Introduction
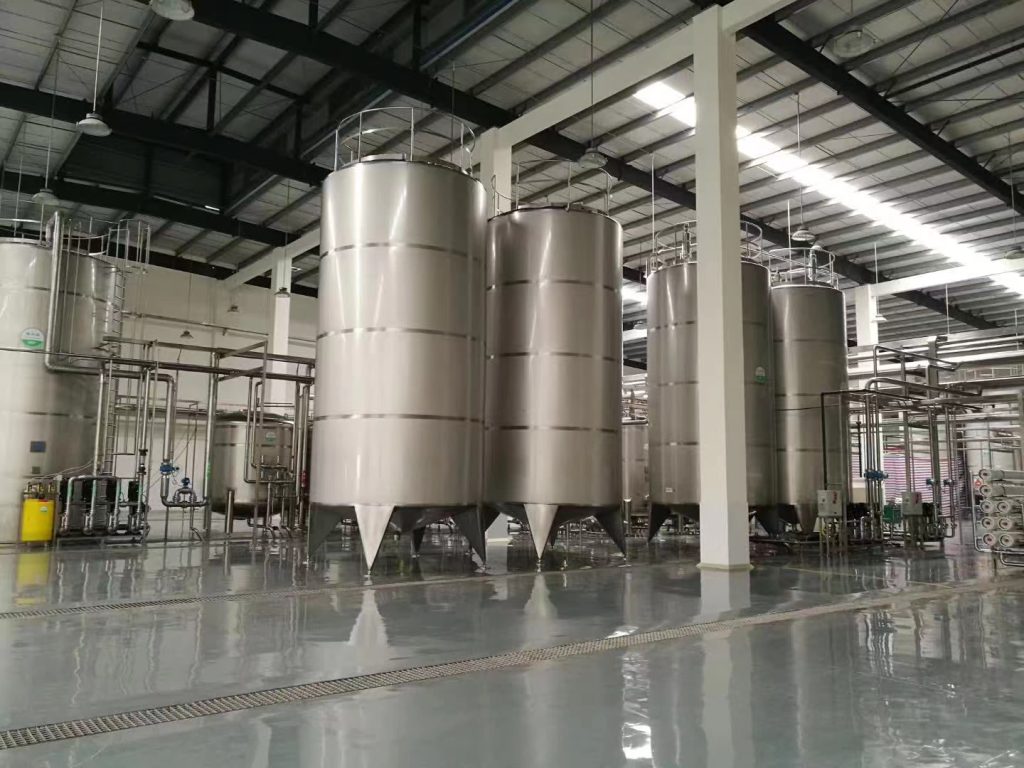
In the dairy industry, maintaining high standards for milk quality and safety is critical. A key component in achieving this is the use of cooling tanks. These tanks play a crucial role in managing cooling tank milk, ensuring that it remains fresh and safe from the moment it is collected until it reaches consumers. In this blog, we will explore the significance of cooling tanks, their impact on dairy quality, and best practices for their use.
What is a Cooling Tank?
A cooling tank is a specialized container used to cool and store milk. The primary purpose of a cooling tank is to rapidly reduce the temperature of the milk after milking, which helps prevent bacterial growth and spoilage. Effective cooling of cooling tank milk is essential for preserving its freshness and safety. These tanks are designed to handle large volumes of milk and maintain it at a consistent, ideal temperature.
How Cooling Tanks Enhance Dairy Quality
Temperature Control
Cooling tanks are designed to lower the temperature of cooling tank milk to approximately 4°C (39°F) quickly. This rapid cooling is crucial for inhibiting bacterial growth and maintaining the quality of the milk. By keeping cooling tank milk at a stable, low temperature, these tanks help preserve the milk’s nutritional value and taste.
