Introduction
In today’s industrial landscape, the need for efficient and reliable material transport systems is paramount. Pipe Conveyor Systems have emerged as a revolutionary solution, offering numerous advantages over traditional conveyor systems. This blog will delve into the intricacies of Pipe Conveyor Systems, exploring their benefits, applications, and key features. By the end of this article, you’ll have a comprehensive understanding of why Pipe Conveyor Systems are the future of material transport.
What is a Pipe Conveyor System?
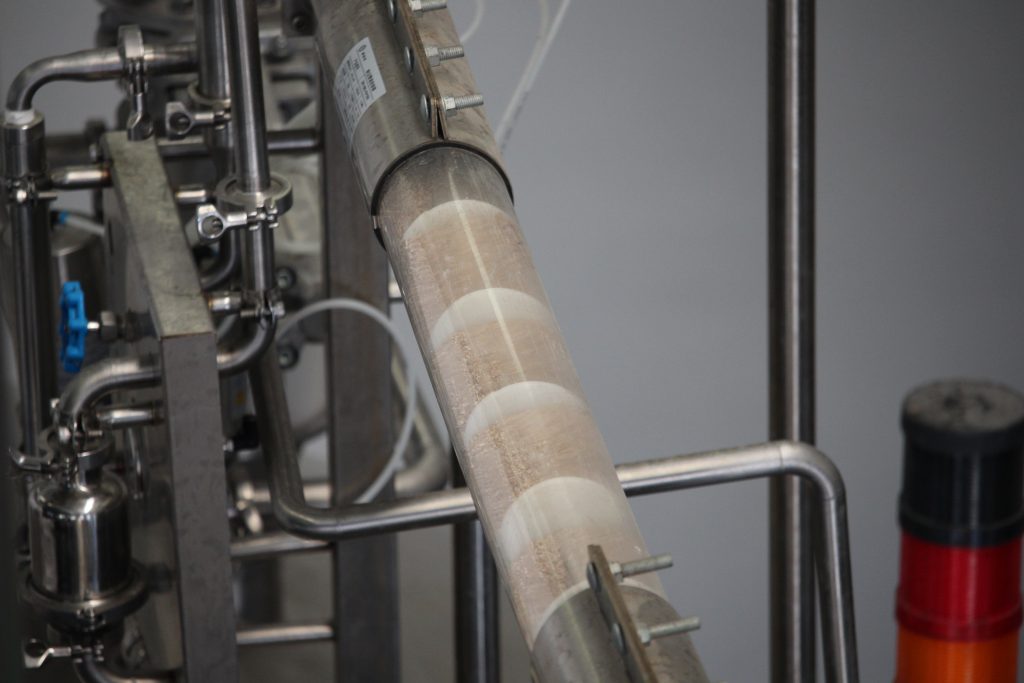
A Pipe Conveyor System is an advanced and innovative type of conveyor belt system designed to handle and transport materials efficiently and safely. Unlike traditional conveyor belts, which consist of a flat surface that carries the material from one point to another, a Pipe Conveyor System encases the material within a tubular or pipe-shaped enclosure. This unique design offers several distinct advantages, making it a preferred choice for various industrial applications.
The Mechanics of Pipe Conveyor Systems
The core component of a Pipe Conveyor System is the conveyor belt, which is engineered to transform from a flat shape into a circular, pipe-like structure. This transformation occurs gradually as the belt moves through specially designed rollers and idlers that guide and mold the belt into the desired shape. The edges of the belt overlap to form a complete enclosure, effectively sealing the material inside the pipe. At the unloading point, the belt returns to its flat shape, allowing the material to be discharged.
Key Features of Pipe Conveyor Systems
- Enclosed Design: The pipe-shaped enclosure of the conveyor belt is a defining feature that sets Pipe Conveyor Systems apart from traditional conveyors. This design ensures that the material remains securely contained within the belt, preventing spillage and contamination. The enclosed system also protects the material from external elements such as wind, rain, and dust, which can degrade the quality of the transported material.
- Flexibility and Versatility: Pipe Conveyor Systems are highly flexible and can be configured to navigate complex routes, including sharp curves, steep inclines, and declines. This adaptability makes them suitable for a wide range of industrial settings, where space constraints and challenging terrain are common.
- Environmental Benefits: By preventing material spillage and reducing dust and noise emissions, Pipe Conveyor Systems contribute to a cleaner and more environmentally friendly operation. The enclosed system minimizes the impact on the surrounding environment, making it an ideal choice for industries with stringent environmental regulations.
