Introduction
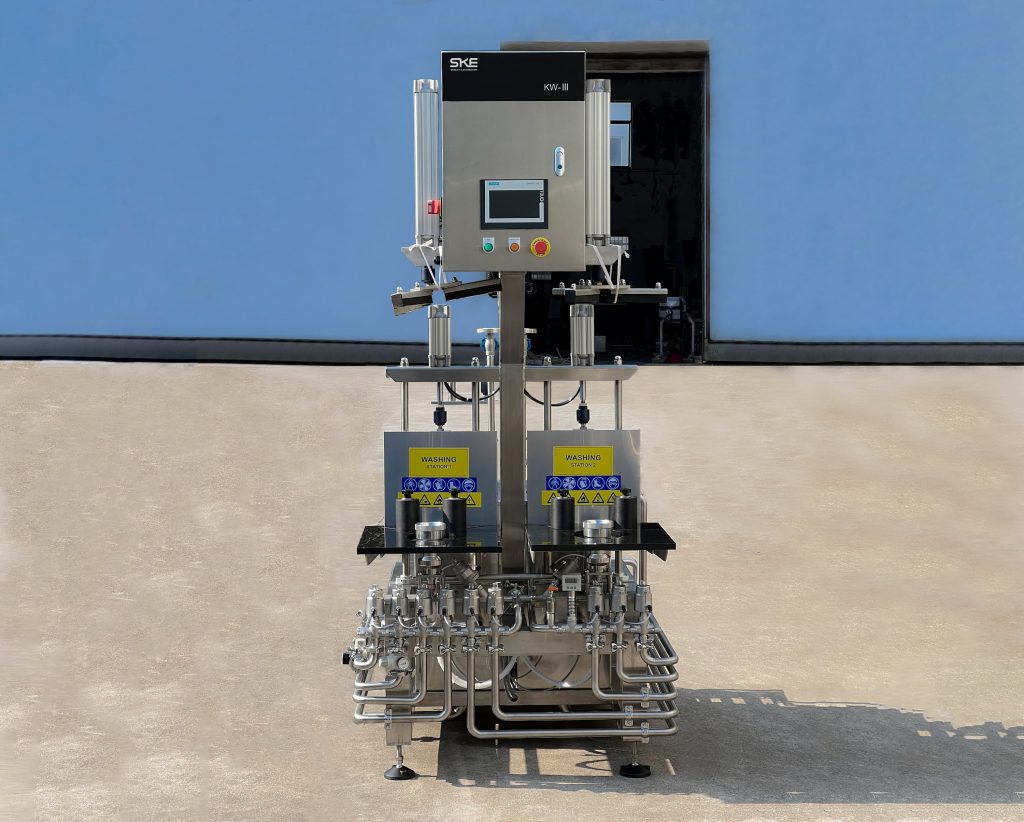
Efficiency is the lifeblood of any brewery operation, where every step in the process impacts quality, throughput, and ultimately, profitability. One critical area often overlooked is keg filler efficiency. This blog delves into why optimizing this aspect of brewery operations is crucial for success.
What is a Keg Filler?
At its core, a keg filler is a machine designed to automate the filling of kegs with beer or other beverages. It ensures that each keg is filled accurately and efficiently, minimizing waste and maximizing productivity. Modern keg fillers are equipped with advanced technologies such as flow meters, automated cleaning systems, and programmable logic controllers (PLCs), which streamline the filling process and enhance consistency.
Importance of Efficient Keg Filling
Efficient keg filling goes beyond mere speed. It directly impacts the bottom line of a brewery by reducing operational costs associated with labor, energy, and materials. Moreover, it plays a pivotal role in maintaining product quality and extending shelf life. Breweries that prioritize keg filler efficiency can deliver fresher, more consistent products to their customers, thereby enhancing their reputation and customer satisfaction.
Factors Influencing Keg Filler Efficiency
Several factors contribute to the efficiency of a keg filler. Equipment design and quality are paramount, as well as regular maintenance and calibration. Operator training and skill level also play a crucial role in maximizing efficiency. Ensuring that all these elements work harmoniously is essential for achieving optimal performance from a keg filler.
Technologies Advancing Keg Filler Efficiency
Recent advancements in keg filling technology have revolutionized brewery operations. For instance, the integration of sensor-based fill level detection systems allows for precise filling, reducing product loss due to overfilling or underfilling. Automated cleaning systems not only save time but also improve hygiene standards, crucial in the beverage industry.
