Introduction
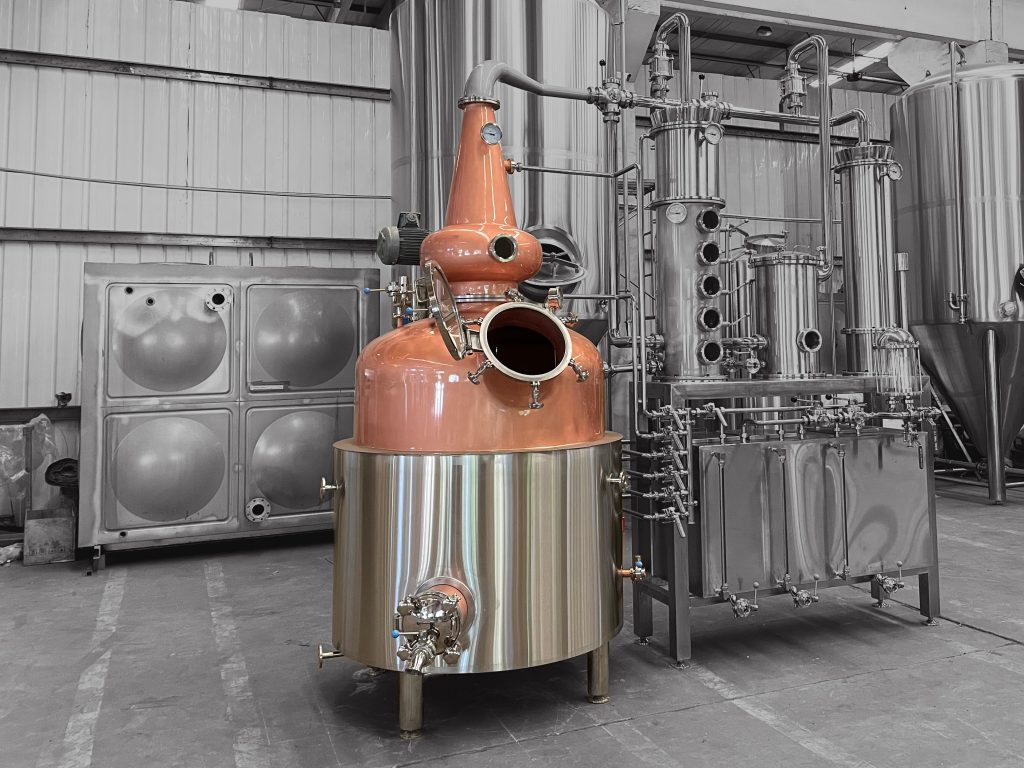
A distillation column is a vital piece of equipment used in industries such as chemical processing, oil refining, and pharmaceutical manufacturing. It is designed to separate liquid mixtures into their component parts based on differences in boiling points. Whether it is used for refining crude oil, purifying chemicals, or producing alcoholic beverages, a well-built system ensures efficiency, cost savings, and optimal product quality. Choosing a high-quality unit can significantly impact production output, energy consumption, and long-term operational costs. This blog explores the importance of investing in the right equipment, the key factors to consider, and how it influences different industrial applications.
What Is a Distillation Column?
A distillation column is a tall, vertical vessel used in separation processes. It works by heating a liquid mixture so that the more volatile components vaporize and rise through the column, while the heavier fractions condense and fall. This repeated vaporization and condensation process allows different substances to be collected at varying heights. The equipment is commonly used in industries that require highly purified liquids, such as oil refineries, chemical plants, and beverage production facilities. Due to the complexity of the separation process, precise control of temperature, pressure, and flow rates is necessary to achieve high efficiency.
The Role of a Distillation Column in Industrial Applications
Oil Refining
In petroleum refineries, distillation columns are essential for separating crude oil into valuable products like gasoline, diesel, jet fuel, and lubricants. The process, known as fractional distillation, divides crude oil into different fractions based on boiling points. The efficiency of the column plays a crucial role in determining the yield and quality of these refined products. A well-designed system reduces energy consumption while maximizing output, making it a critical component in modern refining operations.
