Introduction
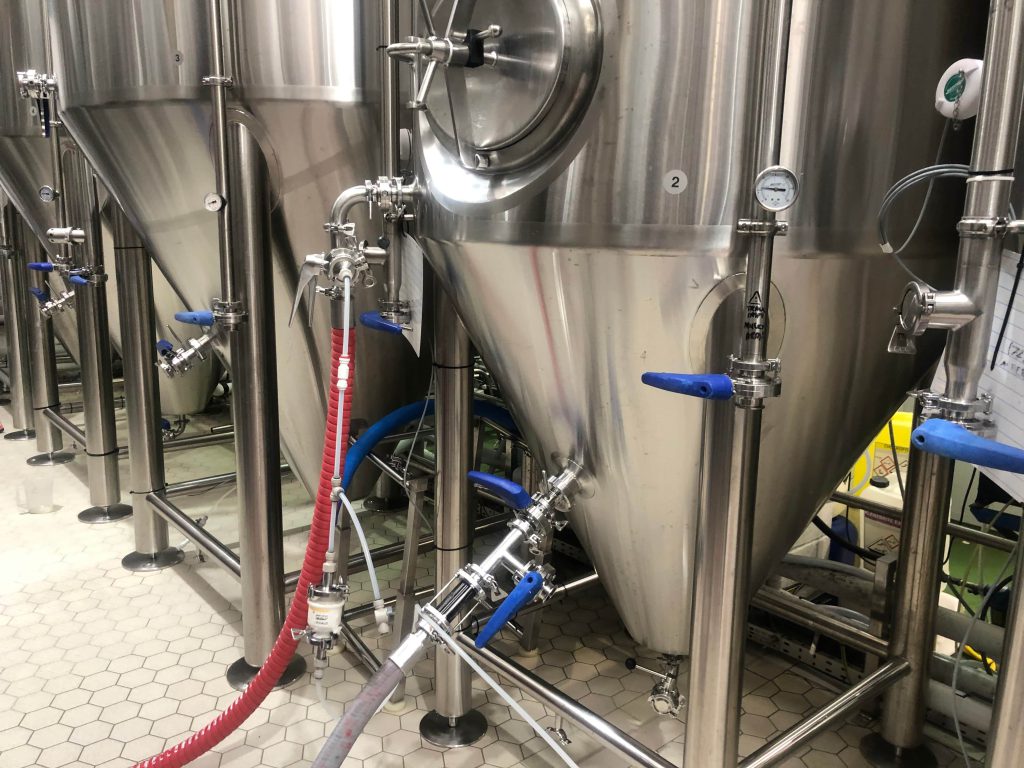
The industrial beer equipment sector is undergoing a rapid transformation, driven by technological advancements, evolving consumer preferences, and increasing demands for sustainability. In this comprehensive guide, we delve into the latest trends shaping the industry, providing insights into how breweries can optimize their operations, enhance product quality, and stay competitive in the dynamic global market. Whether you are a large-scale industrial brewer or a craft brewery looking to scale up, understanding these trends is crucial for making informed investment decisions and ensuring long-term success.
Advanced Brewing Systems for Enhanced Efficiency
Automated Mashing and Lautering Systems
Modern industrial beer equipment emphasizes automation to improve efficiency and consistency. Automated mashing and lautering systems, for instance, utilize precise temperature controls and automated processes to optimize sugar extraction and minimize manual intervention. These systems reduce labor costs, enhance product uniformity, and allow brewers to focus on other critical aspects of production. This is a very important part of industrial beer equipment.
High-Efficiency Wort Boiling and Cooling
Wort boiling and cooling are critical stages in the brewing process. Latest industrial beer equipment incorporates high-efficiency heat exchangers and advanced temperature control systems to reduce energy consumption and shorten processing times. These innovations not only lower operational costs but also contribute to a more sustainable brewing process.
Fermentation Technology and Innovations
Cylindrical Conical Fermenters with Advanced Controls
Cylindrical conical fermenters (CCVs) remain a staple in industrial breweries, but recent advancements have focused on enhancing control and monitoring capabilities. Modern CCVs are equipped with sophisticated sensors and automation systems that allow precise control of temperature, pressure, and other critical parameters. This precise control ensures optimal fermentation conditions and consistent product quality.
Accelerated Fermentation Techniques
To meet the growing demand for faster production cycles, breweries are exploring accelerated fermentation techniques. These methods involve optimizing yeast strains, temperature profiles, and other fermentation parameters to reduce fermentation times without compromising beer quality. This trend is particularly relevant for breweries looking to increase production capacity without significant capital investments.
Packaging and Filling Solutions
High-Speed Bottling and Canning Lines
Packaging efficiency is paramount in large-scale brewing operations. High-speed bottling and canning lines, equipped with advanced automation and quality control systems, ensure rapid and accurate filling, sealing, and labeling. These lines minimize downtime, reduce product waste, and enhance overall productivity. The industrial beer equipment that is used in this process is very important.
Sustainable Packaging Innovations
With increasing environmental concerns, breweries are adopting sustainable packaging solutions. This includes using recyclable materials, reducing packaging waste, and implementing eco-friendly labeling practices. Innovations in packaging technology also focus on minimizing the environmental impact of transportation and storage.
Quality Control and Monitoring Systems
Advanced Sensor Technology for Real-Time Monitoring
Real-time monitoring is essential for maintaining consistent product quality. Advanced sensor technology, including inline sensors and analytical instruments, allows breweries to monitor critical parameters such as temperature, pH, gravity, and dissolved oxygen throughout the brewing process. This real-time data enables brewers to make immediate adjustments and prevent potential quality issues.