- Enhanced Safety: The enclosed nature of Pipe Conveyor Systems enhances workplace safety by minimizing the risk of accidents related to material spillage and exposure to moving parts. The system also reduces the generation of airborne dust, which can pose health hazards to workers.
- Cost-Effectiveness: Over time, Pipe Conveyor Systems can lead to significant cost savings. The enclosed design reduces the need for frequent cleaning and maintenance, as the material is protected from contamination and external damage. Additionally, the robust construction of the system ensures a longer service life, reducing the frequency of replacements and repairs.
Applications of Pipe Conveyor Systems
Pipe Conveyor Systems are employed across various industries due to their efficiency and versatility. In the mining industry, they are used to transport bulk materials such as coal, ore, and aggregate, where the enclosed design prevents material loss and contamination. In the cement industry, Pipe Conveyor Systems are ideal for transporting raw materials and finished products through complex plant layouts. Power plants utilize these systems to move coal and other fuels, minimizing dust emissions and enhancing safety. The chemical industry benefits from the ability to safely transport hazardous materials, while the food and beverage industry uses Pipe Conveyor Systems to maintain the integrity and quality of transported ingredients and products.
Benefits of Using Pipe Conveyor Systems
Pipe Conveyor Systems offer a multitude of advantages that make them a superior choice for material transport in various industrial applications. These benefits stem from their innovative design, which enhances efficiency, safety, and environmental sustainability. Here, we will delve deeper into the key benefits of using Pipe Conveyor Systems and how they can transform material handling processes.
Environmental Protection
One of the most significant benefits of Pipe Conveyor Systems is their positive impact on the environment. The enclosed design of these systems plays a crucial role in minimizing dust and noise emissions, which are common issues with traditional open conveyor belts. This reduction in emissions contributes to a cleaner and safer working environment, which is particularly important in industries subject to strict environmental regulations. Moreover, by containing the material within a pipe, these systems prevent contamination of the surrounding area, protecting both the environment and the health of workers.
Flexibility in Routing
Pipe Conveyor Systems offer unparalleled flexibility in routing, making them an ideal solution for complex industrial layouts. They can easily navigate through sharp curves, steep inclines, and declines, which would pose significant challenges for traditional conveyor belts. This ability to adapt to difficult terrains and confined spaces allows for more efficient use of available space in industrial facilities. As a result, companies can optimize their material handling processes without the need for extensive modifications to existing infrastructure.
Reduced Material Loss
Material spillage is a common problem with conventional conveyor belts, leading to product loss, increased cleaning costs, and potential environmental hazards. Pipe Conveyor Systems address this issue effectively by securely enclosing the material within the pipe-shaped belt. This design ensures that no material is lost during transport, leading to higher efficiency and reduced waste. Additionally, the prevention of spillage minimizes the need for frequent cleanup operations, saving both time and resources.
Improved Safety
Safety is a paramount concern in industrial operations, and Pipe Conveyor Systems significantly enhance workplace safety. The enclosed design reduces the risk of accidents associated with exposed moving parts and material spillage. By containing the material, these systems also lower the likelihood of slips, trips, and falls caused by scattered debris. Furthermore, the reduction in dust emissions contributes to better air quality, reducing the risk of respiratory issues among workers. Overall, Pipe Conveyor Systems create a safer and healthier work environment.
Lower Maintenance Costs
The robust construction and innovative design of Pipe Conveyor Systems lead to lower maintenance and operational costs compared to traditional conveyor belts. The enclosed system protects the belt and the transported material from external elements such as wind, rain, and debris, which can cause wear and tear. This protection extends the lifespan of the belt and reduces the frequency of repairs and replacements. Additionally, the reduced need for cleaning and the prevention of material spillage contribute to lower maintenance expenses, resulting in significant cost savings over time.
Enhanced Efficiency
Pipe Conveyor Systems enhance the overall efficiency of material transport operations. Their ability to handle various materials, including fine powders, granules, and bulk solids, makes them versatile for different industrial applications. The enclosed design ensures a continuous and uninterrupted flow of material, minimizing downtime and maximizing productivity. Moreover, the systems can operate over long distances with minimal energy consumption, further improving their efficiency and reducing operational costs.
