Introduction

Steam condensers play a crucial role in various industrial processes, particularly in power generation. They are integral components of steam power plants, responsible for converting exhaust steam from turbines back into water for reuse. The efficiency and design of steam condensers significantly impact the overall performance of power plants. In this blog post, we delve into the science behind steam condenser design, exploring key principles, considerations, and advancements in this critical engineering aspect.
Understanding Steam Condensers
Steam condensers are devices used to condense exhaust steam from turbines into liquid water by transferring heat to a coolant medium, typically cooling water. This condensation process allows for the efficient reuse of steam in power generation cycles. Several types of steam condensers exist, including surface condensers and direct contact condensers, each with its unique advantages and applications.
Principles of Steam Condensation
The process of steam condensation is fundamental to various industrial applications, particularly in power generation. Understanding the principles governing this phenomenon is crucial for optimizing the design and performance of steam condensers.
At its core, steam condensation involves the transformation of gaseous steam into liquid water upon contact with a cooler surface. This transformation occurs due to the transfer of thermal energy from the steam to the surface, leading to a decrease in temperature and a phase change from gas to liquid. Several key principles govern this heat transfer process:
- Temperature Gradient: The efficiency of steam condensation is greatly influenced by the temperature difference between the steam and the cooling medium. A larger temperature gradient results in faster heat transfer and more efficient condensation. Therefore, maintaining a significant temperature differential between the steam and the condenser surface is essential for optimal performance.
- Surface Area for Condensation: The surface area available for steam condensation directly impacts the rate at which heat is transferred from the steam to the cooling medium. Increasing the surface area of the condenser enhances the efficiency of the condensation process by allowing more steam molecules to come into contact with the cooler surface simultaneously. This is typically achieved through the use of finned tubes, extended surfaces, or compact heat exchanger designs.
- Flow Characteristics: The flow of both the steam and the cooling medium within the condenser significantly influences heat transfer efficiency. Turbulent flow regimes promote better mixing and increased heat transfer rates compared to laminar flow. Optimizing the flow patterns and velocities within the condenser can help maximize heat transfer and minimize thermal gradients, thereby improving overall performance.
- Heat Transfer Coefficients: The rate of heat transfer between the steam and the condenser surface is quantified by the heat transfer coefficient. This coefficient depends on factors such as the properties of the fluid (steam and coolant), the geometry of the condenser, and the flow conditions. Increasing the heat transfer coefficient through design modifications or enhancements can lead to higher condensation rates and improved efficiency.
- Surface Properties: The material composition and surface characteristics of the condenser influence its ability to facilitate efficient steam condensation. Materials with high thermal conductivity and corrosion resistance are preferred for condenser construction to ensure optimal heat transfer and longevity. Additionally, surface treatments or coatings may be applied to enhance heat transfer properties and mitigate fouling or scaling issues.
Design Considerations
Designing an efficient steam condenser involves optimizing several parameters to maximize heat transfer while minimizing energy losses and operational costs. Factors such as condenser size, tube layout, cooling water flow rate, and material selection are crucial considerations in achieving optimal performance. Additionally, factors like fouling, corrosion, and environmental conditions must be taken into account to ensure long-term reliability and efficiency.
Advancements in Steam Condenser Technology
Advancements in materials science, computational modeling, and manufacturing techniques have led to significant improvements in steam condenser design and performance. Enhanced surface coatings, improved tube geometries, and advanced monitoring systems have enabled engineers to develop more efficient and durable condenser solutions. Additionally, innovations in computational fluid dynamics (CFD) allow for more accurate simulations and optimization of condenser designs.
Case Studies and Performance Analysis
Analyzing real-world performance data and case studies provides valuable insights into the effectiveness of different steam condenser designs and configurations. By evaluating factors such as heat transfer efficiency, pressure drop, and energy consumption, engineers can identify areas for improvement and optimize condenser performance to meet specific operational requirements.
