Introduction
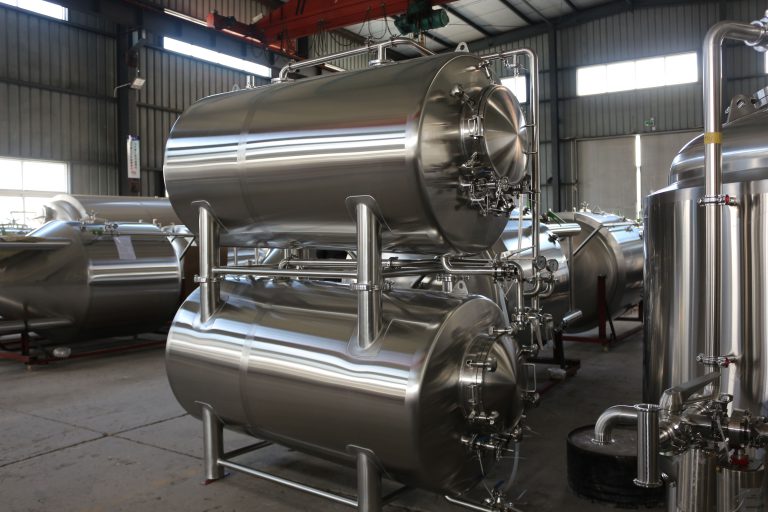
Beer production is a delicate craft, blending artistry with science. An often-overlooked aspect of this process is the selection of appropriate beer tanks. In this comprehensive guide, we delve into the science behind beer tank selection, shedding light on the crucial factors that brewers must consider to achieve optimal results.
Types of Beer Tanks
Fermentation Tanks
Fermentation is a critical stage in beer production, where yeast converts sugars into alcohol and carbon dioxide. The choice of fermentation tank significantly impacts the fermentation process and ultimately the flavor profile of the beer.
Tank Type | Material | Capacity | Features |
---|---|---|---|
Stainless Steel | Stainless Steel | Varies | Temperature Control, Sanitary Design |
Wooden | Wood | Varies | Traditional Flavor Influence, Limited Sizes |
Conical | Stainless Steel/Plastic | Varies | Yeast Collection, Sedimentation |
Conditioning Tanks
Conditioning tanks, also known as maturation tanks, play a crucial role in refining the flavor and carbonation of beer after fermentation. They allow the beer to mature, clarifying and stabilizing its flavor before packaging.
Tank Type | Material | Capacity | Features |
---|---|---|---|
Bright Tanks | Stainless Steel | Varies | Pressure Regulation, Carbonation Control |
Horizontal Tanks | Stainless Steel | Varies | Large Capacity, Efficient Cooling |
Factors Influencing Beer Tank Selection
Size and Capacity
The size and capacity of beer tanks are fundamental considerations for breweries of all sizes. Larger tanks are typically preferred by high-volume breweries due to their ability to handle larger batches, leading to increased efficiency in production. These tanks can accommodate the substantial quantities of ingredients needed for large-scale brewing operations, streamlining the process and reducing labor costs per unit of beer produced.
On the other hand, smaller tanks offer advantages for craft breweries and those producing specialty or experimental batches. They provide the flexibility to produce smaller quantities of beer, allowing brewers to experiment with new recipes or cater to niche markets without committing to large production runs. Smaller tanks also enable breweries to maintain a diverse product lineup and respond quickly to changing consumer preferences, contributing to their competitiveness in the dynamic craft beer market.
Material
Beer tanks are primarily constructed from stainless steel or wood, each material offering unique advantages and considerations.
Stainless steel is the preferred choice for the majority of modern breweries due to its exceptional durability, corrosion resistance, and ease of cleaning. Stainless steel tanks are non-reactive, ensuring that they do not impart any unwanted flavors or aromas to the beer during fermentation or conditioning. Additionally, stainless steel tanks can withstand high temperatures and pressures, making them suitable for a wide range of brewing processes, including fermentation, conditioning, and storage. Their smooth surfaces also facilitate effective cleaning and sanitation, crucial for maintaining hygiene and product quality in the brewery.
Wooden tanks, although less common in modern brewing, are still valued for their traditional craftsmanship and unique flavor contributions to certain beer styles. Wood has a porous nature that allows for slight oxygenation and micro-oxygenation during fermentation and maturation, which can influence the flavor profile of the beer, adding complexity and depth. However, wooden tanks require meticulous maintenance to prevent contamination and deterioration, and they are generally less durable and more challenging to clean compared to stainless steel tanks.
Temperature Control
Temperature control is critical throughout the brewing process to ensure optimal fermentation and conditioning conditions, which directly impact the quality and consistency of the final product. Beer tanks with efficient temperature control mechanisms help brewers maintain precise temperature levels, promoting yeast activity and flavor development while minimizing the risk of off-flavors or fermentation flaws.
Modern beer tanks often feature integrated temperature control systems, such as jacketed designs or glycol cooling jackets, which allow brewers to regulate the temperature of the fermenting or conditioning beer accurately. These systems enable precise temperature adjustments according to the specific requirements of different beer styles, ensuring that each batch achieves the desired flavor profile and quality standards.
Sanitary Design
Maintaining strict hygiene standards is essential in beer production to prevent microbial contamination and safeguard product quality. Beer tanks with sanitary designs play a crucial role in minimizing the risk of bacterial growth and contamination, ensuring that the beer remains safe for consumption and free from off-flavors or spoilage.
Sanitary tank design features include smooth, crevice-free surfaces that are easy to clean and sanitize, minimizing the potential for microbial buildup or cross-contamination. Additionally, tanks may incorporate sanitary fittings, such as tri-clamp connections and CIP (Clean-In-Place) spray balls, which facilitate thorough cleaning and sterilization procedures. Regular cleaning and sanitation protocols, combined with sanitary tank design, are integral to maintaining hygienic conditions in the brewery and producing consistently high-quality beer.
By carefully considering these factors—size and capacity, material, temperature control, and sanitary design—breweries can select beer tanks that align with their production requirements, quality standards, and brewing philosophy, ultimately contributing to the success and reputation of their beer brands.
Conclusion
Selecting the right beer tanks is a nuanced process that blends scientific principles with practical considerations. By understanding the various types of tanks available and the factors influencing their selection, brewers can optimize their brewing processes and deliver exceptional quality beer to consumers.
FAQ
Q: Can I use plastic tanks for beer fermentation?
A: Yes, plastic fermentation tanks are commonly used in homebrewing and small-scale production. However, they may not offer the same level of durability and temperature control as stainless steel tanks.
Q: How do I clean and sanitize beer tanks effectively?
A: Cleaning and sanitizing beer tanks require thorough attention to detail. Use specialized cleaning agents and follow recommended procedures to ensure proper sanitation and prevent contamination.
Q: What is the lifespan of beer tanks?
A: Stainless steel beer tanks can last for decades with proper maintenance and care. However, wooden tanks may require more frequent replacement due to wear and tear over time.
Q: Are there any environmental considerations in beer tank selection?
A: Stainless steel tanks are highly recyclable and have a lower environmental impact compared to other materials. Choosing energy-efficient tank designs can also reduce carbon emissions during the brewing process.