Versatility in Applications
The versatility of Pipe Conveyor Systems makes them suitable for a wide range of industries, including mining, cement, power plants, chemical, and food and beverage. In the mining industry, for instance, these systems are used to transport coal, ore, and aggregate, ensuring safe and efficient handling of bulk materials. In the cement industry, Pipe Conveyor Systems facilitate the movement of raw materials and finished products through complex plant layouts. Power plants benefit from their ability to transport coal and other fuels with minimal environmental impact. The chemical industry relies on these systems for the safe transport of hazardous materials, while the food and beverage industry uses them to maintain the quality and integrity of transported ingredients and products.
Applications of Pipe Conveyor Systems
Pipe Conveyor Systems are highly versatile and adaptable, making them suitable for a wide range of industries and applications. Their innovative design and numerous advantages enable them to meet the specific needs of various sectors, enhancing operational efficiency and safety. Below, we will explore the primary applications of Pipe Conveyor Systems in different industries and how they contribute to improved material handling processes.
Mining Industry
The mining industry is one of the primary beneficiaries of Pipe Conveyor Systems. These systems are employed to transport bulk materials such as coal, ore, and aggregate from extraction sites to processing plants or storage facilities. The enclosed design of Pipe Conveyor Systems is particularly advantageous in mining operations, where dust control and material spillage are significant concerns. By containing the material within the pipe, these systems prevent dust emissions, reduce environmental impact, and ensure that valuable resources are not lost during transport. Additionally, the flexibility of Pipe Conveyor Systems allows them to navigate the challenging terrains and complex routes often found in mining sites, including steep inclines, declines, and sharp curves.
Cement Industry
In the cement industry, Pipe Conveyor Systems play a crucial role in the efficient transport of raw materials and finished products. Cement plants often have complex layouts with multiple levels and confined spaces, making traditional conveyor systems impractical. Pipe Conveyor Systems, with their ability to handle curved routes and steep angles, provide an ideal solution for navigating these intricate plant designs. They are used to transport materials such as limestone, clay, clinker, and cement, ensuring that the production process remains smooth and uninterrupted. The enclosed design also helps in maintaining the quality of the transported materials by protecting them from contamination and external elements.
Power Plants
Power plants, especially those that rely on coal and other bulk fuels, utilize Pipe Conveyor Systems for efficient fuel transport. The systems are used to convey coal from storage yards to the boiler house, ensuring a continuous and reliable supply of fuel. The enclosed nature of Pipe Conveyor Systems significantly reduces dust emissions, which is a critical factor in maintaining air quality and adhering to environmental regulations. Moreover, by preventing material spillage, these systems enhance the overall safety of the power plant operations. Their ability to handle long distances and complex routes also makes them suitable for large-scale power generation facilities.
Chemical Industry
The chemical industry demands safe and efficient transport solutions for a wide range of materials, including hazardous and sensitive substances. Pipe Conveyor Systems provide an optimal solution for these requirements by securely enclosing the transported materials, thereby preventing leaks and spills that could pose significant safety and environmental risks. They are used to transport chemicals, powders, granules, and other bulk materials, ensuring that they reach their destination without contamination. The enclosed design also minimizes the exposure of workers to potentially harmful substances, enhancing workplace safety. Furthermore, the flexibility of Pipe Conveyor Systems allows them to be integrated into complex chemical processing facilities with ease.
Food and Beverage Industry
In the food and beverage industry, maintaining the integrity and quality of transported materials is of utmost importance. Pipe Conveyor Systems are widely used to transport ingredients, raw materials, and finished products within food processing plants. The enclosed design protects the transported materials from contamination, dust, and environmental factors, ensuring that they remain safe and hygienic. This is particularly crucial for products that are sensitive to external conditions or require strict adherence to sanitary standards. Pipe Conveyor Systems also help in reducing product loss and waste, contributing to more efficient and cost-effective operations.
Agricultural Sector
The agricultural sector benefits from Pipe Conveyor Systems for the transport of grains, seeds, and other bulk agricultural products. The enclosed design prevents the spillage and loss of valuable crops, while also protecting them from external elements such as moisture and pests. This ensures that the quality of the agricultural products is maintained throughout the transport process. Pipe Conveyor Systems are also used in grain handling and storage facilities, where they facilitate the efficient movement of large quantities of grain over long distances and through complex routes.
Port and Marine Terminals
Port and marine terminals utilize Pipe Conveyor Systems for the loading and unloading of bulk materials from ships. These systems are used to transport materials such as coal, minerals, grains, and other bulk commodities between storage facilities and vessels. The enclosed design helps in preventing material spillage into the water, reducing environmental pollution and adhering to maritime regulations. Pipe Conveyor Systems also offer the flexibility to handle varying ship sizes and docking configurations, making them a versatile solution for port operations.
