Introduction
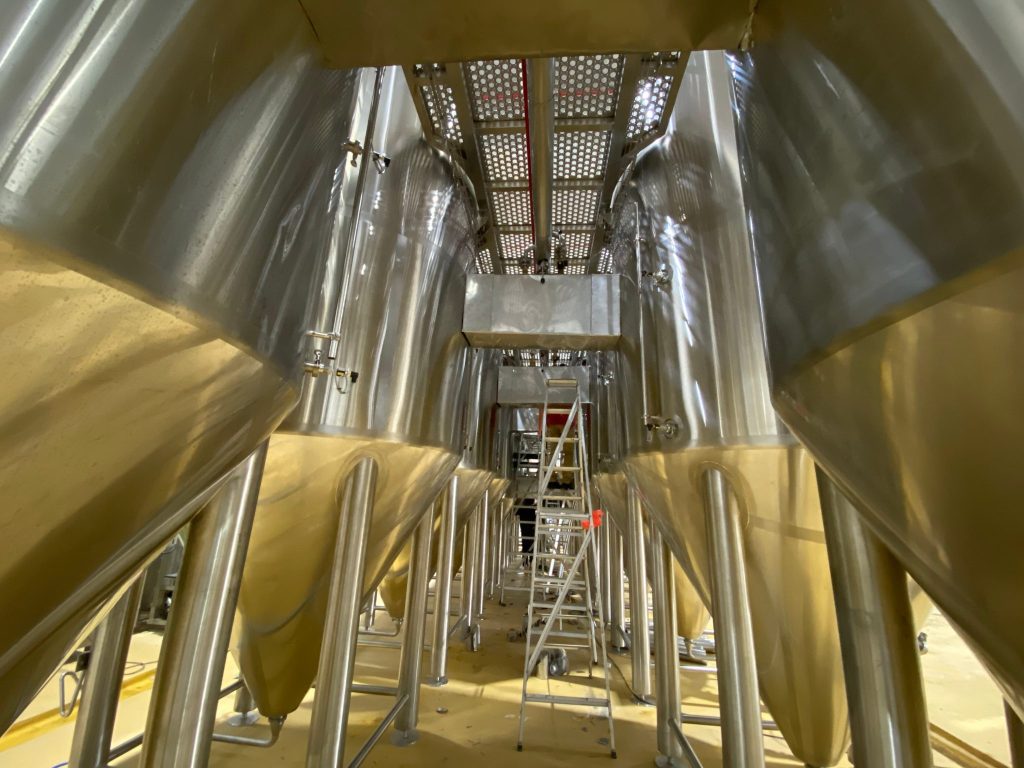
In the dynamic world of beverage manufacturing, consistency and quality are paramount. Whether you’re producing refreshing juices, fizzy sodas, or complex cocktails, the beverage mixing tank stands as a cornerstone of your operation. This seemingly simple piece of equipment plays a crucial role in ensuring that every batch of your product meets the high standards your customers expect. A well-mixed beverage is essential for delivering the desired taste, texture, and appearance. In this comprehensive guide, we’ll delve into the myriad benefits of using a beverage mixing tank, exploring how it can revolutionize your production process.
What is a Beverage Mixing Tank?
A beverage mixing tank is a specialized vessel designed to blend various liquids and ingredients in the production of beverages. These tanks come in a variety of sizes and configurations, tailored to meet the specific needs of different beverage manufacturers. They are typically constructed from stainless steel to ensure hygiene and durability, and they often incorporate features like agitators, temperature control systems, and level indicators to optimize the mixing process. These tanks are engineered to handle a range of viscosities and ingredient types, from thin liquids to thicker mixtures containing solids. Understanding the different types of mixing tanks available is crucial for selecting the right equipment for your production needs.
The Key Benefits of Using a Beverage Mixing Tank
Consistent Product Quality
One of the most significant advantages of using a beverage mixing tank is the ability to achieve consistent product quality. The tank’s design and features ensure that all ingredients are thoroughly mixed, resulting in a uniform flavor, color, and texture in every batch. This consistency is essential for maintaining customer satisfaction and brand loyalty. By controlling the mixing process, you can minimize variations and ensure that each product tastes exactly as intended. This level of control is particularly important for brands that rely on a signature flavor profile.
Increased Production Efficiency
Beverage mixing tanks can significantly enhance your production efficiency. With their ability to handle large volumes of liquids and automate the mixing process, these tanks can reduce the time and labor required to produce your beverages. This increased efficiency can lead to higher output, lower costs, and improved profitability. Automated mixing also frees up personnel to focus on other critical tasks in the production line. Furthermore, optimized mixing can reduce waste by ensuring that ingredients are used effectively.
Enhanced Flexibility
Beverage mixing tanks offer a high degree of flexibility in beverage production. They can be used to mix a wide variety of ingredients, from simple combinations of water and flavorings to more complex blends of juices, concentrates, and additives. This versatility makes them suitable for producing a diverse range of beverages, catering to different market demands. This adaptability allows manufacturers to quickly respond to changing consumer preferences and introduce new products with minimal downtime. Whether you’re creating a new flavor or adjusting an existing recipe, a beverage mixing tank provides the flexibility you need.
Improved Hygiene and Safety
Hygiene and safety are critical considerations in beverage manufacturing. Beverage mixing tanks are typically made from stainless steel, a material that is easy to clean and sanitize. This helps to prevent contamination and ensures that your beverages are safe for consumption. Additionally, many tanks are equipped with features like sealed lids and CIP (Clean-in-Place) systems to further enhance hygiene and safety. These features minimize the risk of bacterial growth and ensure that the tanks meet stringent sanitary standards. Proper sanitation procedures are essential for maintaining product quality and protecting public health.
