Introduction
In the competitive world of brewing, efficiency and cleanliness are paramount. One of the most significant advancements in maintaining brewery hygiene while optimizing production time is the adoption of Clean-In-Place (CIP) systems. This technology allows brewers to clean tanks, pipes, and vessels without disassembly, reducing downtime and ensuring that the quality of the beer remains high. This blog post explores the intricacies of CIP brewing technology and how it can be leveraged to enhance operational efficiency in breweries.
What is CIP Brewing Technology?
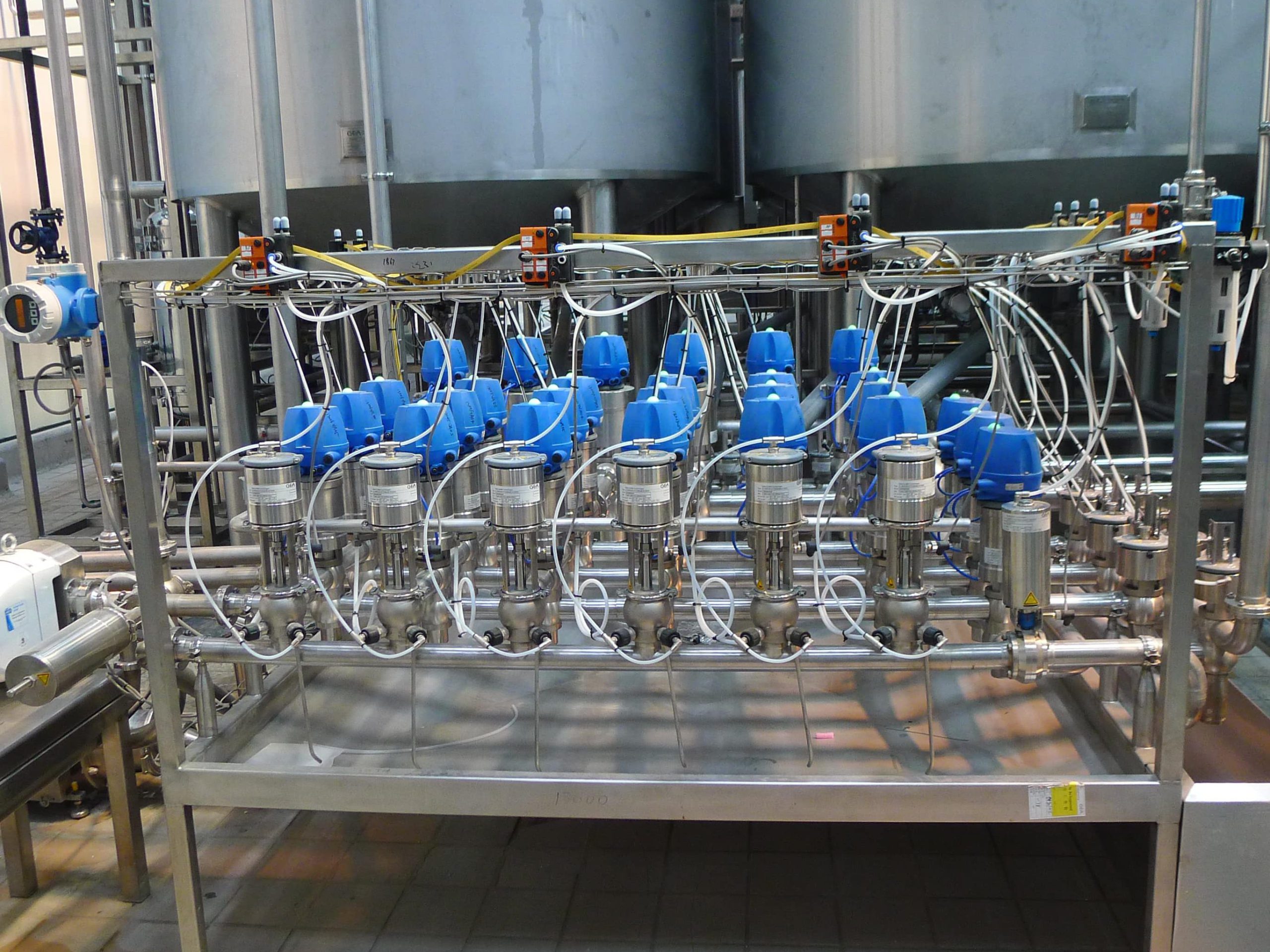
CIP, or Clean-In-Place, brewing technology refers to a system used within brewing setups to clean the interior surfaces of tanks and pipes without the need to dismantle the entire apparatus. This method not only saves valuable time but also reduces the risk of contamination, which can compromise the quality of the brew. By using a combination of water, chemicals, and heat circulated through the system, breweries can maintain a sterile environment that is crucial for the production of high-quality beer.