Waste Management and Recycling
In the waste management and recycling industry, Pipe Conveyor Systems are used to transport waste materials and recyclables efficiently. The enclosed design minimizes odor, dust, and leakage, ensuring a cleaner and safer environment. These systems are used in waste sorting facilities, recycling plants, and landfill operations to move materials such as household waste, industrial scrap, and recyclables. By enhancing the efficiency of waste transport, Pipe Conveyor Systems contribute to more effective waste management and recycling processes.
Key Components of a Pipe Conveyor System
To understand the effectiveness of Pipe Conveyor Systems, it’s important to look at their key components. Here is a table summarizing the main parts of a typical Pipe Conveyor System:
Component | Description |
---|---|
Belt | The flexible, pipe-shaped belt that encloses the material. |
Rollers | Support and guide the belt along its path. |
Drive System | Powers the movement of the belt. |
Idlers | Provide additional support and help maintain the belt’s shape. |
Tensioning System | Maintains the proper tension in the belt to ensure smooth operation. |
Loading/Unloading Stations | Points where material is loaded onto and unloaded from the belt. |
Design Considerations for Pipe Conveyor Systems
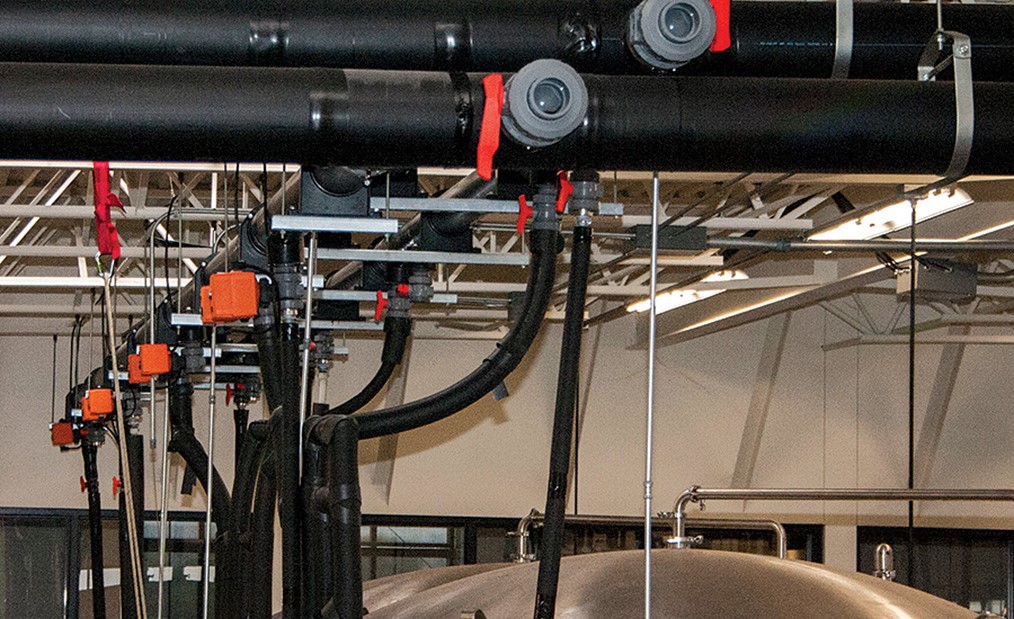
Designing a Pipe Conveyor System requires careful consideration of various factors to ensure optimal performance, efficiency, and safety. The unique characteristics of Pipe Conveyor Systems, such as their enclosed design and ability to handle complex routes, necessitate a thorough understanding of the specific requirements of the application. Below, we delve into the critical design considerations that must be taken into account when planning and implementing a Pipe Conveyor System.
Material Characteristics
Understanding the properties of the material to be transported is paramount in the design of a Pipe Conveyor System. Key material characteristics include particle size, density, moisture content, abrasiveness, and flowability. These properties influence the selection of the belt material, the design of the loading and unloading stations, and the overall system configuration. For example, abrasive materials may require a belt with high wear resistance, while sticky materials might necessitate special cleaning mechanisms to prevent buildup inside the pipe.
