically takes several days or weeks, depending on the beer style. After fermentation, the beer may undergo a maturation period to further develop its flavor and complexity.
Filtration and Packaging: Preparing the Final Product
The beer is filtered to remove any remaining yeast and solids before being packaged into bottles, cans, or kegs.
Industrial Brew System Design Considerations
Designing an industrial brew system is a complex undertaking that requires meticulous planning and careful consideration of numerous interconnected factors. A well-designed system not only meets current production needs but also allows for future growth and adaptation.
Capacity and Scalability: Meeting Current and Future Demands
Determining the appropriate capacity is paramount. This involves a thorough market analysis to forecast current and projected demand. Factors to consider include:
- Current Market Share: Understanding the existing market share and potential for growth is crucial.
- Projected Growth: Forecasting future demand based on market trends, consumer preferences, and expansion plans is essential.
- Production Volume: Defining the required annual or monthly production volume in hectoliters or barrels.
- Brewing Schedule: Determining the number of brews per day or week and the required turnaround time between brews.
Scalability is equally important. The system should be designed to accommodate future expansion without requiring major overhauls. This can be achieved by:
- Modular Design: Implementing a modular design allows for the addition of new equipment as needed.
- Space Allocation: Allocating sufficient space for future expansion within the brewery layout.
- Utility Infrastructure: Ensuring that the utility infrastructure (water, electricity, steam) can support future capacity increases.
Automation and Control: Ensuring Consistency and Efficiency
Automation is a cornerstone of modern industrial brewing, enabling consistent product quality and optimized production efficiency. Key aspects of automation include:
- Process Control Systems: Implementing sophisticated process control systems (e.g., SCADA) to monitor and control all stages of the brewing process.
- Automated Valves and Pumps: Utilizing automated valves and pumps for precise control of liquid flow and transfer.
- Automated Cleaning Systems (CIP): Implementing Clean-in-Place (CIP) systems for automated cleaning of tanks and pipelines, reducing downtime and ensuring hygiene.
- Data Logging and Analysis: Collecting and analyzing data from various sensors and instruments to optimize brewing parameters and identify potential issues.
Automation not only ensures consistency but also reduces labor costs, minimizes human error, and improves overall efficiency.
Energy Efficiency and Sustainability: Minimizing Environmental Impact
Modern industrial breweries place a strong emphasis on energy efficiency and sustainability to minimize their environmental footprint and reduce operating costs. Strategies include:
- Heat Recovery Systems: Implementing heat recovery systems to capture and reuse waste heat from the brewing process.
- Energy-Efficient Equipment: Utilizing high-efficiency boilers, chillers, and other equipment to reduce energy consumption.
- Water Conservation: Implementing water-saving technologies and practices to reduce water usage.
- Waste Management: Implementing effective waste management programs to minimize waste generation and maximize recycling.
- Renewable Energy Sources: Exploring the use of renewable energy sources such as solar or wind power.
By prioritizing energy efficiency and sustainability, industrial breweries can reduce their environmental impact, enhance their brand image, and achieve long-term cost savings.
Industrial Brew System Maintenance and Troubleshooting
Proper maintenance is crucial for ensuring the reliable and efficient operation of an industrial brew system. A proactive maintenance program can prevent costly downtime, extend equipment lifespan, and maintain product quality.
Regular Cleaning and Inspections: Preventing Problems
Regular cleaning and inspections are essential for preventing equipment malfunctions and ensuring optimal performance. Key practices include:
- Scheduled Cleaning: Implementing a regular cleaning schedule for all equipment, including tanks, pipelines, and heat exchangers.
- Preventive Maintenance: Performing regular inspections and maintenance tasks, such as lubricating moving parts, replacing worn seals, and checking electrical connections.
- Calibration: Regularly calibrating sensors and instruments to ensure accurate readings and precise control.
- Record Keeping: Maintaining detailed records of all maintenance activities, including dates, tasks performed, and any issues encountered.
By implementing a proactive maintenance program, breweries can identify and address potential problems before they escalate into major issues.
Troubleshooting Common Issues: Addressing Problems Effectively
Having a well-defined troubleshooting process is crucial for addressing any issues that may arise during the brewing process. This involves:
- Troubleshooting Guides: Developing comprehensive troubleshooting guides for common equipment malfunctions and brewing problems.
- Training: Providing thorough training to brewery staff on troubleshooting procedures and best practices.