Key components and functions of a condenser:
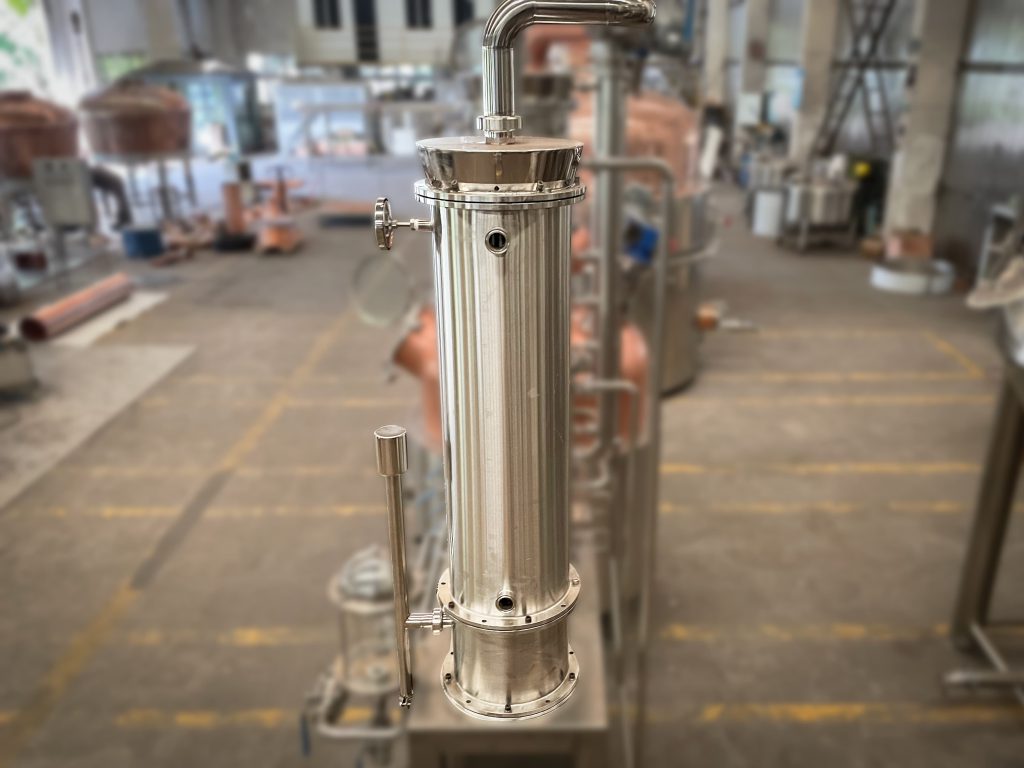
Before delving deeper into the intricacies of steam condenser design, let’s take a moment to overview the key components and functions of a typical surface condenser.
Component | Function |
---|---|
Condenser Shell | Enclosure for the condensation process |
Tube Bundle | Contains tubes through which steam flows for condensation |
Cooling Water Inlet | Inlet for the cooling water |
Cooling Water Outlet | Outlet for the cooling water |
Steam Inlet | Inlet for the exhaust steam from turbines |
Steam Outlet | Outlet for the condensed liquid water |
Air Removal System | Removes non-condensable gases from the condenser |
Vacuum System | Maintains a vacuum within the condenser to enhance condensation |
Drain System | Drains condensed water and prevents accumulation |
Conclusion
In conclusion, the design of steam condensers plays a critical role in the efficiency and reliability of steam power plants and industrial processes. By understanding the underlying principles of steam condensation and considering various design parameters, engineers can develop optimized condenser solutions that enhance energy efficiency, reduce operational costs, and minimize environmental impact. Continued research and innovation in steam condenser technology will further drive improvements in power generation and industrial applications.
FAQ
Q:What is the purpose of a steam condenser?
A:A steam condenser is used to convert exhaust steam from turbines into liquid water for reuse in power generation cycles.
Q:What are the types of steam condensers?
A:There are two primary types of steam condensers: surface condensers and direct contact condensers, each with its unique design and applications.
Q:How does a steam condenser work?
A:Steam condensation occurs as steam comes into contact with a cooler surface, transferring heat and transforming into liquid water.
Q:What factors affect steam condenser performance?
A:Factors such as condenser size, tube layout, cooling water flow rate, and material selection impact the efficiency and effectiveness of steam condensers.
Q:What advancements have been made in steam condenser technology?
A:Advancements in materials science, computational modeling, and manufacturing techniques have led to improved efficiency and durability in steam condenser design.
Q:Why is steam condenser design important?
A:Efficient steam condenser design is crucial for maximizing energy efficiency, reducing operational costs, and minimizing environmental impact in power generation and industrial processes.