Introduction
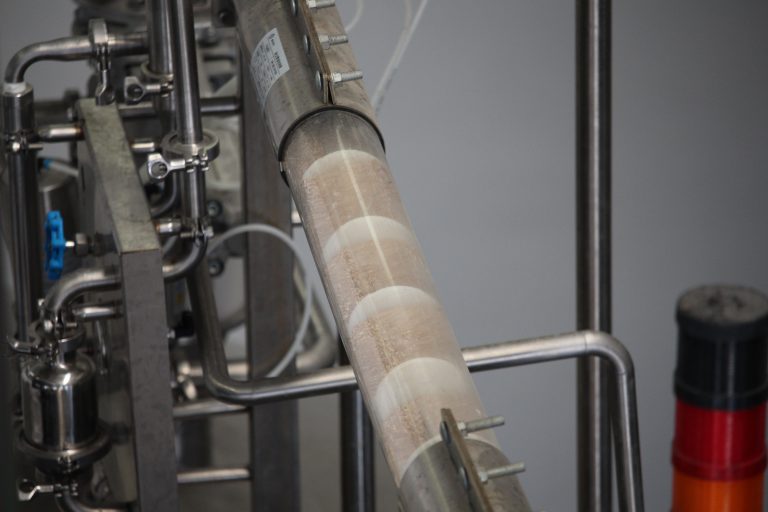
In today’s fast-paced manufacturing environments, the role of automatic conveyor systems cannot be overstated. These systems have revolutionized production lines across industries by enhancing efficiency, reliability, and safety. This blog explores the transformative impact of automatic conveyor systems on manufacturing processes.
Understanding Automatic Conveyor Systems
Automatic conveyor systems are mechanized solutions designed to transport materials or products from one location to another within a facility. These systems operate autonomously or semi-autonomously, utilizing various technologies such as motorized rollers, belts, or chains to move goods efficiently. The key components include:
- Drive units: Drive units in automatic conveying systems serve as the primary power sources that move the conveyor belts or chains, utilizing electric motors or hydraulic systems to drive motion along the production line efficiently.
- Belts/chains: Belts or chains are integral mechanisms within automatic conveyor systems, designed to carry materials or products from one point to another. They are constructed from durable materials such as rubber, plastic, or metal, ensuring reliable and smooth transportation.
- Control systems: Automated control systems form the brain of automatic conveying systems, overseeing operations such as speed control, start/stop sequences, and material flow management. These systems use sensors, PLCs (Programmable Logic Controllers), and software algorithms to optimize performance and maintain synchronization across the entire conveyor network.
Benefits of Automatic Conveyor Systems
The adoption of automatic conveying systems brings several advantages to manufacturing operations:
Benefits | Description |
---|---|
Increased Efficiency | Streamlined material handling processes lead to faster production cycles and reduced downtime. |
Enhanced Safety | Minimized manual handling reduces the risk of accidents and injuries in the workplace. |
Improved Accuracy | Precise movement ensures consistent product quality and reduces errors. |
Space Optimization | Vertical and horizontal integration allows for better use of floor space. |
Cost Savings | Lower labor costs and decreased operational expenses contribute to overall savings. |
Applications Across Industries
Automatic conveyor systems find applications in diverse industries, including:
- Automotive: Assembly lines for vehicle production heavily rely on automatic conveying systems to ensure seamless movement of components and parts, optimizing the manufacturing process from start to finish.
- Food and Beverage: In the food and beverage industry, automatic conveyor systems play a critical role in the handling and packaging of goods, maintaining hygiene standards and facilitating high-speed production lines.
- Logistics and Warehousing: Within logistics and warehousing, automatic conveying systems enable efficient movement of goods within distribution centers, enhancing inventory management and order fulfillment processes.
- Pharmaceuticals: Automatic conveying systems are essential in pharmaceuticals for maintaining controlled environments during drug manufacturing, ensuring product safety and compliance with stringent regulatory standards.
Case Studies: Real-World Applications
Automotive Industry
In automotive manufacturing, automatic conveyor systems enable just-in-time production, reducing inventory costs and improving assembly line efficiency. For example, Ford’s adoption of conveyor technology has significantly streamlined their production processes.
