Introduction
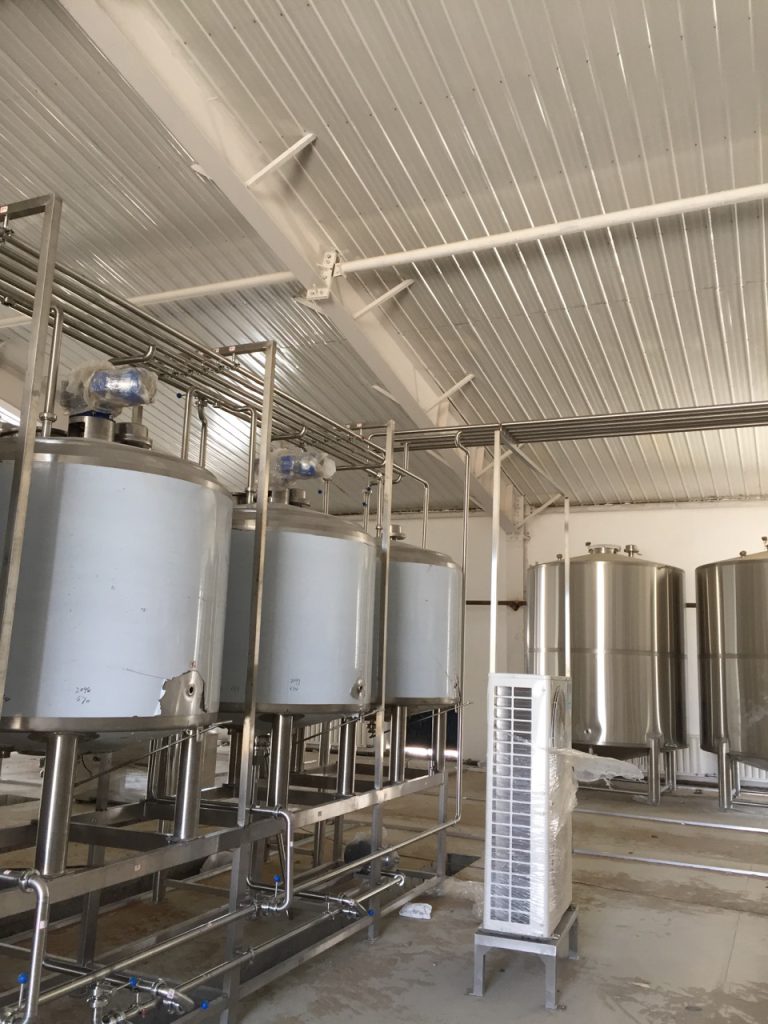
In the dairy industry, the proper cooling of milk tanks is essential for maintaining milk quality and ensuring the safety of dairy products. This blog explores the critical role of cooling milk tanks, the technologies involved, and their impact on dairy operations.
Importance of Cooling Milk Tanks
Preservation of Milk Quality
Cooling milk tanks immediately after milking is crucial to preserve the freshness and nutritional integrity of milk. Rapid cooling inhibits bacterial growth, including pathogens like Listeria and Salmonella, which thrive in warmer environments. By maintaining temperatures around 4°C (39°F), cooling milk tanks effectively prolong the shelf life of milk and maintain its nutritional value.
Ensuring Food Safety
Effective cooling of milk tanks is paramount for preventing microbial contamination and ensuring the safety of dairy products. By reducing the temperature promptly after milking, dairy farms mitigate the risk of spoilage and foodborne illnesses. This step not only meets regulatory standards but also maintains consumer confidence in the quality and safety of dairy products.
Optimization of Dairy Production
Efficient cooling systems optimize dairy production by maintaining consistent temperatures in milk tanks. This stability ensures that milk quality remains high throughout processing, minimizing waste and maximizing product yield. By integrating advanced cooling technologies, dairy farms can enhance operational efficiency and meet the demands of a competitive market.
Technologies for Cooling Milk Tanks
Direct Expansion (DX) Systems
Direct expansion systems are widely used for cooling milk tanks due to their efficiency and reliability. These systems employ refrigerants to cool milk directly, swiftly lowering its temperature to optimal levels. DX systems are favored in large-scale dairy operations for their capacity to handle high volumes of milk effectively.
Ice Bank Cooling Systems
Ice bank cooling systems utilize stored ice to indirectly cool milk. Water is frozen during off-peak hours and used later to maintain milk tank temperatures. This method is energy-efficient and suitable for dairy farms seeking to manage electricity costs and peak demand effectively. Ice bank systems also provide a buffer against power fluctuations, ensuring continuous cooling without compromising milk quality.
Plate Heat Exchangers
Plate heat exchangers facilitate heat transfer between milk and a cooling medium (water or glycol) through interconnected plates. These compact devices offer precise temperature control and energy efficiency, making them ideal for smaller dairy operations or those requiring flexible cooling solutions.
