Introduction
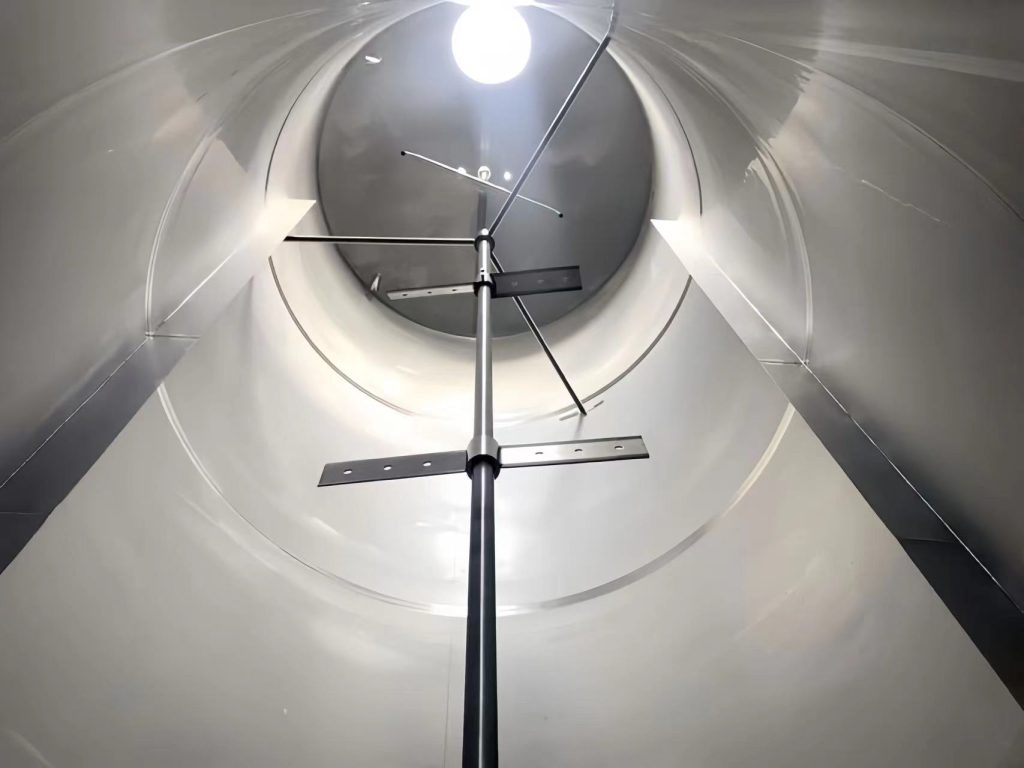
Industrial tank mixers are indispensable tools in various industries, from chemical processing to food and beverage manufacturing. These robust machines are designed to blend, mix, and homogenize a wide range of materials, ensuring consistent product quality and efficient production. In this comprehensive guide, we will delve into the world of industrial tank mixers, exploring their types, applications, and the benefits they offer. We will also discuss the factors to consider when selecting the right tank mixer for your specific needs.
Understanding Industrial Tank Mixers
What is an Industrial Tank Mixer?
An industrial tank mixer is a mechanical device used to agitate and blend substances within a tank or vessel. These mixers are essential for a variety of processes, including:
- Blending: Combining multiple ingredients to create a homogeneous mixture.
- Mixing: Incorporating solid particles or liquid additives into a base fluid.
- Homogenization: Breaking down large particles and creating a uniform dispersion.
- Emulsification: Combining two immiscible liquids, such as oil and water.
How do Industrial Tank Mixers Work?
The working principle of industrial tank mixers involves the use of an impeller, which is a rotating component that creates the mixing action. The impeller is driven by a motor and submerged in the liquid or slurry within the tank. As the impeller rotates, it generates turbulence and shear forces, which break down agglomerates, disperse solids, and promote uniform mixing.
Types of Industrial Tank Mixers
Industrial tank mixers can be categorized based on their impeller design and mixing action. Some common types include:
Turbine Mixers:
- Feature flat blades that create a radial flow pattern, making them suitable for mixing low-viscosity liquids.
- Ideal for applications such as blending water-based solutions and mixing light-duty slurries.
Propeller Mixers:
- Generate an axial flow pattern, making them ideal for mixing large volumes of liquids.
- Commonly used for mixing tanks, blending tanks, and process vessels in various industries.
High-Shear Mixers:
- Designed for intense mixing and emulsification, high-shear mixers produce high shear rates to break down particles and create fine dispersions.
- Used in applications such as homogenizing milk, emulsifying cosmetics, and dispersing pigments in paints.
Anchor Mixers:
- Anchor mixers are used for viscous materials and solids suspension. The impeller design prevents settling and ensures uniform mixing.
- Commonly used in the food industry for mixing dough, batter, and other viscous substances.
Applications of Industrial Tank Mixers
Industrial tank mixers find applications in a wide range of industries, including:
- Chemical Processing: Mixing chemicals, blending additives, and creating emulsions.