Food and Beverage Sector
In food processing plants, conveyor systems ensure hygienic handling of products while maintaining high throughput rates. Companies like Nestlé rely on conveyor belts to transport goods safely and efficiently.
Challenges and Considerations
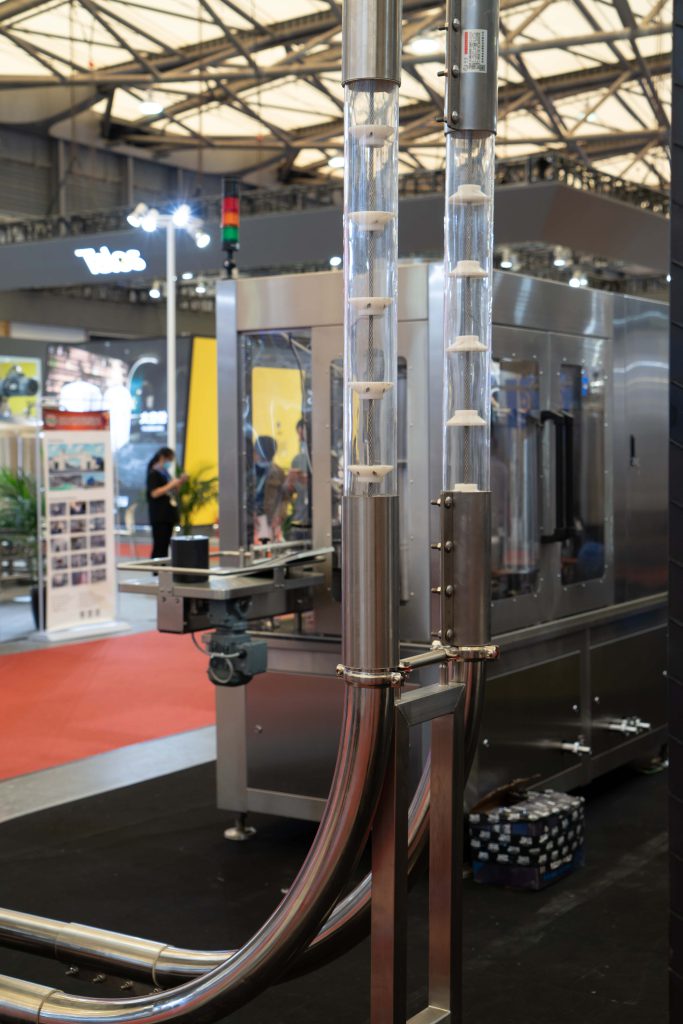
While automatic conveyor systems offer numerous benefits, they also present challenges such as initial investment costs, maintenance requirements, and integration complexities with existing infrastructure. Addressing these challenges involves:
- Cost Analysis: Evaluating ROI and long-term savings.
- Maintenance Planning: Implementing proactive maintenance schedules.
- Integration Strategies: Ensuring compatibility with other automated systems.
Conclusion
Automatic conveyor systems represent a cornerstone of modern manufacturing, optimizing production processes across industries. Their ability to enhance efficiency, ensure safety, and improve overall operational effectiveness makes them indispensable in today’s competitive market. As technology continues to evolve, these systems will play an increasingly vital role in shaping the future of manufacturing.
FAQ
Q: What are automatic conveyor systems?
Automatic conveyor systems are mechanized solutions used to transport materials or products within manufacturing facilities. They operate autonomously or semi-autonomously, utilizing various technologies for efficient material handling.
Q: What industries benefit from automatic conveyor systems?
Industries such as automotive, food and beverage, logistics, pharmaceuticals, and more benefit from automatic conveyor systems due to increased efficiency, improved safety, and cost savings.
Q: What challenges do automatic conveyor systems pose?
Challenges include initial investment costs, maintenance requirements, and integration complexities with existing infrastructure. However, these challenges are outweighed by the significant benefits offered by these systems.
This comprehensive overview underscores the pivotal role of automatic conveyor systems in driving manufacturing efficiency and innovation. Whether in optimizing workflow, ensuring product quality, or enhancing workplace safety, these systems continue to redefine the landscape of modern manufacturing.