Extended Shelf Life
One of the significant benefits of using cooling tanks is the extended shelf life they provide. By maintaining a low temperature, cooling tanks help keep cooling tank milk fresh for longer periods. This is particularly important for dairy producers and processors who need to transport milk over long distances or store it for extended durations. The extended shelf life also reduces waste and ensures that consumers receive high-quality milk.
Quality Assurance
Modern cooling tanks come equipped with various monitoring and control systems to ensure optimal performance. These systems often include temperature sensors, automatic alarms, and data logging features. Continuous monitoring of cooling tank milk helps maintain high standards of quality and safety by promptly addressing any deviations from the desired temperature range.
Types of Cooling Tanks
Vertical Cooling Tanks
Vertical cooling tanks are commonly used in smaller dairy operations. These tanks store cooling tank milk in an upright cylindrical shape. The vertical design allows for efficient cooling in spaces with limited room, making them suitable for smaller-scale operations.
Horizontal Cooling Tanks
Horizontal cooling tanks are designed to lie flat and are often used in larger dairy operations. These tanks have a greater capacity for cooling tank milk and are more suitable for high-volume storage. The horizontal design provides a larger surface area for cooling, which enhances efficiency.
Plate Coolers
Plate coolers are a type of cooling system that uses a series of plates to transfer heat from cooling tank milk to a cooling medium. They are highly efficient and are often used in conjunction with cooling tanks to achieve rapid cooling. Plate coolers are particularly effective for large volumes of cooling tank milk and can significantly improve the overall cooling process.
Best Practices for Managing Cooling Tank Milk
Regular Cleaning and Sanitization
To maintain the quality of cooling tank milk, it is essential to regularly clean and sanitize the cooling tanks. Proper cleaning procedures help prevent contamination and ensure that the equipment remains in good condition. Dairy producers should follow a strict cleaning schedule and use appropriate cleaning agents to maintain the integrity of cooling tank milk.
Temperature Monitoring
Accurate temperature monitoring is crucial for effective cooling of cooling tank milk. Regularly checking temperature readings ensures that the milk is kept at the optimal temperature, preventing spoilage and maintaining quality. Any deviations from the ideal temperature should be addressed immediately to ensure the safety and freshness of cooling tank milk.
Preventive Maintenance
Routine maintenance checks are essential for keeping cooling tank milk systems in good working condition. Regular inspections of cooling components, refrigerant levels, and other critical parts help identify potential issues before they become major problems. Preventive maintenance ensures that cooling tanks operate efficiently and reliably, preserving the quality of cooling tank milk.
Cooling Tank Maintenance Checklist
Task | Frequency | Notes |
---|---|---|
