Introduction
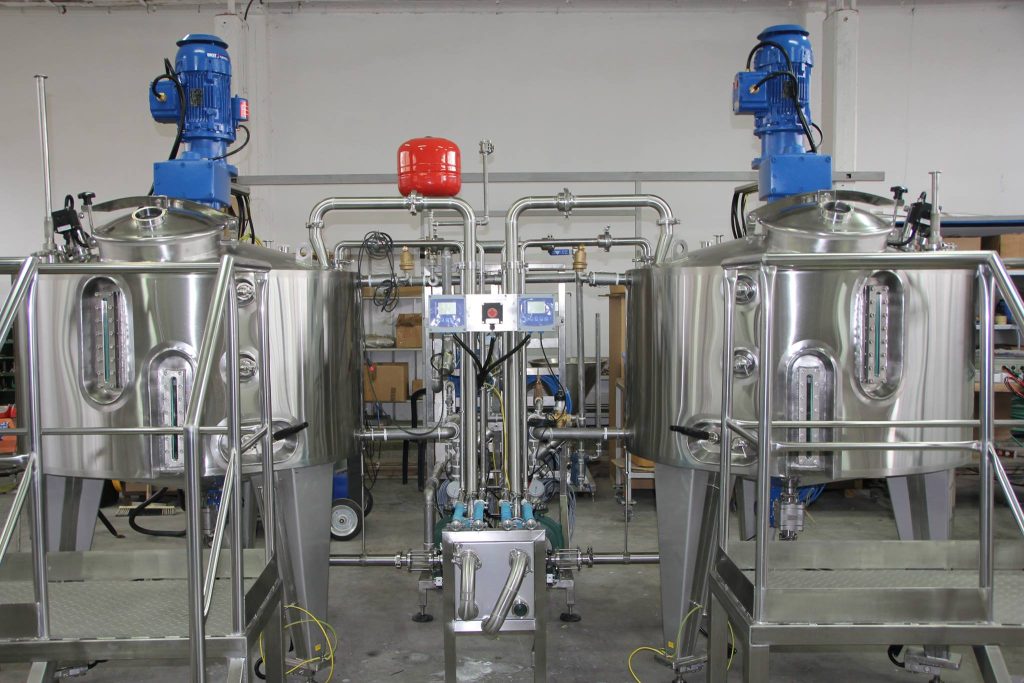
In the complex world of manufacturing, particularly in industries involving chemical production, the role of chemical tank mixers is paramount. These devices are not just accessories but critical components in ensuring that products meet stringent quality standards. This blog delves into how chemical tank mixers contribute to quality control, exploring their various functionalities, benefits, and impacts on the manufacturing process.
Understanding Chemical Tank Mixers
Chemical tank mixers are specialized equipment used to blend chemicals and other substances in industrial tanks. Their primary function is to ensure uniformity and consistency in the mixture, which is crucial for maintaining product quality. Here are some key aspects to understand about tank mixers:
- Types of Chemical Tank Mixers:
- Propeller Mixers: These are commonly used for low-viscosity fluids. They offer high shear and are effective in maintaining homogeneity.
- Hydraulic Mixers: Designed for higher viscosity fluids, hydraulic mixers ensure thorough blending by using hydraulic energy.
- Paddle Mixers: Suitable for granular materials and slurries, paddle mixers ensure consistent blending through their design.
- Operational Principles: Chemical tank mixers operate based on principles like fluid dynamics and shear force. The choice of mixer depends on the chemical properties and the desired outcome of the mixing process.
Importance of Chemical Tank Mixers in Quality Control
Quality control in manufacturing is a rigorous process that demands precision and reliability. Chemical tank mixers play a vital role in this regard:
- Uniformity of Mixtures: Ensuring that each batch of product is consistent is crucial for quality control. Chemical tank mixers provide the necessary agitation and mixing to achieve uniformity, which prevents variations in the final product.
- Prevention of Chemical Reactions: In some cases, improper mixing can lead to unwanted chemical reactions. Chemical tank mixers help in controlling the reaction conditions, thus preventing potential issues in the final product.
- Regulatory Compliance: Many industries are subject to strict regulatory standards that require consistent product quality. Tank mixers help manufacturers meet these standards by ensuring uniform blending of ingredients.