Cost Savings
Investing in a beverage mixing tank can lead to significant cost savings in the long run. By increasing production efficiency, reducing labor costs, and minimizing waste, these tanks can help you optimize your operations and improve your bottom line. Additionally, the durability of stainless steel tanks means that they can last for many years with proper maintenance, providing a solid return on your investment. Reduced labor costs and minimized waste contribute to a quicker return on investment. The long lifespan of the equipment further enhances its cost-effectiveness.
Precise Control and Monitoring
Modern beverage mixing tanks are often equipped with advanced control and monitoring systems. These systems allow you to precisely control parameters like mixing speed, temperature, and time, ensuring that each batch is mixed to perfection. Additionally, they provide real-time data on the mixing process, allowing you to monitor performance and make adjustments as needed. This level of control ensures consistency and quality from batch to batch. Real-time monitoring allows for quick identification and correction of any deviations in the mixing process.
Scalability
Whether you’re a small-scale producer or a large-scale manufacturer, a beverage mixing tank can grow with your business. These tanks are available in a range of sizes, allowing you to choose the one that best suits your current needs and future expansion plans. As your production volume increases, you can easily add more tanks to your line, ensuring that you can meet growing demand. This scalability makes beverage mixing tanks a valuable asset for businesses of all sizes. Planning for future growth is essential, and choosing the right equipment now can save time and money later.
Beverage Mixing Tank Configurations
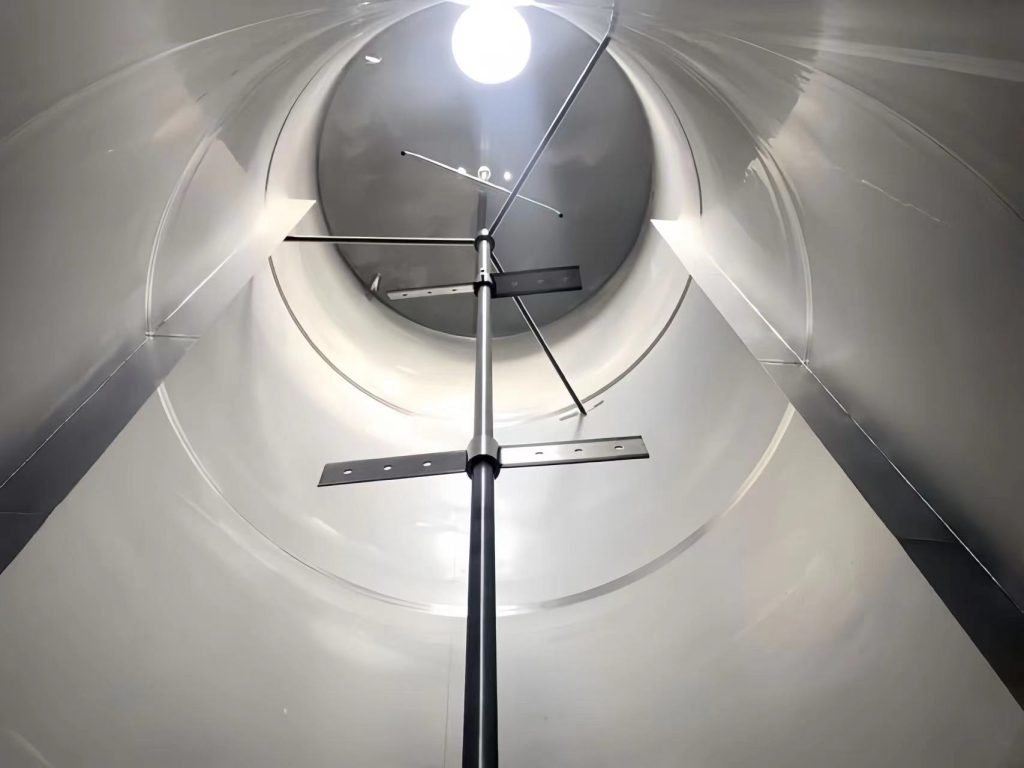
Feature | Description |
---|---|
Material | Stainless steel (typically 304 or 316) |
Capacity | Varies widely, from hundreds to thousands of gallons |
Agitation | Different types of impellers (e.g., propeller, turbine, paddle) |
Temperature Control | Jackets or coils for heating and cooling |
Control Systems | PLC-based systems for automation and monitoring |
Additional Features | Level indicators, CIP systems, load cells |
Conclusion
In the competitive beverage industry, a beverage mixing tank is more than just a piece of equipment – it’s a strategic asset. By ensuring consistent quality, increasing efficiency, and enhancing flexibility, these tanks empower beverage manufacturers to meet the demands of a dynamic market. Whether you’re a small-scale producer or a large-scale manufacturer, investing in a high-quality beverage mixing tank is a decision that can elevate your production process and drive your business forward. A well-chosen mixing tank can streamline your operations and improve your bottom line. By optimizing your mixing process, you can gain a competitive edge in the beverage market.
FAQ
Q: What is the typical lifespan of a beverage mixing tank?
A: With proper maintenance, a stainless steel beverage mixing tank can last for many years, often exceeding a decade.
Q: Can a beverage mixing tank be used for different types of beverages?
A: Yes, beverage mixing tanks are versatile and can be used to mix a wide range of beverages, including juices, sodas, dairy drinks, and alcoholic beverages.
Q: How do I choose the right size of beverage mixing tank for my needs?
A: The size of the tank will depend on your production volume, batch size, and future growth plans. It’s best to consult with a tank manufacturer or expert to determine the optimal size for your specific needs.