Route Complexity
One of the significant advantages of Pipe Conveyor Systems is their ability to navigate complex routes, including sharp curves, steep inclines, and declines. The design must account for the specific path the conveyor will follow, ensuring that the system can handle the required turns and elevation changes without compromising performance. Detailed route planning involves mapping out the conveyor’s path, identifying potential obstacles, and determining the necessary supports and structural elements. The flexibility of Pipe Conveyor Systems allows for more efficient use of space in industrial facilities, but this requires precise engineering to maintain belt integrity and material containment.
Load Capacity
The load capacity of the Pipe Conveyor System is a critical design consideration. It encompasses the weight and volume of the material to be transported and affects the choice of belt width, strength, and tensioning mechanisms. The system must be designed to handle the maximum expected load without causing excessive wear or operational issues. Accurate load calculations ensure that the conveyor can operate efficiently under varying conditions, preventing overloading and minimizing the risk of belt damage or system failure.
Environmental Conditions
The operating environment significantly impacts the design of a Pipe Conveyor System. Factors such as temperature, humidity, exposure to chemicals, and weather conditions must be considered when selecting materials and designing components. For instance, extreme temperatures may require heat-resistant belts, while corrosive environments might necessitate the use of stainless steel or other durable materials. Additionally, outdoor installations must account for weather-related challenges such as rain, wind, and snow, ensuring that the system remains reliable and safe under all conditions.
System Integration
Integrating the Pipe Conveyor System with existing infrastructure and processes is essential for seamless operation. This involves ensuring compatibility with other material handling equipment, such as feeders, hoppers, and storage bins. The design must facilitate smooth transitions at loading and unloading points, minimizing disruptions and maintaining the integrity of the transported material. Effective system integration enhances overall efficiency and reduces the risk of operational bottlenecks.
Maintenance and Accessibility
Designing for ease of maintenance and accessibility is crucial for minimizing downtime and ensuring long-term reliability. The system should include features that facilitate routine inspections, cleaning, and repairs. For example, easy access to rollers, idlers, and tensioning mechanisms can simplify maintenance tasks and reduce the time required for troubleshooting and repairs. Additionally, incorporating condition monitoring systems can help detect issues early, allowing for proactive maintenance and preventing costly breakdowns.
Safety Considerations
Safety is a top priority in the design of Pipe Conveyor Systems. The enclosed design inherently reduces the risk of material spillage and dust emissions, but additional safety features are necessary to protect workers and equipment. These may include emergency stop buttons, safety guards, warning alarms, and automated shutdown mechanisms in case of malfunctions. The system must comply with industry safety standards and regulations, and regular safety audits should be conducted to ensure ongoing compliance.
Energy Efficienc
Energy efficiency is an important consideration in the design of Pipe Conveyor Systems, especially for long-distance or high-capacity installations. Selecting energy-efficient motors, optimizing belt speed, and minimizing frictional losses can significantly reduce operational costs and environmental impact. Additionally, incorporating energy recovery systems, such as regenerative braking, can further enhance the system’s efficiency and sustainability.
Cost Considerations
While Pipe Conveyor Systems offer numerous advantages, they also represent a significant investment. The design process must balance performance requirements with budget constraints, ensuring that the system delivers value over its operational life. This involves evaluating the total cost of ownership, including initial capital expenditure, maintenance costs, energy consumption, and potential downtime. A well-designed system should provide a favorable return on investment through enhanced efficiency, reduced operational costs, and improved reliability.
Case Study: Implementing a Pipe Conveyor System in a Mining Operation
Implementing a Pipe Conveyor System in a mining operation can significantly improve efficiency, safety, and environmental sustainability. This case study explores the practical application of a Pipe Conveyor System in a large-scale mining operation, detailing the challenges faced, the solutions provided by the Pipe Conveyor System, and the overall impact on the mining process.
Background
A large mining company, operating in a remote and environmentally sensitive area, needed an efficient solution to transport coal from an open-pit mine to a processing plant located several kilometers away. The traditional conveyor systems previously used were inadequate due to the complex terrain, which included steep inclines, sharp curves, and significant elevation changes. Additionally, the open design of these conventional systems resulted in substantial material spillage and dust emissions, posing environmental and safety concerns.
Challenges
The primary challenges faced by the mining operation included:
- Complex Terrain: The route from the mine to the processing plant involved navigating steep inclines, declines, and multiple sharp curves. Traditional conveyor systems struggled with these complex routes, leading to frequent operational disruptions and inefficiencies.
- Material Spillage and Dust Emissions: The open design of the existing conveyor systems resulted in significant material loss and dust emissions. This not only led to economic losses but also created environmental and safety hazards.