Factors Affecting the Efficiency of Chemical Tank Mixers
The efficiency of a chemical tank mixer can significantly impact the quality of the final product. Several factors influence this efficiency:
- Mixer Design and Type: The design and type of mixer used can affect how well the chemicals are blended. For instance, a poorly designed mixer may leave unmixed pockets in the tank.
- Mixing Speed and Duration: The speed at which the mixer operates and the duration of mixing are crucial for achieving the desired consistency. Too fast or too slow mixing can affect the product quality.
- Tank Shape and Size: The shape and size of the tank where mixing occurs can influence the mixer’s performance. An appropriately sized mixer for the tank ensures effective blending.
Table: Comparison of Chemical Tank Mixer Types
Mixer Type | Ideal For | Key Features | Pros | Cons |
---|---|---|---|---|
Propeller Mixer | Low-viscosity fluids | High shear, simple design | Efficient for low-viscosity fluids | Not suitable for high viscosity |
Hydraulic Mixer | High-viscosity fluids | Uses hydraulic energy | Effective for thick fluids | Complex design, higher cost |
Paddle Mixer | Granular materials, slurries | Blades with paddles | Consistent blending of solids | Not ideal for low-viscosity fluids |
Maintenance and Troubleshooting of Chemical Tank Mixers
Regular maintenance and troubleshooting are essential for ensuring the optimal performance of chemical tank mixers:
- Routine Maintenance:
- Inspection: Regularly check for wear and tear on mixer components.
- Cleaning: Ensure that mixers are cleaned thoroughly to prevent contamination.
- Troubleshooting Common Issues:
- Uneven Mixing: Check for issues with mixer speed or design.
- Noise or Vibration: Inspect the mixer for mechanical issues or misalignment.
Case Studies: Successful Applications of Chemical Tank Mixers
To illustrate the impact of chemical tank mixers on quality control, let’s explore a few case studies:
- Case Study: Pharmaceutical Industry
- Challenge: Achieving precise drug formulation.
- Solution: Implementation of high-shear mixers to ensure uniform mixing of active ingredients.
- Outcome: Consistent product quality and adherence to regulatory standards.
- Case Study: Food and Beverage Industry
- Challenge: Blending of viscous sauces.
- Solution: Use of paddle mixers for thorough blending of ingredients.
- Outcome: Enhanced product consistency and taste quality.
Future Trends in Chemical Tank Mixing Technology
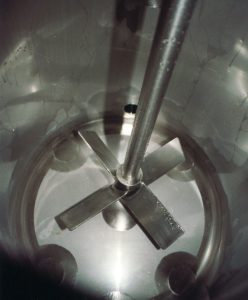
The field of chemical tank mixing is continually evolving. Some emerging trends include:
- Integration of IoT: Smart mixers equipped with IoT sensors provide real-time monitoring and adjustments.
- Energy Efficiency: Advances in mixer design aim to reduce energy consumption while maintaining performance.
- Advanced Materials: Use of new materials in mixer construction for improved durability and performance.
Conclusion
Chemical tank mixers are indispensable in maintaining the quality control standards required in modern manufacturing. By ensuring uniform mixing, preventing unwanted chemical reactions, and aiding regulatory compliance, these mixers play a critical role in the production process. As technology continues to advance, the capabilities of chemical tank mixers will likely evolve, further enhancing their role in quality control.
FAQ
Q:What is the primary function of a chemical tank mixer?
A:The primary function of a chemical tank mixer is to blend chemicals and other substances to achieve a uniform mixture.
Q:How does the type of mixer affect the quality of the final product?
A:Different types of mixers are suited for various viscosities and types of substances. The choice of mixer impacts the consistency and quality of the final product.
Q:What are common issues with chemical tank mixers and how can they be resolved?
A:Common issues include uneven mixing and mechanical failures. Regular maintenance and proper troubleshooting can address these issues.
Q:How can I determine the right mixer for my application?
A:Consider factors such as the viscosity of the fluids, the required mixing speed, and the size of the tank. Consulting with a specialist can also help in selecting the appropriate mixer.
Q:What are the benefits of incorporating advanced technologies in chemical tank mixers?
A:Advanced technologies like IoT integration and energy-efficient designs offer improved performance, real-time monitoring, and reduced operational costs.