Key Components of a CIP System
- Tanks: Used to mix cleaning chemicals with water.
- Pumps: Propel the cleaning solution through the system.
- Spray Balls: Distribute the cleaning solution evenly inside tanks.
- Heat Exchangers: Heat the solution to the required temperature.
- Control System: Automates the cleaning cycles and monitors performance.
Benefits of Implementing CIP Brewing Technology
The implementation of CIP technology in brewing operations offers several benefits:
- Consistency and Quality: Ensures every batch of beer is produced in a clean environment.
- Efficiency: Reduces cleaning time and increases production capacity.
- Safety: Minimizes the need for manual cleaning, reducing worker exposure to harmful chemicals.
- Sustainability: Decreases water usage and chemical waste.
How to Integrate CIP Systems into Your Brewery
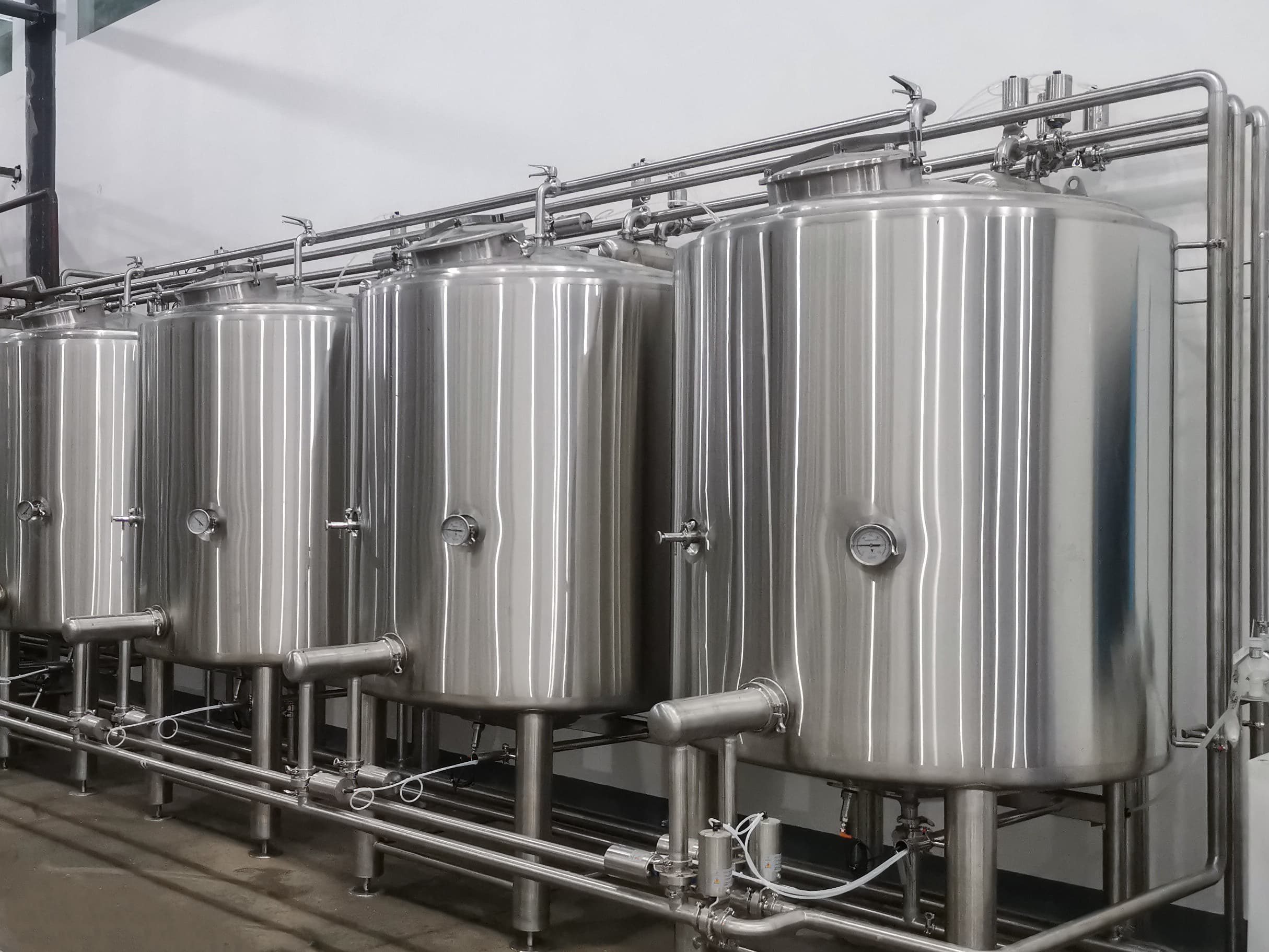
Step-by-Step Guide
- Assessment: Evaluate your current cleaning processes and identify potential integration points.
- Design: Work with a CIP system provider to design a system tailored to your specific needs.
- Installation: Install the system with professional help to ensure it operates correctly.
- Training: Educate your staff on how to use the system effectively.
- Maintenance: Set up regular maintenance checks to keep the system running smoothly.
Table: Comparison of Traditional vs. CIP Cleaning Methods
Factor | Traditional Cleaning | CIP Brewing Technology |
---|---|---|
Time | 3-4 hours | 1-2 hours |
Water Usage | 500 gallons | 300 gallons |
Chemical Usage | 15 gallons | 10 gallons |
Labor Intensity | High | Low |
Safety | Moderate Risk | High Safety |
Optimizing Your CIP Process