- Maintenance and Downtime: The harsh mining environment caused rapid wear and tear on the conveyor components, leading to frequent maintenance and prolonged downtime. This negatively impacted the overall productivity and operational efficiency of the mine.
- Environmental Regulations: Operating in an environmentally sensitive area, the mining company had to comply with stringent environmental regulations. The existing systems failed to meet these standards, resulting in potential regulatory penalties and reputational damage.
Solution: Implementing a Pipe Conveyor System
To address these challenges, the mining company decided to implement a Pipe Conveyor System. This decision was based on the system’s ability to handle complex routes, minimize material spillage, reduce dust emissions, and enhance overall operational efficiency.
System Design and Implementation
The design process involved several critical steps:
- Route Planning: Detailed route planning was conducted to map out the most efficient path from the mine to the processing plant. The flexibility of the Pipe Conveyor System allowed it to navigate the steep inclines, declines, and sharp curves with ease.
- Material Selection: The belt material was selected based on the specific properties of the coal, including its abrasiveness and moisture content. A high-strength, wear-resistant belt was chosen to ensure durability and longevity in the harsh mining environment.
- Structural Support: Robust supporting structures were designed to provide stability and support along the entire route. This included specialized supports for steep inclines and declines, ensuring the belt remained in the correct shape and alignment.
- Environmental Protection: The enclosed design of the Pipe Conveyor System was crucial in preventing material spillage and dust emissions. Additional features such as dust suppression systems were integrated at loading and unloading points to further reduce environmental impact.
- Safety Features: Comprehensive safety features were incorporated into the system, including emergency stop buttons, safety guards, and automated shutdown mechanisms. These measures ensured the safety of workers and compliance with industry safety standards.
Installation and Commissioning
The installation process was carefully planned to minimize disruptions to ongoing mining operations. The Pipe Conveyor System was installed in sections, with each section tested thoroughly before being integrated into the overall system. The commissioning phase involved extensive testing and calibration to ensure optimal performance and efficiency.
Results and Impact
The implementation of the Pipe Conveyor System resulted in several significant benefits for the mining operation:
- Enhanced Efficiency: The ability of the Pipe Conveyor System to handle complex routes and operate continuously without significant maintenance reduced operational disruptions and increased overall efficiency. The system transported 1,000 tons of coal per hour over a total distance of 5 kilometers.
- Reduced Material Loss: The enclosed design prevented material spillage, reducing material loss by 10%. This not only improved the economic efficiency of the operation but also minimized environmental contamination.
- Lower Dust Emissions: Dust and noise emissions were significantly reduced, contributing to a cleaner and safer working environment. This improvement helped the company comply with environmental regulations and avoid potential penalties.
- Improved Safety: The risk of accidents was minimized due to the enclosed design and comprehensive safety features. The reduction in material spillage and dust emissions also contributed to a safer working environment for employees.
- Cost Savings: Maintenance and operational costs were reduced by 15%, resulting in significant cost savings over time. The robust design of the system decreased the frequency of repairs and downtime, further enhancing productivity.
Conclusion
Pipe Conveyor Systems represent a significant advancement in the field of material transport. Their enclosed design, flexibility, and numerous benefits make them an ideal solution for a wide range of industries. By investing in Pipe Conveyor Systems, companies can enhance their operational efficiency, reduce environmental impact, and improve workplace safety. As the demand for efficient and sustainable material transport solutions continues to grow, Pipe Conveyor Systems are poised to play a crucial role in shaping the future of the industry.
FAQ
What is the main advantage of a Pipe Conveyor System?
The main advantage of a Pipe Conveyor System is its enclosed design, which prevents material spillage and contamination. This leads to improved environmental protection, safety, and efficiency.
Can Pipe Conveyor Systems handle steep inclines?
Yes, Pipe Conveyor Systems are capable of handling steep inclines and tight curves, making them suitable for complex routing scenarios.
What industries benefit most from Pipe Conveyor Systems?
Industries such as mining, cement, power plants, chemical, and food and beverage benefit significantly from Pipe Conveyor Systems due to their versatility and efficiency.
How do Pipe Conveyor Systems improve safety?
By enclosing the material within a pipe, Pipe Conveyor Systems reduce dust and noise emissions, prevent material spillage, and minimize the risk of accidents associated with exposed moving parts.
Are Pipe Conveyor Systems cost-effective?
Yes, Pipe Conveyor Systems are cost-effective in the long run due to their reduced maintenance and operational costs, longer service life, and enhanced efficiency.