Laboratory Equipment and Analysis Techniques
Modern breweries invest in state-of-the-art laboratory equipment and analysis techniques to ensure product quality and consistency. This includes using spectrophotometers, chromatographs, and other analytical instruments to perform detailed analyses of raw materials, wort, and finished beer. These tools help brewers identify potential issues early and maintain high standards of quality.
Energy Efficiency and Sustainability
Energy-Efficient Heating and Cooling Systems
Energy consumption is a major concern for industrial breweries. Latest industrial beer equipment incorporates energy-efficient heating and cooling systems, such as heat recovery systems and high-efficiency chillers, to reduce energy costs and minimize environmental impact. These systems help breweries achieve significant energy savings and contribute to a more sustainable operation.
Water Conservation and Treatment
Water conservation is another critical aspect of sustainable brewing. Modern breweries are implementing water-saving technologies and wastewater treatment systems to reduce water consumption and minimize environmental impact. This includes using high-efficiency cleaning systems, recycling water, and treating wastewater to meet environmental standards.
Automation and Digitalization
Integrated Control Systems and Automation Platforms
Automation and digitalization are transforming the industrial beer equipment landscape. Integrated control systems and automation platforms enable breweries to streamline operations, enhance efficiency, and improve product quality. These systems provide real-time data, automated control of brewing processes, and seamless integration with other brewery systems.
Data Analytics and Predictive Maintenance
Data analytics and predictive maintenance are becoming increasingly important in modern breweries. By collecting and analyzing data from various sensors and systems, breweries can identify potential issues early and perform proactive maintenance. This approach minimizes downtime, reduces maintenance costs, and ensures optimal equipment performance.
Table: Key Industrial Beer Equipment Components and Functions
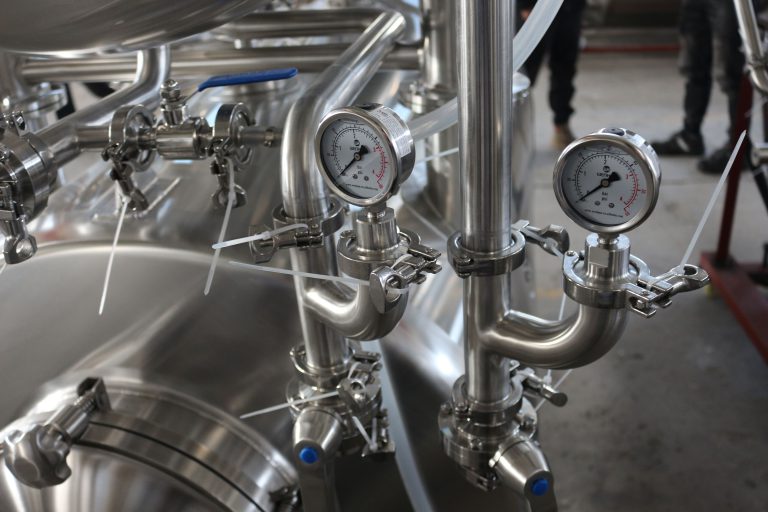
Component | Function | Key Features |
---|---|---|
Mash Tun | Converts starches into sugars | Automated temperature control, efficient mixing |
Lauter Tun | Separates wort from spent grains | Efficient filtration, optimized grain bed design |
Wort Kettle | Boils wort and adds hops | High-efficiency heating, precise temperature control |
Fermenter | Ferments wort into beer | Temperature control, pressure management, sanitary design |
Bright Beer Tank | Conditions and clarifies beer | Temperature control, CO2 management, sanitary design |
Filtration System | Removes suspended particles | High-efficiency filters, automated backflushing |
Packaging Line | Bottles or cans finished beer | High-speed filling, automated sealing, labeling |
Cleaning System | Cleans and sanitizes equipment | Automated CIP, high-pressure cleaning, sanitary design |
Control System | Manages and monitors brewing processes | Integrated sensors, automated controls, data logging |
Conclusion
The industrial beer equipment sector is continually evolving, driven by technological advancements and changing market demands. By staying informed about the latest trends and investing in modern equipment, breweries can enhance their operations, improve product quality, and achieve long-term success.
Are you ready to upgrade your brewery with the latest industrial beer equipment? Contact our team today to learn more about our comprehensive solutions and how we can help you achieve your brewing goals. We offer a wide range of high-quality equipment, expert support, and tailored solutions to meet your specific needs. Invest in the future of your brewery and elevate your brew to new heights.
FAQ
What are the key benefits of upgrading to modern industrial beer equipment?
Upgrading to modern industrial beer equipment offers numerous benefits, including improved efficiency, enhanced product quality, reduced energy consumption, and increased automation. These advancements can help breweries optimize their operations, lower costs, and stay competitive in the market.
What are the latest innovations in fermentation technology?
Latest innovations in fermentation technology include advanced cylindrical conical fermenters with precise control systems, accelerated fermentation techniques, and improved yeast management systems. These advancements allow brewers to achieve better control over the fermentation process, enhance product consistency, and reduce production times.
How can breweries ensure the longevity of their industrial beer equipment?
Breweries can ensure the longevity of their industrial beer equipment by implementing preventative maintenance programs, performing regular inspections, and using high-quality cleaning and sanitation practices. Additionally, investing in equipment from reputable manufacturers and providing proper training to staff can help extend the lifespan of the equipment.
How can breweries improve energy efficiency in their operations?
Breweries can improve energy efficiency by investing in energy-efficient heating and cooling systems, implementing heat recovery systems, and optimizing their brewing processes. Additionally, using energy-efficient lighting, insulation, and water conservation techniques can help reduce energy consumption.