Chemical Processing
The chemical industry relies on distillation columns to purify solvents, extract essential compounds, and separate reaction products. The effectiveness of the separation process determines the quality and purity of the final chemicals. Whether producing high-grade solvents, specialty chemicals, or intermediates for pharmaceuticals, industries require advanced separation systems to meet strict purity standards. The right column design ensures higher efficiency, reducing waste and improving overall process sustainability.
Pharmaceutical Production
Pharmaceutical manufacturers use distillation columns to produce purified solvents, active pharmaceutical ingredients (APIs), and essential drug components. Purity is a key requirement in this industry, as even slight impurities can affect drug effectiveness and safety. The ability to precisely control separation parameters helps manufacturers comply with regulatory standards while ensuring the consistency of pharmaceutical products. Investing in a high-performance system can also lower operational costs by reducing the need for additional purification steps.
Alcohol and Beverage Industry
In the alcoholic beverage industry, distillation is the primary method for producing spirits such as whiskey, vodka, and rum. The process determines the purity, flavor, and alcohol concentration of the final product. A well-constructed distillation column helps achieve the desired alcohol content while preserving essential flavor compounds. Consistency is crucial in beverage production, and using a high-quality system ensures uniformity across different batches. Many distilleries invest in specialized designs to optimize both efficiency and product quality.
Key Features of a High-Quality Distillation Column
Efficient Heat Transfer
Proper heat distribution is critical for effective separation. A high-performance system incorporates advanced heat exchangers and optimized heating mechanisms to ensure uniform vaporization and condensation. This not only improves separation efficiency but also reduces energy consumption, leading to lower operating costs over time.
Optimized Packing and Trays
The internal structure plays a key role in the separation process. High-efficiency systems use advanced packing materials or precision-engineered trays to enhance vapor-liquid contact. Structured packing improves mass transfer, while well-designed trays allow for better liquid distribution, both of which contribute to higher separation efficiency. Choosing the right internal configuration depends on the specific application and separation requirements.
Corrosion Resistance
Many industrial processes involve corrosive substances that can damage equipment over time. To ensure durability, high-quality units are constructed from corrosion-resistant materials such as stainless steel, titanium, or specialized alloys. Proper material selection extends the lifespan of the equipment and reduces maintenance costs.
Energy Efficiency
Energy consumption is a significant operational cost in separation processes. Modern designs incorporate features like optimized reflux ratios, improved insulation, and heat recovery systems to reduce energy usage. By minimizing heat loss and optimizing operational parameters, companies can achieve higher efficiency while lowering fuel and electricity expenses.
Customization Options
Every industry has unique separation requirements, and a one-size-fits-all approach does not always work. Customizable options allow businesses to tailor the design, size, and internal configurations to match specific production needs. This flexibility ensures that the system operates at peak performance for the intended application.
Comparing Different Types of Distillation Columns
Type of Distillation Column | Best Used For | Advantages | Disadvantages |
---|---|---|---|
Packed Column | Fine chemical separations, pharmaceuticals | High efficiency, better mass transfer | Higher pressure drop |
Tray Column | Oil refining, large-scale separation | Robust design, easier maintenance | Lower efficiency compared to packed columns |
Fractional Distillation Column | Petroleum, alcohol production | Higher purity levels, precise separation | More complex setup |
Vacuum Distillation Column | Heat-sensitive substances | Low-temperature separation, energy savings | Higher equipment costs |
How to Choose the Right Distillation Column
Consider Your Industry’s Needs
Each industry has different requirements when it comes to separation processes. Understanding these needs helps in selecting the most suitable system. For example, large-scale oil refining typically requires tray-based designs, whereas fine chemical separations benefit from packed columns.
Evaluate Material Construction
Durability is a major factor in selecting a unit. Corrosion-resistant materials help extend the lifespan of the equipment, especially in environments where aggressive chemicals are processed. Stainless steel and other specialized alloys are commonly used to ensure long-term performance.
Assess Energy Consumption
Operational costs are a key consideration for industrial facilities. Choosing an energy-efficient model with optimized reflux control and heat recovery can lead to significant cost savings. Advanced thermal management techniques improve overall efficiency while reducing environmental impact.
Ensure Proper Sizing
Selecting the right size is crucial for maintaining productivity and efficiency. Oversized equipment can lead to unnecessary energy waste, while undersized systems may limit production capacity. Properly designed units strike a balance between throughput and performance.