- Root Cause Analysis: Conducting thorough root cause analysis to identify the underlying cause of any recurring problems.
- Spare Parts Inventory: Maintaining an adequate inventory of spare parts to minimize downtime in case of equipment failure.
- Remote Monitoring and Diagnostics: Utilizing remote monitoring and diagnostic tools to identify and diagnose problems remotely.
By having a well-defined troubleshooting process and a trained staff, breweries can quickly and effectively address any issues that arise, minimizing downtime and ensuring consistent production.
Comparing Industrial Brew Systems to Craft Brewing Systems
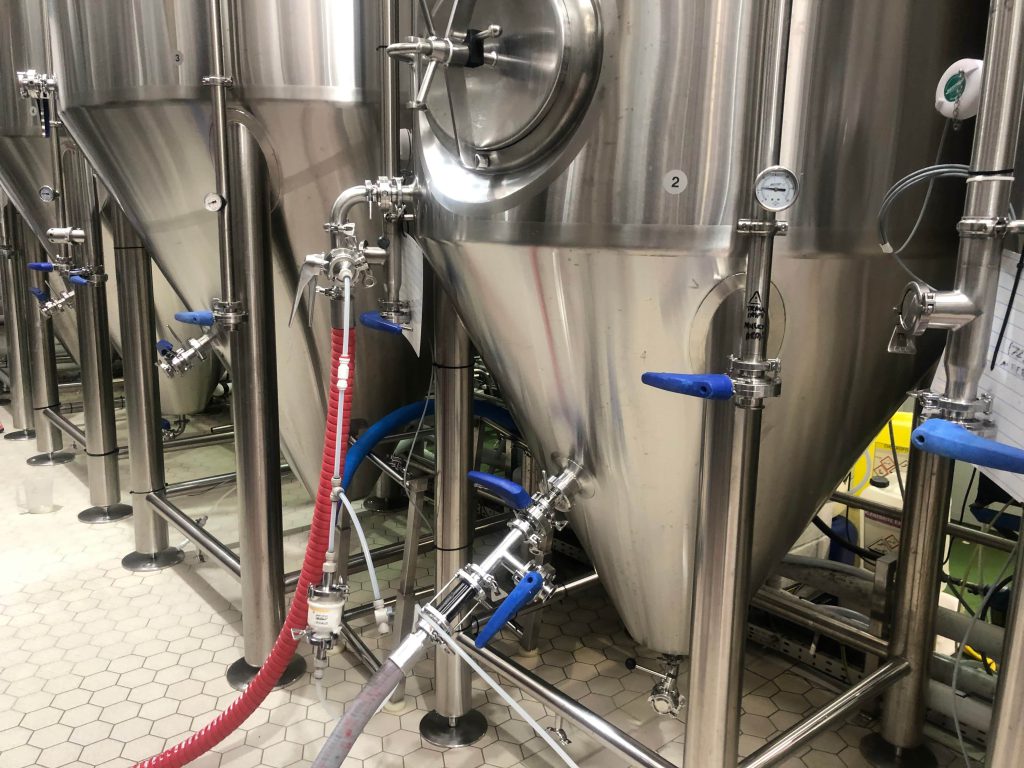
Feature | Industrial Brew Systems | Craft Brewing Systems |
---|---|---|
Production Volume | High | Low to Medium |
Automation | High | Low to Medium |
Focus | Efficiency, Consistency, Volume | Flavor, Innovation, Variety |
Target Market | Mass Market | Niche Market |
System Size | Large | Small to Medium |
Equipment Cost | High | Medium to High |
Product Variety | Limited | Wide |
Conclusion
Industrial brew systems will continue to evolve, driven by advancements in technology and changing consumer demands. The future of industrial brewing will likely focus on greater automation, increased sustainability, and the development of new and innovative beer styles. These systems remain crucial for meeting global beer demand, and their ongoing development ensures the continued availability of beer worldwide.
FAQ
What is the typical lifespan of an industrial brew system?
With proper maintenance, an industrial brew system can last for several decades.
How much does an industrial brew system cost?
The cost of an industrial brew system can vary significantly depending on its size, capacity, and level of automation. It can range from several million to tens of millions of dollars.
What are the key advantages of using an industrial brew system?
Key advantages include high production capacity, consistent product quality, and efficient operation.
What are some common challenges faced by industrial breweries?
Common challenges include maintaining product consistency at large volumes, managing energy consumption, and adapting to changing consumer preferences.