Best Practices
- Chemical Selection: Choose the right chemicals for your specific brewing materials.
- Temperature Control: Maintain optimal temperatures to maximize cleaning efficiency.
- Regular Audits: Regularly review and optimize your cleaning processes.
- Upgrades: Stay updated with the latest advancements in CIP technology.
Conclusion
CIP brewing technology represents a revolutionary step in brewery management, significantly enhancing efficiency and safety while maintaining the highest quality standards. By understanding and implementing CIP systems effectively, breweries can not only optimize their production processes but also gain a competitive edge in the market. Embracing this technology will be a pivotal move for any brewery looking to improve its operations and output.
Adopting CIP systems is a testament to a brewery’s commitment to quality and efficiency. As the industry evolves, staying ahead of technological advancements like CIP will be essential for success.
FAQ
What is the ideal concentration of chemicals for CIP systems?
The concentration depends on the type of chemicals and the materials being cleaned. Typically, a 1-3% solution is effective for most brewery applications.
How often should CIP systems be maintained?
CIP systems should be inspected and maintained at least once every six months to ensure optimal performance.
Can CIP systems clean all parts of a brewery?
While CIP systems are highly effective, some areas may still require manual cleaning or specialized equipment.
Are there any downsides to using CIP technology?
Initial setup costs can be high, and improper use can lead to incomplete cleaning. Training and adherence to protocols are crucial.