Case Studies on Improved Efficiency
To illustrate the impact of efficient keg filling, consider breweries that have embraced modern technologies. By upgrading their keg fillers, these breweries have reported significant reductions in downtime, improved yield per batch, and enhanced product consistency. Such improvements translate directly into cost savings and increased profitability.
Impact on Brewery Production Schedules
Efficient keg filling directly influences production schedules by reducing bottlenecks and ensuring a steady flow of finished product. Breweries can meet customer demand more effectively, whether it’s filling large orders or managing seasonal fluctuations in demand. This reliability is key to maintaining competitive advantage in a dynamic market.
Quality Control and Consistency
Maintaining stringent quality control standards is non-negotiable in the brewing industry. Efficient keg filling processes contribute to consistent product quality by minimizing exposure to contaminants and ensuring precise filling volumes. This consistency not only meets regulatory requirements but also reinforces brand integrity and customer loyalty.
Cost Analysis: Efficiency vs. Downtime
The financial implications of keg filler efficiency are profound. Reduced downtime means more productive hours, while lower energy consumption and fewer material losses contribute to overall cost savings. Investing in a high-quality, efficient keg filler system thus becomes a strategic decision that pays dividends over time.
Impact of Keg Filler Efficiency on Brewery Operations
Metric | Before Efficiency Improvement | After Efficiency Improvement |
---|---|---|
Downtime (hours/month) | 50 hours | 20 hours |
Yield per Batch (kegs) | 95 kegs | 105 kegs |
Labor Cost Savings (%) | 10% | 15% |
Energy Consumption (kWh/keg) | 0.8 kWh/keg | 0.6 kWh/keg |
Material Losses (%) | 2% | 1% |
Customer Complaints (per month) | 8 | 3 |
Best Practices for Maximizing Efficiency
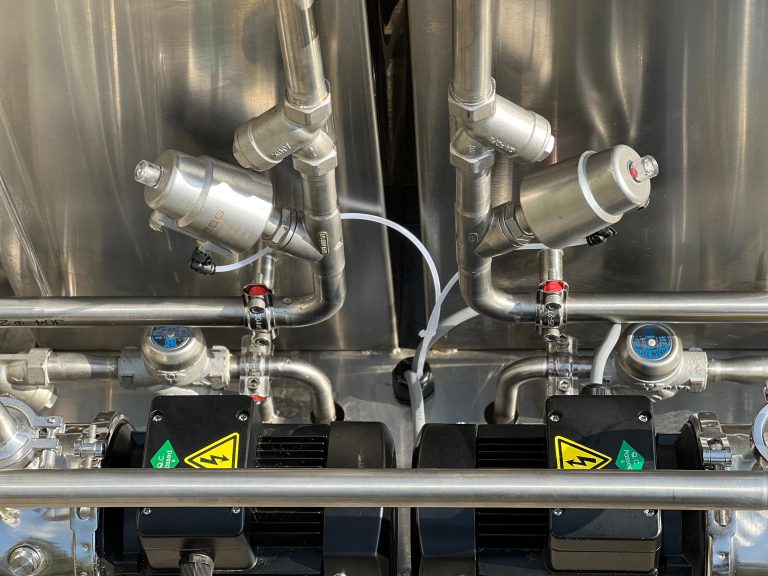
Optimizing keg filler efficiency requires a holistic approach. Regular maintenance schedules, ongoing operator training, and leveraging the latest technological advancements are fundamental. Breweries should also consider data-driven decision-making, using analytics to fine-tune processes and identify areas for improvement.
Conclusion
Efficient keg filling is not just a technical necessity but a strategic advantage for breweries aiming to thrive in a competitive market. By investing in advanced technology, optimizing operational practices, and prioritizing quality control, breweries can enhance efficiency, reduce costs, and deliver superior products to their customers consistently.
FAQ
Q: How often should a keg filler be cleaned?
A: Cleaning frequency depends on usage, but daily cleaning routines are standard to maintain hygiene and operational efficiency.
Q: What are the signs that a keg filler needs maintenance?
A: Signs include inconsistent fill levels, unusual noises, or increased downtime. Regular inspections and preventive maintenance can prevent costly repairs.
Q: Can keg filler efficiency impact product shelf life?
A: Yes, precise filling minimizes exposure to oxygen and contaminants, extending product shelf life and maintaining freshness.