Check temperature settings | Daily | Ensure temperature is consistent and within range |
Clean the tank | After each milking session | Use appropriate cleaning agents and techniques |
Inspect cooling components | Monthly | Look for wear and tear, and replace parts as needed |
Monitor refrigerant levels | Quarterly | Ensure refrigerant is at the correct level for efficient operation |
Test alarm systems | Monthly | Verify alarms and sensors are functioning correctly |
Future Trends in Cooling Tank Milk Technology
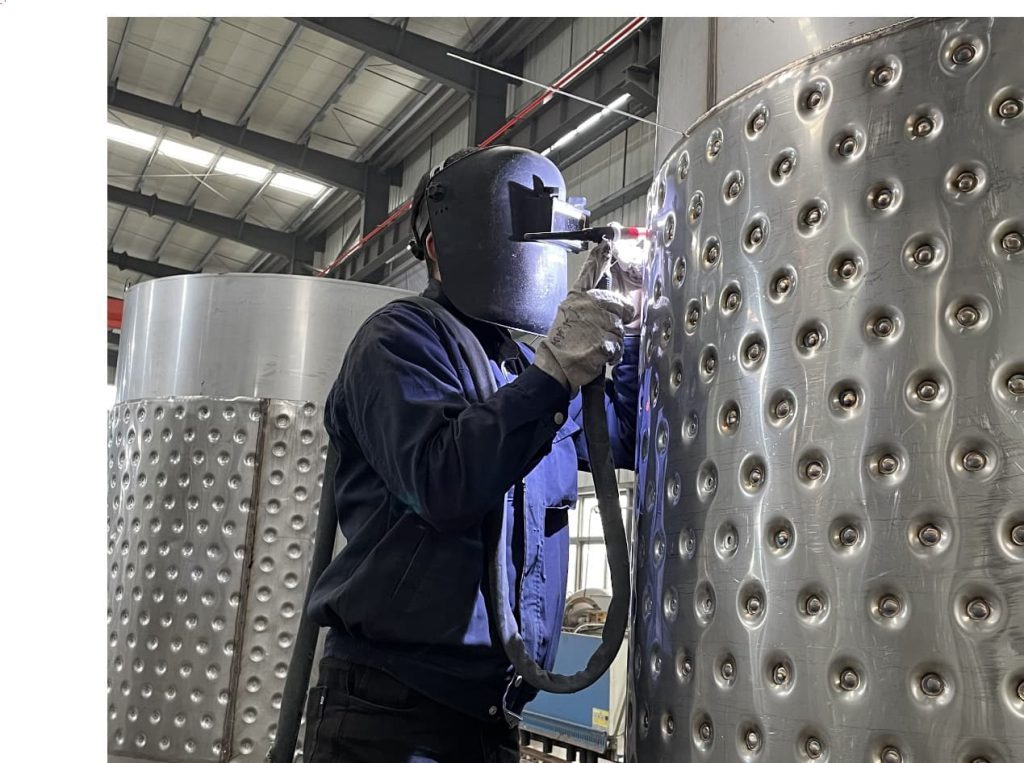
Technological Innovations
The future of cooling tank milk technology is likely to be shaped by advancements in smart cooling systems. These systems use Internet of Things (IoT) technology for real-time monitoring and data analysis. By providing detailed insights into cooling performance, smart cooling systems can optimize the efficiency of cooling tank milk processes and enhance overall operations.
Sustainable Practices
Sustainability is becoming increasingly important in dairy production. Future cooling tank milk systems may incorporate energy-efficient technologies and environmentally friendly refrigerants. These advancements will help reduce energy consumption and minimize the environmental impact of dairy operations, contributing to more sustainable practices in the industry.
Conclusion
Cooling tanks play a vital role in the dairy industry, ensuring that cooling tank milk remains fresh, safe, and of high quality. By effectively managing temperature and extending shelf life, cooling tanks help maintain the nutritional value and taste of milk. Adhering to best practices for maintenance and cleaning, and staying abreast of technological advancements, will further enhance the quality and safety of cooling tank milk. As the dairy industry continues to evolve, the integration of advanced technologies and sustainable practices will play a crucial role in shaping the future of cooling tank milk systems.
FAQ
What is the ideal temperature for storing milk in a cooling tank?
The ideal temperature for storing cooling tank milk is around 4°C (39°F). This temperature helps preserve the milk’s freshness and prevent bacterial growth.
How often should cooling tanks be cleaned?
Cooling tanks should be cleaned regularly, typically after each milking session. Consistent cleaning practices help prevent contamination and ensure the quality of cooling tank milk.
Can cooling tanks be used for other dairy products?
Yes, cooling tanks can be used for various dairy products besides milk, such as cream and yogurt. However, the cooling requirements may vary depending on the product.
What are the signs that a cooling tank needs maintenance?
Signs that a cooling tank needs maintenance include inconsistent temperature readings, unusual noises, or leaks. Regular inspection and monitoring can help identify and address these issues early.
How do plate coolers work in conjunction with cooling tanks?
Plate coolers use a series of plates to transfer heat from cooling tank milk to a cooling medium, achieving rapid cooling. They are often used alongside cooling tanks to enhance the efficiency of the cooling process and ensure that cooling tank milk reaches the desired temperature quickly.