Maintenance Tips for a Long-Lasting Distillation Column
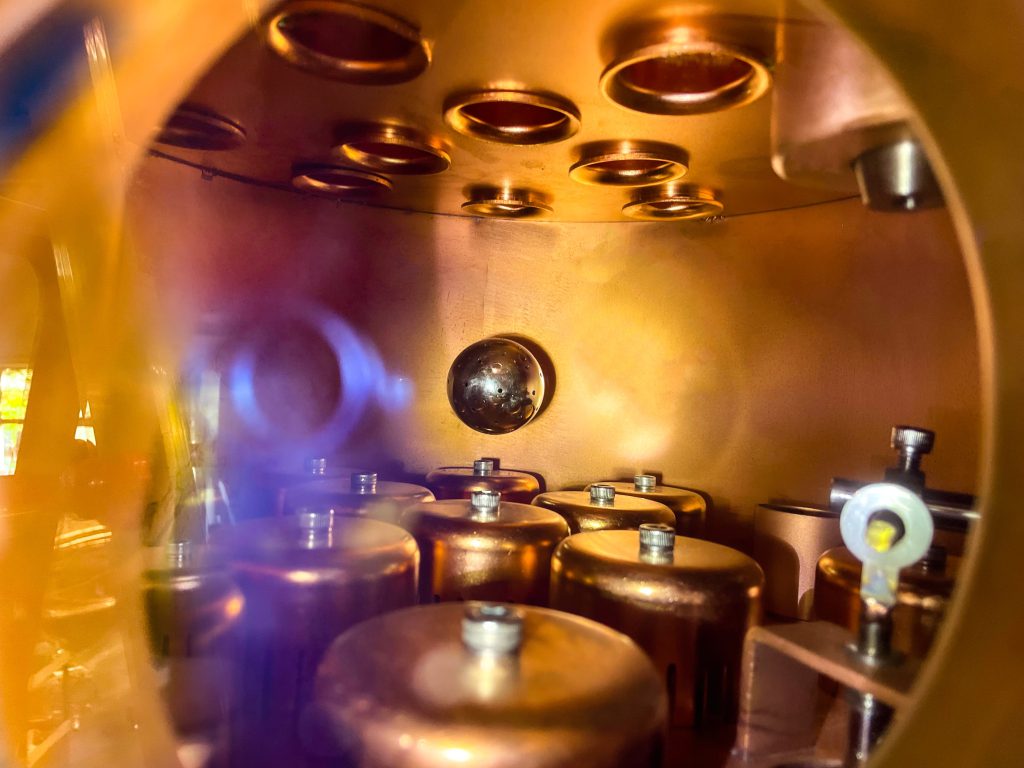
Regular Cleaning and Inspection
Routine maintenance prevents contamination and buildup inside the system, ensuring consistent performance. Periodic inspections help identify potential issues before they escalate into costly repairs.
Monitor Temperature and Pressure
Keeping process parameters within optimal ranges ensures stable operation. Sudden fluctuations in temperature or pressure can lead to inefficiencies or damage over time.
Replace Worn-Out Components
Internal components like trays, packing, and seals degrade over time. Replacing them when necessary helps maintain peak separation efficiency.
Optimize Reflux Ratios
Adjusting reflux ratios according to operational needs ensures the best balance between energy consumption and separation efficiency.
Conclusion
A high-quality distillation column is essential for achieving precise separation in industrial applications. Whether in oil refining, pharmaceuticals, or beverage production, investing in a well-designed system improves efficiency, reduces operational costs, and enhances product quality. Proper selection, maintenance, and customization ensure long-term reliability and performance.
If you are looking for a top-tier solution, contact us today to discuss your needs and find the best equipment for your application.
FAQ
What factors affect the efficiency of a distillation column?
Several factors influence performance, including heat distribution, reflux control, internal design, and material selection. Regular maintenance is also key to maintaining efficiency.
How long does a distillation column last?
With proper care and maintenance, a high-quality unit can last for several decades. The lifespan depends on factors such as material durability and operating conditions.
What is the difference between a packed and tray distillation column?
Packed designs use structured materials for improved mass transfer, while tray-based systems rely on perforated plates. Each has advantages depending on the specific application.