- Food and Beverage: Mixing ingredients, creating batters, and homogenizing products.
- Pharmaceutical: Mixing active ingredients, creating suspensions, and blending ointments.
- Cosmetics: Mixing creams, lotions, and perfumes.
- Paint and Coatings: Mixing pigments, dispersing additives, and blending coatings.
- Pulp and Paper: Mixing chemicals, dispersing additives, and blending slurries.
Benefits of Using Industrial Tank Mixers
- Improved Product Quality: Consistent and uniform mixing ensures reliable product quality.
- Increased Efficiency: Faster mixing times and reduced batch cycle times.
- Reduced Energy Consumption: Efficient impeller designs and optimized motor controls minimize energy usage.
- Scalability: Tank mixers are available in various sizes to accommodate different production volumes.
- Versatility: Suitable for a wide range of materials and applications.
Factors to Consider When Selecting an Industrial Tank Mixer
When selecting an industrial tank mixer, several factors must be considered to ensure optimal performance and efficiency:
- Material Properties: Viscosity, density, and particle size of the materials being mixed.
- Tank Size and Geometry: Dimensions and shape of the tank.
- Mixing Requirements: Desired mixing intensity, mixing time, and temperature control.
- Process Conditions: Pressure, temperature, and atmosphere.
- Safety Considerations: Hazardous materials, explosion-proof requirements.
- Budget: Cost of the mixer, installation, and maintenance.
Key Characteristics of Different Impeller Types
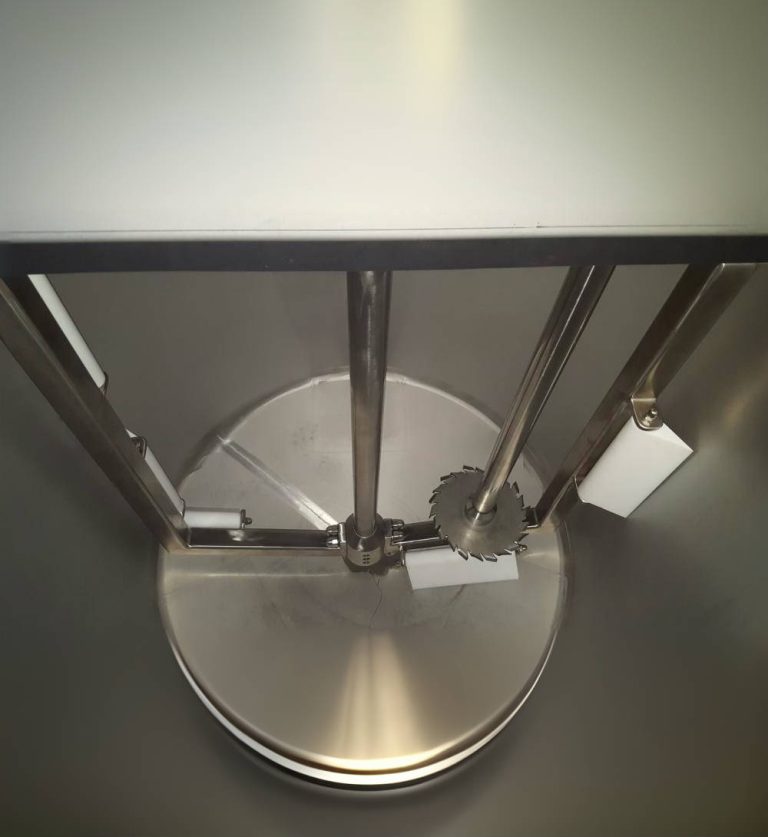
Impeller Type | Advantages | Applications |
---|---|---|
Turbine | High flow rates, low shear | Blending, mixing low-viscosity liquids |
Propeller | Axial flow, efficient mixing | Large volume mixing, tank aeration |
High-shear | Intense mixing, emulsification | Dispersing solids, creating emulsions |
Anchor | Suspending solids, mixing viscous materials | Pastes, slurries, viscous liquids |
Conclusion
Industrial tank mixers are essential tools for a wide range of industries, providing efficient and effective mixing solutions. By understanding the different types of mixers and their applications, you can select the most suitable equipment for your specific needs. Investing in a high-quality industrial tank mixer can lead to improved product quality, increased productivity, and reduced operating costs.
FAQ
What is the difference between a turbine mixer and a propeller mixer?
Turbine mixers create a radial flow pattern, while propeller mixers generate an axial flow pattern.
How do I select the right impeller for my application?
Consider the viscosity, density, and particle size of the materials being mixed.
Can industrial tank mixers be used for mixing solids?
Yes, anchor mixers are specifically designed for mixing viscous materials and solids suspension.
What safety precautions should be taken when operating an industrial tank mixer?
Follow safety guidelines, wear appropriate protective equipment, and be aware of potential hazards.
How can I optimize the performance of my industrial tank mixer?
Regular maintenance, proper impeller selection, and optimized operating conditions can improve performance.