Case Studies: Effective Implementation
Case Study: Large-Scale Dairy Facility
At a large-scale dairy facility processing 100,000 liters of milk daily, the adoption of direct expansion cooling systems significantly improved milk quality and safety. By consistently maintaining low temperatures in milk tanks, the facility enhanced product reliability and compliance with stringent regulatory requirements.
Parameter | Details |
---|---|
Facility Size | 100,000 liters/day |
Cooling System Used | Direct Expansion (DX) |
Results | Enhanced milk quality and safety |
Case Study: Small Family Farm
On a small family farm processing 1,000 liters of milk daily, an ice bank cooling system reduced energy costs and ensured reliable milk cooling. By efficiently utilizing stored ice, the system maintained consistent milk temperatures throughout the day, supporting sustainable dairy farming practices.
Parameter | Details |
---|---|
Facility Size | 1,000 liters/day |
Cooling System Used | Ice Bank System |
Results | Reduced energy costs, reliable cooling |
Challenges in Cooling Milk Tanks
Energy Consumption
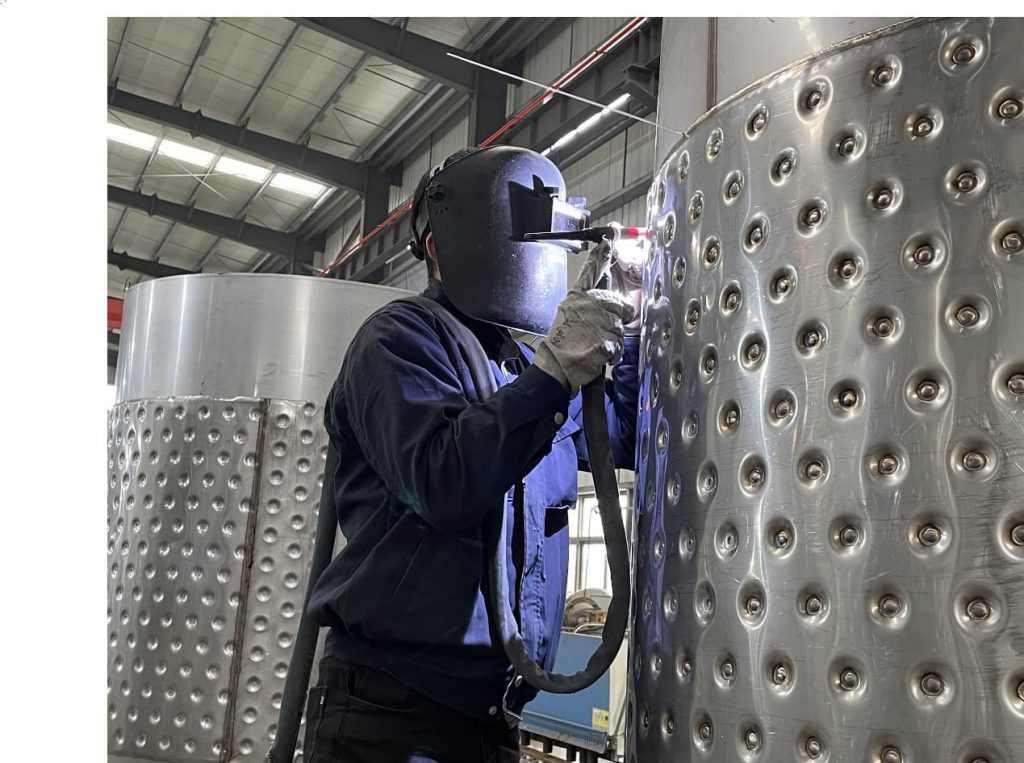
Managing energy consumption remains a significant challenge in dairy cooling operations. The refrigeration requirements for maintaining optimal milk temperatures demand substantial energy inputs, impacting overall operational costs. Dairy farms must adopt energy-efficient technologies and practices to minimize consumption while meeting cooling requirements effectively.
Temperature Fluctuations
External factors such as ambient temperature changes and power interruptions can affect the performance of cooling systems. Implementing backup systems and robust monitoring protocols helps dairy farms maintain consistent milk temperatures and mitigate risks associated with temperature fluctuations.
Conclusion
Effective cooling milk tanks is fundamental to preserving milk quality, ensuring food safety, and optimizing dairy production processes. By leveraging advanced cooling technologies such as direct expansion systems, ice bank cooling systems, and plate heat exchangers, dairy farms can enhance operational efficiency, reduce waste, and meet consumer expectations for high-quality dairy products consistently.
FAQ
Q: Why is rapid cooling important for milk?
Rapid cooling inhibits bacterial growth and preserves milk quality, extending its shelf life and ensuring safety for consumption.
Q: What are the benefits of plate heat exchangers in dairy farms?
Plate heat exchangers offer precise temperature control and energy efficiency, making them suitable for various dairy farm sizes and operational needs.
Q: How can dairy farms reduce energy consumption during milk cooling?
Implementing energy-efficient cooling systems like ice bank systems or optimizing cooling schedules can help dairy farms reduce overall energy consumption while maintaining effective milk cooling.